Das Phänomen des Sputterns wurde erstmals 1852 von einem Wissenschaftler namens Grove (manchmal auch als Groe bezeichnet) entdeckt.Er beobachtete die Abscheidung von Metallschichten durch elektrische Entladungen in einer Kaltkathodenanlage.Dies markierte die erste Anerkennung des Sputterverfahrens, das sich später zu einem bedeutenden Verfahren für die Abscheidung von Dünnschichten entwickelte.Im Laufe der Jahre erweiterten Fortschritte wie die Einführung des Hochfrequenzsputterns und eine verbesserte Vakuumtechnik die Anwendungsmöglichkeiten, insbesondere für die Abscheidung von Refraktärmetallen und dielektrischen Materialien.Das Verfahren wurde in den 1930er Jahren kommerziell genutzt und erlangte in den späten 1950er und frühen 1960er Jahren aufgrund des technologischen Fortschritts wieder an Bedeutung.
Die wichtigsten Punkte werden erklärt:
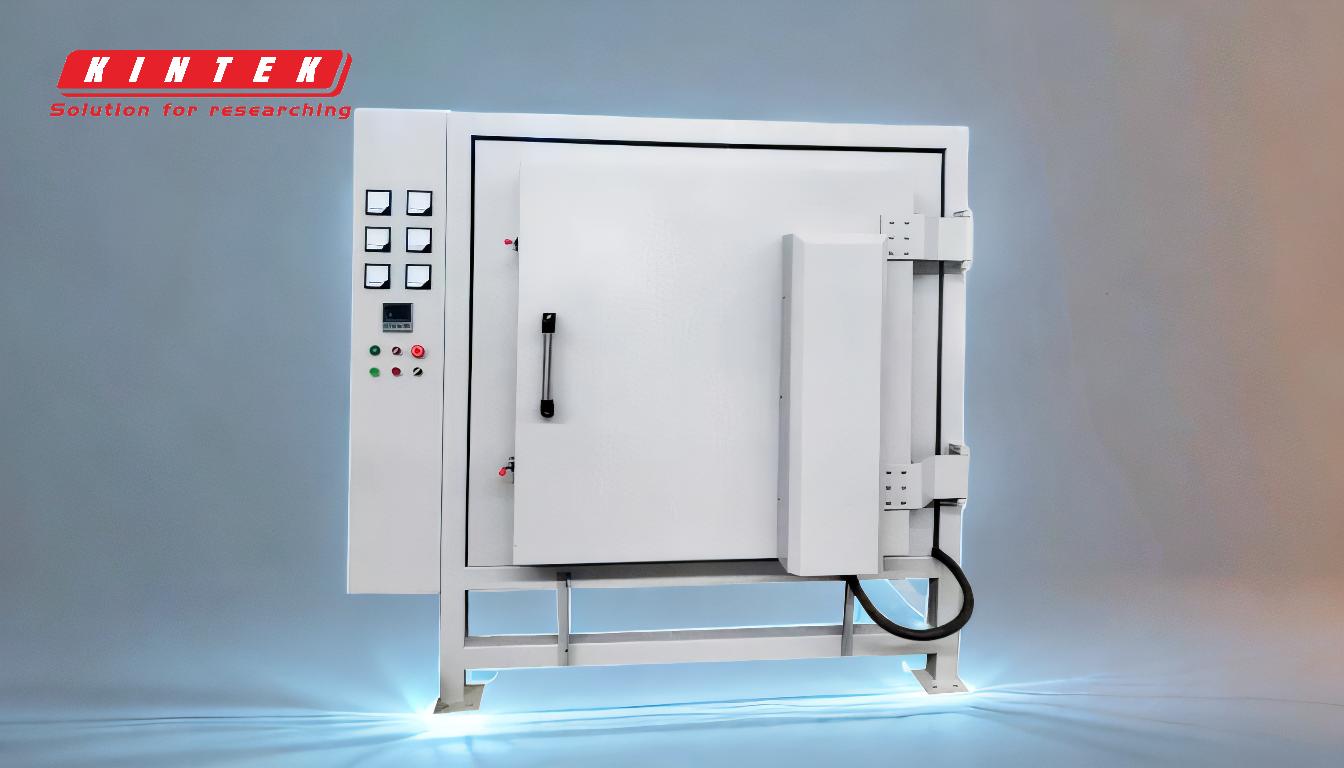
-
Entdeckung des Sputterns (1852):
- Das Sputtern wurde erstmals 1852 von Grove (oder Groe) entdeckt, der elektrische Entladungen zur Abscheidung von Metallschichten auf einer kalten Kathode verwendete.
- Diese frühe Beobachtung umfasste die Verwendung von Gleichstrom-Glimmentladungen, die zur Abscheidung dünner Metallschichten führten.
- Diese Entdeckung war insofern von Bedeutung, als sie eine Methode zur Abscheidung hochschmelzender Metalle einführte, die mit den herkömmlichen thermischen Verdampfungstechniken nur schwer abzuscheiden waren.
-
Entwicklung als Dünnschichtabscheidungstechnik (1920):
- Der Sputtering-Mechanismus wurde 1920 von Irving Langmuir zu einem praktischen Verfahren für die Abscheidung von Dünnschichten weiterentwickelt.
- Langmuirs Arbeit legte den Grundstein für das Verständnis und die Optimierung des Sputterverfahrens, wodurch es für industrielle und wissenschaftliche Zwecke besser anwendbar wurde.
- Diese Entwicklung markierte den Übergang von einer bloßen wissenschaftlichen Beobachtung zu einer brauchbaren Technologie.
-
Kommerzielle Anwendungen (1930er Jahre):
- In den 1930er Jahren fand das Sputtern seine ersten kommerziellen Anwendungen.
- Die Fähigkeit, dünne Schichten aus verschiedenen Materialien, einschließlich hochschmelzender Metalle, abzuscheiden, machte es wertvoll für Industrien, die präzise und dauerhafte Beschichtungen benötigten.
- In den 1950er Jahren wurde das Sputtern jedoch weitgehend durch die thermische Verdampfung ersetzt, da letztere einfacher und effizienter war.
-
Wiederaufleben in den späten 1950er und frühen 1960er Jahren:
- In den späten 1950er und frühen 1960er Jahren gewann das Sputtern aufgrund von Fortschritten in der Vakuumtechnik wieder an Interesse.
- Verbesserte Vakuumsysteme ermöglichten eine bessere Kontrolle über die Sputterumgebung, wodurch die Qualität und Konsistenz der abgeschiedenen Schichten verbessert wurde.
- Die Einführung des DC-Sputterns ermöglichte die Abscheidung einer breiten Palette von leitfähigen Materialien, während das RF-Sputtern die Technik auf dielektrische Materialien ausweitete.
-
Einführung des RF-Sputterns:
- Das RF-Sputtern, bei dem Hochfrequenzwellen eingesetzt werden, war ein bedeutender Fortschritt, der die Abscheidung dielektrischer Schichten ermöglichte.
- Mit dieser Innovation wurde eine wesentliche Einschränkung früherer Sputtertechniken beseitigt, die in erster Linie für leitfähige Materialien geeignet waren.
- Das HF-Sputtern erweiterte den Anwendungsbereich des Sputterns und machte es zu einem vielseitigen Werkzeug in der Materialwissenschaft und -technik.
-
Moderne Sputtering-Geräte (1970):
- 1970 stellte Peter J. Clarke das erste Sputtering-Gerät vor, das Elektronen- und Ionenkollisionen nutzte, um atomare Schichten auf Zieloberflächen abzuscheiden.
- Diese Entwicklung bedeutete einen großen Fortschritt in Bezug auf die Präzision und Kontrolle des Sputterprozesses und ermöglichte die Abscheidung ultradünner und äußerst gleichmäßiger Schichten.
- Clarkes Arbeit trug dazu bei, dass sich das Sputtern in verschiedenen Hightech-Industrien, darunter Halbleiter und Optik, durchsetzte.
-
Historischer Kontext und Entwicklung:
- Das Sputtern hat seit seiner Entdeckung im Jahr 1852 eine bedeutende Entwicklung durchlaufen.
- Von der anfänglichen Verwendung für die Abscheidung von Refraktärmetallen bis hin zu den modernen Anwendungen für die Abscheidung einer breiten Palette von Materialien hat sich das Sputtern als vielseitige und wertvolle Technik erwiesen.
- Das Wiederaufleben des Verfahrens in der Mitte des 20. Jahrhunderts und die nachfolgenden Fortschritte unterstreichen seine Anpassungsfähigkeit und Bedeutung in der Materialwissenschaft.
Wenn man die Geschichte und die Entwicklung des Sputterns versteht, kann man seine Bedeutung als Dünnschichtabscheidungstechnik und seine anhaltende Relevanz in der modernen Technologie einschätzen.
Zusammenfassende Tabelle:
Meilenstein | Jahr | Wichtige Entwicklung |
---|---|---|
Entdeckung des Sputterns | 1852 | Grove beobachtete die Abscheidung von Metallschichten durch elektrische Entladungen in einer Kaltkathode. |
Entwicklung als Dünnschichtverfahren | 1920 | Irving Langmuir optimierte die Sputtertechnik für industrielle und wissenschaftliche Anwendungen. |
Kommerzielle Anwendungen | 1930s | Sputtern wird für präzise Beschichtungen in Industrien verwendet, die haltbare Materialien benötigen. |
Wiederaufschwung mit Vakuumfortschritten | 1950-60er Jahre | Verbesserte Vakuumsysteme und RF-Sputtering erweitern die Materialkompatibilität. |
Einführung des RF-Sputterns | 1960s | Ermöglichte die Abscheidung dielektrischer Schichten und erweiterte die Anwendungsmöglichkeiten des Sputterns. |
Moderne Sputtering-Geräte | 1970 | Peter J. Clarke führte Geräte für die ultradünne, gleichmäßige Schichtabscheidung ein. |
Entdecken Sie, wie das Sputtern Ihre materialwissenschaftlichen Projekte verbessern kann. Kontaktieren Sie unsere Experten noch heute !