Bei der Herstellung von Legierungen wird eine inerte Atmosphäre verwendet, um unerwünschte chemische Reaktionen wie Oxidation oder Verunreinigungen bei Verfahren wie Wärmebehandlung, Sintern oder heißisostatischem Pressen zu verhindern. Durch die Schaffung einer kontrollierten Umgebung mit Gasen wie Argon oder Stickstoff können die Hersteller sicherstellen, dass die Legierung ihre gewünschten Eigenschaften wie Festigkeit, Haltbarkeit und Oberflächenqualität beibehält. Dies ist besonders wichtig in Branchen wie der Luft- und Raumfahrt, der Automobilindustrie und der petrochemischen Fertigung, wo die Integrität des Materials von größter Bedeutung ist. Die inerte Atmosphäre verringert auch Risiken wie Feuer, Explosionen und Verunreinigungen und sorgt für sicherere und effizientere Produktionsprozesse.
Die wichtigsten Punkte werden erklärt:
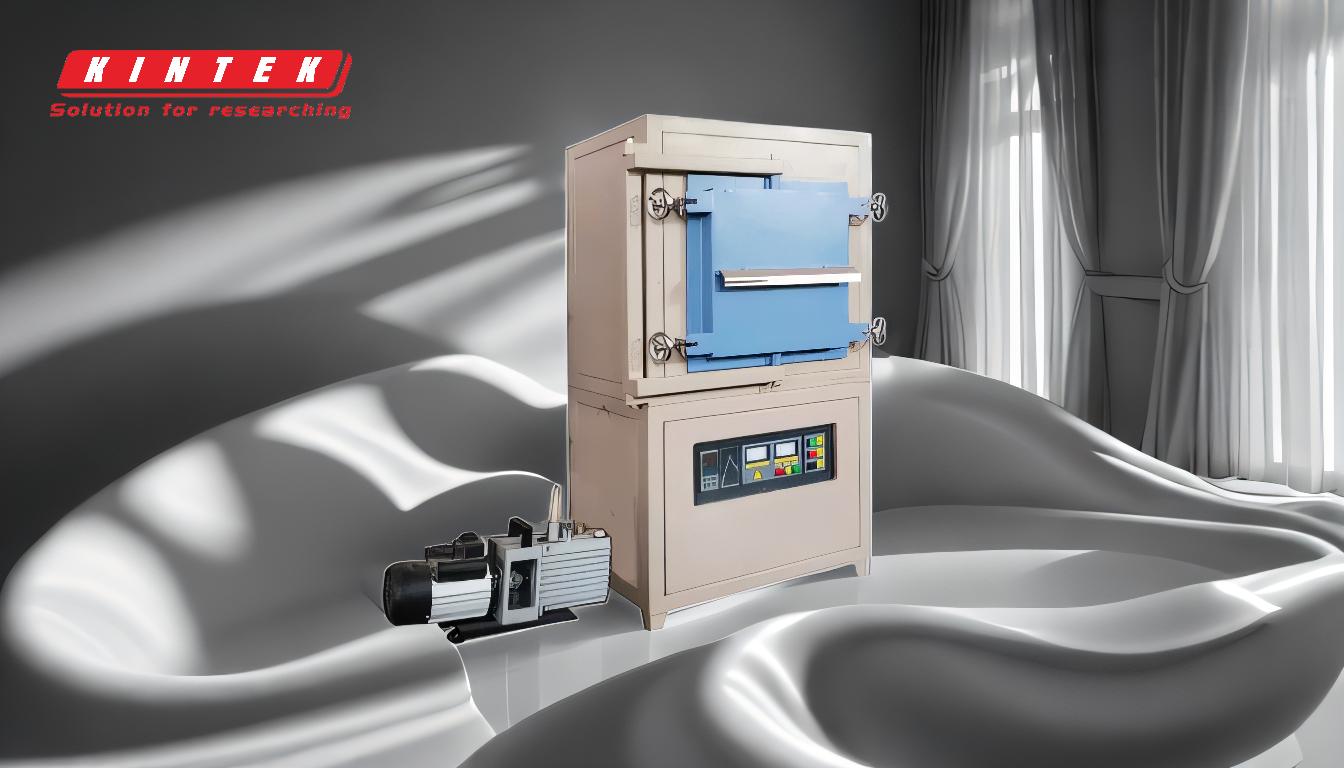
-
Verhinderung von Oxidation und Kontamination
- Oxidation tritt auf, wenn Metalle mit Luftsauerstoff reagieren und Oxide bilden, die die Oberfläche und die mechanischen Eigenschaften der Legierung beeinträchtigen können.
- Eine inerte Atmosphäre, die in der Regel mit Gasen wie Argon oder Stickstoff erzeugt wird, verdrängt Sauerstoff und andere reaktive Gase und verhindert so Oxidation und Kontamination.
- Dadurch wird sichergestellt, dass die Legierung ihre gewünschte chemische Zusammensetzung und Oberflächenqualität beibehält, was für Anwendungen, die hohe Präzision und Haltbarkeit erfordern, von entscheidender Bedeutung ist.
-
Pflege der Materialeigenschaften
- Bei Wärmebehandlungsverfahren wie Sintern, Blankglühen oder Karbonitrieren werden das Mikrogefüge und die mechanischen Eigenschaften der Legierung sorgfältig kontrolliert.
- Eine inerte Atmosphäre sorgt dafür, dass diese Prozesse ohne Beeinträchtigung durch äußere Faktoren ablaufen und die Festigkeit, Härte und andere wichtige Eigenschaften der Legierung erhalten bleiben.
- In der Luft- und Raumfahrt oder im Automobilbau zum Beispiel können schon geringe Abweichungen in den Materialeigenschaften zu katastrophalen Ausfällen führen.
-
Verbesserte Prozesskontrolle
- Eine inerte Atmosphäre sorgt für eine hochgradig kontrollierte Umgebung, die die Variabilität im Herstellungsprozess reduziert.
- Dies ist besonders wichtig bei Prozessen wie dem heißisostatischen Pressen (HIP) oder Vakuumverfahren, bei denen eine präzise Steuerung von Temperatur, Druck und Gaszusammensetzung erforderlich ist.
- Durch die Minimierung unerwünschter Reaktionen können die Hersteller konsistente Ergebnisse erzielen und Abfall reduzieren.
-
Sicherheit und Risikominderung
- Inerte Atmosphären verringern die Brand- und Explosionsgefahr, insbesondere bei Arbeiten mit reaktiven Metallen oder Hochtemperaturprozessen.
- Durch die Verdrängung von Sauerstoff wird die Wahrscheinlichkeit einer Verbrennung deutlich verringert, was eine sicherere Arbeitsumgebung schafft.
- Dies ist besonders wichtig in Branchen wie der petrochemischen Industrie, in denen die Sicherheit oberste Priorität hat.
-
Anwendungen in kritischen Industrien
- Branchen wie die Luft- und Raumfahrt, die Automobilindustrie und die petrochemische Industrie sind auf inerte Atmosphären angewiesen, um hochwertige Legierungen mit präzisen Spezifikationen herzustellen.
- In der Luft- und Raumfahrt zum Beispiel müssen Legierungen extremen Bedingungen standhalten, und jede Verunreinigung oder Oxidation könnte ihre Leistung beeinträchtigen.
- Auch im Automobilbau werden für Komponenten wie Motorteile oder Getriebesysteme Materialien mit gleichbleibenden Eigenschaften benötigt, um Zuverlässigkeit und Langlebigkeit zu gewährleisten.
-
Kosten- und Effizienzvorteile
- Die Schaffung einer inerten Atmosphäre ist zwar mit zusätzlichen Kosten verbunden, aber die langfristigen Vorteile überwiegen oft die Anfangsinvestitionen.
- Durch die Verringerung von Oxidation und Verunreinigung können die Hersteller den Materialabfall und die Nacharbeit minimieren, was zu Kosteneinsparungen führt.
- Außerdem kann die verbesserte Konsistenz und Qualität der Legierungen die Gesamteffizienz des Herstellungsprozesses erhöhen.
Zusammenfassend lässt sich sagen, dass eine inerte Atmosphäre in der Legierungsherstellung unerlässlich ist, um Oxidation zu verhindern, die Materialeigenschaften zu erhalten, die Prozesskontrolle zu gewährleisten, die Sicherheit zu verbessern und die strengen Anforderungen kritischer Industrien zu erfüllen. Durch die Verwendung von Inertgasen wie Argon oder Stickstoff können Hersteller hochwertige Legierungen mit gleichbleibender Leistung herstellen, was sie zu einem wichtigen Bestandteil moderner Industrieprozesse macht.
Zusammenfassende Tabelle:
Die wichtigsten Vorteile der inerten Atmosphäre | Einzelheiten |
---|---|
Verhindert Oxidation und Verschmutzung | Verwendet Gase wie Argon oder Stickstoff, um Sauerstoff zu verdrängen und die Integrität der Legierung zu gewährleisten. |
Behält die Materialeigenschaften bei | Bewahrt Festigkeit, Härte und Haltbarkeit während der Wärmebehandlung. |
Verbessert die Prozesskontrolle | Verringert die Variabilität und gewährleistet gleichbleibende Ergebnisse bei Verfahren wie HIP oder Sintern. |
Verbessert die Sicherheit | Verringert die Brand- und Explosionsgefahr durch Verdrängung von Sauerstoff in Hochtemperaturprozessen. |
Kritische Industrieanwendungen | Unverzichtbar für die Luft- und Raumfahrt, die Automobilindustrie und die petrochemische Industrie. |
Kosten- und Effizienzvorteile | Verringert Abfall und Nacharbeit und verbessert so langfristig die Fertigungseffizienz. |
Erfahren Sie, wie eine inerte Atmosphäre Ihren Legierungsherstellungsprozess optimieren kann kontaktieren Sie unsere Experten noch heute !