Das Sintern ist ein wichtiges Verfahren zur Verarbeitung keramischer Werkstoffe, da es pulverförmige keramische Werkstoffe in dichte, feste und dauerhafte polykristalline Strukturen verwandelt, ohne sie zu schmelzen. Bei diesem Verfahren wird das keramische Pulver bei hohen Temperaturen unterhalb seines Schmelzpunktes erhitzt, wodurch die Partikelbindung erleichtert, die Porosität verringert und die Materialdichte erhöht wird. Das Sintern ist für die Erzielung der gewünschten mechanischen, thermischen und elektrischen Eigenschaften von Keramik unerlässlich und daher in Branchen, die fortschrittliche keramische Werkstoffe mit spezifischen Leistungsmerkmalen benötigen, unverzichtbar. Das Verfahren ist kostengünstig, vielseitig und ermöglicht eine genaue Kontrolle über die Mikrostruktur und die Eigenschaften des Endprodukts.
Die wichtigsten Punkte werden erklärt:
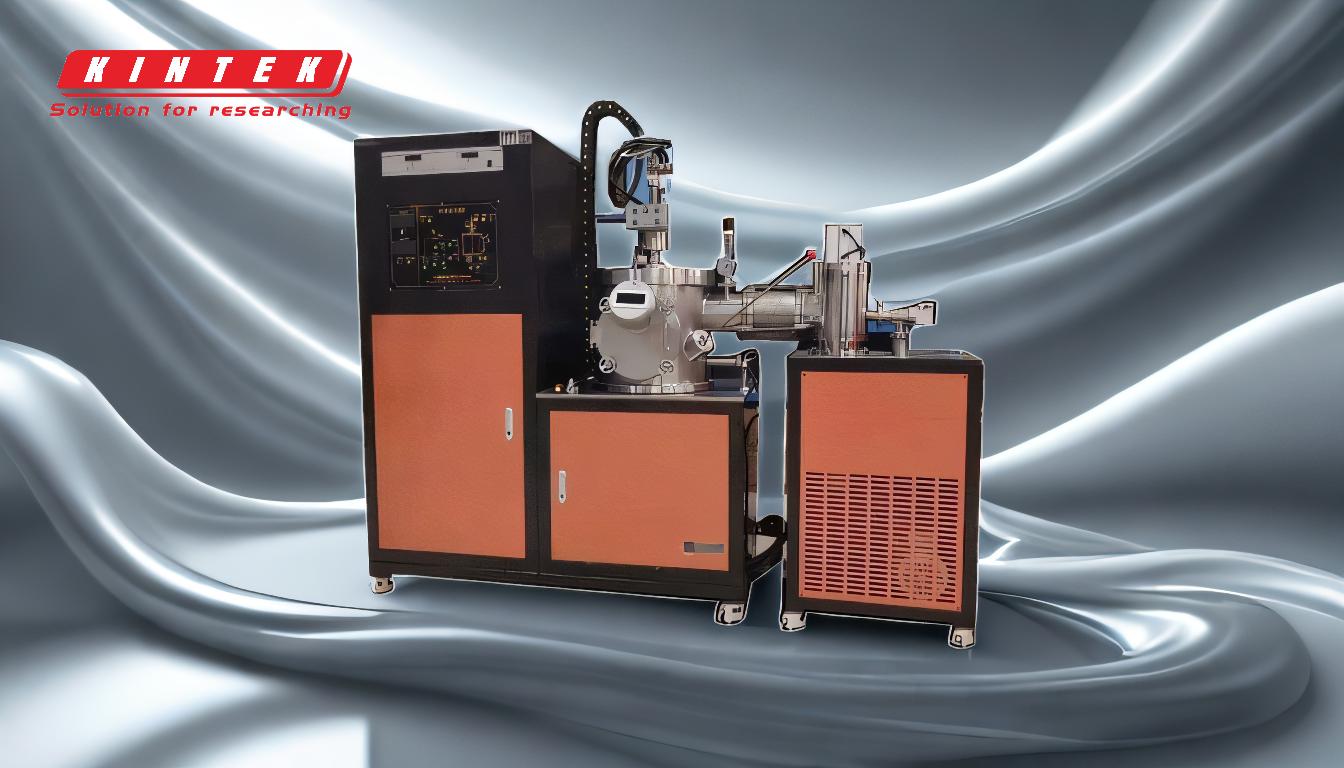
-
Verdichtung und Verbesserung der Festigkeit:
- Beim Sintern wird loses Keramikpulver in eine dichte, kohäsive Struktur umgewandelt, indem die Partikel bei hohen Temperaturen miteinander verbunden werden.
- Das Verfahren verringert die Porosität und erhöht die Dichte, was zu einem Material mit verbesserter mechanischer Festigkeit und Haltbarkeit führt.
- Dies ist von entscheidender Bedeutung für Anwendungen, bei denen Keramik hohen Belastungen, Verschleiß oder thermischen Belastungen standhalten muss.
-
Kontrolle der Mikrostruktur:
- Das Sintern ermöglicht die Bildung einer einheitlichen polykristallinen Mikrostruktur, die für die Erzielung gleichmäßiger Materialeigenschaften unerlässlich ist.
- Durch die Steuerung von Sinterparametern wie Temperatur, Zeit und Atmosphäre können die Hersteller die Korngröße, Dichte und Porosität an die jeweiligen Anwendungsanforderungen anpassen.
-
Kosten-Nutzen-Verhältnis und Effizienz:
- Das Sintern ist ein kostengünstiges Verfahren, da das Material nicht geschmolzen werden muss, was Energie spart und die Produktionskosten senkt.
- Das Verfahren ist hocheffizient und skalierbar, so dass es sich für die Massenproduktion von Keramikbauteilen eignet.
-
Branchenübergreifende Vielseitigkeit:
- Sinterkeramik wird aufgrund ihrer hervorragenden thermischen, elektrischen und mechanischen Eigenschaften in einer Vielzahl von Branchen eingesetzt, darunter Elektronik, Luft- und Raumfahrt, Automobilbau und medizinische Geräte.
- Beispiele sind keramische Isolatoren, Schneidwerkzeuge, Lager und biomedizinische Implantate.
-
Verbesserte funktionale Eigenschaften:
- Das Sintern verbessert die funktionellen Eigenschaften von Keramik, wie Wärmeleitfähigkeit, elektrische Isolierung und chemische Beständigkeit.
- Diese Eigenschaften machen Sinterkeramik ideal für Hochleistungsanwendungen in rauen Umgebungen.
-
Schrumpfung und Maßgenauigkeit:
- Während des Sinterns erfährt das Material eine kontrollierte Schrumpfung, die bei der Konstruktion und Verdichtung berücksichtigt wird.
- Dadurch wird sichergestellt, dass das Endprodukt präzise Abmessungen hat und die engen Toleranzen einhält, die für moderne Anwendungen erforderlich sind.
-
Kontrollierte Atmosphäre und Abkühlungsraten:
- Das Sintern erfolgt unter kontrollierter Atmosphäre, um Oxidation oder Verunreinigung zu vermeiden und die Reinheit und Integrität des keramischen Materials zu gewährleisten.
- Die Anpassung der Abkühlungsgeschwindigkeit ermöglicht eine Feinabstimmung der Materialeigenschaften, wie z. B. Härte und Zähigkeit.
-
Umwandlung von Pulver in einen festen Körper:
- Das Sintern wandelt pulverförmige keramische Werkstoffe in einen festen, dichten Körper mit spezifischen Eigenschaften um und ist damit ein grundlegender Schritt in der Keramikherstellung.
- Diese Umwandlung wird durch Diffusions- und Stoffübertragungsmechanismen erreicht, die Poren beseitigen und eine starke, kohäsive Struktur schaffen.
Zusammenfassend lässt sich sagen, dass das Sintern für die Verarbeitung keramischer Werkstoffe unverzichtbar ist, da es eine kostengünstige, effiziente und vielseitige Methode zur Herstellung dichter, fester und leistungsfähiger Keramiken mit maßgeschneiderten Eigenschaften darstellt. Seine Fähigkeit, die Mikrostruktur zu kontrollieren, die funktionalen Eigenschaften zu verbessern und die Maßhaltigkeit zu gewährleisten, macht es zu einem Eckpfeiler der modernen Keramikherstellung.
Zusammenfassende Tabelle:
Hauptaspekt | Einzelheiten |
---|---|
Verdichtung & Festigkeit | Bindet Partikel, reduziert die Porosität und erhöht die mechanische Festigkeit. |
Kontrolle der Mikrostruktur | Maßgeschneiderte Korngröße, Dichte und Porosität für gleichbleibende Eigenschaften. |
Kosten-Wirksamkeit | Energieeffizient und skalierbar für die Massenproduktion. |
Vielseitigkeit | Wird in der Elektronik-, Luft- und Raumfahrt-, Automobil- und Medizinindustrie verwendet. |
Funktionelle Eigenschaften | Verbessert die Wärmeleitfähigkeit, die elektrische Isolierung und die chemische Beständigkeit. |
Maßgenauigkeit | Gewährleistet präzise Abmessungen und enge Toleranzen. |
Kontrollierte Atmosphäre | Verhindert Oxidation und Verunreinigung für die Materialintegrität. |
Pulver zu Festkörper | Verwandelt pulverförmige Keramiken in dichte, kohäsive Strukturen. |
Sind Sie bereit, Ihren Keramikherstellungsprozess zu verbessern? Kontaktieren Sie uns heute für kompetente Lösungen!