Heißpressen verstehen
Inhaltsverzeichnis
Definition und Ablauf des Heißpressens
Beim Heißpressen handelt es sich um einen pulvermetallurgischen Prozess mit hohem Druck und niedriger Dehnungsrate, mit dem Pulver oder Pulverpresskörper bei hohen Temperaturen geformt werden, um Sinter- und Kriechprozesse auszulösen. Dabei werden durch die gleichzeitige Anwendung von Wärme und Druck harte und spröde Materialien hergestellt.
Primäre Verwendung und Anwendung
Heißpressen wird hauptsächlich zur Verfestigung von Diamant-Metall-Verbundschneidwerkzeugen, technischer Keramik und anderen harten und spröden Materialien eingesetzt. Es funktioniert durch Partikelumlagerung und plastischen Fluss an den Partikelkontakten. Das lose Pulver oder der vorverdichtete Teil wird in eine Graphitform gefüllt, die eine Induktions- oder Widerstandserwärmung auf Temperaturen von typischerweise 2.400 °C (4.350 °F) ermöglicht. Es können Drücke von bis zu 50 MPa (7.300 psi) angewendet werden. Heißpressen wird auch beim Pressen verschiedener Arten von Polymeren eingesetzt.
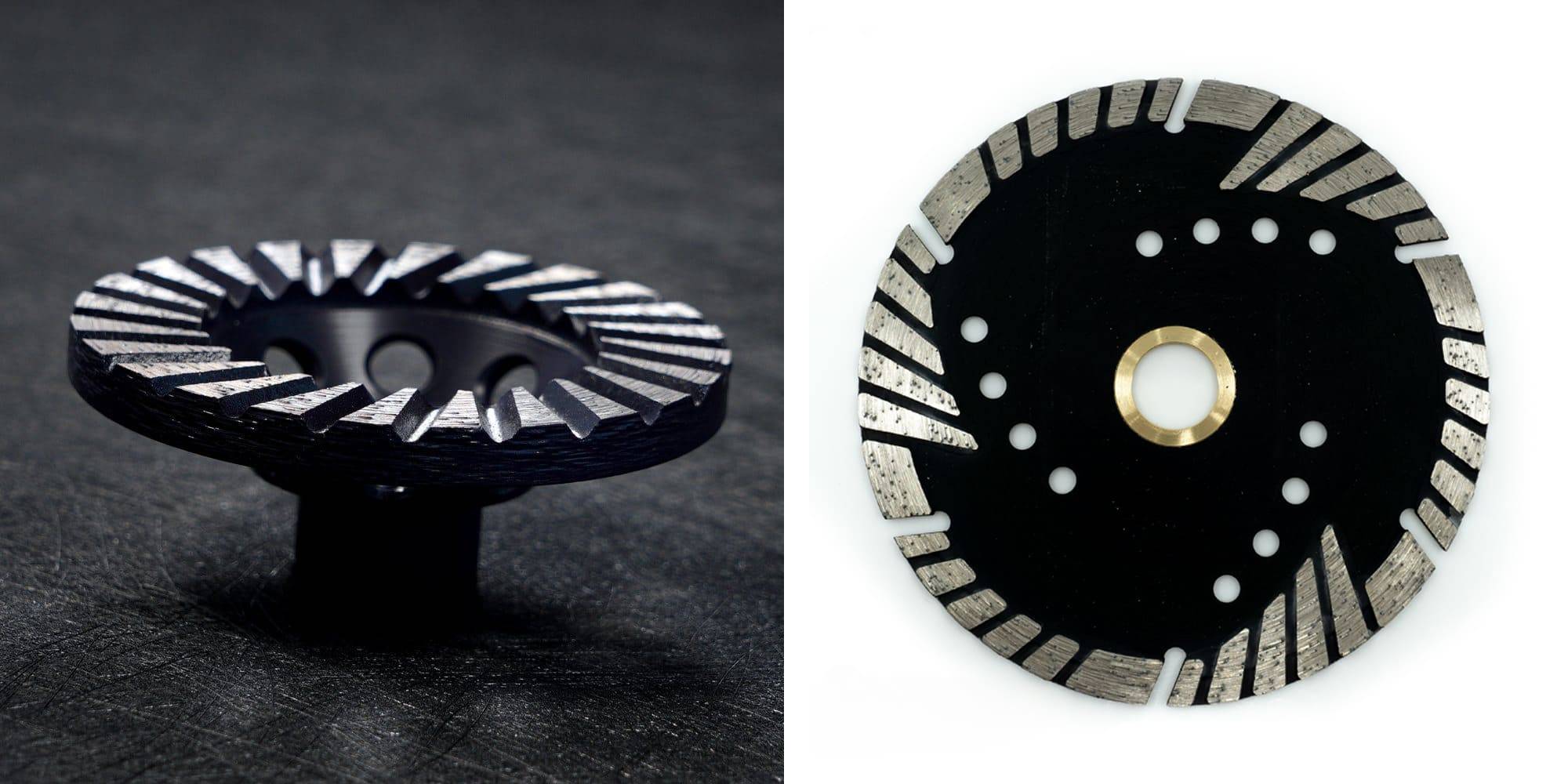
Heißgepresste Diamanten
Verdichtung durch Partikelumlagerung und plastisches Fließen
Der Verdichtungsprozess beim Heißpressen erfolgt durch Partikelumlagerung und plastisches Fließen an den Partikelkontakten. Der beim Heißpressen ausgeübte äußere Druck führt zur Zerstörung innerer Defekte und Poren, was dazu führt, dass die Innenflächen miteinander in Kontakt kommen. Das Material durchläuft dann ein Hochtemperaturkriechen, das eine gegenseitige Durchdringung und Diffusionsbindung ermöglicht und Defekte und Porosität vollständig beseitigt.
Verwendung von Graphitformen und Heiztemperaturen
Beim Heißpressen wird üblicherweise eine Graphitform verwendet, um das lose Pulver oder den vorverdichteten Teil aufzunehmen. Die Graphitform ermöglicht eine effiziente Erwärmung durch Induktion oder Widerstandserwärmung. Die beim Heißpressen verwendeten Temperaturen können bis zu 2.400 °C (4.350 °F) erreichen und sorgen so für die für die Verdichtung notwendigen Sinter- und Kriechprozesse.
Mit dem Prozess verbundene Belastungen
Beim Heißpressen werden hohe Drücke angewendet, um eine Verdichtung zu erreichen. Beim Heißpressvorgang können Drücke von bis zu 50 MPa (7.300 psi) ausgeübt werden. Der hohe Druck unterstützt die Neuordnung der Partikel und den plastischen Fluss, was zu einem kompakten und dichten Endprodukt führt.
Heißpressen in der Polymerindustrie
Auch in der Polymerindustrie wird das Heißpressen häufig eingesetzt. Durch den Einsatz der Heißpresstechnik können Hersteller auf Bindemittel in ihrem Herstellungsprozess verzichten und stattdessen die Kombination aus Kraft und Temperatur nutzen, um ihre Teile vollständig zu verbinden. Dies ermöglicht die Herstellung hochwertiger Polymerprodukte mit verbesserten mechanischen Eigenschaften und Maßgenauigkeit.
Zusammenfassend ist Heißpressen ein pulvermetallurgisches Verfahren zur Herstellung harter und spröder Materialien. Dabei werden durch die Anwendung von Wärme und Druck Sinter- und Kriechprozesse eingeleitet, die zu einer Verdichtung führen. Heißpressen wird häufig in verschiedenen Branchen eingesetzt, darunter in der Luft- und Raumfahrt, in der Keramik- und Polymerherstellung. Der Prozess nutzt eine Graphitform und kann hohe Temperaturen und Drücke erreichen, um die gewünschten Ergebnisse zu erzielen.
Arten der Erwärmung beim Heißpressen
Einführung in drei Arten der Erwärmung: Induktionserwärmung, indirekte Widerstandserwärmung und feldunterstützte Sintertechnik (FAST) / direktes Heißpressen
Heißpressen ist eine in der Fertigungsindustrie weit verbreitete Technik zur Herstellung dauerhafter und fester Verbindungen zwischen Materialien. Dabei handelt es sich um die Kombination zusätzlicher Kräfte beim Sintern von Hochtemperaturmaterialien, entweder im Vakuum oder unter einem Überdruck eines Inertgases. Dieser Druck trägt zu einer stärkeren Verdichtung des Materials bei, was zu einem Materialblock mit Dichten führt, die nahezu theoretisch sind.
Es gibt zwei Haupttypen von Heißpressöfen: solche, die heiße und kalte Stäbe zum Ausüben von Druck verwenden, und solche, die Stempel und Matrizen aus Graphit oder Pressplatten verwenden, um die Kraft beim Diffusionsschweißen auszuüben. Diese Öfen machen den Einsatz von Bindemitteln im Herstellungsprozess überflüssig und sind daher äußerst effizient.
Innerhalb der Heißpresstechnologie gibt es drei verschiedene Arten von Heizmethoden: Induktionserwärmung, indirekte Widerstandserwärmung und feldunterstützte Sintertechnik (FAST)/direktes Heißpressen.
Induktive Erwärmung
Die induktive Erwärmung ist eine häufig verwendete Methode zum Sintern von Metall-, Keramik- und einigen feuerfesten Metallpulvern aus intermetallischen Verbindungen. Dabei wird elektromagnetische Induktion genutzt, um im Material Wärme zu erzeugen.
Dabei wird ein Wechselstrom durch eine Spule geleitet, wodurch ein Magnetfeld entsteht. Dieses Magnetfeld induziert Wirbelströme im Material, die wiederum Wärme erzeugen. Anschließend wird die Hitze genutzt, um das Material zu sintern und die gewünschte Verbindung herzustellen.
Induktive Erwärmung ist für ihre Effizienz und Präzision bekannt. Es ermöglicht schnelle Aufheizraten und eine präzise Kontrolle der Temperaturverteilung, was zu hochwertigen Verbindungen führt. Es eignet sich besonders für Materialien mit hoher elektrischer Leitfähigkeit.
Indirekte Widerstandsheizung
Eine weitere beim Heißpressen häufig verwendete Methode ist die indirekte Widerstandserwärmung. Dabei wird elektrischer Widerstand genutzt, um im Material Wärme zu erzeugen.
Dabei wird ein elektrischer Strom durch das Material geleitet, wodurch Widerstand entsteht und Wärme entsteht. Anschließend wird die Hitze genutzt, um das Material zu sintern und die gewünschte Verbindung herzustellen.
Die indirekte Widerstandsheizung ist für ihre Einfachheit und Vielseitigkeit bekannt. Es kann bei einer Vielzahl von Materialien eingesetzt werden und eignet sich besonders für Materialien mit geringer elektrischer Leitfähigkeit. Es ermöglicht eine präzise Kontrolle der Temperatur und kann hohe Heizraten erzielen.
Field-Assisted Sintering Technique (FAST) / Direktes Heißpressen
Die feldunterstützte Sintertechnik (FAST), auch direktes Heißpressen genannt, ist eine relativ neue Methode des Heißpressens. Dabei wird ein elektrisches Feld zur Unterstützung des Sinterprozesses eingesetzt.
Bei diesem Prozess wird ein elektrischer Strom durch das Material geleitet, wodurch ein elektrisches Feld entsteht. Dieses elektrische Feld erhöht die Beweglichkeit der Atome im Material und ermöglicht so ein beschleunigtes Sintern und Verdichten.
Das FAST-/Direkt-Heißpressen ist für seine Fähigkeit bekannt, hochdichte und gleichmäßige Materialien herzustellen. Es ermöglicht schnelle Sinterraten und kann hohe Dichten nahe der Theorie erreichen. Es eignet sich besonders für Materialien mit geringer Diffusionsfähigkeit und hoher elektrischer Leitfähigkeit.
Zusammenfassend lässt sich sagen, dass das Heißpressen in der Fertigungsindustrie eine wertvolle Technik zur Herstellung dauerhafter und fester Verbindungen zwischen Materialien ist. In der Heißpresstechnologie werden üblicherweise drei Arten von Heizmethoden verwendet: Induktionserwärmung, indirekte Widerstandserwärmung und feldunterstützte Sintertechnik (FAST)/direktes Heißpressen. Jede Methode hat ihre eigenen Vorteile und eignet sich für unterschiedliche Materialien und Anwendungen.
Induktive Erwärmung
Ablauf und Funktionsweise der induktiven Erwärmung
Bei der induktiven Erwärmung werden elektrisch leitende Materialien wie Metalle oder Halbleiter mithilfe elektromagnetischer Induktion erhitzt. Dies wird erreicht, indem ein hochfrequenter Wechselstrom durch einen Elektromagneten geleitet wird, wodurch ein schnell wechselndes Magnetfeld entsteht. Dieses Magnetfeld induziert Wirbelströme im Material, die durch seinen Widerstand fließen und durch Joulesche Erwärmung Wärme erzeugen. In ferromagnetischen und ferrimagnetischen Materialien entsteht auch Wärme durch magnetische Hystereseverluste. Die Frequenz des verwendeten elektrischen Stroms hängt von Faktoren wie der Größe und dem Material des Objekts, der Kopplung zwischen der Arbeitsspule und dem Objekt sowie der Eindringtiefe ab.
Diese Heizmethode wird üblicherweise zum Schmelzen von Metallen und zur Herstellung von Legierungen verwendet. Vakuum-Induktionsschmelzen, das eine kontrollierte Atmosphäre und eine präzise Steuerung des Schmelzprozesses kombiniert, ist eine beliebte Anwendung der induktiven Erwärmung. Induktionsöfen können Temperaturen von 1800 °C oder mehr erreichen und bestehen typischerweise aus einem Kühler, einem Netzteil und einer Vakuumeinheit.
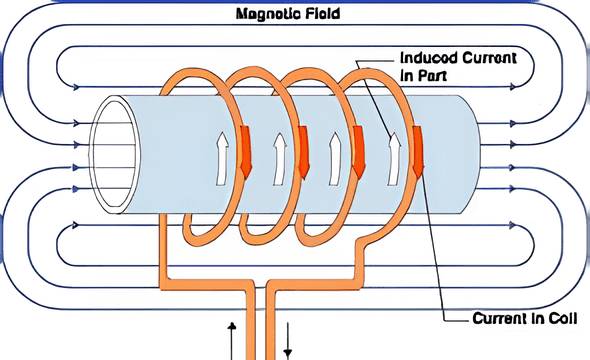
Vor- und Nachteile der induktiven Erwärmung
Die induktive Erwärmung bietet gegenüber anderen Erwärmungsmethoden mehrere Vorteile. Dank des Induktionsprinzips ist es ein schnellerer Prozess im Vergleich zur Elektro- oder Gasheizung. Induktionsöfen zeichnen sich zudem durch eine schnelle Anlaufzeit aus, da kein Aufwärm- oder Abkühlzyklus erforderlich ist. Die Induktionsstromversorgung erzeugt eine starke Rührwirkung, was zu homogenen Mischungen flüssigen Metalls führt. Darüber hinaus benötigen Induktionsöfen im Vergleich zu brennstoffbefeuerten Öfen weniger feuerfeste Materialien. Sie sind energieeffizienter und können den Stromverbrauch beim Schmelzen von Metallen senken. Induktionsöfen sind außerdem kompakt, was eine einfachere Installation ermöglicht und aufgrund kürzerer Schmelzzeiten höhere Produktionsraten ermöglicht.
Allerdings sind auch einige Nachteile zu berücksichtigen. Die Nennleistung von Induktionsöfen spiegelt möglicherweise nicht immer ihre tatsächliche Arbeitsleistung wider, was zu einer verringerten Schmelzeffizienz führt. Es ist wichtig sicherzustellen, dass der Lieferant über eine selbst entwickelte Induktions-Power-Board-Technologie verfügt und flexible, maßgeschneiderte Lösungen anbieten kann. Darüber hinaus kann die Induktionserwärmung Probleme bei der Wärmeverteilung und der Aufheizgeschwindigkeit mit sich bringen, was eine sorgfältige Abwägung der spezifischen Anwendung und des zu erwärmenden Materials erfordert.
Probleme mit der Wärmeverteilung und der Heizrate
Durch Induktionserwärmung können hohe Leistungsdichten erzeugt werden, was kurze Wechselzeiten zum Erreichen der erforderlichen Temperatur ermöglicht. Dies führt zu einer genauen Kontrolle des Heizmusters, das genau dem angelegten Magnetfeld folgt. Diese präzise Steuerung trägt dazu bei, thermische Verformungen und Schäden am erhitzten Material zu reduzieren.
Bei der Induktionserwärmung können jedoch die Wärmeverteilung und die Erwärmungsrate potenzielle Probleme darstellen. Eine ungleichmäßige Wärmeverteilung kann auftreten, wenn die Induktionsspule keinen ordnungsgemäßen Kontakt mit dem Material hat oder wenn das Material eine unregelmäßige Form oder Zusammensetzung aufweist. Es ist wichtig, eine ordnungsgemäße Kopplung zwischen der Arbeitsspule und dem zu erhitzenden Objekt sicherzustellen, um eine gleichmäßige Erwärmung zu erreichen.
Die Aufheizrate kann auch durch Faktoren wie die Größe und das Material des Objekts sowie die Eindringtiefe des elektromagnetischen Feldes beeinflusst werden. Das Verständnis dieser Faktoren und ihrer Auswirkungen auf den Erwärmungsprozess ist entscheidend, um bei Induktionsheizungsanwendungen die gewünschten Ergebnisse zu erzielen.
Insgesamt ist die induktive Erwärmung eine vielseitige und effiziente Methode zur Erwärmung elektrisch leitfähiger Materialien. Seine Vorteile in Bezug auf Geschwindigkeit, Energieeffizienz und Steuerbarkeit machen es zu einer beliebten Wahl in verschiedenen Branchen, darunter Metallurgie, Halbleiterfertigung und Goldguss. Durch die Berücksichtigung der spezifischen Anforderungen und Herausforderungen jeder Anwendung können Unternehmen fundierte Entscheidungen beim Einsatz der induktiven Heiztechnologie treffen.
Indirekte Widerstandsheizung
Indirekte Widerstandsheizung ist eine in Elektroöfen verwendete Technologie, bei der eine Form oder Ladung mithilfe von Graphitheizelementen erhitzt wird. Die Wärme wird erzeugt, indem ein elektrischer Strom durch diese Elemente geleitet wird, die die Wärme dann durch Konvektion an die Form übertragen. Dieser Vorgang wird als indirekte Widerstandserwärmung bezeichnet.
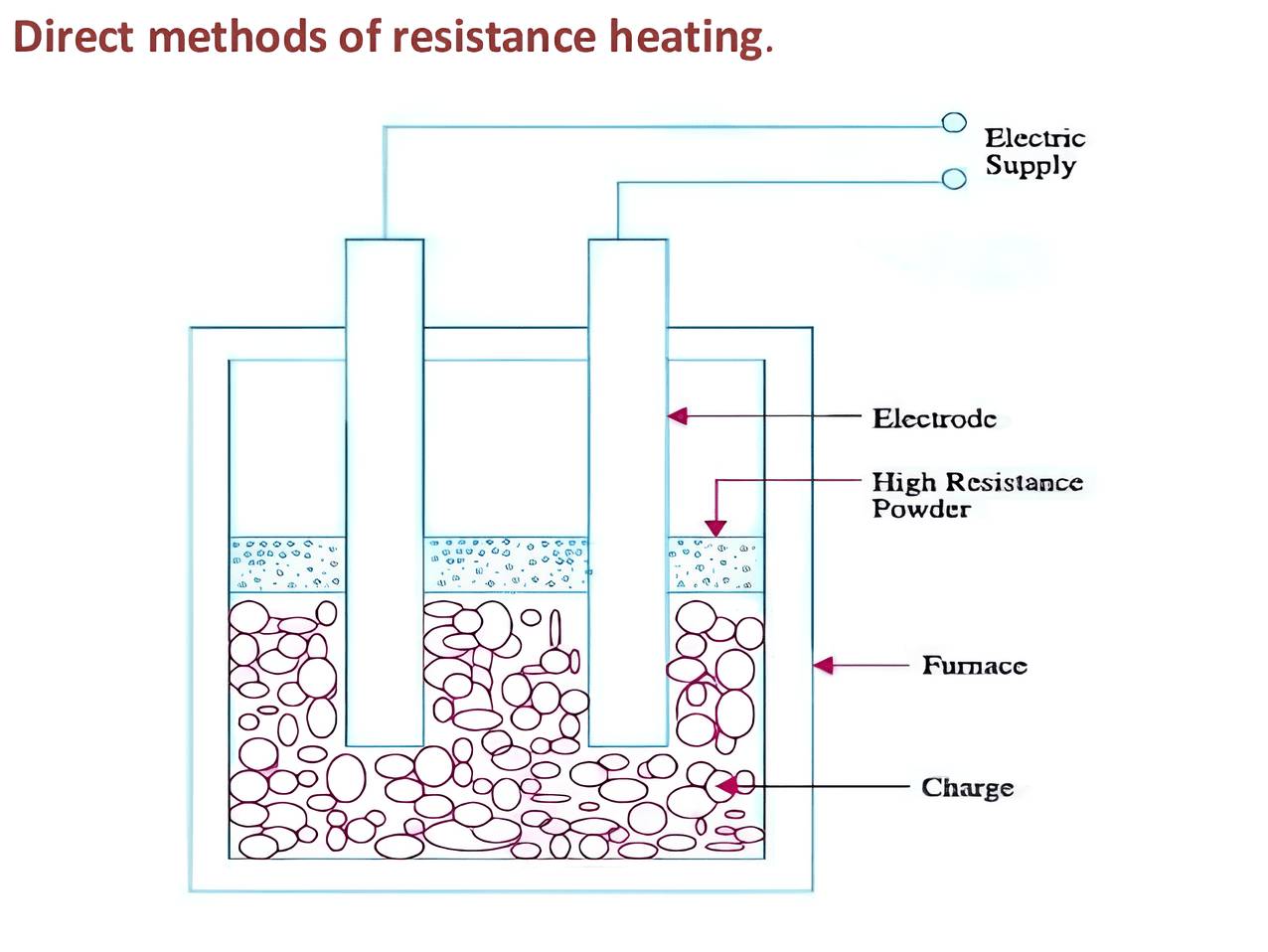
Ablauf und Funktionsweise der indirekten Widerstandsheizung
Bei der indirekten Widerstandsheizung wird die Form in eine Heizkammer gestellt, in der sich Graphitheizelemente befinden. Diese Elemente werden durch den durch sie fließenden elektrischen Strom erhitzt. Die von den Heizelementen erzeugte Wärme wird dann durch Konvektion auf die Form übertragen, was zu einer Erwärmung der Form führt.
Vor- und Nachteile der indirekten Widerstandsheizung
Einer der Vorteile der indirekten Widerstandsheizung ist die Möglichkeit, hohe Temperaturen zu erreichen. Die erreichte Temperatur ist unabhängig von der Leitfähigkeit der Form und wird nicht durch Hitze und Druck beeinflusst. Ein Hauptnachteil der indirekten Widerstandsheizung ist jedoch die Zeit, die zum Aufheizen der Form benötigt wird. Die Wärmeübertragung von der Ofenatmosphäre zur Formoberfläche und über den gesamten Querschnitt der Form ist relativ langsam.
Geschichte und aktuelles Interesse an Widerstandsheizungen
Widerstandsheizungen werden seit vielen Jahren in verschiedenen Anwendungen eingesetzt. Es wird häufig in Haushaltsgeräten wie Elektroherden und Toastern verwendet. In den letzten Jahren besteht ein wachsendes Interesse an Widerstandsheizungen für industrielle Anwendungen, beispielsweise in der Heißpresstechnik. Induktionserwärmung und feldunterstützte Sintertechnik (FAST) / direktes Heißpressen sind weitere Erwärmungsmethoden, die in Verbindung mit der Widerstandserwärmung eingesetzt werden.
Widerstandsheizelemente wie Widerstandsdrähte oder -bänder werden häufig in verschiedenen Heizgeräten und Industrieöfen verwendet. Diese Elemente wandeln elektrische Energie durch Joulesche Erwärmung in Wärme um. Der Widerstand, auf den der durch das Element fließende elektrische Strom trifft, führt zu einer Erwärmung des Elements.
Zusammenfassend lässt sich sagen, dass es sich bei der indirekten Widerstandsheizung um eine Technologie handelt, die Graphitheizelemente verwendet, um eine Form oder Ladung durch Konvektion zu erhitzen. Es bietet Vorteile wie hohe erreichbare Temperaturen, unabhängig von Formleitfähigkeit und Hitze/Druck. Allerdings hat es den Nachteil, dass die Wärmeübertragung relativ langsam ist. Widerstandsheizelemente, beispielsweise Widerstandsdrähte, werden häufig in verschiedenen Heizgeräten und Industrieöfen verwendet.
Field Assisted Sintering Technique (FAST) / Direktes Heißpressen
Konzept und Umsetzung von FAST
Die feldunterstützte Sintertechnologie/Funken-Plasma-Sintern (FAST/SPS) nutzt einen elektrischen Gleichstrom, um die Form und/oder die Probe durch Joule-Heizung direkt zu erhitzen. Durch diese direkte Erwärmung können hohe Aufheizraten und kurze Bearbeitungszykluszeiten erreicht werden. Es ermöglicht auch die Konsolidierung einer breiten Palette metallischer, keramischer und funktionaler Materialien. FAST/SPS bietet neue Möglichkeiten zur Herstellung von Materialien mit potenziell außergewöhnlichen Eigenschaften. Es können auch Multimaterial-Verbundwerkstoffe, funktionale Materialien und Diffusionsverbundmaterialien verarbeitet werden.
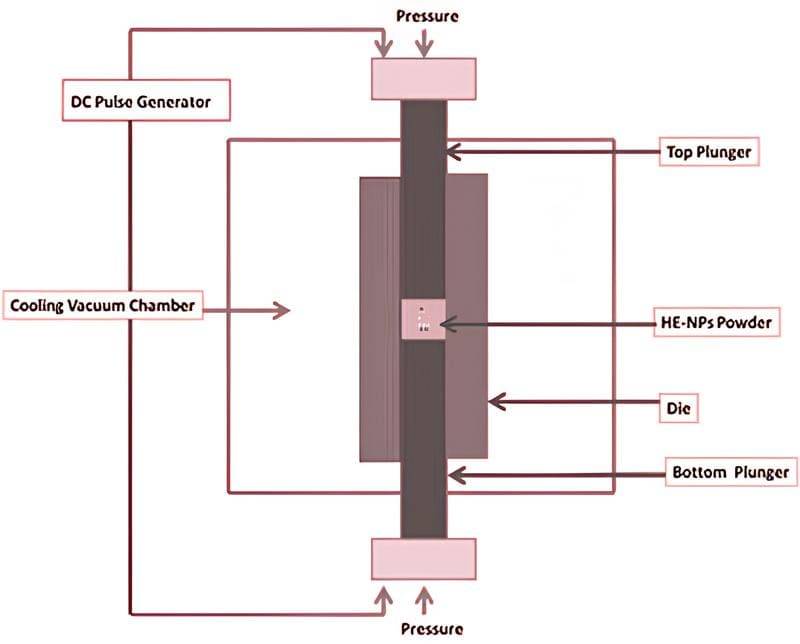
Gründe für die Verkürzung der Zykluszeit
Der zwingende Grund für die Verkürzung der Zykluszeit beim direkten Heißpressen ist die Vermeidung von Kornwachstum und die Einsparung von Energie. Beim direkten Heißpressen ist die Form direkt an den Strom angeschlossen und erzeugt durch den spezifischen Widerstand der Form und des Pulverteils Wärme in der Form. Dies führt zu sehr hohen Aufheizraten und erhöht die Sinteraktivität feiner Metallpulveraggregate deutlich. Kurze Zykluszeiten von wenigen Minuten werden möglich, und das Verfahren senkt die Schwellentemperatur und den Sinterdruck im Vergleich zu herkömmlichen Sintertechniken. Die direkte Widerstandsheizung sorgt dafür, dass die Wärme dort entsteht, wo sie benötigt wird.
Vorteile des direkten Heißpressens
Das direkte Heißpressen bietet im Vergleich zu herkömmlichen pulvermetallurgischen Sintertechniken mehrere Vorteile. Es ermöglicht die Herstellung einzigartiger Eigenschaften durch niedrigere Verarbeitungstemperaturen und/oder kürzere Verarbeitungszeiten. Es ermöglicht das Heißpresssintern von Metall- und Keramikpulvern, die Herstellung von Keramik-/Metall-Verbundwerkstoffen und intermetallischen Verbindungen sowie die Forschung und Entwicklung von Diffusionsschweißverfahren. Es erleichtert auch das Verdichtungs-Heißpresssintern von Sauerstoff-/Stickstoff-/Bor-/Kohlenstoffverbindungen und deren Mischungen.
Unterschiede zwischen Sintern mit gepulstem oder ungepulstem Strom
Aktuelle Forschungsergebnisse deuten darauf hin, dass es keinen grundsätzlichen Unterschied zwischen dem Sintern mit gepulstem oder ungepulstem Strom (SPS oder FAST) gibt. Prinzipiell lassen sich mit allen Techniken des direkten Heißpressens im Vergleich zum konventionellen Heißpressen verbesserte Sinterergebnisse erzielen, wenn die Verbesserung nur auf der In-situ-Erwärmung des Pulvers beruht. Wenn jedoch zusätzliche physikalische Effekte vorliegen, die mit der elektrischen Stromdichte selbst verbunden sind, hat ein gepulster Strom häufig zusätzliche positive Auswirkungen. Denn bei jedem Impuls erreicht die elektrische Stromdichte einen deutlich höheren Wert als ein Gleichstrom mit vergleichbarer Heizleistung.
Zusammenfassend lässt sich sagen, dass die Field Assisted Sintering Technique (FAST) oder das direkte Heißpressen mit elektrischem Gleichstrom zahlreiche Vorteile im Hinblick auf kürzere Verarbeitungszykluszeiten, niedrigere Temperaturen und Drücke sowie die Möglichkeit bietet, einzigartige Eigenschaften in einer Vielzahl von Materialien zu erzeugen. Unabhängig davon, ob gepulster oder ungepulster Strom verwendet wird, können mit der direkten Heißpresstechnik im Vergleich zu herkömmlichen Methoden verbesserte Sinterergebnisse erzielt werden.
Anwendungen des Heißpressens
Herstellung kritischer Artikel wie Sputtertargets und Hochleistungskeramikkomponenten
Die Heißpresstechnologie wird erfolgreich bei der Herstellung kritischer Artikel wie Sputtertargets und Hochleistungskeramikkomponenten eingesetzt. Mit diesem Verfahren wurden Materialien wie Borcarbid, Titandiborid und Sialon hergestellt. Durch die Verwendung von Metallpulver ermöglicht die Leitfähigkeit der Form eine schnelle Erwärmung des Werkstücks. Diese Methode eignet sich besonders für Anwendungen, die hohe Aufheizraten erfordern, und ist daher ideal für Materialien, die nur kurzzeitig auf hohen Temperaturen gehalten werden können, oder für Prozesse, die schnelle Aufheizraten für eine hohe Produktivität erfordern.
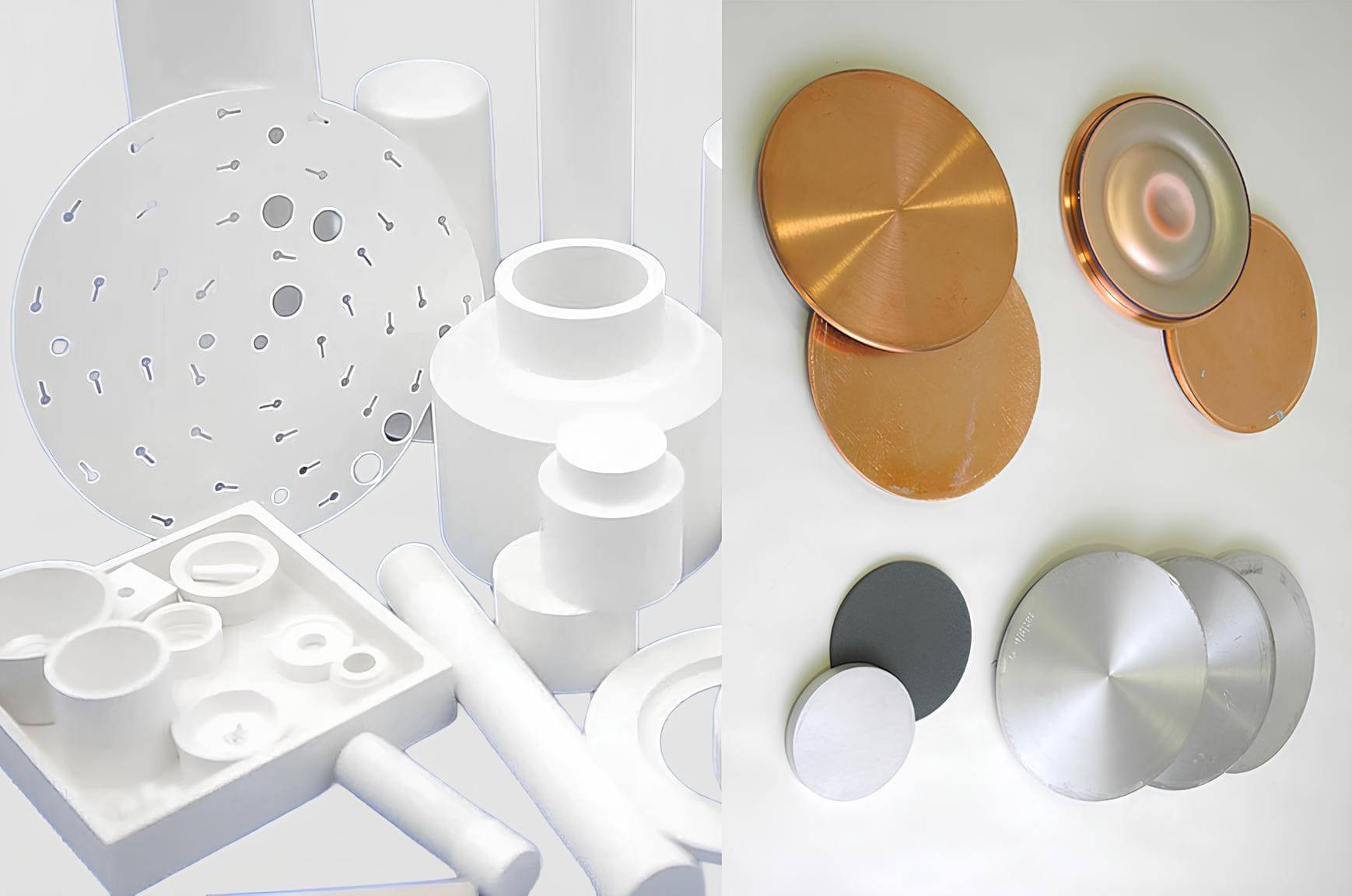
Vorteile der Verwendung von Metallpulver
Einer der Vorteile der Verwendung von Metallpulver im Heißpressverfahren besteht darin, dass es eine schnelle Erwärmung des Werkstücks ermöglicht. Formen mit großem Durchmesser und relativ geringer Höhe können schnell erhitzt werden, was zu einer höheren Effizienz und Produktivität führt. Darüber hinaus macht die Verwendung von Metallpulver den Einsatz von Bindemitteln im Herstellungsprozess überflüssig, sodass eine vollständige Verbindung der Teile mithilfe einer Kombination aus Kraft und Temperatur möglich ist.
Eignung des Verfahrens für hohe Aufheizraten
Das Heißpressverfahren eignet sich besonders für Anwendungen, die hohe Heizraten erfordern. Dies ist von Vorteil für Materialien, die nur kurzzeitig auf hohen Temperaturen gehalten werden können, oder für Prozesse, die schnelle Aufheizraten erfordern, um eine hohe Produktivität zu erreichen. Die Kombination aus Kraft und Temperatur beim Heißpressen ermöglicht eine schnelle und effiziente Verbindung der Teile.
Rolle des direkten Heißpressens in der Reibmaterialindustrie
Die Technologie des direkten Heißpressens spielt in der Reibmaterialindustrie eine bedeutende Rolle. Es ermöglicht das Sintern von Materialien auf ihre endgültige Dichte und erreicht so ein hohes Maß an endkonturnaher Präzision. Diese Präzision macht eine mechanische Nachbearbeitung schwer zu bearbeitender Materialien oft überflüssig. Das direkte Heißpressen eignet sich besonders für Materialien, die ein hohes Maß an Dichte und Präzision in der Endform erfordern.
Anwendungen von gesinterten Bremsbelägen und Kupplungsscheiben
Heißpressen wird häufig bei der Herstellung von gesinterten Bremsbelägen und Kupplungsscheiben eingesetzt. Der Prozess ermöglicht die Herstellung dichter und leistungsstarker Materialien, die hervorragende Brems- und Kupplungseingriffseigenschaften bieten. Gesinterte Bremsbeläge und Kupplungsscheiben sind für ihre Haltbarkeit, Hitzebeständigkeit und konstante Leistung bekannt und werden daher in der Automobilindustrie sehr geschätzt.
Zusammenfassend lässt sich sagen, dass das Heißpressen ein vielseitiges und wertvolles Verfahren ist, das in verschiedenen Branchen Anwendung findet. Es ist besonders nützlich bei der Herstellung kritischer Artikel wie Sputtertargets und Hochleistungskeramikkomponenten. Die Verwendung von Metallpulver beim Heißpressen bietet Vorteile wie schnelles Erhitzen und Eliminierung von Bindemitteln. Das Verfahren eignet sich für hohe Aufheizraten und spielt eine bedeutende Rolle in der Reibmaterialindustrie. Darüber hinaus wird Heißpressen häufig bei der Herstellung von gesinterten Bremsbelägen und Kupplungsscheiben eingesetzt und sorgt für überlegene Leistung und Haltbarkeit in Automobilanwendungen.
Kontaktieren Sie uns für eine kostenlose Beratung
Die Produkte und Dienstleistungen von KINTEK LAB SOLUTION werden von Kunden auf der ganzen Welt anerkannt. Unsere Mitarbeiter helfen Ihnen gerne bei allen Fragen weiter. Kontaktieren Sie uns für eine kostenlose Beratung und sprechen Sie mit einem Produktspezialisten, um die am besten geeignete Lösung für Ihre Anwendungsanforderungen zu finden!