Die Sintertemperatur spielt eine entscheidende Rolle bei der Bestimmung der Dichte eines Materials, da sie den Grad der Partikelbindung und die Verringerung der Porosität direkt beeinflusst.Bei optimalen Sintertemperaturen verbinden sich die Partikel effektiv, was zu einer höheren Dichte und besseren mechanischen Eigenschaften führt.Abweichungen von diesem optimalen Bereich - entweder zu hoch oder zu niedrig - können sich jedoch negativ auf die Dichte und die Gesamtleistung des Materials auswirken.Hohe Temperaturen können übermäßiges Kornwachstum oder Defekte verursachen, während niedrige Temperaturen zu unzureichender Bindung und erhöhter Porosität führen können.Das Verständnis des Verhältnisses zwischen Sintertemperatur und Dichte ist für das Erreichen der gewünschten Materialeigenschaften bei Keramik und Metallen von entscheidender Bedeutung.
Die wichtigsten Punkte werden erklärt:
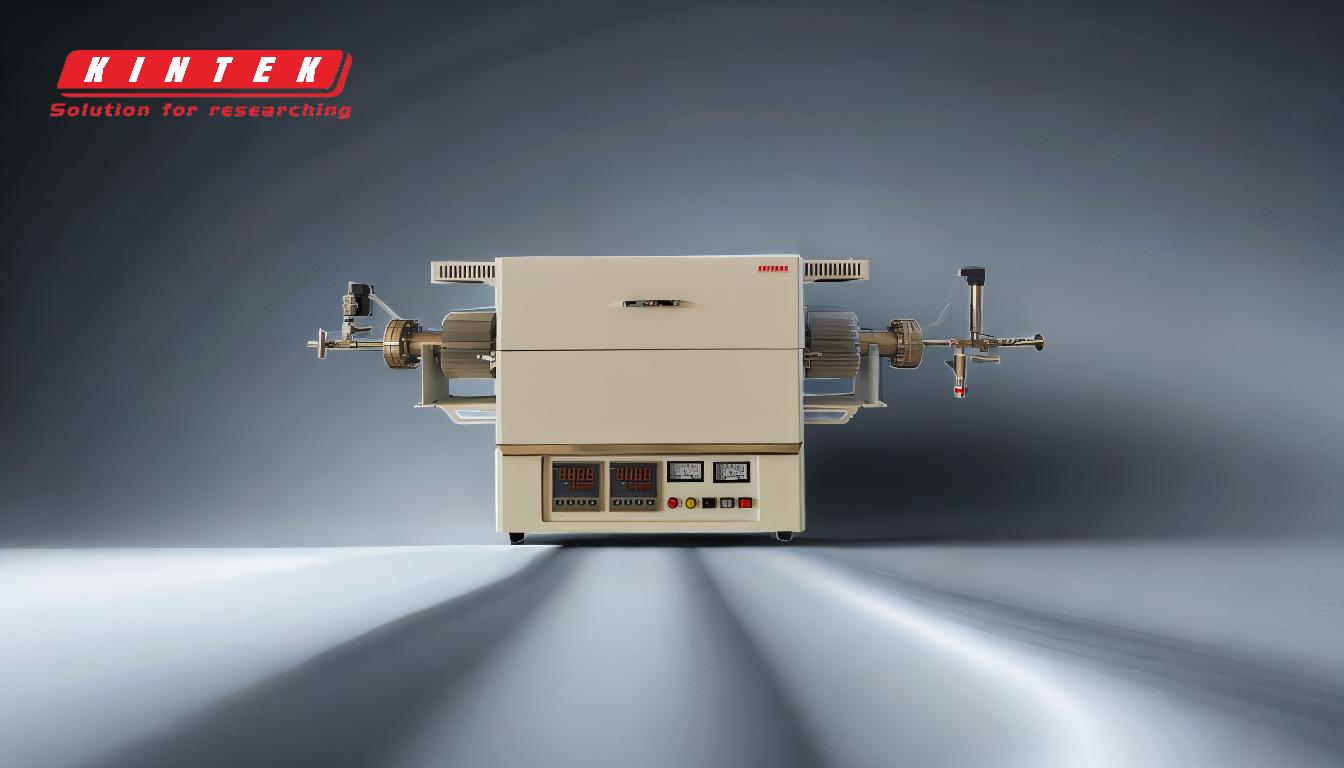
-
Optimale Sintertemperatur und Dichte:
- Die Sintertemperatur muss sorgfältig kontrolliert werden, um die gewünschte Dichte zu erreichen.Bei der optimalen Temperatur verbinden sich die Partikel effektiv, wodurch die Porosität verringert und die Dichte erhöht wird.
- Studien über Zirkoniumdioxid zeigen beispielsweise, dass die Festigkeit und Dichte beim Sintern bei etwa 1500℃ maximiert werden.Abweichungen von dieser Temperatur können zu einer verminderten Dichte aufgrund von unsachgemäßer Bindung oder übermäßigem Kornwachstum führen.
-
Auswirkungen von hohen Sintertemperaturen:
- Zu hohe Sintertemperaturen können zu einer Übersinterung führen, die Defekte wie Kornvergröberung oder Rissbildung verursachen kann.Diese Defekte erhöhen die Porosität und verringern die Dichte.
- Hohe Temperaturen können auch zur Verdampfung flüchtiger Bestandteile oder zu unerwünschten Phasenumwandlungen führen, was die Materialeigenschaften weiter verschlechtert.
-
Auswirkungen von niedrigen Sintertemperaturen:
- Unzureichende Sintertemperaturen führen zu einer unvollständigen Partikelbindung, was zu Restporosität und geringerer Dichte führt.
- Niedrige Temperaturen können auch verhindern, dass das Material sein volles mechanisches Potenzial erreicht, da die Bindungen zwischen den Partikeln nicht stark genug sind, um die gewünschten Eigenschaften zu unterstützen.
-
Die Rolle der Sinterzeit:
- Die Sinterzeit ist eng mit der Temperatur verbunden.Längere Sinterzeiten bei angemessenen Temperaturen können die Dichte erhöhen, da mehr Zeit für die Partikelbindung und Porenbeseitigung zur Verfügung steht.
- Übermäßig lange Sinterzeiten bei hohen Temperaturen können jedoch zu Übersinterung und Defekten führen, während eine unzureichende Zeit bei niedrigen Temperaturen möglicherweise keine ordnungsgemäße Verdichtung ermöglicht.
-
Materialspezifische Überlegungen:
- Verschiedene Werkstoffe haben unterschiedliche Sintertemperaturbereiche.Zirkoniumdioxid beispielsweise erreicht seine optimale Dichte bei etwa 1500℃, während für andere Materialien höhere oder niedrigere Temperaturen erforderlich sein können.
- Das Verständnis des spezifischen Sinterverhaltens eines Materials ist entscheidend für das Erreichen der gewünschten Dichte und mechanischen Eigenschaften.
-
Praktische Auswirkungen für Einkäufer von Anlagen und Verbrauchsmaterialien:
- Bei der Auswahl von Sinteranlagen ist darauf zu achten, dass das System eine präzise Temperaturregelung innerhalb des für das zu verarbeitende Material optimalen Bereichs ermöglicht.
- Verbrauchsmaterialien wie Sinteröfen und Temperatursensoren sollten nach ihrer Fähigkeit ausgewählt werden, konsistente und genaue Temperaturprofile zu liefern.
- Die Überwachung und Steuerung von Sinterparametern, einschließlich Temperatur und Zeit, ist für die Herstellung von Bauteilen mit hoher Dichte und gleichbleibender Qualität unerlässlich.
Durch eine sorgfältige Steuerung der Sintertemperatur und -zeit können die Hersteller die gewünschte Dichte und die gewünschten Materialeigenschaften erreichen und sicherstellen, dass das Endprodukt den Leistungsanforderungen entspricht.
Zusammenfassende Tabelle:
Schlüsselfaktor | Einfluss auf die Dichte |
---|---|
Optimale Sintertemperatur | Maximiert die Dichte, indem sie eine effektive Partikelbindung und Porositätsreduzierung ermöglicht. |
Hohe Sintertemperaturen | Verursacht Defekte wie Kornvergröberung, erhöhte Porosität und geringere Dichte. |
Niedrige Sintertemperaturen | Führt zu einer unvollständigen Bindung und hinterlässt Restporosität und geringere Dichte. |
Sinterzeit | Längere Zeiten bei optimalen Temperaturen erhöhen die Dichte; falsche Zeiten führen zu Defekten. |
Materialspezifische Erfordernisse | Verschiedene Werkstoffe erfordern für eine optimale Dichte bestimmte Temperaturbereiche (z. B. Zirkoniumdioxid bei 1500℃). |
Erzielen Sie die perfekten Sinterergebnisse für Ihre Materialien. Kontaktieren Sie noch heute unsere Experten für maßgeschneiderte Lösungen!