Die chemische Abscheidung und die physikalische Abscheidung sind zwei unterschiedliche Verfahren, die bei der Herstellung dünner Schichten zum Einsatz kommen und jeweils ihre eigenen Prozesse, Vorteile und Grenzen haben.Die chemische Abscheidung, z. B. die chemische Gasphasenabscheidung (CVD), beruht auf chemischen Reaktionen zur Bildung dünner Schichten, die oft hohe Temperaturen erfordern und zu Verunreinigungen führen können.Im Gegensatz dazu wird bei der physikalischen Abscheidung, z. B. der physikalischen Gasphasenabscheidung (PVD), das Material physikalisch auf ein Substrat übertragen, in der Regel bei niedrigeren Temperaturen und ohne korrosive Nebenprodukte.Das Verständnis dieser Unterschiede ist entscheidend für die Auswahl des geeigneten Verfahrens auf der Grundlage der gewünschten Schichteigenschaften, der Substratkompatibilität und der Anwendungsanforderungen.
Die wichtigsten Punkte werden erklärt:
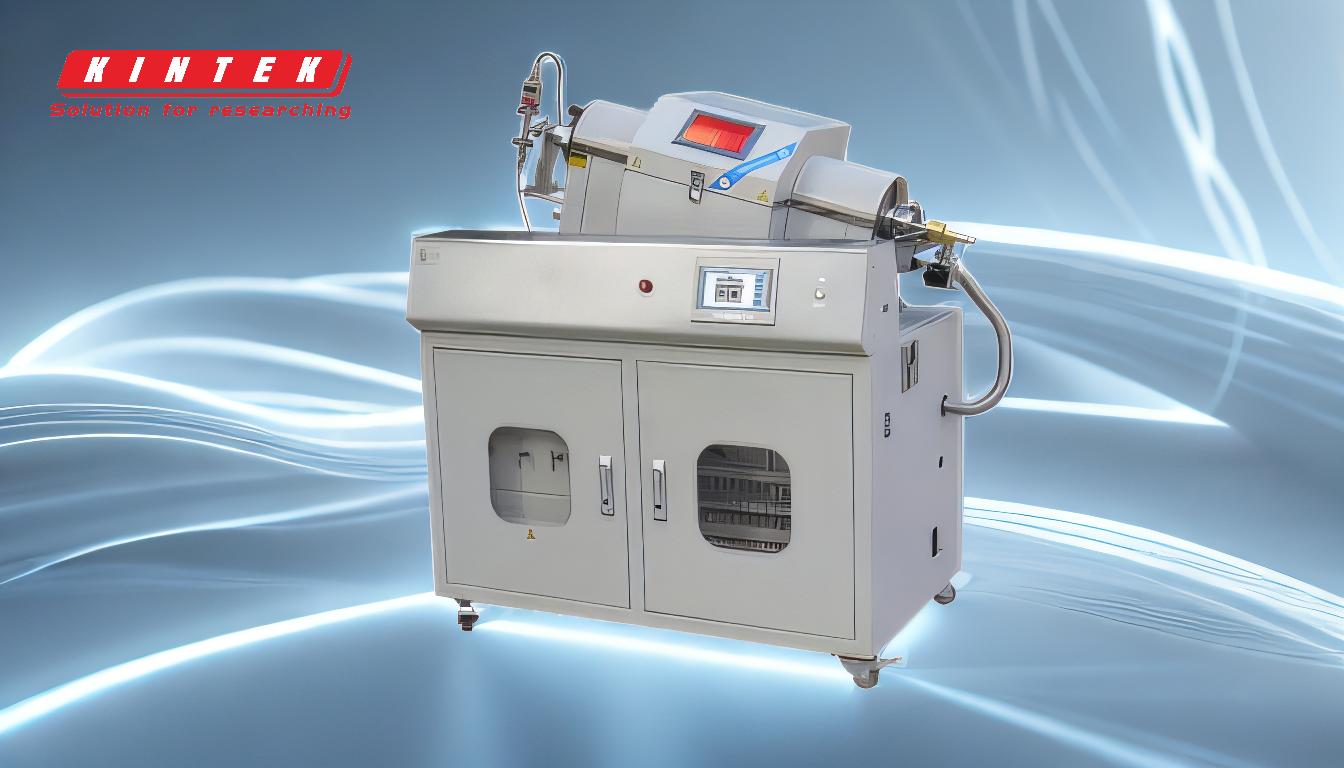
-
Prozessmechanismen:
-
Chemische Abscheidung (CVD):
- Es handelt sich um chemische Reaktionen zwischen gasförmigen Vorläufern, die einen festen Film auf dem Substrat bilden.
- Erfordert hohe Temperaturen zur Aktivierung der chemischen Reaktionen, was häufig zur Bildung korrosiver gasförmiger Nebenprodukte führt.
- Beispiele sind thermische CVD, plasmaunterstützte CVD (PECVD) und Atomlagenabscheidung (ALD).
-
Physikalische Abscheidung (PVD):
- Physikalische Übertragung des Materials von einer Quelle (z. B. Sputtern oder Verdampfen) auf das Substrat.
- Sie beruht nicht auf chemischen Reaktionen und ermöglicht die Abscheidung bei niedrigeren Temperaturen.
- Beispiele sind Sputtern, Verdampfen und physikalische Dampfabscheidung mit Elektronenstrahlen (EBPVD).
-
Chemische Abscheidung (CVD):
-
Anforderungen an die Temperatur:
-
CVD:
- In der Regel sind hohe Temperaturen (oft über 500 °C) erforderlich, um chemische Reaktionen und das Filmwachstum zu erleichtern.
- Hohe Temperaturen können die Arten von Substraten, die verwendet werden können, einschränken, da sich einige Materialien unter solchen Bedingungen zersetzen oder verziehen können.
-
PVD:
- Kann bei viel niedrigeren Temperaturen durchgeführt werden und eignet sich daher für hitzeempfindliche Substrate.
- Niedrigere Temperaturen verringern auch das Risiko einer Beschädigung oder Verformung des Substrats.
-
CVD:
-
Filmreinheit und Verunreinigungen:
-
CVD:
- Durch die chemischen Reaktionen können Verunreinigungen in den Film gelangen, insbesondere wenn die Ausgangsstoffe oder Reaktionsbedingungen nicht sorgfältig kontrolliert werden.
- Es können auch korrosive Nebenprodukte entstehen, die zusätzliche Maßnahmen zur Abfallentsorgung und zur Gewährleistung der Sicherheit erfordern.
-
PVD:
- Erzeugt im Allgemeinen Filme mit höherer Reinheit, da das Verfahren auf physikalischer Übertragung und nicht auf chemischen Reaktionen beruht.
- Es fallen keine korrosiven Nebenprodukte an, was die Abfallentsorgung vereinfacht und Sicherheitsbedenken verringert.
-
CVD:
-
Ablagerungsraten:
-
CVD:
- Im Vergleich zu PVD bietet es in der Regel höhere Abscheideraten und eignet sich daher für Anwendungen, die dicke Schichten erfordern.
- Die Rate kann jedoch je nach CVD-Technik und Prozessparametern variieren.
-
PVD:
- Im Allgemeinen sind die Abscheideraten niedriger, obwohl Techniken wie EBPVD Raten von 0,1 bis 100 μm/min erreichen können.
- Die niedrigeren Raten werden häufig durch die Fähigkeit ausgeglichen, hochwertige, gleichmäßige Schichten zu erzeugen.
-
CVD:
-
Effizienz der Materialverwendung:
-
CVD:
- Die Effizienz der Materialausnutzung kann aufgrund der Bildung von Nebenprodukten und der möglichen Verschwendung von Vorläufergasen geringer sein.
-
PVD:
- Verfahren wie EBPVD bieten eine sehr hohe Materialausnutzung, was sie für bestimmte Anwendungen kostengünstig macht.
-
CVD:
-
Anwendungen:
-
CVD:
- Wird häufig bei der Halbleiterherstellung, der Beschichtung von Werkzeugen und der Herstellung dünner Schichten für optische und elektronische Geräte verwendet.
- Geeignet für Anwendungen, die hohe Temperaturstabilität und komplexe chemische Zusammensetzungen erfordern.
-
PVD:
- Weit verbreitet bei der Herstellung von dünnen Schichten für die Mikroelektronik, Optik und dekorative Beschichtungen.
- Ideal für Anwendungen, die hochreine Schichten und Kompatibilität mit hitzeempfindlichen Substraten erfordern.
-
CVD:
Durch die Kenntnis dieser Hauptunterschiede können Käufer von Anlagen und Verbrauchsmaterialien fundierte Entscheidungen darüber treffen, welche Beschichtungsmethode am besten für ihre spezifischen Anforderungen geeignet ist, wobei Faktoren wie Temperaturanforderungen, Schichtreinheit, Beschichtungsraten und Materialeffizienz berücksichtigt werden müssen.
Zusammenfassende Tabelle:
Aspekt | Chemische Abscheidung (CVD) | Physikalische Abscheidung (PVD) |
---|---|---|
Prozess-Mechanismus | Beruht auf chemischen Reaktionen zwischen gasförmigen Ausgangsstoffen zur Bildung eines festen Films auf dem Substrat. | Beinhaltet die physikalische Übertragung von Material von einer Quelle auf das Substrat (z. B. Sputtern). |
Temperatur | Hohe Temperaturen (oft >500°C) erforderlich, was die Substratverträglichkeit einschränkt. | Niedrigere Temperaturen, geeignet für hitzeempfindliche Substrate. |
Reinheit des Films | Mögliche Verunreinigungen durch chemische Reaktionen; es können sich korrosive Nebenprodukte bilden. | Filme mit höherer Reinheit; keine korrosiven Nebenprodukte. |
Abscheideraten | Höhere Raten, geeignet für dicke Schichten. | Niedrigere Raten, erzeugt aber hochwertige, gleichmäßige Filme. |
Materialeffizienz | Geringerer Wirkungsgrad aufgrund von Nebenprodukten und verschwendeten Vorläufergasen. | Hoher Wirkungsgrad, insbesondere bei Verfahren wie EBPVD. |
Anwendungen | Halbleiterherstellung, Werkzeugbeschichtungen, optische/elektronische Geräte. | Mikroelektronik, Optik, dekorative Beschichtungen und hitzeempfindliche Substrate. |
Benötigen Sie Hilfe bei der Auswahl der richtigen Beschichtungsmethode für Ihre Anwendung? Kontaktieren Sie noch heute unsere Experten !