Die PVD-Beschichtung (Physical Vapour Deposition) wird durch einen streng kontrollierten und präzisen Prozess aufgebracht, bei dem ein Zielmaterial verdampft und auf einem Substrat abgeschieden wird, um eine dünne, haltbare und leistungsstarke Beschichtung zu bilden. Der Prozess wird in einer Vakuumkammer durchgeführt, um Reinheit und Präzision zu gewährleisten. Zu den wichtigsten Schritten gehören die Reinigung und Vorbehandlung des Substrats, das Verdampfen des Targetmaterials mithilfe von Methoden wie Sputtern oder Elektronenbeschuss, der Transport der verdampften Atome zum Substrat und deren Abscheidung, um einen gleichmäßigen Film zu erzeugen. Faktoren wie Oberflächenreinheit, Vorbehandlung und Vakuumbedingungen sind entscheidend für die Erzielung der gewünschten Beschichtungseigenschaften, einschließlich Haftung, Härte und Korrosionsbeständigkeit.
Wichtige Punkte erklärt:
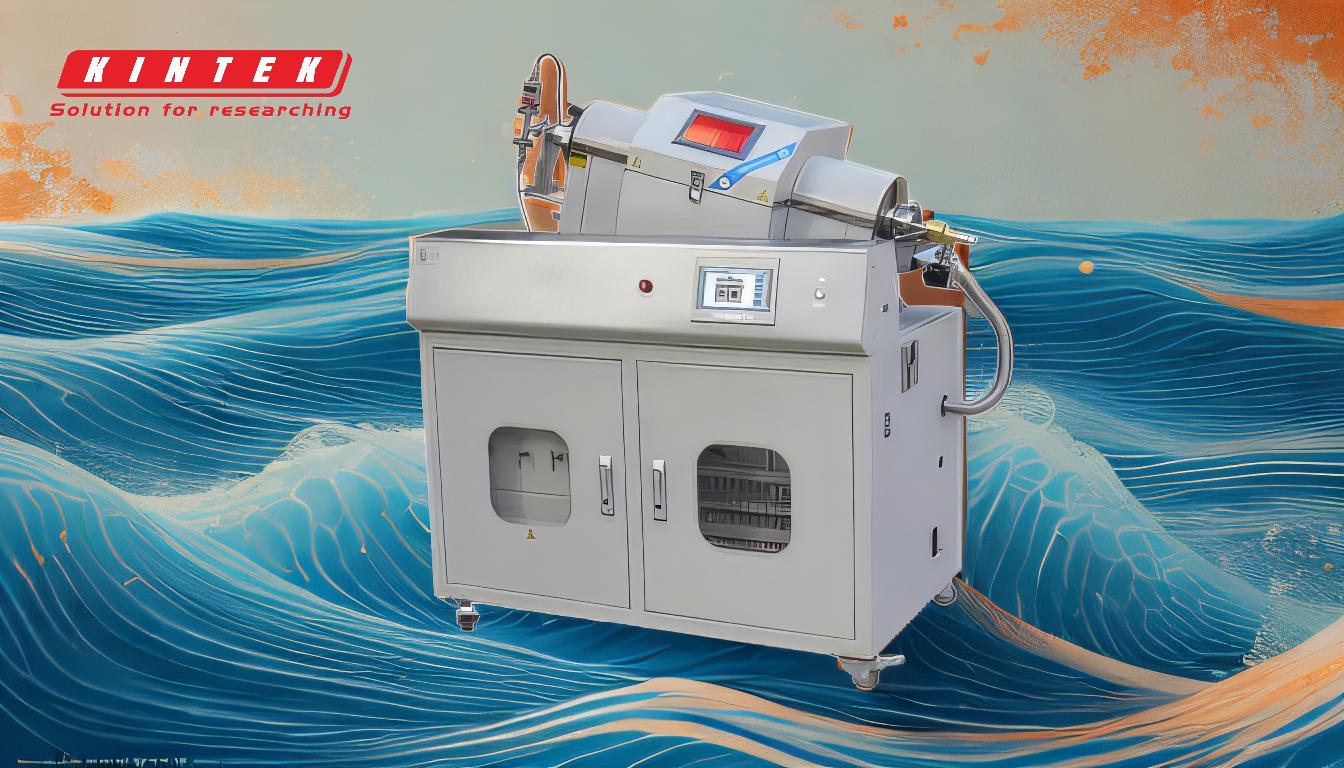
-
Reinigung und Vorbehandlung:
- Bevor der PVD-Prozess beginnt, muss das Substrat einer gründlichen Reinigung unterzogen werden, um Verunreinigungen wie Öle, Schmierstoffe und Kühlemulsionen zu entfernen. Dies erfolgt typischerweise durch Ultraschallreinigung, Spülung und Trocknung.
- Um die Haftung der Beschichtung auf dem Untergrund zu verbessern, wird häufig eine Vorbehandlung wie Oberflächenaktivierung oder Aufrauen durchgeführt. Dieser Schritt stellt sicher, dass die Beschichtung fest und gleichmäßig haftet.
-
Einrichtung der Vakuumkammer:
- Der PVD-Prozess findet in einer Hochvakuumkammer statt, um Verunreinigungen zu beseitigen und eine kontrollierte Umgebung zu schaffen. Das Vakuum verhindert eine Kontamination und stellt sicher, dass das verdampfte Material ungehindert zum Substrat gelangen kann.
- Das Zielmaterial, das die Beschichtung bilden wird, wird in die Kammer eingebracht. Dieses Material kann je nach den gewünschten Eigenschaften der Beschichtung ein Edelmetall oder eine Kombination aus Metallen und reaktiven Gasen sein.
-
Verdampfung des Zielmaterials:
- Das Targetmaterial wird mit Methoden wie Sputtern, Elektronenstrahlbeschuss oder thermischer Verdampfung verdampft. Beim Sputtern bombardiert eine Plasmaentladung das Targetmaterial, wodurch Atome herausgeschleudert und verdampft werden.
- Die verdampften Atome werden dann durch die Vakuumkammer zum Substrat transportiert. In einigen Fällen reagieren diese Atome mit in die Kammer eingeführten Gasen und bilden Verbindungen mit spezifischen Eigenschaften.
-
Ablagerung auf dem Substrat:
- Die verdampften Atome kondensieren auf dem Substrat und bilden einen dünnen, gleichmäßigen Film. Dieser Schritt wird streng kontrolliert, um die gewünschte Dicke, Dichte und Struktur der Beschichtung sicherzustellen.
- Der Sichtliniencharakter des Verfahrens bedeutet, dass die Beschichtung direkt auf Oberflächen aufgetragen wird, die dem Zielmaterial zugewandt sind, was eine sorgfältige Positionierung des Substrats erfordert.
-
Qualitätskontrolle und Endbearbeitung nach der Abscheidung:
- Nach der Abscheidung wird das beschichtete Substrat einer Qualitätskontrolle unterzogen, um sicherzustellen, dass die Beschichtung Spezifikationen für Eigenschaften wie Härte, Haftung und Korrosionsbeständigkeit erfüllt.
- Zusätzliche Endbearbeitungsschritte wie Polieren oder Oberflächenbehandlungen können angewendet werden, um das Aussehen oder die Leistung der Beschichtung zu verbessern.
-
Vorteile der PVD-Beschichtung:
- PVD-Beschichtungen sind für ihre Haltbarkeit, Abriebfestigkeit und Fähigkeit zur Reibungsreduzierung bekannt. Sie verbessern außerdem die Oxidationsbeständigkeit und können die Härte des Untergrunds erhöhen.
- Das Verfahren ermöglicht eine präzise Kontrolle der Eigenschaften der Beschichtung und eignet sich daher für Anwendungen in Branchen wie der Luft- und Raumfahrt, der Automobilindustrie und der Medizintechnik.
Durch die Befolgung dieser Schritte wird die PVD-Beschichtung aufgetragen, um Hochleistungsbeschichtungen zu schaffen, die strenge Qualitäts- und Leistungsanforderungen erfüllen. Die Präzision und Vielseitigkeit des Verfahrens machen es zur bevorzugten Wahl für Anwendungen, die dauerhafte und funktionelle Oberflächenbehandlungen erfordern.
Übersichtstabelle:
Schritt | Beschreibung |
---|---|
Reinigung und Vorbehandlung | Der Untergrund wird gereinigt und vorbehandelt, um eine starke Haftung und Gleichmäßigkeit zu gewährleisten. |
Einrichtung der Vakuumkammer | Der Prozess findet in einer Hochvakuumkammer statt, um Kontaminationen und Verunreinigungen zu verhindern. |
Verdampfung | Das Targetmaterial wird durch Sputtern oder Elektronenstrahlverfahren verdampft. |
Ablagerung | Verdampfte Atome kondensieren auf dem Substrat und bilden einen dünnen, gleichmäßigen Film. |
Qualitätskontrolle | Der beschichtete Untergrund wird auf Härte, Haftung und Korrosionsbeständigkeit geprüft. |
Vorteile | Langlebige, abriebfeste und oxidationsbeständige Beschichtungen für verschiedene Branchen. |
Entdecken Sie, wie PVD-Beschichtungen Ihre Produkte verbessern können – Kontaktieren Sie noch heute unsere Experten für weitere Details!