Dünne Schichten werden durch eine Vielzahl von Abscheidungstechniken gebildet, die sich grob in chemische und physikalische Methoden einteilen lassen. Mit diesen Verfahren lassen sich Dicke, Zusammensetzung und Eigenschaften der Schichten genau steuern, so dass sie sich für eine breite Palette von Anwendungen eignen, von Halbleitern bis hin zu flexiblen Solarzellen und OLEDs. Zu den wichtigsten Verfahren gehören die chemische Gasphasenabscheidung (CVD), die physikalische Gasphasenabscheidung (PVD) und andere Spezialtechniken wie Spincoating, Sputtern und Atomlagenabscheidung (ALD). Jede Methode hat ihre eigenen Vorteile und wird je nach den spezifischen Anforderungen der Anwendung ausgewählt.
Die wichtigsten Punkte werden erklärt:
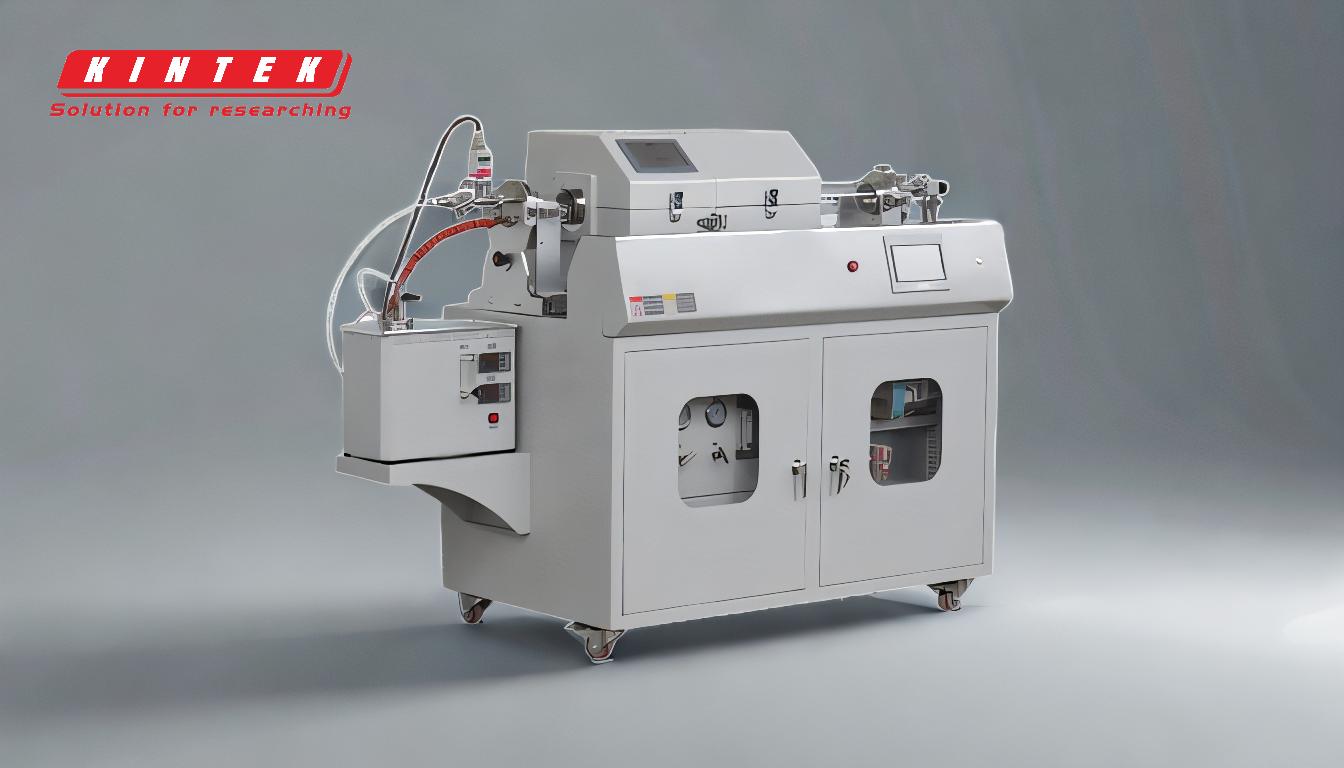
-
Chemische Abscheidungsmethoden:
- Chemische Gasphasenabscheidung (CVD): Bei diesem Verfahren werden chemische Reaktionen zur Herstellung hochreiner dünner Schichten eingesetzt. Vorläufergase werden in eine Reaktionskammer eingeleitet, wo sie auf der Substratoberfläche reagieren und die gewünschte Schicht bilden. Varianten wie die plasmaunterstützte CVD (PECVD) verwenden Plasma, um die Reaktion bei niedrigeren Temperaturen zu verstärken.
- Sol-Gel: Bei dieser Technik wird eine Lösung (Sol) in einen gelartigen Zustand überführt, der dann getrocknet und gesintert wird, um eine dünne Schicht zu bilden. Dieses Verfahren wird häufig zur Herstellung von Oxidschichten verwendet.
- Tauchbeschichtung und Spin-Coating: Bei diesen Verfahren wird ein Substrat in eine Lösung getaucht oder geschleudert, die anschließend getrocknet wird, um einen dünnen Film zu bilden. Die Schleuderbeschichtung ist besonders nützlich für die Herstellung gleichmäßiger Schichten mit kontrollierter Dicke.
-
Physikalische Abscheidungsmethoden:
-
Physikalische Gasphasenabscheidung (PVD): Diese Kategorie umfasst Techniken, bei denen ein festes Material im Vakuum verdampft und dann auf ein Substrat aufgebracht wird. Zu den gängigen PVD-Verfahren gehören:
- Sputtern: Ein Zielmaterial wird mit Ionen beschossen, wodurch Atome herausgeschleudert werden und sich auf dem Substrat ablagern.
- Thermische Verdampfung: Das Material wird in einem Vakuum bis zu seinem Verdampfungspunkt erhitzt, und der Dampf kondensiert auf dem Substrat.
- Elektronenstrahlverdampfung: Das Material wird mit einem Elektronenstrahl erhitzt, wodurch es verdampft und sich auf dem Substrat niederschlägt.
- Molekularstrahlepitaxie (MBE): Hierbei handelt es sich um eine hochgradig kontrollierte Form der Verdampfung, bei der hochwertige kristalline Schichten Schicht für Schicht erzeugt werden.
- Gepulste Laserabscheidung (PLD): Ein Hochleistungslaserpuls wird verwendet, um Material von einem Ziel abzutragen, das dann auf das Substrat aufgebracht wird.
-
Physikalische Gasphasenabscheidung (PVD): Diese Kategorie umfasst Techniken, bei denen ein festes Material im Vakuum verdampft und dann auf ein Substrat aufgebracht wird. Zu den gängigen PVD-Verfahren gehören:
-
Hybride und spezialisierte Techniken:
- Atomlagenabscheidung (ALD): Diese Technik ermöglicht die Abscheidung von Schichten in atomarer Form und bietet eine außergewöhnliche Kontrolle über Dicke und Zusammensetzung. Es ist besonders nützlich für die Herstellung ultradünner Schichten mit hoher Gleichmäßigkeit.
- Magnetron-Sputtering: Eine Variante des Sputterns, bei der Magnetfelder zur Verstärkung der Ionisierung des Sputtergases eingesetzt werden, wodurch die Abscheidungsrate erhöht und die Schichtqualität verbessert wird.
- Tropfengießen und Ölbad: Hierbei handelt es sich um einfachere Techniken, bei denen eine Lösung auf ein Substrat getropft oder das Substrat in eine Lösung getaucht wird, um anschließend zu trocknen und eine dünne Schicht zu bilden.
-
Anwendungen und Überlegungen:
- Halbleiter: Verfahren wie CVD und MBE werden in der Halbleiterherstellung häufig eingesetzt, da sie hochreine und hochwertige Schichten erzeugen können.
- Flexible Elektronik: Verfahren wie Spin-Coating und PVD werden zur Herstellung dünner Schichten für flexible Solarzellen und OLEDs verwendet, bei denen Flexibilität und Gleichmäßigkeit entscheidend sind.
- Optische Beschichtungen: Sputtern und Aufdampfen werden häufig zur Herstellung dünner Schichten für optische Anwendungen wie Antireflexionsbeschichtungen und Spiegel verwendet.
-
Kontrolle und Präzision:
- Kontrolle der Schichtdicke: Verfahren wie ALD und Spin-Coating ermöglichen eine präzise Kontrolle der Schichtdicke, was für Anwendungen, die bestimmte optische, elektrische oder mechanische Eigenschaften erfordern, von entscheidender Bedeutung ist.
- Kontrolle der Zusammensetzung: Verfahren wie CVD und MBE ermöglichen eine genaue Kontrolle der chemischen Zusammensetzung der Schicht und damit die Herstellung komplexer Mehrschichtstrukturen.
Zusammenfassend lässt sich sagen, dass bei der Herstellung dünner Schichten eine Vielzahl von Abscheidetechniken zum Einsatz kommen, von denen jede ihre eigenen Vorteile und Anwendungen hat. Die Wahl des Verfahrens hängt von den gewünschten Schichteigenschaften wie Dicke, Zusammensetzung und Gleichmäßigkeit sowie von den spezifischen Anforderungen der Anwendung ab.
Zusammenfassende Tabelle:
Kategorie | Verfahren | Wesentliche Merkmale |
---|---|---|
Chemische Abscheidung | CVD, Sol-Gel, Tauchbeschichtung, Spin-Coating | Hochreine Schichten, gleichmäßige Dicke, Erzeugung von Oxidschichten |
Physikalische Abscheidung | Sputtern, thermische Verdampfung, Elektronenstrahlverdampfung, MBE, PLD | Vakuumbasiertes, präzises schichtweises Wachstum, hochwertige kristalline Schichten |
Hybride Techniken | ALD, Magnetronsputtern, Tropfengießen, Ölbad | Kontrolle auf atomarer Ebene, verbesserte Abscheidungsraten, einfach und kostengünstig |
Anwendungen | Halbleiter, flexible Elektronik, optische Beschichtungen | Hochreine, flexible, antireflektierende Beschichtungen |
Kontrolle & Präzision | Kontrolle der Schichtdicke (ALD, Spin Coating), Kontrolle der Zusammensetzung (CVD, MBE) | Präzise Dicke und Zusammensetzung für optische, elektrische und mechanische Anforderungen |
Benötigen Sie Hilfe bei der Auswahl der richtigen Beschichtungstechnik für Ihre Anwendung? Kontaktieren Sie unsere Experten noch heute!