Das Sintern ist ein entscheidender Prozess in der Materialwissenschaft und der Fertigung, bei dem pulverförmige Materialien durch kontrollierte Erhitzung und Verfestigung in eine feste, kohäsive Struktur umgewandelt werden.Der Prozess wird durch sechs primäre Mechanismen gesteuert, die die Partikelbindung und Verdichtung vorantreiben.Zu diesen Mechanismen gehören Oberflächendiffusion, Korngrenzendiffusion, Gitterdiffusion, Dampftransport, plastisches Fließen und Verdampfungskondensation.Jeder dieser Mechanismen spielt eine einzigartige Rolle im Sinterprozess und trägt zu den endgültigen Eigenschaften des gesinterten Produkts bei.Das Verständnis dieser Mechanismen ist entscheidend für die Optimierung der Sinterbedingungen in einem Sinteröfen um die gewünschten Materialeigenschaften wie Dichte, Festigkeit und Gefüge zu erreichen.
Die wichtigsten Punkte werden erklärt:
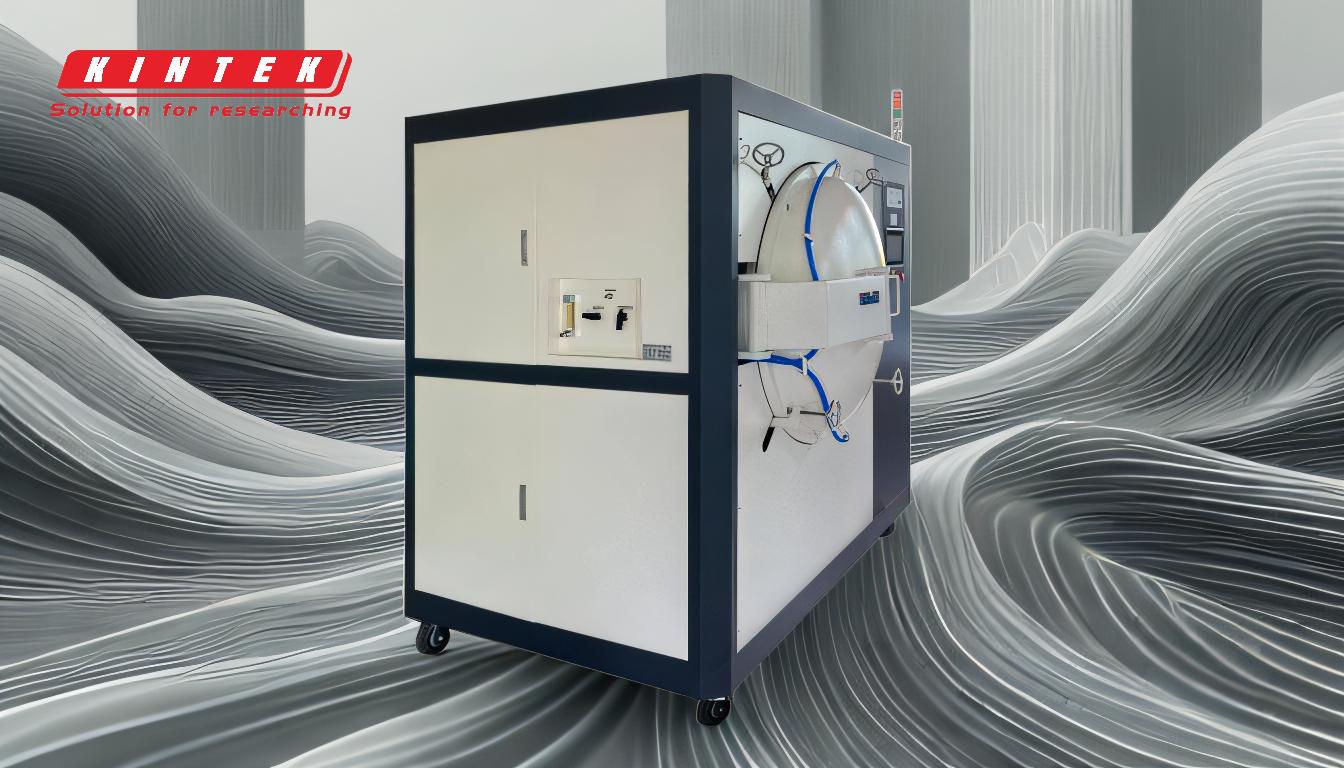
-
Oberflächendiffusion:
- Bei der Oberflächendiffusion bewegen sich die Atome entlang der Oberfläche der Partikel.Dieser Mechanismus ist vor allem bei niedrigeren Temperaturen aktiv und trägt in der Anfangsphase der Sinterung zur Bildung von Nasen zwischen den Partikeln bei.
- Er trägt zur Verringerung der Oberflächenenergie bei, indem er Oberflächenunregelmäßigkeiten ausgleicht, was zur anfänglichen Bindung der Teilchen führt.
-
Korngrenzendiffusion:
- Die Korngrenzendiffusion tritt auf, wenn sich Atome entlang der Grenzen zwischen den Partikeln bewegen.Dieser Mechanismus ist bei höheren Temperaturen von größerer Bedeutung und spielt eine entscheidende Rolle bei der Verdichtung.
- Er erleichtert die Bewegung von Material von den Korngrenzen zu den Nasen zwischen den Partikeln und fördert so die weitere Verdichtung und Verfestigung des Materials.
-
Gitterdiffusion:
- Die Gitterdiffusion, auch bekannt als Volumendiffusion, beinhaltet die Bewegung von Atomen durch das Innere der Partikel.Dieser Mechanismus ist bei hohen Temperaturen vorherrschend und ist für die letzten Phasen des Sinterns von wesentlicher Bedeutung.
- Er trägt zur Beseitigung von Poren und zur allgemeinen Verdichtung des Materials bei, was zu einer homogeneren und dichteren Struktur führt.
-
Dampftransport:
- Beim Dampftransport wird Material von der Oberfläche der Partikel verdampft und kondensiert anschließend auf anderen Oberflächen.Dieser Mechanismus ist in Systemen mit hohen Dampfdrücken von größerer Bedeutung.
- Er trägt zur Umverteilung des Materials bei und hilft dabei, Unebenheiten der Oberfläche auszugleichen und die Partikelbindung zu fördern.
-
Plastischer Fluss:
- Das plastische Fließen bezieht sich auf die Verformung von Partikeln unter Spannung, in der Regel bei hohen Temperaturen.Dieser Mechanismus ist in den frühen Phasen der Sinterung wichtig, wenn die Partikel noch relativ weich sind.
- Er hilft bei der Neuanordnung der Partikel, was zu einer besseren Packung und anfänglichen Verdichtung führt.
-
Verdampfung-Kondensation:
- Bei der Verdampfungskondensation wird das Material durch die Dampfphase von Bereichen mit starker Krümmung (z. B. scharfe Kanten) auf Bereiche mit geringer Krümmung (z. B. Hälse zwischen Partikeln) übertragen.
- Dieser Mechanismus ist besonders wichtig in Systemen, in denen das Material bei der Sintertemperatur einen erheblichen Dampfdruck aufweist, und trägt zur Glättung der Partikeloberflächen und zur Bildung starker Bindungen bei.
Das Verständnis dieser sechs Mechanismen ist entscheidend für die Optimierung des Sinterprozesses in einem Sinterofen .Durch die Steuerung von Faktoren wie Temperatur, Druck und Atmosphäre können die Hersteller die vorherrschenden Mechanismen beeinflussen, um die gewünschten Materialeigenschaften zu erzielen.Höhere Temperaturen können beispielsweise die Gitter- und Korngrenzendiffusion verbessern, was zu einer stärkeren Verdichtung führt, während die Kontrolle der Atmosphäre unerwünschte Reaktionen verhindern und die Stabilität des gesinterten Produkts gewährleisten kann.
Zusammenfassende Tabelle:
Mechanismus | Beschreibung | Schlüsselrolle bei der Sinterung |
---|---|---|
Oberflächendiffusion | Bewegung von Atomen entlang der Teilchenoberfläche; aktiv bei niedrigeren Temperaturen. | Bildet Verengungen zwischen den Teilchen, reduziert die Oberflächenenergie. |
Diffusion an den Korngrenzen | Bewegung von Atomen entlang von Partikelgrenzen; bedeutend bei höheren Temperaturen. | Fördert die Verdichtung und stärkt das Material. |
Gitterdiffusion | Bewegung von Atomen durch das Innere von Partikeln; vorherrschend bei hohen Temperaturen. | Eliminiert Poren, verbessert die Verdichtung. |
Dampftransport | Verdampfung und Kondensation von Material; relevant in Systemen mit hohem Dampfgehalt. | Verteilt das Material neu, glättet die Oberflächen. |
Plastisches Fließen | Verformung der Partikel unter Spannung; wichtig in frühen Sinterphasen. | Ordnet die Partikel neu an, verbessert die Packung. |
Verdampfung/Kondensation | Stoffübertragung über die Dampfphase; wichtig in Systemen mit hohem Dampfdruck. | Glättet Oberflächen, bildet starke Bindungen. |
Optimieren Sie Ihren Sinterprozess mit Expertenwissen. Kontaktieren Sie uns noch heute !