Das Sintern ist ein wichtiges Herstellungsverfahren, bei dem pulverförmige Materialien in dichte, feste Massen umgewandelt werden, ohne dass die Materialien schmelzen.Es beinhaltet die Anwendung von Hitze und Druck, um Partikel miteinander zu verbinden und so Materialeigenschaften wie Festigkeit, Haltbarkeit und Härte zu verbessern.Der Prozess wird durch Faktoren wie Temperatur, Druck, Partikelgröße, Zusammensetzung und die umgebende Atmosphäre beeinflusst.Das Sintern ist in Branchen wie der Pulvermetallurgie und der Keramikherstellung weit verbreitet, wo es sich direkt auf die Mikrostruktur und Leistung des Endprodukts auswirkt.Das Verständnis der Eigenschaften des Sinterns ist für die Optimierung der Materialeigenschaften und die Erzielung der gewünschten Ergebnisse bei verschiedenen Anwendungen von wesentlicher Bedeutung.
Die wichtigsten Punkte werden erklärt:
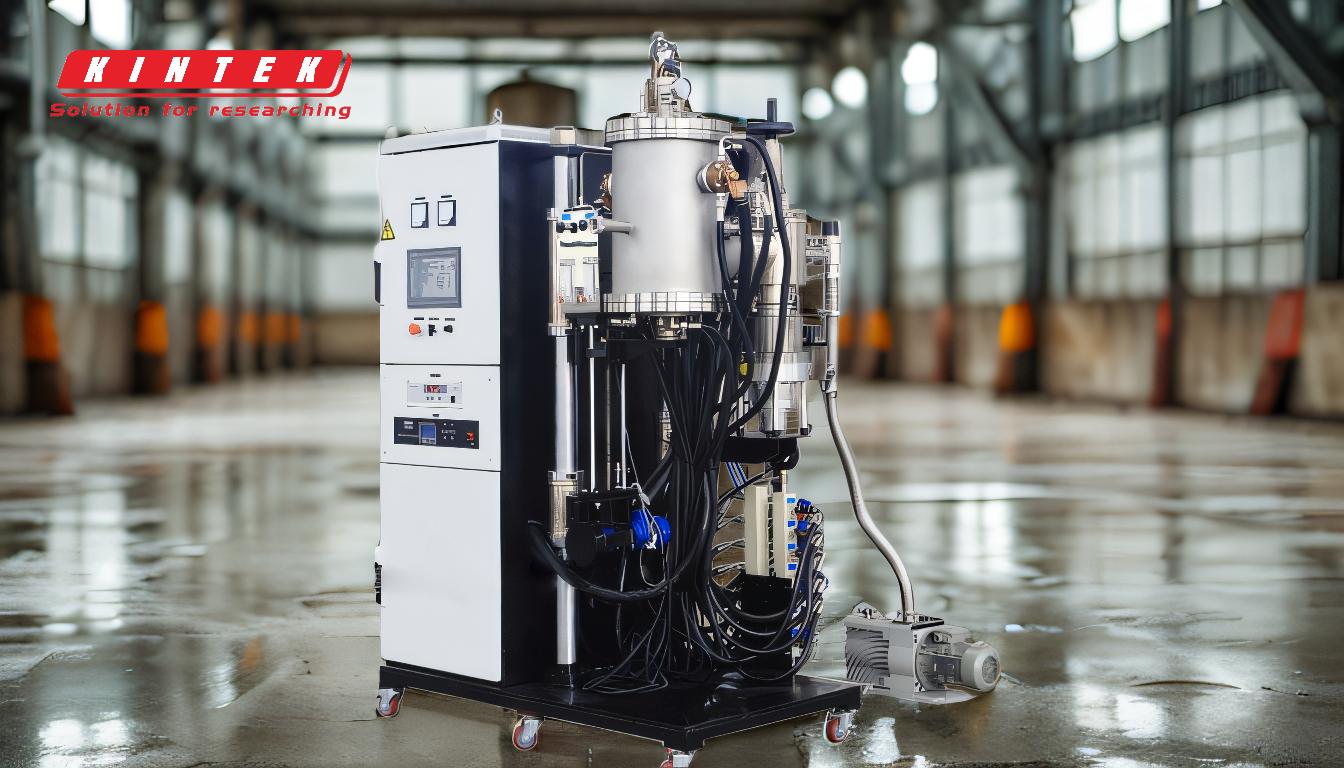
-
Definition und Zweck des Sinterns:
- Das Sintern ist ein Verfahren, bei dem kleine Partikel zu einer festen Masse verbunden werden, ohne dass die Materialien schmelzen.Erreicht wird dies durch die Anwendung von Hitze und Druck, wodurch die Atome zu engeren Bindungen gezwungen werden, was zu einem härteren, stärkeren und haltbareren Material führt.
- Dieses Verfahren wird häufig in der Pulvermetallurgie und der Keramikherstellung eingesetzt, wo es pulverförmige Materialien in dichte Körper mit verbesserten mechanischen Eigenschaften verwandelt.
-
Schlüsselfaktoren, die das Sintern beeinflussen:
- Temperatur:Bestimmt die Kinetik der Sinterung und die endgültigen Materialeigenschaften.Höhere Temperaturen verbessern im Allgemeinen die Verdichtung und die Bindung zwischen den Partikeln.
- Aufheizrate:Beeinflusst die Geschwindigkeit, mit der die Verdichtung erfolgt.Eine kontrollierte Erwärmungsrate ist entscheidend, um Defekte zu vermeiden und eine gleichmäßige Verdichtung zu gewährleisten.
- Druck:Verbessert die Umstrukturierung der Partikel und trägt zur Beseitigung von Porosität bei, was zu einem kompakteren und dichteren Material führt.
- Partikelgröße:Kleinere Partikel haben ein größeres Verhältnis von Oberfläche zu Volumen, was eine bessere Verdichtung und Bindung während des Sinterns fördert.
- Zusammensetzung:Homogene Zusammensetzungen führen zu einem gleichmäßigeren Sinterverhalten und besseren Materialeigenschaften.
-
Mikrostrukturelle Veränderungen während des Sinterns:
- Das Sintern wirkt sich direkt auf die Korngröße, die Porengröße und die Form und Verteilung der Korngrenzen im Mikrogefüge von Werkstoffen aus.
- Diese Veränderungen beeinflussen die mechanischen Eigenschaften des Materials, wie Festigkeit, Haltbarkeit und Härte.So kann beispielsweise die Verringerung der Porosität durch Sintern die Zugfestigkeit und Ermüdungsbeständigkeit des Materials erheblich verbessern.
-
Atmosphäre und Abkühlgeschwindigkeit:
- Die Atmosphäre, in der die Sinterung stattfindet (z. B. Luft, Vakuum oder Inertgase wie Argon oder Stickstoff), kann die endgültigen Materialeigenschaften beeinflussen.So kann beispielsweise das Sintern im Vakuum oder in einer inerten Atmosphäre die Oxidation verhindern und die Materialqualität verbessern.
- Auch die Abkühlungsgeschwindigkeit nach dem Sintern spielt eine Rolle bei der Bestimmung des endgültigen Gefüges und der Eigenschaften.Eine schnelle Abkühlung kann zu feineren Kornstrukturen führen, während eine langsamere Abkühlung zu größeren Körnern führen kann.
-
Anwendungen des Sinterns:
- Das Sintern wird häufig bei der Herstellung von Keramik verwendet, wo es Ton und andere Keramikpulver in haltbare Produkte wie Töpferwaren und Fliesen verwandelt.
- In der Pulvermetallurgie wird das Sintern zur Herstellung von Metallteilen mit komplexen Formen und hoher Festigkeit verwendet, wie z. B. Zahnräder, Lager und Automobilteile.
- Das Verfahren ist auch auf Kunststoffe und andere Materialien anwendbar, wo es die mechanischen Eigenschaften und die Haltbarkeit des Endprodukts verbessert.
-
Vorteile des Sinterns:
- Verbesserte Materialeigenschaften:Das Sintern verbessert die Festigkeit, Härte und Haltbarkeit von Werkstoffen, indem es die Porosität verringert und die atomare Bindung verbessert.
- Kostengünstig:Das Sintern ermöglicht die Herstellung komplexer Formen mit minimalem Materialabfall, was es zu einem kosteneffizienten Fertigungsverfahren macht.
- Vielseitigkeit:Das Verfahren kann auf eine Vielzahl von Materialien angewendet werden, darunter Metalle, Keramiken und Kunststoffe, was es vielseitig für verschiedene industrielle Anwendungen einsetzbar macht.
-
Herausforderungen und Beschränkungen:
- Kontrolle der Prozessparameter:Um die gewünschten Materialeigenschaften zu erreichen, müssen Temperatur, Druck und andere Sinterparameter präzise gesteuert werden.Inkonsistente Bedingungen können zu Defekten oder suboptimalen Materialeigenschaften führen.
- Grenzen des Materials:Nicht alle Materialien sind für das Sintern geeignet.Einige Werkstoffe erfordern besondere Bedingungen oder Zusatzstoffe, um die gewünschte Verdichtung und Bindung zu erreichen.
Wenn die Hersteller diese Hauptmerkmale des Sinterns verstehen, können sie den Prozess optimieren, um Materialien mit maßgeschneiderten Eigenschaften für bestimmte Anwendungen herzustellen.Ob Keramik, Metalle oder Kunststoffe - das Sintern ist nach wie vor ein grundlegendes Verfahren zur Verbesserung der Materialleistung und zur Herstellung hochwertiger, langlebiger Produkte.
Zusammenfassende Tabelle:
Hauptaspekt | Einzelheiten |
---|---|
Definition | Verbindet Teilchen zu einer festen Masse, ohne zu schmelzen. |
Schlüsselfaktoren | Temperatur, Druck, Partikelgröße, Zusammensetzung, Atmosphäre. |
Anwendungen | Keramik, Pulvermetallurgie, Kunststoffe. |
Vorteile | Erhöhte Festigkeit, Kosteneffizienz, Vielseitigkeit. |
Herausforderungen | Präzise Parametersteuerung, Materialeignung. |
Optimieren Sie Ihren Sinterprozess für hervorragende Materialeigenschaften - Kontaktieren Sie unsere Experten noch heute !