Die Kalzinierung ist ein thermischer Behandlungsprozess, der dazu dient, eine thermische Zersetzung, einen Phasenübergang oder die Entfernung einer flüchtigen Fraktion in Materialien zu bewirken.Die für die Kalzinierung verwendeten Geräte, die so genannten Kalzinatoren, gibt es in verschiedenen Konfigurationen, die jeweils auf die spezifischen Bedürfnisse der Industrie zugeschnitten sind.Zu den Haupttypen von Kalzinieranlagen gehören Muffelöfen, Flammöfen und Schachtöfen oder Brennöfen.Diese Typen unterscheiden sich in Konstruktion, Betrieb und Anwendung und eignen sich daher für unterschiedliche Materialien und Prozesse.Im Folgenden werden diese Typen im Detail untersucht, wobei der Schwerpunkt auf ihren einzigartigen Merkmalen, Vorteilen und typischen Anwendungen liegt.
Die wichtigsten Punkte erklärt:
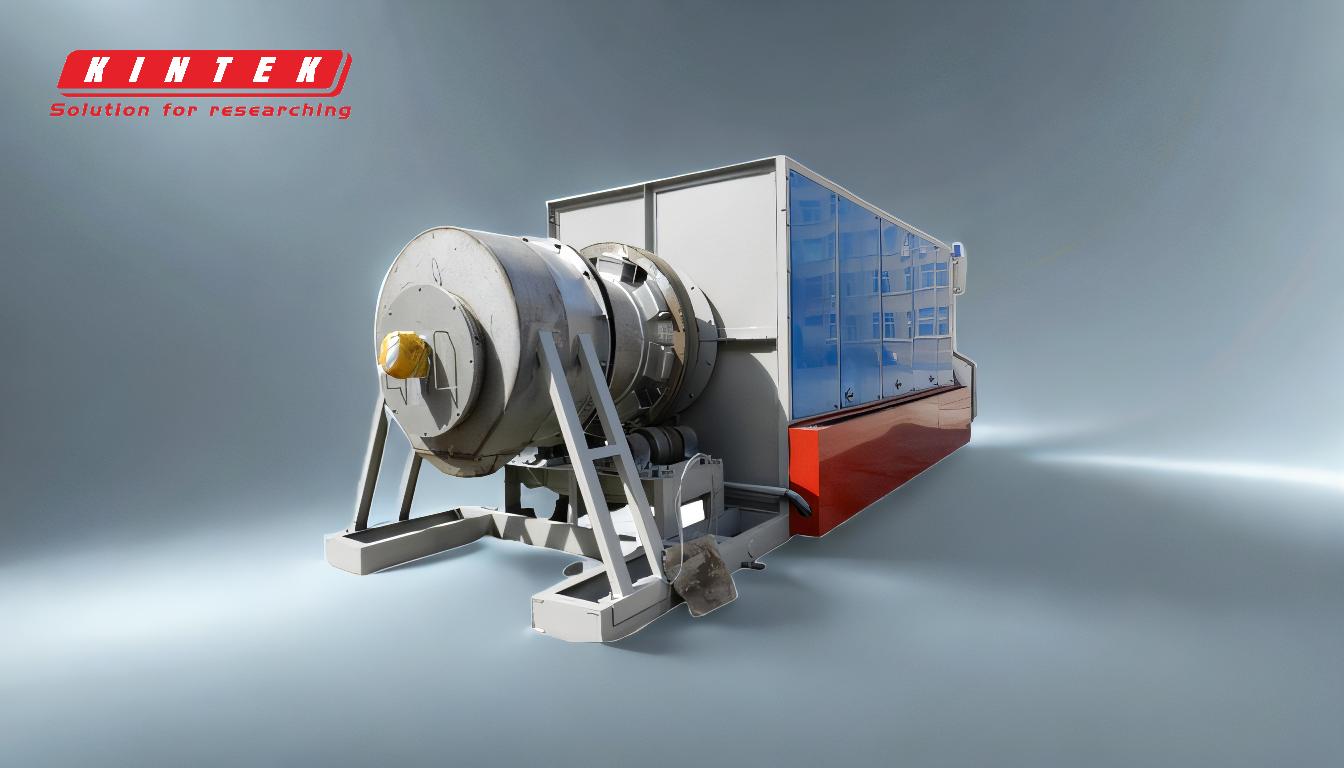
-
Muffelöfen
- Konstruktion und Betrieb:Muffelöfen sind mit einer separaten Kammer (der Muffel) ausgestattet, die das zu verarbeitende Material von den Verbrennungsgasen isoliert.Dadurch wird das Material indirekt erhitzt und eine saubere und kontrollierte Umgebung aufrechterhalten.
-
Vorteile:
- Präzise Temperaturregelung.
- Schutz der Materialien vor Verunreinigung durch Verbrennungsgase.
- Geeignet für Anwendungen in kleinem Maßstab oder im Labor.
-
Anwendungen:
- Kalzinierung von empfindlichen Materialien wie Keramik, Glas und bestimmten Metallen.
- Forschung und Entwicklung im Labor.
-
Flammstrahlöfen
- Konstruktion und Betrieb:Hallöfen verfügen über eine große, offene Kammer, in der die Wärme von der Decke und den Wänden auf das Material reflektiert wird (Nachhall).Das Material wird direkt durch die Flammen und indirekt durch die reflektierte Wärme erhitzt.
-
Vorteile:
- Hoher Durchsatz für industrielle Prozesse im großen Maßstab.
- Fähigkeit, Schüttgut zu verarbeiten.
- Gleichmäßige Erwärmung durch den Nachhall der Wärme.
-
Anwendungen:
- Kalzinierung von Erzen, wie z. B. Bauxit zur Herstellung von Tonerde.
- Verarbeitung von Zementklinker und anderen Industriemineralien.
-
Schachtöfen oder Öfen
- Konstruktion und Betrieb:Schachtöfen sind vertikale Konstruktionen, bei denen das Material von oben zugeführt wird und sich durch eine beheizte Zone nach unten bewegt.Die Wärme wird in der Regel durch die Verbrennung von Brennstoff am Boden erzeugt, und das Material wird beim Herabsteigen kalziniert.
-
Vorteile:
- Effiziente Wärmenutzung durch den Gegenstrom von Material und Gasen.
- Kontinuierlicher Betrieb, daher geeignet für Großserien.
- Kompakte Bauweise im Vergleich zu horizontalen Öfen.
-
Anwendungen:
- Kalzinierung von Kalkstein zur Herstellung von Kalk.
- Verarbeitung von Eisenerzpellets und andere metallurgische Anwendungen.
-
Vergleich der Kalzinatorentypen
- Umfang des Betriebs:Muffelöfen eignen sich ideal für kleine oder präzise Anwendungen, während sich die Trommel- und Schachtöfen besser für großtechnische Prozesse eignen.
- Material-Kompatibilität:Muffelöfen werden bevorzugt für empfindliche Materialien eingesetzt, während für Schüttgüter wie Erze und Mineralien Trommel- und Schachtöfen verwendet werden.
- Energie-Effizienz:Schachtöfen sind aufgrund ihrer Bauweise im Allgemeinen energieeffizienter, während Muffelöfen für die indirekte Beheizung mehr Energie benötigen.
-
Auswahlkriterien für Kalzinieranlagen
- Materialeigenschaften:Die Art des zu verarbeitenden Materials (z. B. Empfindlichkeit gegenüber Verunreinigungen, Partikelgröße) beeinflusst die Wahl des Kalzinators.
- Produktionsmaßstab:Der erforderliche Durchsatz entscheidet darüber, ob ein kleiner Muffelofen oder ein groß angelegter Trommel- oder Schachtofen benötigt wird.
- Anforderungen an die Temperatur:Verschiedene Kalzinatoren haben unterschiedliche Temperaturkapazitäten, die auf die Kalzinierungstemperatur des Materials abgestimmt sein müssen.
- Energie-Effizienz:Für einen kosteneffizienten Betrieb ist die Energieeffizienz ein entscheidender Faktor, insbesondere in großindustriellen Anlagen.
Zusammenfassend lässt sich sagen, dass die Wahl des Kalzinators von den spezifischen Anforderungen des Materials und des Prozesses abhängt.Muffelöfen eignen sich ideal für präzise, kleintechnische Anwendungen, während sich Flammöfen bei großtechnischen Prozessen auszeichnen und Schachtöfen einen energieeffizienten Dauerbetrieb für Schüttgut bieten.Das Verständnis dieser Unterschiede ist entscheidend für die Auswahl der richtigen Anlage für die Kalzinierung.
Zusammenfassende Tabelle:
Kalzinator Typ | Aufbau und Betrieb | Vorteile | Anwendungen |
---|---|---|---|
Muffelofen | Separate Kammer isoliert das Material von den Verbrennungsgasen; indirekte Beheizung. | Präzise Temperaturregelung, kontaminationsfrei, ideal für den Einsatz in kleinem Maßstab. | Kalzinierung von Keramik, Glas, Metallen; Forschung und Entwicklung im Labor. |
Hallraum-Ofen | Offene Kammer mit von den Wänden reflektierter Wärme; direkte und indirekte Beheizung. | Hoher Durchsatz, Verarbeitung von Schüttgut, gleichmäßige Erwärmung. | Kalzinierung von Erzen (z. B. Bauxit), Zementklinker, Industriemineralien. |
Schachtofen/Kiln | Vertikale Struktur; das Material fällt durch die beheizte Zone; Wärmefluss im Gegenstrom. | Energieeffizienter, kontinuierlicher Betrieb, kompakte Bauweise. | Kalzinierung von Kalkstein, Eisenerzpellets, metallurgische Anwendungen. |
Benötigen Sie Hilfe bei der Auswahl des richtigen Kalzinators für Ihr Verfahren? Kontaktieren Sie noch heute unsere Experten !