Die physikalische Gasphasenabscheidung (PVD) ist eine vielseitige und umweltfreundliche Technik zur Herstellung dünner, hochreiner Beschichtungen auf Substraten. Bei diesem Prozess werden Materialien im Vakuum verdampft und Atom für Atom auf einer Oberfläche abgeschieden. PVD wird in der Industrie häufig eingesetzt, da es langlebige Hochleistungsbeschichtungen mit präziser Kontrolle über Zusammensetzung und Dicke herstellen kann. Die beiden häufigsten Arten von PVD sind Sputtern Und Verdunstung , mit Verdunstung weiter unterteilt in thermische Verdampfung Und Elektronenstrahlverdampfung (E-Beam). . Die Auswahl dieser Methoden richtet sich nach den spezifischen Anforderungen der Anwendung, wie etwa Materialverträglichkeit, Beschichtungsqualität und Prozesseffizienz.
Wichtige Punkte erklärt:
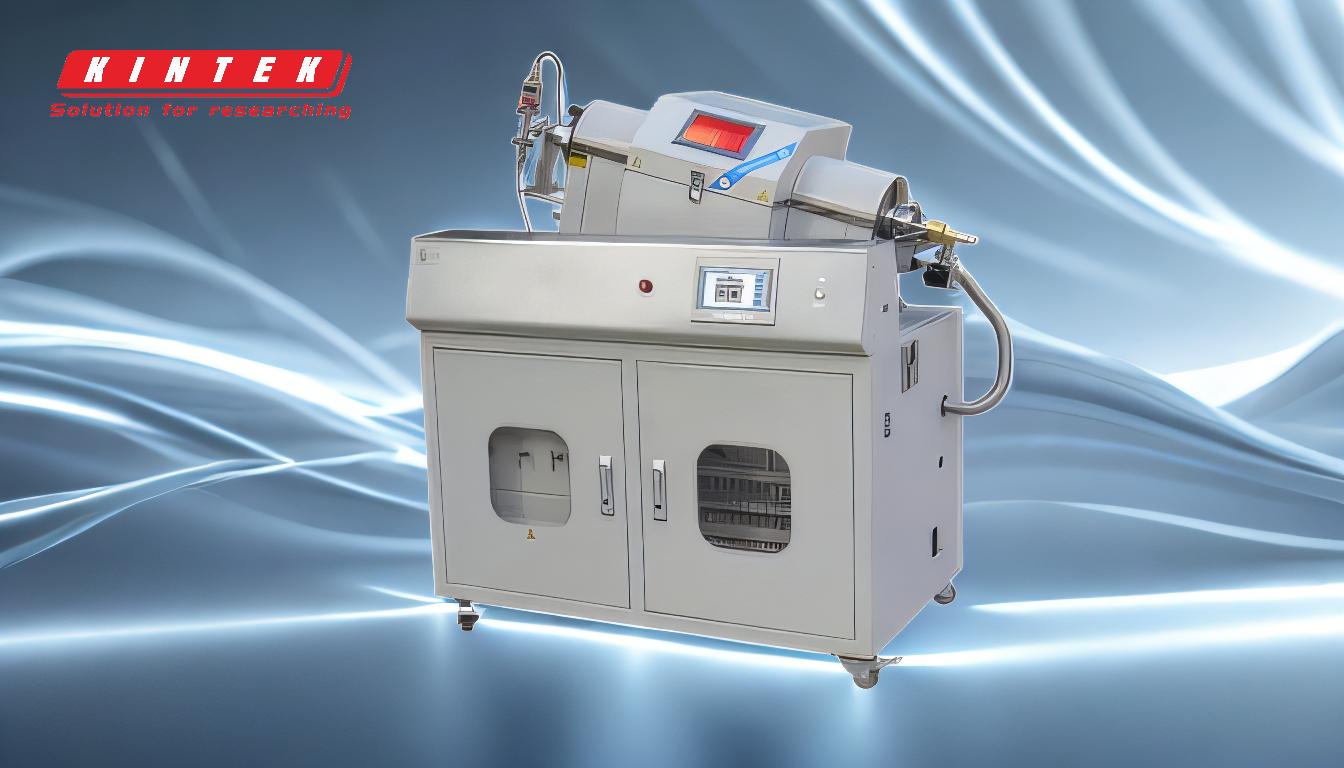
-
Sputtern in PVD:
- Sputtern ist eine weit verbreitete PVD-Technik, bei der ein Targetmaterial mit hochenergetischen Ionen beschossen wird, wodurch Atome herausgeschleudert und auf einem Substrat abgeschieden werden. Dieses Verfahren eignet sich besonders gut zur Herstellung gleichmäßiger und haftfester Beschichtungen.
- Magnetronsputtern ist eine gängige Variante, die Magnetfelder nutzt, um die Effizienz des Sputterprozesses zu steigern, wodurch sie sich für die Abscheidung einer breiten Palette von Materialien, einschließlich Metallen, Legierungen und Keramiken, eignet.
- Sputtern ist ideal für Anwendungen, die hochwertige, dichte Beschichtungen mit hervorragender Haftung und Haltbarkeit erfordern.
-
Verdampfung bei PVD:
-
Beim Verdampfen wird ein Material im Vakuum erhitzt, bis es verdampft. Der Dampf kondensiert dann auf einem Substrat und bildet einen dünnen Film. Diese Methode ist in zwei Haupttypen unterteilt:
- Thermische Verdampfung: Eine einfache und kostengünstige Methode, bei der das Material mithilfe einer Widerstandswärmequelle erhitzt wird. Es wird häufig zum Abscheiden von Metallen und einfachen Verbindungen verwendet.
- Elektronenstrahlverdampfung (E-Beam).: Bei dieser Methode wird das Material mit einem fokussierten Elektronenstrahl erhitzt, was die Abscheidung von Materialien mit hohem Schmelzpunkt ermöglicht. Im Vergleich zur thermischen Verdampfung bietet es eine bessere Kontrolle über die Filmdicke und -zusammensetzung.
- Die Verdampfung wird für Anwendungen bevorzugt, die hochreine Beschichtungen und eine präzise Kontrolle der Filmeigenschaften erfordern.
-
Beim Verdampfen wird ein Material im Vakuum erhitzt, bis es verdampft. Der Dampf kondensiert dann auf einem Substrat und bildet einen dünnen Film. Diese Methode ist in zwei Haupttypen unterteilt:
-
Vergleich von Sputtern und Verdampfen:
- Materialkompatibilität: Sputtern ist vielseitiger und kann ein breiteres Spektrum an Materialien abscheiden, einschließlich komplexer Legierungen und Keramiken, während Aufdampfen besser für einfachere Materialien geeignet ist.
- Beschichtungsqualität: Sputtern erzeugt dichtere und besser haftende Beschichtungen und eignet sich daher für anspruchsvolle Anwendungen. Die Verdampfung, insbesondere die Elektronenstrahlverdampfung, liefert hochreine Beschichtungen mit ausgezeichneter Gleichmäßigkeit.
- Prozesseffizienz: Sputtern ist für die Produktion im großen Maßstab effizienter, während die Verdampfung häufig für kleinere, hochpräzise Anwendungen eingesetzt wird.
-
Vorteile von PVD:
- PVD ist umweltfreundlich, da keine chemischen Reagenzien oder eine Nachbehandlungsreinigung erforderlich sind.
- Es erzeugt dünne, reine Beschichtungen mit ausgezeichneter Haftung, Beständigkeit und Haltbarkeit.
- Die Technik ermöglicht eine präzise Kontrolle der Zusammensetzung und Dicke der Beschichtungen und eignet sich daher für ein breites Anwendungsspektrum, von der Elektronik bis hin zu medizinischen Geräten.
-
Anwendungen von PVD:
- Elektronik: PVD wird zur Abscheidung dünner Schichten für Halbleiter, Solarzellen und optische Beschichtungen verwendet.
- Medizinische Geräte: Mit der Technik werden biokompatible Beschichtungen für Implantate und chirurgische Instrumente hergestellt.
- Luft- und Raumfahrt: PVD-Beschichtungen verbessern die Leistung und Haltbarkeit von Bauteilen, die extremen Bedingungen ausgesetzt sind.
- Dekorative Beschichtungen: PVD wird verwendet, um langlebige und ästhetisch ansprechende Oberflächen auf Verbraucherprodukten zu erzeugen.
-
Vergleich mit chemischer Gasphasenabscheidung (CVD):
- Während PVD auf physikalischen Prozessen zur Abscheidung von Materialien beruht, Chemische Gasphasenabscheidung mit Mikrowellenplasma beinhaltet chemische Reaktionen zur Bildung dünner Filme. CVD wird häufig zur Abscheidung komplexer Materialien und zur Erzielung hoher Abscheidungsraten eingesetzt, erfordert jedoch im Vergleich zur PVD höhere Temperaturen und eine komplexere Ausrüstung.
Zusammenfassend lässt sich sagen, dass PVD-Techniken wie Sputtern und Verdampfen je nach Anwendung deutliche Vorteile bieten. Sputtern ist ideal für die Herstellung dichter, hochwertiger Beschichtungen, während die Verdampfung, insbesondere die Elektronenstrahlverdampfung, sich hervorragend für die Herstellung hochreiner, präziser Filme eignet. Beide Methoden sind integraler Bestandteil der modernen Fertigung und bieten umweltfreundliche Lösungen für eine Vielzahl von Branchen.
Übersichtstabelle:
PVD-Typ | Untertypen | Hauptmerkmale | Anwendungen |
---|---|---|---|
Sputtern | Magnetronsputtern | Hochwertige, dichte Beschichtungen; ausgezeichnete Haftung; vielseitiger Materialauftrag | Elektronik, medizinische Geräte, Luft- und Raumfahrt, dekorative Beschichtungen |
Verdunstung | Thermische Verdampfung | Kostengünstig; einfacher Prozess; Geeignet für Metalle und einfache Verbindungen | Hochreine Beschichtungen, präzise Filmkontrolle |
Elektronenstrahlverdampfung | Materialien mit hohem Schmelzpunkt; Präzise Kontrolle der Dicke und Zusammensetzung | Halbleiter, optische Beschichtungen, fortschrittliche Materialien |
Entdecken Sie, welche PVD-Technik für Ihre Anwendung am besten geeignet ist – Kontaktieren Sie noch heute unsere Experten !