Die chemische Gasphasenabscheidung (CVD) ist eine weit verbreitete Technik für die Abscheidung von dünnen Schichten und Beschichtungen, die jedoch einige Nachteile mit sich bringt.Dazu gehören hohe Betriebstemperaturen, die die Kompatibilität mit dem Substrat einschränken können, der Bedarf an giftigen und flüchtigen chemischen Vorläufersubstanzen und die Entstehung gefährlicher Nebenprodukte.Darüber hinaus sind CVD-Prozesse energieintensiv, kostspielig und erfordern eine genaue Kontrolle über mehrere Parameter.Das Verfahren ist auch in Bezug auf die Substratgröße und die Arten von Materialien, die synthetisiert werden können, begrenzt, insbesondere bei Mehrkomponentensystemen.Trotz ihrer Vorteile, wie z. B. hohe Reinheit und Gleichmäßigkeit, ist die CVD-Methode aufgrund dieser Nachteile für bestimmte Anwendungen weniger geeignet und im Vergleich zu anderen Abscheidetechniken schwieriger zu realisieren.
Die wichtigsten Punkte werden erklärt:
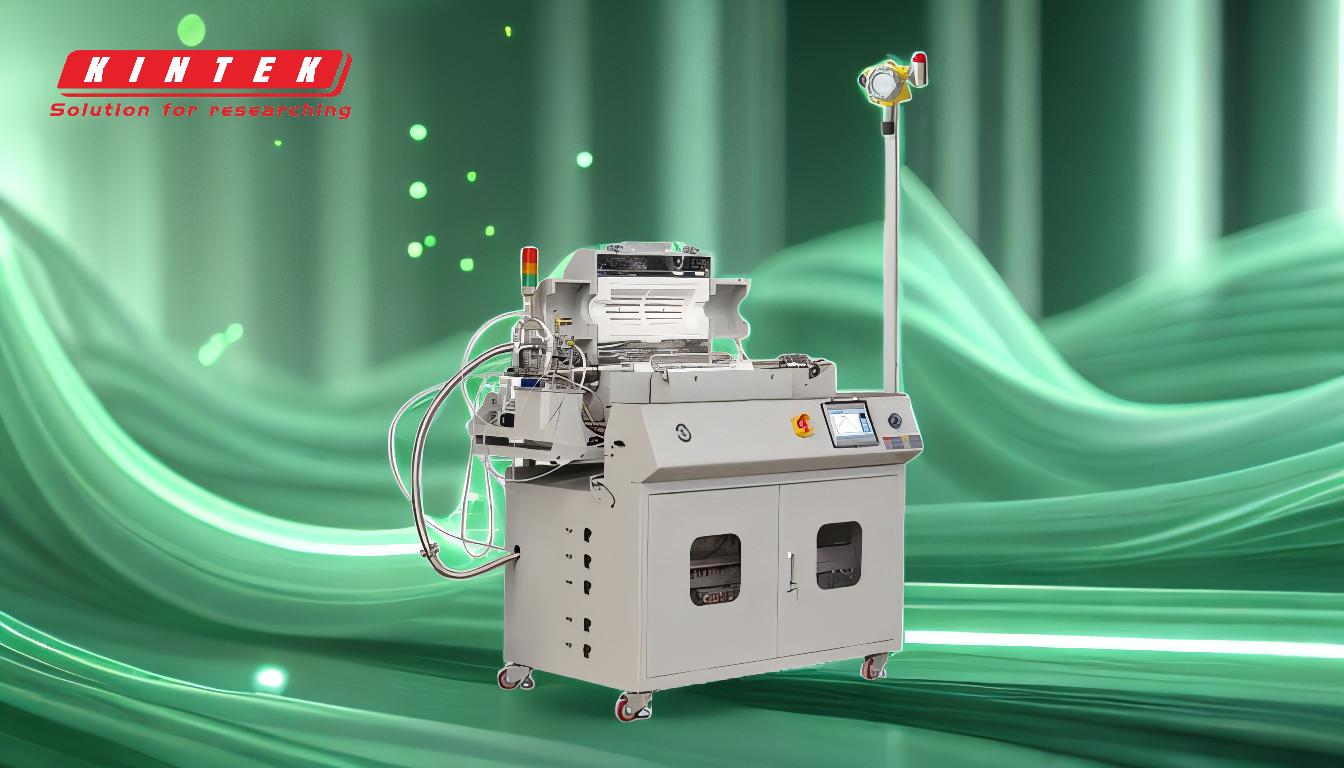
-
Hohe Betriebstemperaturen:
- CVD erfordert in der Regel Temperaturen von über 600 °C, was bei vielen Substraten zu thermischer Instabilität führen kann.Dies schränkt die Arten von Materialien ein, die verwendet werden können, da einige von ihnen sich bei solch hohen Temperaturen zersetzen oder verformen können.
- Der mit diesen Temperaturen verbundene hohe Energieverbrauch erhöht zudem die Betriebskosten.
-
Toxische und flüchtige chemische Vorläuferstoffe:
- Bei der CVD werden chemische Ausgangsstoffe mit hohem Dampfdruck verwendet, wie Halogenide und Metallcarbonylverbindungen, die oft giftig, pyrophor oder gefährlich sind.Dies birgt erhebliche Gesundheits- und Sicherheitsrisiken bei der Handhabung und Verarbeitung.
- Der Mangel an ungiftigen und nichtpyrophoren Vorprodukten erschwert den Prozess zusätzlich.
-
Gefährliche Nebenprodukte:
- Beim CVD-Verfahren entstehen Nebenprodukte, die oft giftig und korrosiv sind, wie Chlorwasserstoff oder andere flüchtige Verbindungen.Die Neutralisierung dieser Nebenprodukte erfordert zusätzliche Anlagen und Verfahren, was sowohl die Komplexität als auch die Kosten erhöht.
-
Hohe Kosten und hoher Energieverbrauch:
- CVD-Anlagen sind teuer, und das Verfahren ist aufgrund der hohen Temperaturen und der erforderlichen präzisen Steuerung sehr energieintensiv.Dadurch ist CVD für einige Anwendungen im Vergleich zu alternativen Verfahren wie der physikalischen Gasphasenabscheidung (PVD) wirtschaftlich weniger interessant.
-
Begrenzte Substratgröße und Kompatibilität:
- Die Größe der Substrate, die verarbeitet werden können, ist durch die Abmessungen der CVD-Kammer begrenzt.Dies schränkt die Skalierbarkeit des Verfahrens für größere Anwendungen ein.
- Außerdem können die hohen Temperaturen und die chemische Reaktivität der Ausgangsstoffe die Arten von Substraten einschränken, die mit CVD kompatibel sind.
-
Anforderungen an Komplexität und Präzision:
- CVD erfordert eine präzise Steuerung mehrerer Parameter, darunter Gasdurchsatz, Substrattemperatur und Verarbeitungszeit.Dies macht das Verfahren komplexer und weniger fehlerverzeihend als andere Abscheidetechniken.
-
Beschränkungen bei der Materialsynthese:
- Die Synthese von Mehrkomponentenmaterialien ist aufgrund von Schwankungen des Dampfdrucks, der Keimbildung und der Wachstumsraten während der Umwandlung von Gas in Partikel eine Herausforderung.Dies führt oft zu heterogenen Zusammensetzungen und uneinheitlichen Materialeigenschaften.
-
Dicke und strukturelle Beschränkungen:
- CVD eignet sich in erster Linie für die Abscheidung dünner Schichten im Bereich von einigen Nanometern bis zu einigen Mikrometern.Für die Herstellung dickerer Schichten oder dreidimensionaler Strukturen ist es nicht gut geeignet, was seine Anwendbarkeit in bestimmten Bereichen einschränkt.
-
Umwelt- und Sicherheitsaspekte:
- Die Verwendung von gefährlichen Gasen und Chemikalien in CVD-Verfahren wirft Umwelt- und Sicherheitsfragen auf.Die ordnungsgemäße Handhabung, Lagerung und Entsorgung dieser Stoffe ist notwendig und erhöht die Gesamtkomplexität und die Kosten.
CVD bietet zwar Vorteile wie hohe Reinheit und Gleichmäßigkeit, aber diese Nachteile machen auch die Herausforderungen deutlich, die mit dieser Technik verbunden sind.Für Anwendungen, die niedrigere Temperaturen, einfachere Prozesse oder eine Produktion in größerem Maßstab erfordern, sind alternative Abscheidungsmethoden möglicherweise besser geeignet.
Zusammenfassende Tabelle:
Benachteiligung | Beschreibung |
---|---|
Hohe Betriebstemperaturen | Erfordert >600°C, was die Substratkompatibilität einschränkt und die Energiekosten erhöht. |
Toxische chemische Vorläuferstoffe | Verwendet gefährliche, flüchtige Vorläuferstoffe, die Gesundheits- und Sicherheitsrisiken darstellen. |
Gefährliche Nebenprodukte | Erzeugt giftige und ätzende Nebenprodukte, die eine zusätzliche Neutralisierung erfordern. |
Hohe Kosten und hoher Energieverbrauch | Teure Ausrüstung und energieintensive Prozesse verringern die wirtschaftliche Rentabilität. |
Begrenzte Substratgröße | Begrenzt durch die Abmessungen der Kammer, was die Skalierbarkeit für größere Anwendungen einschränkt. |
Komplexität und Präzision | Erfordert präzise Kontrolle über mehrere Parameter, was die Komplexität des Prozesses erhöht. |
Beschränkungen bei der Materialsynthese | Herausforderungen bei der Synthese von Multikomponenten-Materialien mit gleichbleibenden Eigenschaften. |
Dicke und strukturelle Grenzen | Nur für dünne Schichten geeignet, nicht für dickere oder 3D-Strukturen. |
Umwelt- und Sicherheitsaspekte | Die Handhabung und Entsorgung gefährlicher Materialien ist kompliziert und teuer. |
Suchen Sie nach einer besseren Abscheidungslösung? Kontaktieren Sie uns noch heute um auf Ihre Bedürfnisse zugeschnittene Alternativen zu erkunden!