Die induktive Erwärmung ist zwar in vielen Anwendungen vorteilhaft, hat aber auch einige bemerkenswerte Nachteile. Dazu gehören hohe Anschaffungskosten, der Bedarf an Spezialausrüstung und Fachpersonal, Einschränkungen bei der Veredelungskapazität, Herausforderungen bei der Steuerung der Wärmeverteilung und der Bedarf an speziellen Induktoren. Darüber hinaus erfordern induktive Erwärmungssysteme oft robuste Regelalgorithmen, um mit unterschiedlichen Lasten und Betriebspunkten umzugehen, und sie können Probleme mit ungleichmäßiger Wärmeverteilung und hohen Erwärmungsraten haben. Diese Faktoren können die induktive Erwärmung im Vergleich zu anderen Erwärmungsmethoden weniger flexibel und teurer machen.
Die wichtigsten Punkte werden erklärt:
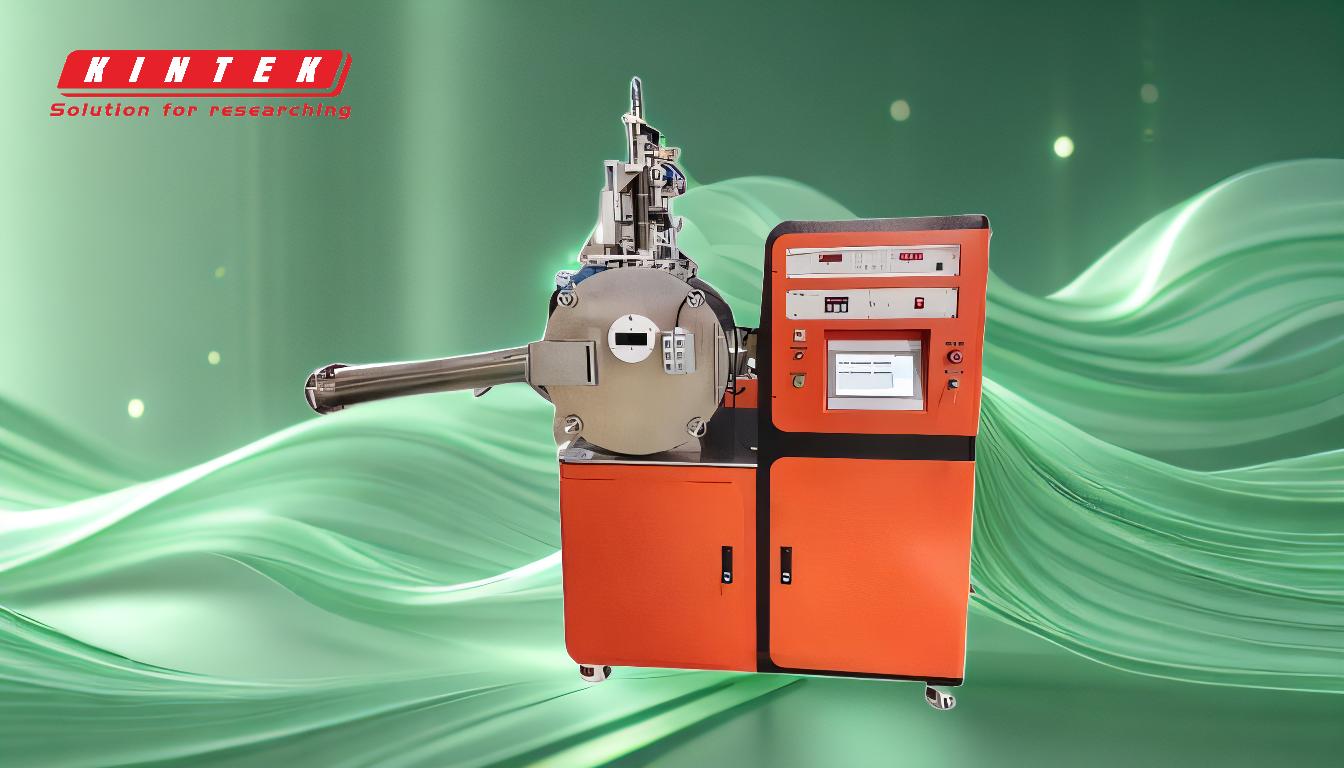
-
Hohe Anfangsinvestition
- Induktionserwärmungssysteme erfordern erhebliche Vorlaufkosten, einschließlich spezieller Ausrüstung wie Hochfrequenzgeneratoren und Stromversorgungen.
- Der Bedarf an qualifiziertem Personal mit Fachkenntnissen über die Prinzipien der Induktionserwärmung und Sicherheitsverfahren erhöht die Betriebskosten zusätzlich.
- Dies macht die induktive Erwärmung für kleine Betriebe oder Anwendungen mit begrenzten Budgets weniger zugänglich.
-
Fehlende Raffineriekapazitäten
- Induktionsöfen können keine Materialien veredeln, d. h. die Einsatzmaterialien müssen frei von Oxiden und von bekannter Zusammensetzung sein.
- Einige Legierungselemente können durch Oxidation während des Erhitzungsprozesses verloren gehen, so dass sie der Schmelze wieder zugeführt werden müssen.
- Diese Einschränkung macht die induktive Erwärmung ungeeignet für Anwendungen, die eine Materialreinigung oder -veredelung erfordern.
-
Bedarf an dedizierten Induktoren
- Die Flexibilität der induktiven Erwärmung wird durch die Notwendigkeit eingeschränkt, kundenspezifische Induktoren für spezifische Anwendungen herzustellen.
- Der Entwurf und die Herstellung dieser Induktoren kann teuer sein, insbesondere bei komplexen oder einzigartigen Geometrien.
- Die Bewältigung hoher Stromdichten in kleinen Kupferinduktoren erfordert oft eine spezielle Technik und eine präzise "Kupferanpassung", was die Kosten weiter erhöht.
-
Herausforderungen bei der Wärmeverteilung
- Bei der induktiven Erwärmung kann es zu einer ungleichmäßigen Wärmeverteilung kommen, die zu ungleichmäßigen Materialeigenschaften des Endprodukts führen kann.
- Hohe Erhitzungsraten können dieses Problem noch verschärfen und zu thermischen Spannungen oder Schäden am Material führen.
- Eine korrekte Ausrichtung und eine gute induktive Kopplung sind für eine gleichmäßige Erwärmung von entscheidender Bedeutung, was den Prozess noch komplexer macht.
-
Abhängigkeit von der Wärmeleitfähigkeit
- Die Wirksamkeit der induktiven Erwärmung hängt von der Wärmeleitfähigkeit des zu erwärmenden Materials ab.
- Materialien mit schlechter Wärmeleitfähigkeit erwärmen sich möglicherweise nicht gleichmäßig, was die Anwendbarkeit der induktiven Erwärmung in bestimmten Szenarien einschränkt.
- Diese Abhängigkeit von den Materialeigenschaften schränkt die Vielseitigkeit der induktiven Erwärmung im Vergleich zu anderen Methoden wie Konvektion oder Strahlungserwärmung ein.
-
Komplexe Kontrollanforderungen
- Robuste Regelungsalgorithmen sind erforderlich, um Stromrichter für unterschiedliche Induktionsheizlasten und Betriebspunkte zu steuern.
- Systeme mit mehreren Spulen stellen zusätzliche Herausforderungen dar und erfordern Echtzeit-Identifikation und adaptive Algorithmen für optimale Leistung.
- Diese komplexe Steuerung kann die Kosten und Schwierigkeiten bei der Implementierung von induktiven Heizsystemen erhöhen.
-
Grenzen der Flächenheizung
- Die Induktionserwärmung ist am effektivsten für die Oberflächenerwärmung, die für Anwendungen, die eine gleichmäßige Erwärmung des gesamten Materials erfordern, möglicherweise nicht geeignet ist.
- Dies schränkt seine Verwendung bei bestimmten Wärmebehandlungsverfahren ein, bei denen eine tiefe oder volumetrische Erwärmung erforderlich ist.
-
Bedenken hinsichtlich der Energieeffizienz
- Die induktive Erwärmung kann zwar für bestimmte Anwendungen energieeffizient sein, aber die erforderlichen Hochfrequenzgeneratoren und Netzteile verbrauchen viel Energie.
- Ineffizienzen im System, wie schlechte induktive Kopplung oder Wärmeverluste, können die Gesamtenergieeffizienz weiter verringern.
-
Wartung und betriebliche Herausforderungen
- Die spezielle Beschaffenheit von induktiven Erwärmungsanlagen erfordert häufig eine regelmäßige Wartung und Fehlersuche durch qualifizierte Techniker.
- Betriebliche Herausforderungen, wie das Management hoher Stromdichten und die Sicherstellung einer ordnungsgemäßen Ausrichtung, können zu Ausfallzeiten und erhöhten Betriebskosten führen.
-
Begrenzte Flexibilität für unterschiedliche Anwendungen
- Die Notwendigkeit kundenspezifischer Induktoren und die Abhängigkeit von den Materialeigenschaften schränken die Anpassungsfähigkeit der induktiven Erwärmung für verschiedene Anwendungen ein.
- Andere Erhitzungsmethoden, wie z. B. Gas- oder Elektroöfen, bieten möglicherweise eine größere Flexibilität für eine breitere Palette von Materialien und Verfahren.
Zusammenfassend lässt sich sagen, dass die induktive Erwärmung zwar Präzision und Effizienz in bestimmten Anwendungen bietet, ihre Nachteile - wie hohe Kosten, begrenzte Veredelungskapazität und Probleme bei der Wärmeverteilung und -steuerung - sie jedoch für bestimmte Szenarien weniger geeignet machen. Das Verständnis dieser Einschränkungen ist entscheidend für fundierte Entscheidungen bei der Auswahl von Erwärmungsmethoden für industrielle oder Fertigungsprozesse.
Zusammenfassende Tabelle:
Nachteil | Beschreibung |
---|---|
Hohe Anfangsinvestition | Erhebliche Vorlaufkosten für Ausrüstung und qualifiziertes Personal. |
Fehlende Raffineriekapazitäten | Kann keine Materialien verfeinern; erfordert vorgereinigte Ladungsmaterialien. |
Bedarf an dedizierten Induktoren | Kundenspezifische Induktoren sind teuer und schränken die Flexibilität ein. |
Herausforderungen bei der Wärmeverteilung | Eine ungleichmäßige Erwärmung kann zu ungleichmäßigen Materialeigenschaften führen. |
Abhängigkeit von der Wärmeleitfähigkeit | Begrenzte Wirksamkeit bei Materialien mit schlechter Wärmeleitfähigkeit. |
Komplexe Kontrollanforderungen | Erfordert robuste Algorithmen für unterschiedliche Lasten und Betriebspunkte. |
Grenzen der Flächenheizung | Nicht geeignet für Tiefen- oder Gleichmäßigkeitsheizungen. |
Bedenken hinsichtlich der Energieeffizienz | Hoher Energieverbrauch und potenzielle Ineffizienzen. |
Herausforderungen bei der Wartung | Erfordert qualifizierte Techniker und regelmäßige Wartung. |
Begrenzte Flexibilität | Weniger anpassungsfähig für verschiedene Anwendungen im Vergleich zu anderen Heizmethoden. |
Benötigen Sie Hilfe bei der Auswahl der richtigen Heizmethode für Ihre Anwendung? Kontaktieren Sie unsere Experten noch heute für eine persönliche Beratung!