Die Sputterdeposition ist eine weit verbreitete Technik für die Abscheidung von Dünnschichten. Sie ist jedoch mit mehreren Nachteilen verbunden, die ihre Effizienz, Kosten und Anwendungsmöglichkeiten beeinträchtigen können.Dazu gehören Probleme wie Überhitzung, Ladungsaufbau, hohe Materialkosten, Schwierigkeiten bei der Kontrolle der Stöchiometrie und Herausforderungen beim reaktiven Sputtern.Das Verständnis dieser Nachteile ist entscheidend für die Auswahl der geeigneten Abscheidungsmethode für bestimmte Anwendungen.
Die wichtigsten Punkte erklärt:
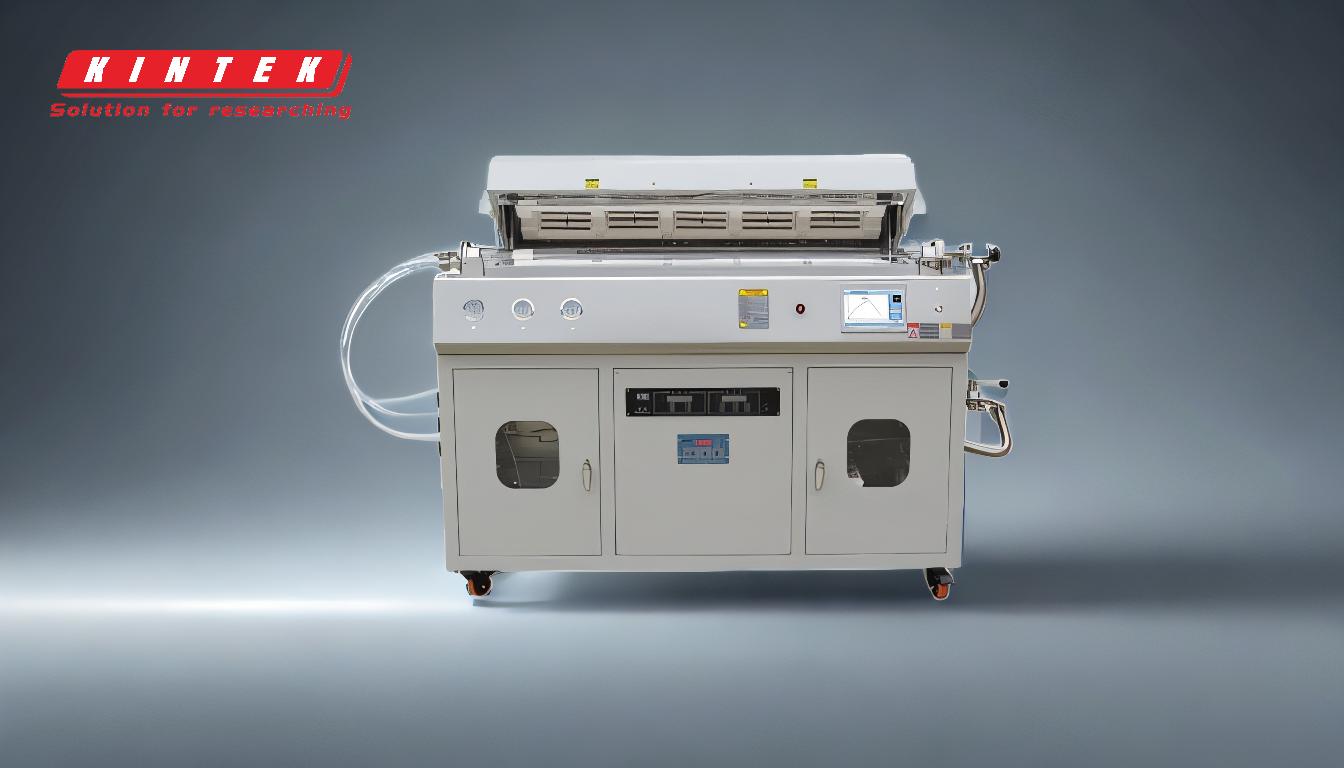
-
Überhitzung beim RF-Sputtern:
- Das RF-Sputtern erfordert eine höhere Leistungsaufnahme zur Erzeugung von Funkwellen, was zu Überhitzung führen kann.Dies ist besonders problematisch bei Anwendungen, bei denen eine präzise Temperaturkontrolle erforderlich ist, um die Integrität des Substrats oder die Qualität der abgeschiedenen Schicht zu erhalten.
-
Ladungsaufbau beim DC-Sputtern:
- Beim DC-Sputtern kann die große Anzahl von Ionen in der Kammer zu einer Aufladung des Targetmaterials führen.Dies kann zu Lichtbogenbildung und Beschädigung des Targets führen, was die Effizienz des Abscheidungsprozesses verringert und möglicherweise zu Defekten in der Dünnschicht führt.
-
Hohe Kosten der Materialien:
- Die beim Sputtern verwendeten Materialien, insbesondere Metalle, können recht teuer sein.Diese hohen Kosten können den Einsatz des Sputterns bei bestimmten Anwendungen einschränken, bei denen Budgetbeschränkungen eine wichtige Rolle spielen.
-
Schwierige Kontrolle der Stöchiometrie:
- Das Erreichen der gewünschten chemischen Zusammensetzung (Stöchiometrie) in der abgeschiedenen Schicht kann eine Herausforderung sein.Dies gilt insbesondere für komplexe Werkstoffe, bei denen eine genaue Kontrolle über die Abscheidung mehrerer Elemente erforderlich ist.
-
Herausforderungen beim reaktiven Sputtern:
- Das reaktive Sputtern, bei dem reaktive Gase zur Bildung von Verbindungen auf dem Substrat eingesetzt werden, kann zu unerwünschten Ergebnissen führen.Dazu gehören die Bildung nicht stöchiometrischer Verbindungen oder das Einbringen von Verunreinigungen, die die Leistung der Dünnschicht beeinträchtigen können.
-
Komplexität und Kosten der Ausrüstung:
- Sputtersysteme sind komplex und erfordern beträchtliche Investitionen in Bezug auf Ausrüstung und Wartung.Die Notwendigkeit von Hochvakuumbedingungen und einer präzisen Kontrolle der Prozessparameter erhöht die Gesamtkosten und die Komplexität des Systems.
-
Begrenzte Abscheideraten:
- Im Vergleich zu anderen Abscheidetechniken können beim Sputtern relativ niedrige Abscheidungsraten erzielt werden.Dies kann bei Fertigungsverfahren mit hohem Durchsatz, bei denen Geschwindigkeit ein entscheidender Faktor ist, ein Nachteil sein.
-
Potenzial für Kontamination:
- Beim Sputtern können Verunreinigungen in die Dünnschicht gelangen, insbesondere wenn die Vakuumkammer oder das Targetmaterial nicht ausreichend sauber ist.Dies kann die Qualität und Leistung des Endprodukts beeinträchtigen.
Die Kenntnis dieser Nachteile ist eine wesentliche Voraussetzung für fundierte Entscheidungen über den Einsatz der Sputtering-Beschichtung in verschiedenen Anwendungen.Es bietet zwar viele Vorteile, wie z. B. hochwertige dünne Schichten und vielseitige Materialien, aber die Nachteile müssen sorgfältig bedacht werden, um die besten Ergebnisse für bestimmte Projekte zu erzielen.
Zusammenfassende Tabelle:
Benachteiligung | Beschreibung |
---|---|
Überhitzung beim RF-Sputtern | Eine hohe Leistungsaufnahme führt zu Überhitzung und beeinträchtigt die Integrität des Substrats und die Qualität der Schichten. |
Ladungsaufbau beim DC-Sputtern | Ionenakkumulation führt zu Lichtbögen, die das Target beschädigen und die Abscheidungseffizienz verringern. |
Hohe Kosten für Materialien | Teure Materialien, insbesondere Metalle, schränken budgetabhängige Anwendungen ein. |
Schwierige Kontrolle der Stöchiometrie | Herausforderungen beim Erreichen einer präzisen chemischen Zusammensetzung für komplexe Materialien. |
Herausforderungen beim reaktiven Sputtern | Reaktive Gase können zu nicht-stöchiometrischen Verbindungen oder Verunreinigungen führen, die die Leistung des Films beeinträchtigen. |
Komplexität und Kosten der Ausrüstung | Hohe Investitionen in Ausrüstung und Wartung aufgrund der Systemkomplexität und der Vakuumanforderungen. |
Begrenzte Abscheidungsraten | Langsamere Abscheidungsraten im Vergleich zu anderen Techniken, was sich auf Prozesse mit hohem Durchsatz auswirkt. |
Potenzielle Verunreinigung | Verunreinigungen aus Vakuumkammern oder Targets können die Filmqualität und -leistung beeinträchtigen. |
Benötigen Sie Hilfe bei der Auswahl der richtigen Abscheidungsmethode für Ihr Projekt? Kontaktieren Sie noch heute unsere Experten für maßgeschneiderte Lösungen!