Die thermische Verdampfung ist eine weit verbreitete Technik der physikalischen Gasphasenabscheidung (PVD). Sie hat jedoch mehrere Nachteile, die ihre Effizienz, Skalierbarkeit und die Qualität der abgeschiedenen Schichten beeinträchtigen können.Zu den wichtigsten Nachteilen gehören ein hoher Gehalt an Verunreinigungen, eine geringe Schichtqualität, eine mäßige Schichtspannung, Schwierigkeiten beim Erreichen einer gleichmäßigen Schichtdicke und die Empfindlichkeit gegenüber Verunreinigungen.Darüber hinaus erschweren Probleme wie Bootsrisse, Temperaturschocks und begrenzte Skalierbarkeit den Einsatz.Zwar können einige dieser Probleme durch Techniken wie Ionenunterstützung oder sorgfältige Energieverwaltung gemildert werden, doch stellen sie für bestimmte Anwendungen nach wie vor erhebliche Einschränkungen dar.
Die wichtigsten Punkte werden erklärt:
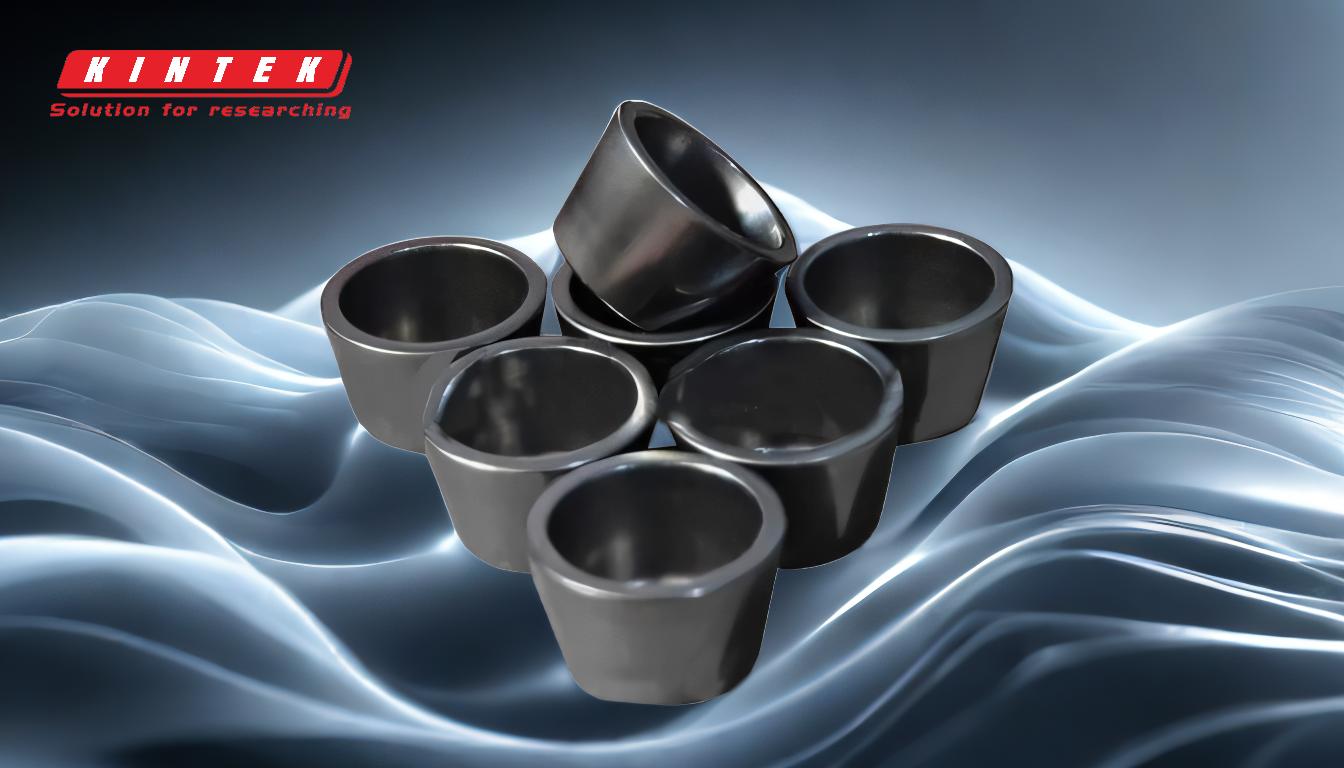
-
Hohe Verunreinigungsgrade
- Die thermische Verdampfung ist dafür bekannt, dass sie die höchsten Verunreinigungsgrade unter den PVD-Verfahren aufweist.Dies ist auf die mögliche Verunreinigung durch die Tiegel- oder Bootsmaterialien zurückzuführen, insbesondere bei hohen Temperaturen.
- Graphittiegel, die häufig für die Hochtemperaturverdampfung verwendet werden, können Kohlenstoffverunreinigungen in das abgeschiedene Material einbringen.
- Verunreinigungsfreie Tiegel sind teuer, was es schwierig macht, hochreine Beschichtungen kosteneffizient zu erzielen.
-
Niedrige Dichte der Schichten
- Durch thermisches Aufdampfen hergestellte Filme haben in der Regel eine geringe Dichte, was ihre mechanischen und optischen Eigenschaften beeinträchtigen kann.
- Dieses Problem kann teilweise mit Hilfe von Ionenunterstützungstechniken gelöst werden, die jedoch die Komplexität und die Kosten des Verfahrens erhöhen.
-
Mäßige Filmspannung
- Bei der thermischen Verdampfung entstehen oft Filme mit mäßigen Spannungen, die im Laufe der Zeit zu Rissen oder Delaminationen führen können.
- Diese Spannungen werden in erster Linie durch die ungleiche Wärmeausdehnung zwischen dem Substrat und dem abgeschiedenen Material während der Abkühlung verursacht.
-
Herausforderungen bei der Erzielung einer gleichmäßigen Schichtdicke
- Ohne den Einsatz von Masken oder Planetensystemen ist es schwierig, eine gleichmäßige Schichtdicke zu erreichen.
- Diese Einschränkung macht die thermische Verdampfung weniger geeignet für Anwendungen, die präzise, gleichmäßige Beschichtungen auf großen oder komplexen Oberflächen erfordern.
-
Anfälligkeit für Verunreinigungen
- Das Verfahren erfordert eine Hochvakuumumgebung, um Verunreinigungen auf ein Minimum zu reduzieren, was die Komplexität und die Kosten des Verfahrens erhöht.
- Verunreinigungen durch die Tiegel- oder Schiffchenmaterialien können die Qualität der abgeschiedenen Schichten weiter verschlechtern.
-
Rissbildung in der Schale und Temperaturschock
- Risse im Boot sind ein häufiges Problem, das durch die Legierung zwischen dem Boot und den Verdampfermaterialien bei hohen Temperaturen verursacht wird.Ist das Boot gerissen, muss es ersetzt werden, was die Kosten erhöht.
- Auch Temperaturschocks, die durch schnelles Aufheizen und Abkühlen entstehen, können zu Rissen im Boot führen.Um dies abzumildern, muss die Leistung gleichmäßig hoch- und runtergefahren werden, was den Prozess noch komplexer macht.
-
Begrenzte Skalierbarkeit
- Die thermische Verdampfung ist im Vergleich zu anderen PVD-Verfahren weniger skalierbar, insbesondere bei geringeren Abscheideraten.
- Diese Einschränkung macht es weniger geeignet für großtechnische Anwendungen, bei denen ein hoher Durchsatz erforderlich ist.
-
Temperaturbeschränkungen und Kühlungsstress
- Der Abscheidungsprozess unterliegt Temperaturbeschränkungen, die sich auf die Arten von Materialien auswirken können, die verdampft werden können.
- Beim Abkühlen können unerwünschte Spannungen entstehen, die die Integrität der abgeschiedenen Schichten weiter beeinträchtigen.
-
Mäßige Systemkomplexität und Kosten
- Obwohl thermische Verdampfungssysteme im Allgemeinen einfacher sind als einige andere PVD-Methoden, sind sie immer noch mit mäßiger Komplexität und Kosten verbunden, insbesondere wenn zusätzliche Funktionen wie Ionenunterstützung oder Planetensysteme erforderlich sind.
-
Begrenzte Materialkompatibilität
- Nicht alle Materialien sind für die thermische Verdampfung geeignet, insbesondere solche mit sehr hohen Schmelzpunkten oder solche, die mit Tiegelmaterialien reagieren.
- Dies schränkt die Vielseitigkeit der Technik für bestimmte fortgeschrittene Anwendungen ein.
Zusammenfassend lässt sich sagen, dass die thermische Verdampfung zwar eine vielseitige und weit verbreitete Abscheidungstechnik ist, dass sie aber aufgrund ihrer Nachteile - hohe Verunreinigungen, Filme mit geringer Dichte, mäßige Belastung und Schwierigkeiten bei der Erzielung von Gleichmäßigkeit - für bestimmte hochpräzise oder großtechnische Anwendungen weniger geeignet ist.Durch eine sorgfältige Prozessoptimierung und den Einsatz von Hilfstechniken können einige dieser Probleme gemildert werden, sie bleiben jedoch inhärente Grenzen der Methode.
Zusammenfassende Tabelle:
Benachteiligung | Erläuterung |
---|---|
Hohe Verunreinigungsgrade | Verunreinigungen von Tiegeln oder Booten, insbesondere bei hohen Temperaturen. |
Filmqualität mit geringer Dichte | Den Folien fehlt es an Dichte, was die mechanischen und optischen Eigenschaften beeinträchtigt. |
Mäßiger Filmstress | Spannungen aufgrund ungleichmäßiger Wärmeausdehnung können Risse oder Delaminationen verursachen. |
Gleichmäßige Dicke - eine Herausforderung | Schwierig zu erreichen ohne Masken oder Planetensysteme. |
Anfälligkeit für Verunreinigungen | Erfordert Hochvakuumumgebungen, was die Komplexität und die Kosten erhöht. |
Rissbildung im Boot und thermischer Schock | Rissbildung aufgrund von Legierungsbildung oder thermischen Schocks, was ein sorgfältiges Energiemanagement erfordert. |
Begrenzte Skalierbarkeit | Aufgrund der geringeren Abscheideraten weniger geeignet für groß angelegte Anwendungen. |
Temperatureinschränkungen | Materialbeschränkungen und Kühlungsbelastungen beeinträchtigen die Integrität des Films. |
Mäßige Systemkomplexität | Zusätzliche Funktionen wie Ionenunterstützung erhöhen Kosten und Komplexität. |
Begrenzte Materialkompatibilität | Nicht alle Materialien sind geeignet, insbesondere solche mit hohem Schmelzpunkt oder reaktivem Material. |
Benötigen Sie Hilfe bei der Optimierung Ihres thermischen Verdampfungsprozesses? Kontaktieren Sie noch heute unsere Experten !