Die thermische Gasphasenabscheidung (TVD), insbesondere die thermische Verdampfung, ist aufgrund ihrer Einfachheit und Kosteneffizienz eine weit verbreitete Technik für die Dünnschichtabscheidung.Sie ist jedoch mit mehreren Nachteilen verbunden, die ihre Anwendung in bestimmten Szenarien einschränken.Zu diesen Nachteilen gehören die schlechte Gleichmäßigkeit des Films, hohe Verunreinigungen, eine geringe Dichte des Films, eine mäßige Spannung des Films und eine begrenzte Skalierbarkeit.Außerdem ist die thermische Verdampfung auf Materialien mit relativ niedrigen Schmelzpunkten beschränkt und anfällig für Verunreinigungen aus dem Tiegel.Aufgrund dieser Einschränkungen eignet sich das Verfahren weniger für fortschrittliche Anwendungen, die hochreine, hochdichte oder mehrkomponentige Materialien erfordern.
Die wichtigsten Punkte werden erklärt:
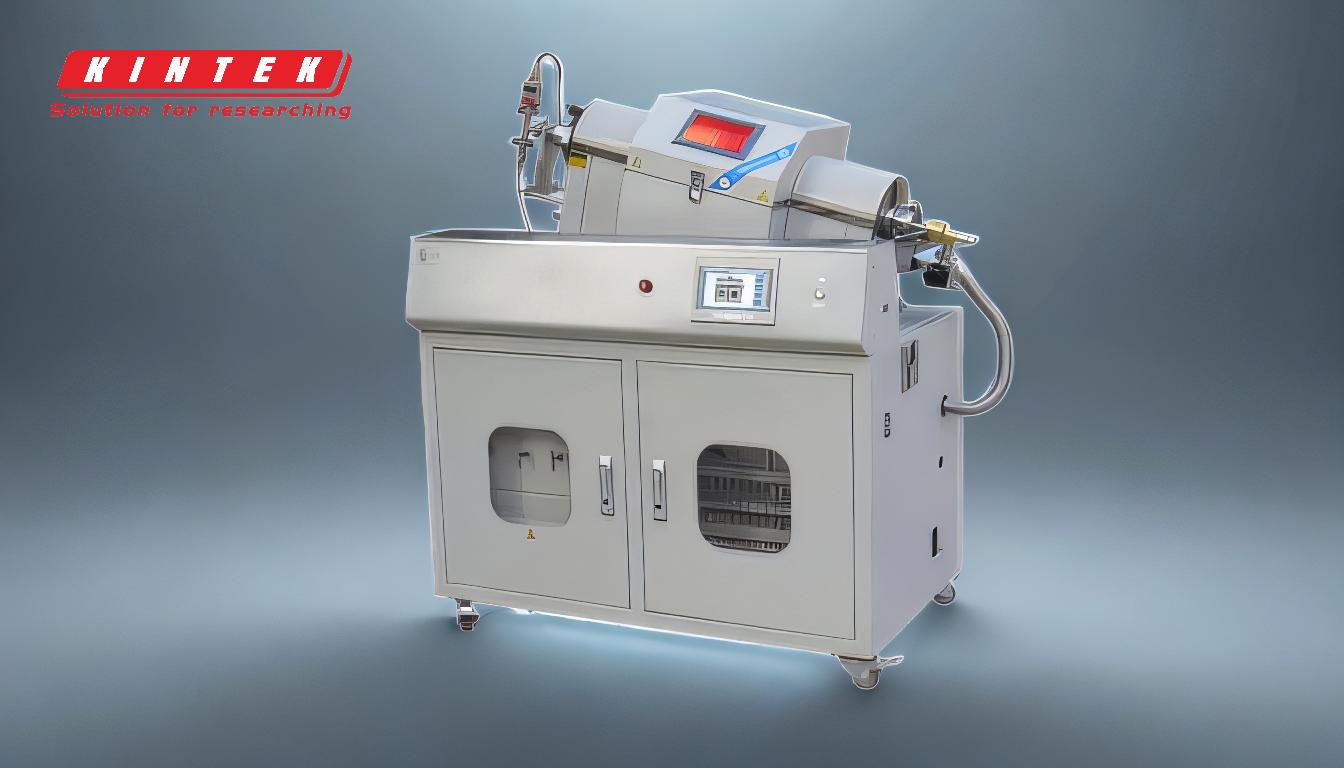
-
Schlechte Filmgleichmäßigkeit:
- Ohne den Einsatz von Planetensystemen und Masken führt die thermische Verdampfung häufig zu einer ungleichmäßigen Schichtdicke auf dem Substrat.Dies ist ein erheblicher Nachteil für Anwendungen, die präzise und gleichmäßige Beschichtungen erfordern.
- Der Mangel an Einheitlichkeit kann zu uneinheitlichen Materialeigenschaften führen, was besonders in Branchen wie Elektronik und Optik problematisch ist.
-
Hohe Verunreinigungsgrade:
- Die thermische Verdampfung weist in der Regel den höchsten Verunreinigungsgrad unter den PVD-Verfahren auf.Dies ist auf die Verunreinigung durch den Tiegel und das Ausgangsmaterial der Verdampfung zurückzuführen.
- Ein hoher Verunreinigungsgrad kann die Leistung der abgeschiedenen Schicht beeinträchtigen, so dass sie für hochreine Anwendungen wie die Halbleiterherstellung nicht geeignet ist.
-
Low-Density-Filmqualität:
- Durch thermisches Aufdampfen hergestellte Schichten haben oft eine geringe Dichte, was ihre mechanischen und elektrischen Eigenschaften beeinträchtigen kann.Dies kann zwar durch ionenunterstützte Techniken verbessert werden, macht das Verfahren jedoch komplexer und teurer.
- Filme mit geringer Dichte sind anfälliger für Defekte und bieten möglicherweise nicht die erforderliche Haltbarkeit für bestimmte Anwendungen.
-
Mäßige Folienspannung:
- Die durch thermische Verdampfung abgeschiedenen Schichten weisen häufig eine mäßige Spannung auf, was im Laufe der Zeit zu Problemen wie Rissen oder Delamination führen kann.
- Dies ist besonders problematisch bei Anwendungen, bei denen die Schicht mechanischen Belastungen oder Temperaturschwankungen standhalten muss.
-
Begrenzte Skalierbarkeit:
- Die thermische Verdampfung lässt sich nicht ohne weiteres für großflächige oder durchsatzstarke Anwendungen skalieren.Das Verfahren ist im Allgemeinen langsamer und weniger effizient als andere Abscheidungsmethoden wie Sputtern oder chemische Gasphasenabscheidung (CVD).
- Diese Einschränkung macht es für die industrielle Produktion weniger attraktiv.
-
Grenzen des Materials:
- Die thermische Verdampfung eignet sich vor allem für Materialien mit relativ niedrigem Schmelzpunkt.Es eignet sich nicht für die Abscheidung von hochschmelzenden Metallen oder Materialien, die sehr hohe Temperaturen erfordern.
- Dies schränkt die Palette der Materialien ein, die mit dieser Methode abgeschieden werden können, und begrenzt ihre Vielseitigkeit.
-
Verunreinigung des Tiegels:
- Die Verwendung eines Tiegels bei der thermischen Verdampfung kann Verunreinigungen in die abgeschiedene Schicht einbringen, was deren Reinheit und Qualität weiter verringert.
- Dies ist ein erheblicher Nachteil für Anwendungen, die hochreine Materialien erfordern, wie z. B. in der Halbleiter- oder Optikindustrie.
-
Herausforderungen bei Multikomponenten-Materialien:
- Die thermische Verdampfung ist für die Abscheidung von Multikomponenten-Materialien weniger effektiv, da der Dampfdruck, die Keimbildung und die Wachstumsraten der verschiedenen Komponenten variieren.
- Dies macht es schwierig, eine homogene Zusammensetzung zu erreichen, die für viele fortschrittliche Anwendungen entscheidend ist.
Zusammenfassend lässt sich sagen, dass die thermische Verdampfung zwar eine einfache und kosteneffiziente Methode für die Dünnschichtabscheidung ist, dass sie sich aber aufgrund ihrer Nachteile - wie schlechte Homogenität, hoher Verunreinigungsgrad, geringe Schichtdichte, mäßige Belastung, begrenzte Skalierbarkeit, Materialbeschränkungen, Tiegelverschmutzung und Probleme mit Mehrkomponentenmaterialien - weniger für fortschrittliche oder hochpräzise Anwendungen eignet.Weitere Informationen über die thermische Verdampfung finden Sie unter Thermische Verdampfung .
Zusammenfassende Tabelle :
Benachteiligung | Beschreibung |
---|---|
Schlechte Gleichmäßigkeit des Films | Ungleichmäßige Dicke, uneinheitliche Materialeigenschaften, problematisch für die Elektronik. |
Hohe Verunreinigungsgrade | Verunreinigung durch Tiegel und Ausgangsmaterial, ungeeignet für hochreine Anwendungen. |
Filmqualität mit geringer Dichte | Anfällig für Defekte, beeinträchtigt mechanische und elektrische Eigenschaften. |
Mäßiger Filmstress | Führt zu Rissbildung oder Delamination, Probleme bei mechanischer oder thermischer Belastung. |
Begrenzte Skalierbarkeit | Nicht geeignet für großflächige oder industrielle Anwendungen mit hohem Durchsatz. |
Materialbeschränkungen | Begrenzt auf Materialien mit niedrigem Schmelzpunkt, was die Vielseitigkeit einschränkt. |
Verunreinigung des Tiegels | Führt Verunreinigungen ein und verringert die Reinheit und Qualität der Folie. |
Herausforderungen bei Multikomponenten-Materialien | Es ist schwierig, eine homogene Zusammensetzung für moderne Anwendungen zu erreichen. |
Benötigen Sie eine bessere Lösung für die Abscheidung von Dünnschichten? Kontaktieren Sie noch heute unsere Experten um fortschrittliche Alternativen zu erkunden!