Sputtern ist ein vakuumbasiertes Verfahren zur Abscheidung von Dünnschichten, bei dem Ionen ein Zielmaterial beschießen, wodurch Atome herausgeschleudert werden und sich auf einem Substrat ablagern.Der Prozess wird von mehreren Schlüsselparametern beeinflusst, darunter die Energie der einfallenden Ionen, die Masse der Ionen und der Zielatome, der Einfallswinkel, die Sputterausbeute, der Kammerdruck und die Art der Stromquelle (Gleichstrom oder Hochfrequenz).Diese Faktoren bestimmen die Effizienz, die Abscheidungsrate und die Qualität der Dünnschicht.Das Verständnis dieser Parameter ist entscheidend für die Optimierung des Sputterprozesses für bestimmte Anwendungen, wie die Herstellung hochreiner Metall- oder Oxidschichten.
Die wichtigsten Punkte werden erklärt:
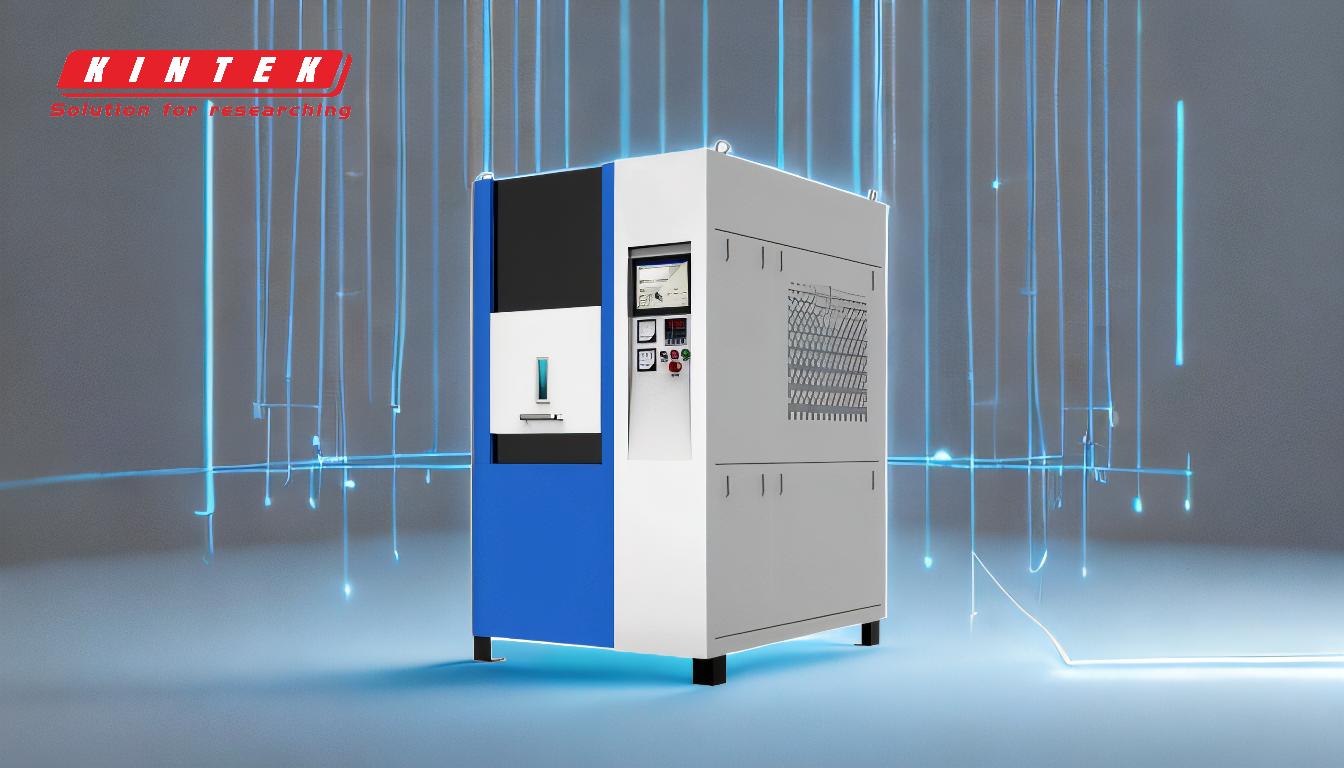
-
Einfallende Ionenenergie:
- Die Energie der Ionen, die das Targetmaterial beschießen, hat einen erheblichen Einfluss auf die Sputterausbeute, d. h. die Anzahl der pro einfallendem Ion ausgestoßenen Targetatome.Eine höhere Ionenenergie erhöht in der Regel die Sputterausbeute, aber eine zu hohe Energie kann zu unerwünschten Effekten wie Substratschäden oder Schichtspannungen führen.
-
Masse der Ionen und Zielatome:
- Die Masse sowohl der einfallenden Ionen als auch der Target-Atome spielt eine entscheidende Rolle beim Sputtering-Prozess.Schwerere Ionen können mehr Impuls auf die Zielatome übertragen, was zu einer höheren Sputterausbeute führt.In ähnlicher Weise bestimmt die Masse der Zielatome, wie leicht sie von der Oberfläche ausgestoßen werden können.
-
Einfallswinkel:
- Der Winkel, in dem die Ionen auf die Oberfläche des Targets treffen, beeinflusst die Sputterausbeute.Im Allgemeinen kann ein schräger Winkel (nicht senkrecht) die Sputterausbeute aufgrund eines effizienteren Energietransfers erhöhen.Extreme Winkel können jedoch die Ausbeute aufgrund von Streifkollisionen verringern.
-
Sputtering Ausbeute:
- Die Sputterausbeute ist ein Maß für die Effizienz des Sputterprozesses, definiert als die Anzahl der pro einfallendem Ion ausgestoßenen Targetatome.Sie variiert je nach Targetmaterial, Ionenenergie, Masse und Einfallswinkel.Die Optimierung dieser Faktoren ist für das Erreichen der gewünschten Abscheideraten und Schichtqualität von entscheidender Bedeutung.
-
Kammerdruck:
- Der Druck in der Zerstäubungskammer beeinflusst die mittlere freie Weglänge der ausgestoßenen Partikel und die Gesamtbedeckung des Substrats.Niedrigere Drücke werden in der Regel verwendet, um Kollisionen zu minimieren und eine gezieltere Abscheidung zu gewährleisten, während höhere Drücke die Bedeckung verbessern, aber die Abscheideraten verringern können.
-
Art der Stromquelle (DC oder RF):
- Die Wahl zwischen Gleichstrom- (DC) und Hochfrequenz- (RF) Stromquellen beeinflusst den Sputterprozess in Bezug auf die Abscheidungsrate, die Materialverträglichkeit und die Kosten.Das Gleichstromsputtern wird üblicherweise für leitende Materialien verwendet, während das Hochfrequenzsputtern für isolierende Materialien geeignet ist, da es die Bildung von Ladungen verhindert.
-
Kinetische Energie der emittierten Teilchen:
- Die kinetische Energie der vom Target ausgestoßenen Partikel bestimmt ihre Richtung und wie sie sich auf dem Substrat ablagern.Eine höhere kinetische Energie kann zu einer besseren Haftung und dichteren Schichten führen, muss aber kontrolliert werden, um eine Beschädigung des Substrats oder Spannungen innerhalb der Schicht zu vermeiden.
-
Überschüssige Energie von Metall-Ionen:
- Die überschüssige Energie der Metallionen während des Sputterprozesses kann die Oberflächenmobilität erhöhen, was die Qualität der abgeschiedenen Schicht beeinträchtigt.Die richtige Steuerung dieser Energie kann zu glatteren und gleichmäßigeren Schichten führen und die Gesamtleistung der abgeschiedenen Schicht verbessern.
Das Verständnis und die Optimierung dieser Parameter sind von entscheidender Bedeutung, um qualitativ hochwertige dünne Schichten mit den gewünschten Eigenschaften für verschiedene Anwendungen, von der Elektronik bis zu optischen Beschichtungen, zu erzielen.
Zusammenfassende Tabelle:
Parameter | Einfluss auf den Sputterprozess |
---|---|
Energie der einfallenden Ionen | Höhere Energie erhöht die Sputterausbeute, kann aber zu Substratschäden führen. |
Masse der Ionen und Zielatome | Schwerere Ionen und Targetatome erhöhen die Sputterausbeute durch Impulsübertragung. |
Einfallswinkel | Schräge Winkel verbessern die Ausbeute, extreme Winkel verringern sie. |
Sputtering-Ausbeute | Misst die Effizienz; hängt von Material, Ionenenergie, Masse und Winkel ab. |
Kammerdruck | Niedriger Druck gewährleistet eine gezielte Ablagerung; höherer Druck verbessert die Abdeckung. |
Stromquelle (DC oder RF) | DC für leitende Materialien; RF für isolierende Materialien, um Ladungsaufbau zu verhindern. |
Kinetische Energie der Partikel | Eine höhere Energie verbessert die Haftung, muss aber kontrolliert werden, um Schäden am Substrat zu vermeiden. |
Überschüssige Energie der Metall-Ionen | Erhöht die Oberflächenbeweglichkeit, was zu glatteren und gleichmäßigeren Schichten führt. |
Sind Sie bereit, Ihr Sputtering-Verfahren zu optimieren? Kontaktieren Sie noch heute unsere Experten für maßgeschneiderte Lösungen!