Sputtern ist eine weit verbreitete Technik der physikalischen Gasphasenabscheidung (PVD) für das Aufbringen dünner Schichten, insbesondere in Branchen wie Halbleiter, optische Geräte und Solarzellen.Bei diesem Verfahren werden Atome aus einem Zielmaterial mit Hilfe eines hochenergetischen Teilchenbeschusses auf ein Substrat geschleudert.Die dabei entstehenden Schichten sind für ihre Gleichmäßigkeit, Dichte, Reinheit und Haftung bekannt.Zu den wichtigsten Parametern, die den Sputterprozess beeinflussen, gehören der Partialdruck der reaktiven Gase, die Gasverteilung in der Kammer, die Sputterdauer, die Materialmasse und die Energie der Partikel.Diese Faktoren bestimmen zusammen die Eigenschaften der Schicht, wie Dicke, Gleichmäßigkeit und Haftung, und machen das Sputtern zu einer vielseitigen und präzisen Methode für die Abscheidung dünner Schichten.
Die wichtigsten Punkte erklärt:
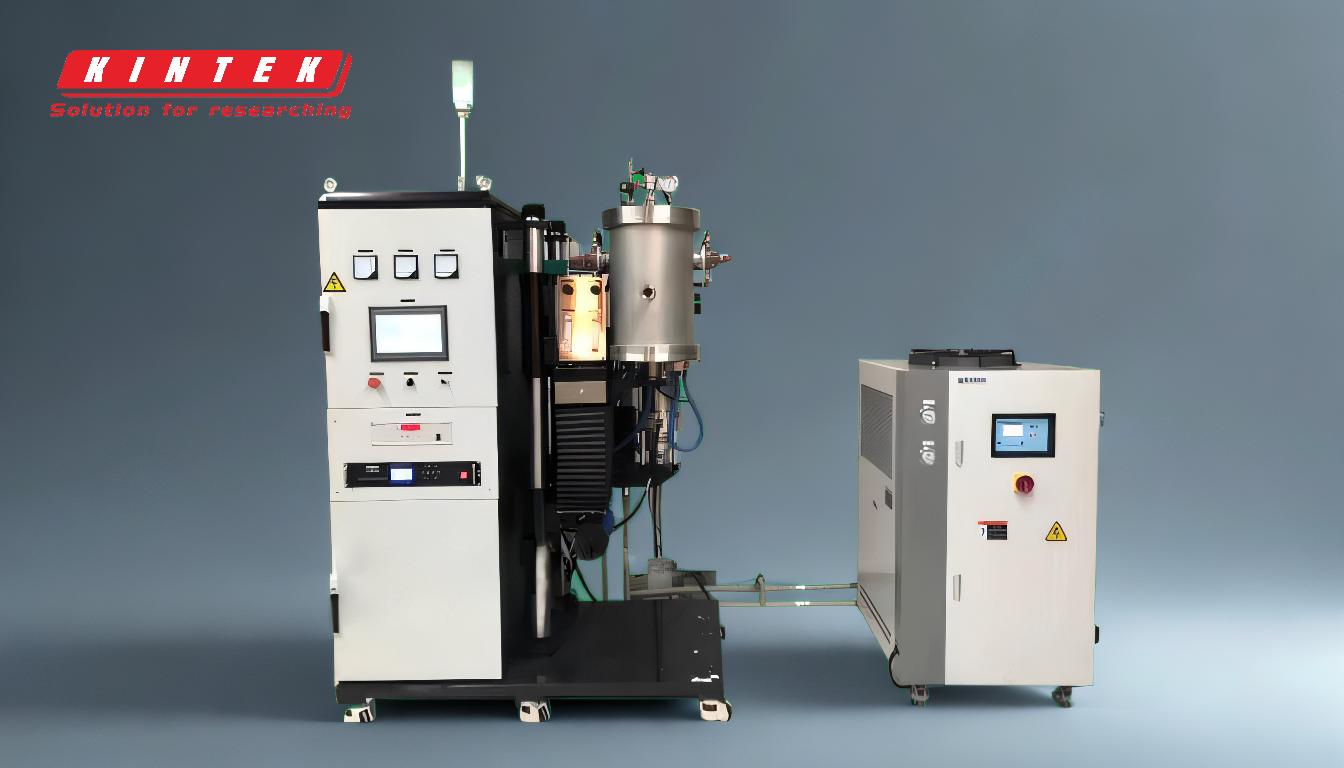
-
Überblick über den Sputtering-Prozess:
- Sputtern ist ein PVD-Verfahren, bei dem Atome, Ionen oder Moleküle aus einem Zielmaterial herausgeschleudert und auf ein Substrat aufgebracht werden.
- Dieses Verfahren ist in Branchen wie der Halbleiterindustrie, der optischen Industrie und der Solarindustrie weit verbreitet, da es die Herstellung hochwertiger Dünnschichten ermöglicht.
-
Eigenschaften des Films:
- Gesputterte Schichten sind bekannt für ihre hervorragende Gleichmäßigkeit, Dichte, Reinheit und Haftung.
- Diese Eigenschaften machen das Sputtern zu einer bevorzugten Methode für Anwendungen, die präzise und zuverlässige dünne Schichten erfordern.
-
Einfluss von reaktiven Gasen:
- Beim reaktiven Sputtern werden die Eigenschaften der Schicht durch den Partialdruck des reaktiven Gases beeinflusst.
- Die Verteilung des reaktiven Gases in der Kammer und die Mechanismen, mit denen das Gas in das Plasma eingebracht wird, spielen ebenfalls eine entscheidende Rolle bei der Bestimmung der Eigenschaften der Schicht.
-
Filmdicke:
- Die Dicke der Dünnschicht wird von mehreren Faktoren bestimmt, unter anderem von der Dauer des Sputtering-Prozesses.
- Auch die Masse der beteiligten Materialien und das Energieniveau der Beschichtungspartikel, das von einigen zehn bis zu Tausenden von Elektronenvolt reichen kann, beeinflussen die Schichtdicke erheblich.
-
Energieniveaus:
- Das Energieniveau der Beschichtungspartikel ist ein kritischer Parameter beim Sputtern.
- Höhere Energieniveaus können zu einem effizienteren Ausstoß von Atomen aus dem Zielmaterial führen, was eine bessere Schichtqualität und Haftung zur Folge hat.
-
Anwendungen:
- Sputtern wird in einer Vielzahl von Anwendungen eingesetzt, u. a. bei der Herstellung von Halbleitern, Plattenlaufwerken, CDs und optischen Geräten.
- Die Fähigkeit, Schichten mit präzisen Eigenschaften zu erzeugen, macht das Sputtern zu einem unverzichtbaren Verfahren für fortschrittliche technologische Anwendungen.
Durch das Verständnis und die Kontrolle dieser Sputterparameter können die Hersteller die Eigenschaften dünner Schichten auf spezifische Anwendungsanforderungen abstimmen und so eine hohe Leistung und Zuverlässigkeit ihrer Produkte gewährleisten.
Zusammenfassende Tabelle:
Parameter | Beschreibung |
---|---|
Reaktiver Gasdruck | Beeinflusst die Filmeigenschaften durch Partialdruck und Gasverteilung. |
Dauer des Sputterns | Bestimmt Schichtdicke und Gleichmäßigkeit. |
Materialmasse | Beeinflusst die Geschwindigkeit und Qualität des Atomauswurfs aus dem Ziel. |
Energieniveaus der Teilchen | Höhere Energieniveaus verbessern die Filmhaftung und -qualität (zehn bis tausende von eV). |
Anwendungen | Halbleiter, optische Geräte, Solarzellen und mehr. |
Benötigen Sie Hilfe bei der Optimierung Ihres Sputtering-Prozesses? Kontaktieren Sie noch heute unsere Experten für maßgeschneiderte Lösungen!