Graphit ist ein vielseitiges Material, das aufgrund seiner einzigartigen Eigenschaften wie geringe Dichte, hohe Wärmeleitfähigkeit und hervorragendes Emissionsvermögen in verschiedenen industriellen Anwendungen, einschließlich Ofenkammern, eingesetzt wird.Der Herstellungsprozess von Graphit umfasst mehrere kritische Schritte, von denen jeder zur endgültigen Qualität und Leistung des Materials beiträgt.Im Folgenden werden die einzelnen Schritte bei der Herstellung von Graphit ausführlich erläutert, wobei der Schwerpunkt auf der Anwendung in Ofenkammern liegt.
Die wichtigsten Punkte werden erklärt:
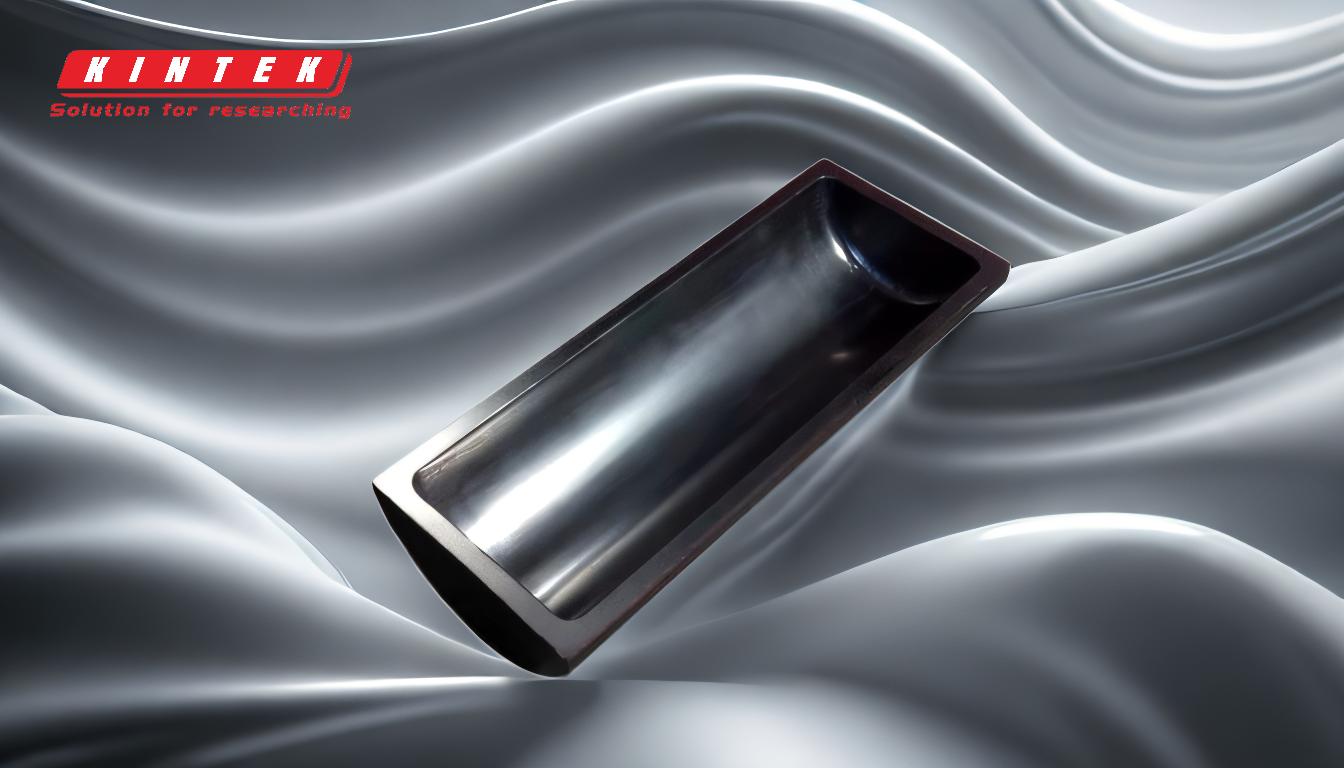
-
Auswahl der Rohmaterialien:
- Der erste Schritt bei der Herstellung von Graphit ist die Auswahl hochwertiger Rohstoffe.In der Regel wird Petrolkoks oder Steinkohlenteerpech als primäre Kohlenstoffquelle verwendet.Diese Materialien werden wegen ihres hohen Kohlenstoffgehalts und ihrer Reinheit ausgewählt, die für die Herstellung von Hochleistungsgraphit unerlässlich sind.
-
Kalzinierung:
- Die ausgewählten Rohstoffe werden einer Kalzinierung unterzogen, bei der sie unter Ausschluss von Sauerstoff auf hohe Temperaturen (etwa 1200 bis 1400 °C) erhitzt werden.Durch diesen Schritt werden flüchtige Bestandteile und Feuchtigkeit entfernt, was zu einem stabileren und reineren Kohlenstoffmaterial führt.Die Kalzinierung ist entscheidend für die strukturelle Integrität und thermische Stabilität des Graphitendprodukts.
-
Mischen und Verformen:
- Nach dem Kalzinieren wird das Kohlenstoffmaterial mit einem Bindemittel, in der Regel Steinkohlenteerpech, zu einem homogenen Gemisch vermischt.Dieses Gemisch wird dann mit verschiedenen Techniken wie Strangpressen, Formen oder isostatischem Pressen in die gewünschte Form gebracht.Der Formgebungsprozess ist entscheidend, um die erforderliche Dichte und mechanische Festigkeit des Graphits zu erreichen.
-
Backen:
- Die geformten Kohlenstoffformen werden in einem Graphit-Ofen bei Temperaturen zwischen 800°C und 1000°C.Das Brennen trägt zur Verkohlung des Bindemittels bei und verwandelt es in eine feste Kohlenstoffmatrix, die die Kohlenstoffpartikel zusammenbindet.Dieser Schritt ist entscheidend für die Entwicklung der ersten strukturellen Eigenschaften des Graphits.
-
Imprägnierung:
- Um die Dichte und die mechanischen Eigenschaften zu verbessern, werden die gebrannten Kohlenstoffformate häufig mit zusätzlichen kohlenstoffhaltigen Materialien imprägniert.Dazu werden die Formen in ein flüssiges Pech oder Harz getaucht und dann erneut gebrannt.Die Imprägnierung kann mehrfach wiederholt werden, um die gewünschten Eigenschaften zu erzielen.
-
Graphitierung:
- Der letzte und kritischste Schritt ist die Graphitierung, bei der die Kohlenstoffformen in einer inerten Atmosphäre auf extrem hohe Temperaturen (bis zu 3000°C) erhitzt werden.Durch diesen Prozess wird der amorphe Kohlenstoff in kristallinen Graphit umgewandelt, was seine thermische und elektrische Leitfähigkeit sowie seine mechanische Festigkeit erheblich verbessert.Die Graphitierung verleiht dem Graphit seine einzigartigen Eigenschaften, die ihn ideal für den Einsatz in Ofenkammern machen.
-
Bearbeitung und Veredelung:
- Nach der Graphitierung werden die Graphitblöcke auf die genauen Abmessungen bearbeitet, die für die jeweiligen Anwendungen erforderlich sind.Dazu gehören Schneiden, Bohren und Oberflächenbearbeitung, um eine perfekte Passform und optimale Leistung in den Ofenkammern zu gewährleisten.
-
Qualitätskontrolle und Prüfung:
- Der letzte Schritt umfasst eine strenge Qualitätskontrolle und Prüfung, um sicherzustellen, dass der Graphit die erforderlichen Spezifikationen erfüllt.Dazu gehören Prüfungen der Dichte, Porosität, Wärmeleitfähigkeit und mechanischen Festigkeit.Erst wenn der Graphit diese Tests bestanden hat, ist er für den Einsatz in Ofenkammern geeignet.
Durch die Befolgung dieser Schritte können die Hersteller hochwertigen Graphit herstellen, der sich gut für die Verwendung in Ofenkammern eignet und eine hervorragende thermische Leistung, Haltbarkeit und Reparaturfreundlichkeit bietet.Die einzigartigen Eigenschaften von Graphit, wie seine geringe Dichte und sein hoher Emissionsgrad, machen ihn zu einem idealen Material für die Herstellung effizienter und langlebiger Ofenkammern.
Zusammenfassende Tabelle:
Schritt | Beschreibung |
---|---|
Auswahl des Rohmaterials | Hochwertiger Petrolkoks oder Steinkohlenteerpech wird wegen seines hohen Kohlenstoffgehalts ausgewählt. |
Kalzinierung | Erhitzen von Rohstoffen auf 1200°C-1400°C, um flüchtige Bestandteile und Feuchtigkeit zu entfernen. |
Mischen und Verformen | Kohlenstoffmaterial wird mit einem Bindemittel gemischt und durch Strangpressen oder Formen in Form gebracht. |
Backen | Die Formen werden bei 800°C-1000°C gebrannt, um das Bindemittel zu karbonisieren. |
Imprägnierung | Die Formen werden in Pech/Harz getränkt und erneut eingebrannt, um die Dichte zu erhöhen. |
Graphitierung | Erhitzung auf 3000°C zur Umwandlung von amorphem Kohlenstoff in kristallinen Graphit. |
Bearbeitung und Endbearbeitung | Die Blöcke werden nach genauen Maßen geschnitten, gebohrt und fertiggestellt. |
Qualitätskontrolle | Strenge Prüfungen auf Dichte, Porosität, Wärmeleitfähigkeit und Festigkeit. |
Sie benötigen hochwertigen Graphit für Ihre Ofenkammern? Kontaktieren Sie noch heute unsere Experten um mehr zu erfahren!