Das Spark-Plasma-Sinterverfahren (SPS) ist ein fortschrittliches pulvermetallurgisches Verfahren, bei dem elektrischer Strom und Druck eingesetzt werden, um Materialien in einem einzigen Schritt zu synthetisieren.Es ist auch unter anderen Namen bekannt, wie z. B. Pulsed Electric Current Sintering (PECS), Field Assisted Sintering Technique (FAST) oder Plasma-Activated Sintering (PAS).Bei diesem Verfahren wird ein modifiziertes Heißpressverfahren angewandt, bei dem elektrischer Strom direkt durch die Pressmatrize (in der Regel Graphit) und das Bauteil fließt, was eine schnelle Erwärmung und kurze Verarbeitungszeiten ermöglicht.SPS zeichnet sich durch eine präzise Steuerung von Temperatur, Druck und Heizrate aus und ermöglicht die Herstellung von Materialien mit einzigartigen Mikrostrukturen und Eigenschaften.Das Verfahren arbeitet im Vakuum oder in einer kontrollierten Atmosphäre, um Oxidation zu verhindern und die Reinheit des Materials zu gewährleisten.Es umfasst in der Regel vier Hauptstufen: Vakuumerzeugung, Druckanwendung, Widerstandserhitzung und Kühlung.Der "Funkenplasmaeffekt" spielt eine Schlüsselrolle bei der Verhinderung des Partikelwachstums und erleichtert die Bildung einzigartiger Materialzusammensetzungen.
Die wichtigsten Punkte werden erklärt:
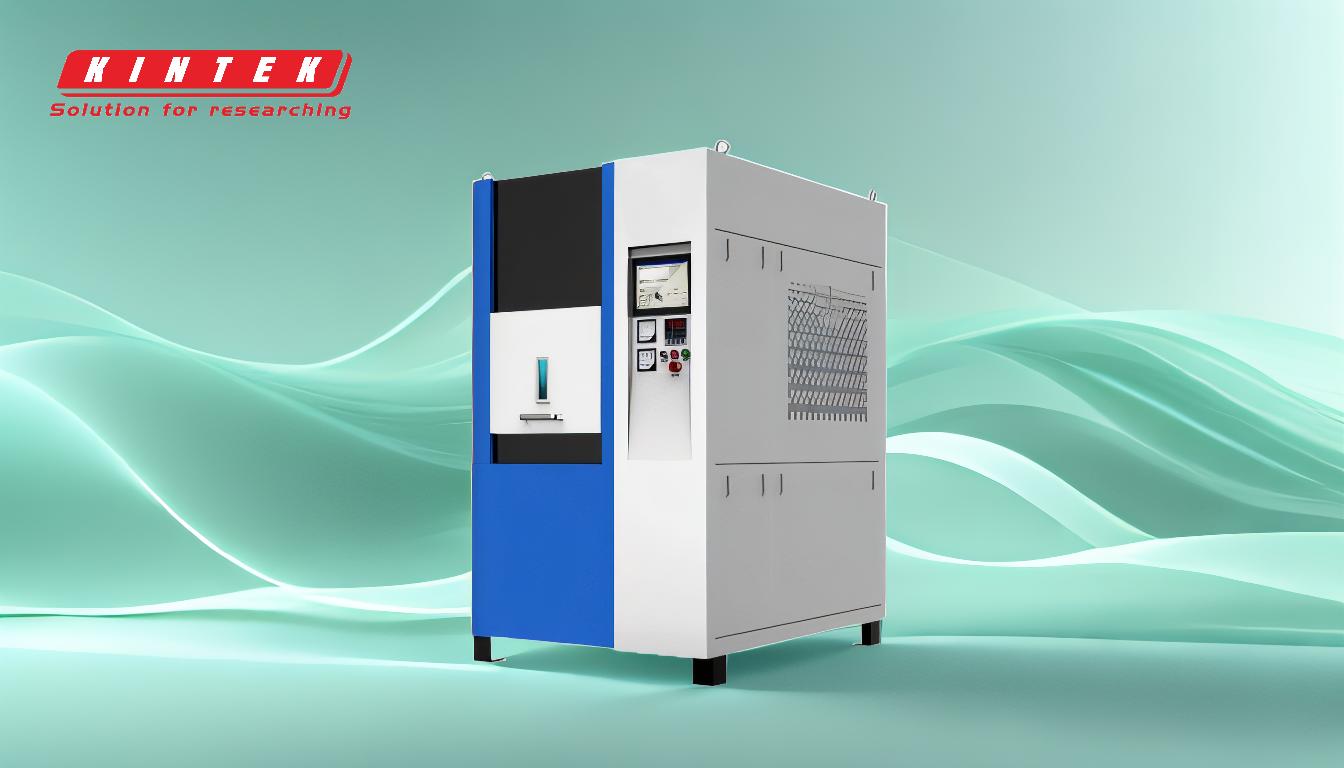
-
Definition und alternative Bezeichnungen:
- SPS steht für Spark Plasma Sintering, eine fortschrittliche Technik der Pulvermetallurgie.
- Es ist auch unter den Bezeichnungen Pulsed Electric Current Sintering (PECS), Field Assisted Sintering Technique (FAST) oder Plasma-Activated Sintering (PAS) bekannt.
-
Kern-Mechanismus:
- Das Verfahren basiert auf einem modifizierten Heißpressverfahren.
- Ein elektrischer Strom fließt direkt durch die Pressform (in der Regel Graphit) und das Bauteil, was eine schnelle Erwärmung und kurze Bearbeitungszeiten ermöglicht.
-
Wesentliche Merkmale:
- Hohe Heizraten:Erzielt sehr schnelle Aufheizzeiten durch gepulste Ströme.
- Kurze Bearbeitungszeiten:Der gesamte Sinterzyklus ist schnell abgeschlossen.
- Niedrige Sintertemperaturen:Ermöglicht die Sinterung bei niedrigeren Temperaturen als bei herkömmlichen Verfahren.
- Präzise Kontrolle:Temperatur, Druck und Erhitzungsgeschwindigkeit können präzise gesteuert werden.
-
Etappen des SPS-Prozesses:
- Vakuum-Erzeugung:Der Prozess beginnt mit der Entfernung von Gas und der Erzeugung eines Vakuums, um Oxidation zu verhindern.
- Druck Anwendung:Druck wird auf das Pulvermaterial ausgeübt, um die Verdichtung zu erleichtern.
- Widerstandsheizung:Ein elektrischer Strom wird durch das Material geleitet, wodurch örtlich hohe Temperaturen und Funkenentladungen entstehen.
- Kühlung:Das Material wird nach dem Sintern abgekühlt, um sein Gefüge zu stabilisieren.
-
Funkenplasma-Effekt:
- Die während des Prozesses erzeugte Funkenentladung verursacht lokal hohe Temperaturen, die zu Verdampfung und Schmelzen auf der Oberfläche der Pulverteilchen führen.
- Dieser Effekt bildet eine Einschnürung um die Kontaktfläche zwischen den Partikeln, wodurch das Partikelwachstum gehemmt wird und die Herstellung von Materialien mit einzigartigen Zusammensetzungen und Eigenschaften ermöglicht wird.
-
Betriebsumgebung:
- Das Verfahren arbeitet im Vakuum oder in einer kontrollierten Atmosphäre, um die Reinheit des Materials zu gewährleisten und Oxidation zu verhindern.
-
Kontrolle und Programmierung:
- Der SPS-Prozess wird über einen Touchscreen gesteuert und programmiert, was eine präzise Kontrolle des Sinterzyklus ermöglicht.
-
Anwendungen und Vorteile:
- Ermöglicht die Herstellung von Materialien mit einzigartigen Mikrostrukturen und Eigenschaften.
- Geeignet für die Synthese sowohl herkömmlicher als auch neuer Materialien in einem einzigen Schritt.
- Reduziert die Verarbeitungszeit und den Energieverbrauch im Vergleich zu herkömmlichen Sinterverfahren.
Wenn man diese Schlüsselpunkte versteht, kann man die Effizienz und Vielseitigkeit des SPS-Verfahrens bei der Materialsynthese und sein Potenzial für die Herstellung fortschrittlicher Materialien mit maßgeschneiderten Eigenschaften schätzen.
Zusammenfassende Tabelle:
Hauptaspekt | Einzelheiten |
---|---|
Alternative Bezeichnungen | Gepulstes elektrisches Stromsintern (PECS), Feldunterstütztes Sinterverfahren (FAST), Plasma-aktiviertes Sintern (PAS) |
Kern-Mechanismus | Modifizierter Heißpressenaufbau mit elektrischem Strom, der durch Graphitmatrize und Bauteil fließt |
Wesentliche Merkmale | Hohe Heizraten, kurze Prozesszeiten, niedrige Sintertemperaturen, präzise Steuerung |
Etappen |
1.Erzeugung von Vakuum
2.Druckanwendung 3.Widerstandsheizung 4.Kühlung |
Funkenplasma-Effekt | Verhindert das Partikelwachstum und ermöglicht einzigartige Materialzusammensetzungen und -eigenschaften |
Betriebsumgebung | Vakuum oder kontrollierte Atmosphäre zur Vermeidung von Oxidation |
Anwendungen | Herstellung von Materialien mit einzigartigen Mikrostrukturen und Eigenschaften |
Möchten Sie erfahren, wie Spark Plasma Sintering Ihre Materialsynthese revolutionieren kann? Kontaktieren Sie uns noch heute für fachkundige Beratung!