Bei der Induktionserwärmung wird Wechselstrom (AC) verwendet, um durch elektromagnetische Induktion Wärme in leitfähigen Materialien zu erzeugen.Die Frequenz des Wechselstroms spielt eine entscheidende Rolle bei der Bestimmung der Erwärmungstiefe, der Effizienz und der Eignung für bestimmte Anwendungen.Die Frequenzen der Induktionserwärmung werden grob in drei Bereiche eingeteilt: Niederfrequenz (50 Hz bis 1 kHz), Zwischenfrequenz (500 Hz bis 10 kHz) und Hochfrequenz (100 kHz bis 500 kHz).Die Wahl der Frequenz hängt von Faktoren wie den Materialeigenschaften, der Dicke, der gewünschten Erwärmungstiefe und den Anwendungsanforderungen ab.So eignen sich beispielsweise niedrigere Frequenzen für die Erwärmung dickerer Materialien, während höhere Frequenzen ideal für dünnere Materialien oder die Oberflächenerwärmung sind.Das Verständnis dieser Frequenzbereiche und ihrer Anwendungen ist für die Entwicklung effizienter Induktionserwärmungssysteme unerlässlich.
Die wichtigsten Punkte werden erklärt:
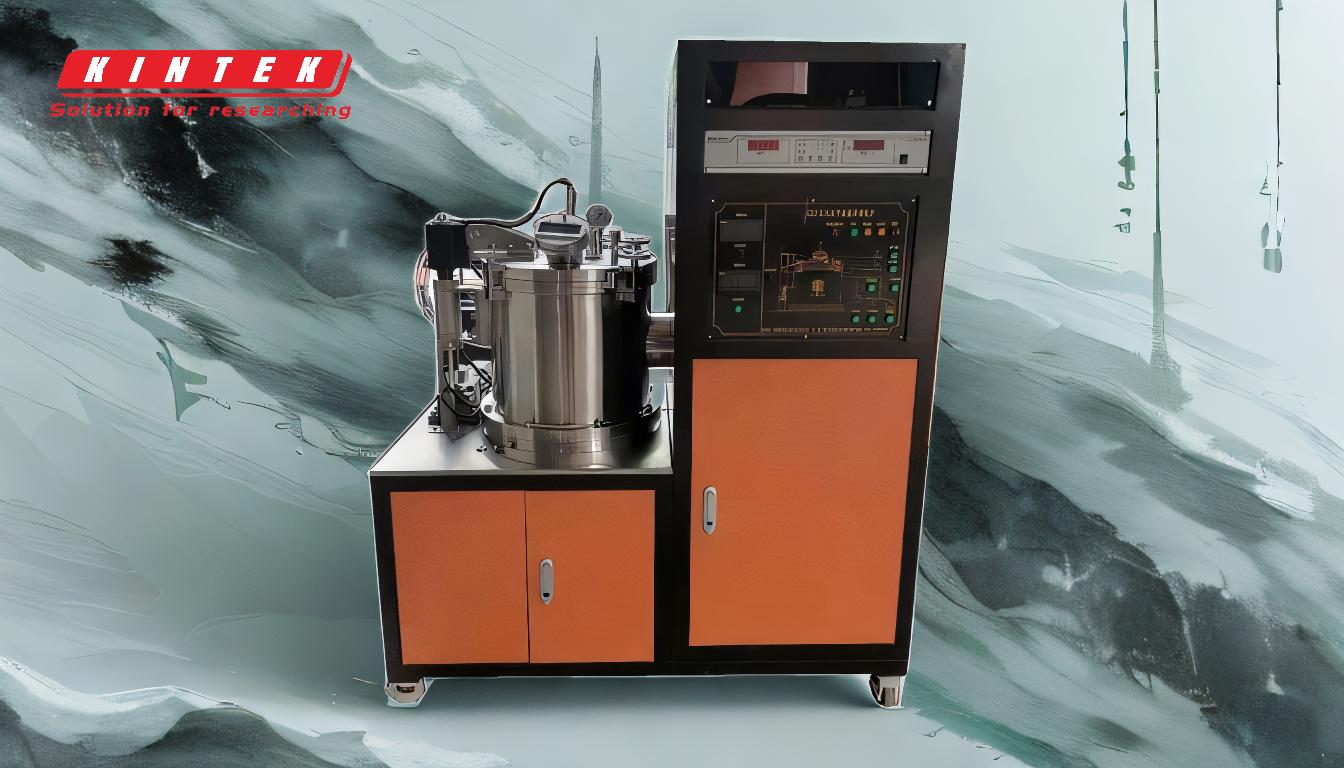
-
Frequenzbereiche bei der Induktionserwärmung:
-
Niederfrequenz (50 Hz bis 1 kHz):
- Wird in der Regel zum Erhitzen großer oder dicker Materialien verwendet.
- Ermöglicht eine tiefere Wärmedurchdringung und eignet sich daher für Anwendungen wie Schmieden oder Schmelzen großer Metallteile.
-
Mittlere Frequenz (500 Hz bis 10 kHz):
- Wird häufig für mittelgroße Teile und Anwendungen verwendet, die eine moderate Erwärmungstiefe erfordern.
- Ideal für Prozesse wie Härten, Glühen und Löten.
-
Hochfrequenz (100 kHz bis 500 kHz):
- Am besten geeignet für dünne Materialien oder Anwendungen zur Oberflächenerwärmung.
- Wird bei Verfahren wie Oberflächenhärtung, Schweißen und Erwärmung kleiner Komponenten verwendet.
-
Niederfrequenz (50 Hz bis 1 kHz):
-
Faktoren, die die Auswahl der Frequenz beeinflussen:
-
Materialeigenschaften:
- Leitfähige und magnetische Materialien erwärmen sich bei der Induktionserwärmung effizienter.
- Materialien mit höherem Widerstand erwärmen sich schneller, während Materialien mit geringerem Widerstand höhere Frequenzen benötigen.
-
Materialdicke:
- Dickere Materialien erfordern niedrigere Frequenzen für ein tieferes Eindringen der Wärme.
- Dünnere Materialien oder Flächenheizungsanwendungen profitieren von höheren Frequenzen.
-
Erwärmungstiefe:
- Höhere Frequenzen führen zu einer geringeren Erwärmungstiefe, während niedrigere Frequenzen tiefer in das Material eindringen.
-
Anforderungen an die Anwendung:
- Der gewünschte Temperaturanstieg, die Heizgeschwindigkeit und die Rührwirkung (bei Schmelzanwendungen) beeinflussen die Wahl der Frequenz.
-
Materialeigenschaften:
-
Frequenz und Heizeffizienz:
- Die Frequenz des Wechselstroms steuert die Geschwindigkeit, mit der sich das Magnetfeld ändert, und wirkt sich direkt auf den induzierten Strom im Werkstück aus.
- Höhere Frequenzen erzeugen mehr Wärme in kürzerer Zeit, aber mit geringerer Eindringtiefe, was sie für die Oberflächenerwärmung energieeffizienter macht.
- Niedrigere Frequenzen sind effizienter für die Massenerwärmung dickerer Materialien, da sie eine gleichmäßige Wärmeverteilung gewährleisten.
-
Praktische Anwendungen von Frequenzbereichen:
- Niederfrequenz:Einsatz in großtechnischen Anwendungen wie Metallschmelzen, Schmieden und Erwärmung von Schwerlastkomponenten.
- Mittlere Frequenz:Angewandt in Prozessen, die eine präzise Temperaturkontrolle erfordern, wie Härten, Glühen und Löten von mittelgroßen Teilen.
- Hochfrequenz:Für Oberflächenbehandlungen, Schweißen und die Erwärmung kleiner oder dünner Komponenten, die eine schnelle Erwärmung erfordern.
-
Konstruktionsüberlegungen für Induktionserwärmungssysteme:
- Das Design der Induktionsspule und die Stromversorgungskapazität müssen auf die gewählte Frequenz abgestimmt sein, um eine effiziente Wärmeerzeugung zu gewährleisten.
- Die spezifische Wärme, die Masse und der erforderliche Temperaturanstieg des Materials beeinflussen den Stromversorgungsbedarf.
- Wärmeverluste aufgrund von Leitung, Konvektion und Strahlung müssen bei der Systemauslegung berücksichtigt werden.
Durch sorgfältige Auswahl des geeigneten Frequenzbereichs auf der Grundlage von Materialeigenschaften, Dicke und Anwendungsanforderungen können Induktionserwärmungssysteme eine optimale Effizienz und Leistung erzielen.Das Verständnis dieser Prinzipien ist für die Käufer von Geräten und Verbrauchsmaterialien entscheidend, um bei der Auswahl von Induktionserwärmungslösungen fundierte Entscheidungen treffen zu können.
Zusammenfassende Tabelle:
Frequenzbereich | Anwendungen | Erwärmungstiefe | Material Eignung |
---|---|---|---|
Niedrig (50 Hz - 1 kHz) | Schmieden, Schmelzen großer Metalle | Tief | dicke Materialien |
Mittlerer Bereich (500 Hz - 10 kHz) | Härten, Glühen, Löten | Mäßig | Mittelgroße Teile |
Hoch (100 kHz - 500 kHz) | Oberflächenhärtung, Schweißen, kleine Bauteile | Untiefe | Dünne Materialien |
Benötigen Sie Hilfe bei der Auswahl der richtigen Induktionserwärmungsfrequenz für Ihre Anwendung? Kontaktieren Sie noch heute unsere Experten für personalisierte Lösungen!