Das Sintern ist ein wichtiger Prozess in der Fertigung, bei dem gepresste Metall- oder Keramikpulver erhitzt werden, um komplexe Strukturteile zu formen. Um die Qualität und Konsistenz der gesinterten Produkte zu gewährleisten, werden Schutzgase verwendet, um eine inerte Atmosphäre zu schaffen, die Oxidation und Entkohlung verhindert. Die am häufigsten verwendeten Gase beim Sintern sind Wasserstoff, Stickstoff und Kohlenmonoxid. Diese Gase tragen dazu bei, den atmosphärischen Druck aufrechtzuerhalten, die Sinterumgebung zu kontrollieren und eine gleichmäßige Leistung zu gewährleisten. Stickstoff ist besonders wirksam bei der Verhinderung von Oxidation in Hochtemperaturzonen, während Wasserstoff und Kohlenmonoxid wegen ihrer reduzierenden Eigenschaften verwendet werden. Die Wahl des Gases hängt von dem zu sinternden Material und den gewünschten Ergebnissen ab.
Die wichtigsten Punkte werden erklärt:
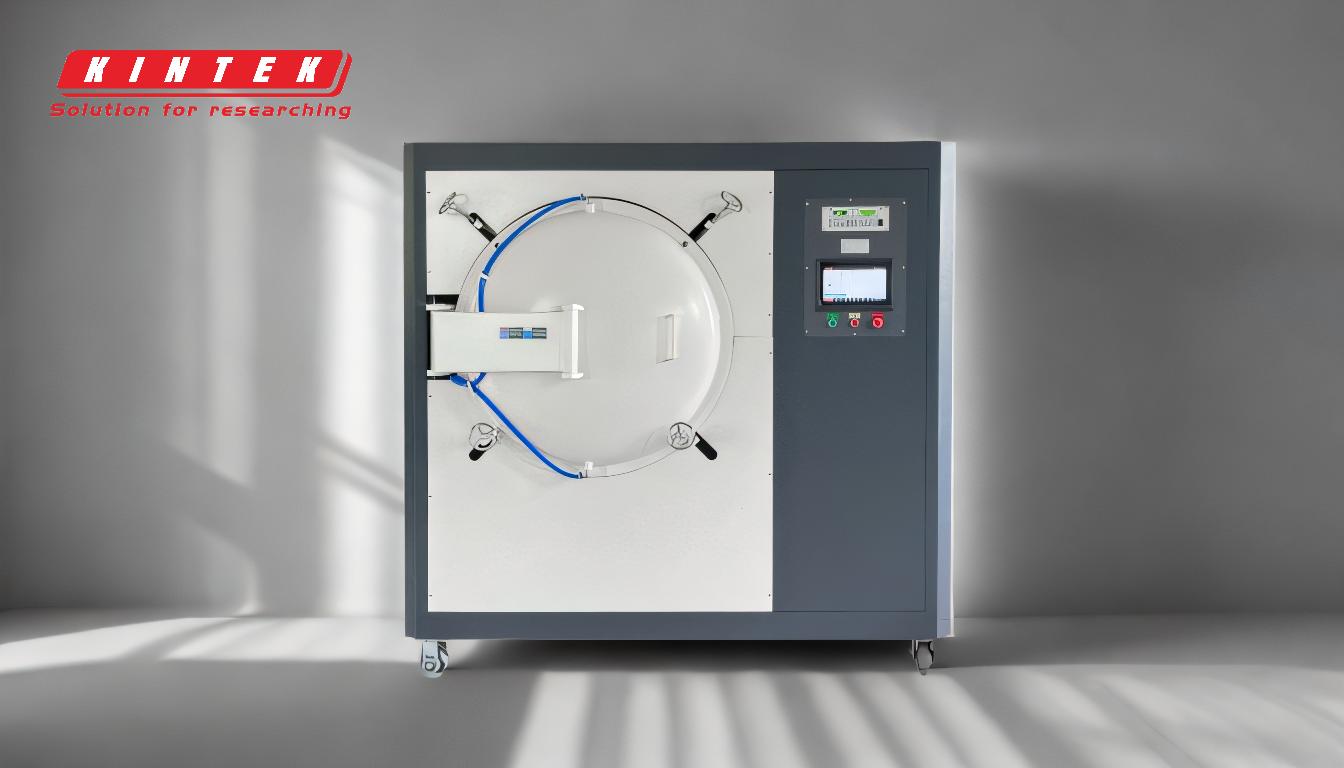
-
Zweck von Schutzgasen bei der Sinterung:
- Verhinderung von Oxidation: Schutzgase schaffen eine inerte Atmosphäre, die verhindert, dass heiße Metalle mit Sauerstoff reagieren, was zur Oxidation und Zersetzung des Materials führen kann.
- Verhinderung der Entkohlung: Bei kohlenstoffhaltigen Materialien helfen Schutzgase, den Verlust von Kohlenstoff zu verhindern, der das Material schwächen kann.
- Aufrechterhaltung des Atmosphärendrucks: Diese Gase tragen dazu bei, den erforderlichen Druck im Sinterofen aufrechtzuerhalten und gleichmäßige Sinterbedingungen zu gewährleisten.
-
Häufig verwendete Gase bei der Sinterung:
-
Wasserstoff (H₂):
- Eigenschaften: Wasserstoff ist ein stark reduzierendes Gas, d. h. er kann Metalloxiden Sauerstoff entziehen und so die Oxidation verhindern.
- Anwendungen: Es wird häufig bei Sinterprozessen eingesetzt, bei denen reduzierende Bedingungen erforderlich sind, wie z. B. beim Sintern von Edelstahl oder anderen Legierungen.
- Vorteile: Wasserstoffbasierte Atmosphären können zu einer gleichmäßigeren Leistung und besseren Oberflächenqualität führen.
- Benachteiligungen: Wasserstoff ist leicht entzündlich und erfordert eine sorgfältige Handhabung und Sicherheitsmaßnahmen.
-
Stickstoff (N₂):
- Eigenschaften: Stickstoff ist ein inertes Gas, d. h. es reagiert nicht mit den meisten Materialien und ist daher ideal für die Schaffung einer inerten Atmosphäre.
- Anwendungen: Er wird üblicherweise in den Hochtemperaturzonen von Sinteröfen eingesetzt, um Oxidation zu verhindern. Stickstoff wird durch winklig eingestellte Öffnungen oder als quer verlaufender laminarer Strahl eingeblasen.
- Vorteile: Stickstoff ist kostengünstig, leicht verfügbar und sicher in der Anwendung.
- Benachteiligungen: Stickstoff ist zwar ein wirksamer Oxidationsschutz, hat aber keine reduzierenden Eigenschaften, so dass er nicht für alle Materialien geeignet ist.
-
Kohlenmonoxid (CO):
- Eigenschaften: Kohlenmonoxid ist ein reduzierendes Gas, das auch als Aufkohlungsmittel wirken kann, indem es dem gesinterten Material Kohlenstoff hinzufügt.
- Anwendungen: Es wird in Sinterprozessen eingesetzt, bei denen sowohl reduzierende als auch aufkohlende Effekte erwünscht sind, wie z. B. beim Sintern von Eisenwerkstoffen.
- Vorteile: Kohlenmonoxid kann die mechanischen Eigenschaften des gesinterten Materials verbessern, indem es seinen Kohlenstoffgehalt erhöht.
- Benachteiligungen: Kohlenmonoxid ist giftig und erfordert eine sorgfältige Handhabung und Belüftung.
-
-
Auswahl von Gasen auf der Grundlage von Material- und Prozessanforderungen:
- Materielle Erwägungen: Die Wahl des Gases hängt von dem zu sinternden Material ab. Wasserstoff wird beispielsweise häufig für rostfreien Stahl verwendet, während Stickstoff für nicht reaktive Materialien bevorzugt wird.
- Prozessanforderungen: Das gewünschte Ergebnis des Sinterprozesses beeinflusst auch die Wahl des Gases. Wenn beispielsweise eine Aufkohlung erforderlich ist, kann Kohlenmonoxid die beste Option sein.
- Sicherheit und Kosten: Sicherheitserwägungen und Kosten sind ebenfalls wichtige Faktoren. Stickstoff ist im Allgemeinen sicherer und kostengünstiger als Wasserstoff oder Kohlenmonoxid.
-
Injektionsmethoden für Schutzgase:
- Winkelmäßig angepasste Ports: Der Stickstoff wird häufig durch winklig eingestellte Öffnungen in den Ofen eingeblasen, um eine gleichmäßige Verteilung und eine effektive Abdeckung des Sintermaterials zu gewährleisten.
- Quer verlaufende laminare Strahlströme: Bei dieser Methode wird das Gas in einem laminaren Strömungsmuster eingeleitet, wodurch eine gleichmäßige inerte Atmosphäre geschaffen und eine lokale Oxidation verhindert wird.
-
Einfluss der Gasauswahl auf die Sinterleistung:
- Konsistenz: Die Verwendung geeigneter Schutzgase kann zu gleichmäßigeren Sinterergebnissen mit weniger Fehlern und besseren mechanischen Eigenschaften führen.
- Oberflächenqualität: Insbesondere wasserstoffbasierte Atmosphären können die Oberflächenqualität von Sinterteilen durch die Reduzierung von Oberflächenoxiden verbessern.
- Mechanische Eigenschaften: Die Wahl des Gases kann sich auch auf die mechanischen Eigenschaften des Sintermaterials, wie Härte, Festigkeit und Zähigkeit, auswirken.
Zusammenfassend lässt sich sagen, dass die Auswahl der Gase beim Sintern ein entscheidender Faktor ist, der die Qualität, Konsistenz und Leistung des Endprodukts beeinflusst. Wasserstoff, Stickstoff und Kohlenmonoxid sind die am häufigsten verwendeten Gase, die jeweils einzigartige Vorteile und Herausforderungen bieten. Die Wahl des Gases sollte sich nach dem zu sinternden Material, den gewünschten Ergebnissen und Sicherheitsaspekten richten. Geeignete Injektionsmethoden und Gasmanagement sind ebenfalls entscheidend für eine effektive Sinterung und qualitativ hochwertige Ergebnisse.
Zusammenfassende Tabelle:
Gas | Eigenschaften | Anwendungen | Vorteile | Benachteiligungen |
---|---|---|---|---|
Wasserstoff (H₂) | Hochgradig reduzierendes Gas, verhindert die Oxidation durch Entfernung von Sauerstoff aus Metalloxiden | Sintern von rostfreiem Stahl und Legierungen | Gleichbleibende Leistung, bessere Oberflächenqualität | Leicht entflammbar, erfordert sorgfältige Handhabung |
Stickstoff (N₂) | Inertes Gas, reagiert nicht mit den meisten Materialien | Hochwärmezonen zur Vermeidung von Oxidation | Kostengünstig, leicht verfügbar, sicher in der Anwendung | Keine reduzierenden Eigenschaften, möglicherweise nicht für alle Materialien geeignet |
Kohlenmonoxid (CO) | Reduktionsgas, wirkt als Aufkohlungsmittel | Sintern von Eisenwerkstoffen, bei denen eine Aufkohlung erforderlich ist | Verbessert die mechanischen Eigenschaften durch Erhöhung des Kohlenstoffgehalts | Giftig, erfordert sorgfältige Handhabung und Belüftung |
Benötigen Sie Hilfe bei der Auswahl des richtigen Gases für Ihren Sinterprozess? Kontaktieren Sie unsere Experten noch heute !