In Wärmebehandlungsöfen werden häufig Inertgase verwendet, um die Materialien vor Oxidation und anderen chemischen Reaktionen während des Erhitzungsprozesses zu schützen.Die am häufigsten verwendeten Inertgase sind Stickstoff und Argon, wobei Stickstoff aufgrund seiner Kosteneffizienz und seiner Nichtreaktivität mit Stahl am weitesten verbreitet ist.Argon ist ebenfalls weit verbreitet, vor allem bei Verfahren, die eine höhere Reinheit erfordern, oder bei der Behandlung von Nichteisenmetallen.Diese Gase tragen dazu bei, die Unversehrtheit und die Eigenschaften der behandelten Materialien zu erhalten, was hochwertige Ergebnisse gewährleistet.Wärmebehandlungsöfen, die mit Schutzgasatmosphären ausgestattet sind, verfügen in der Regel über fortschrittliche Temperaturregelungen und energieeffiziente Isolierung, um die Leistung zu optimieren und Kosten zu sparen.
Die wichtigsten Punkte erklärt:
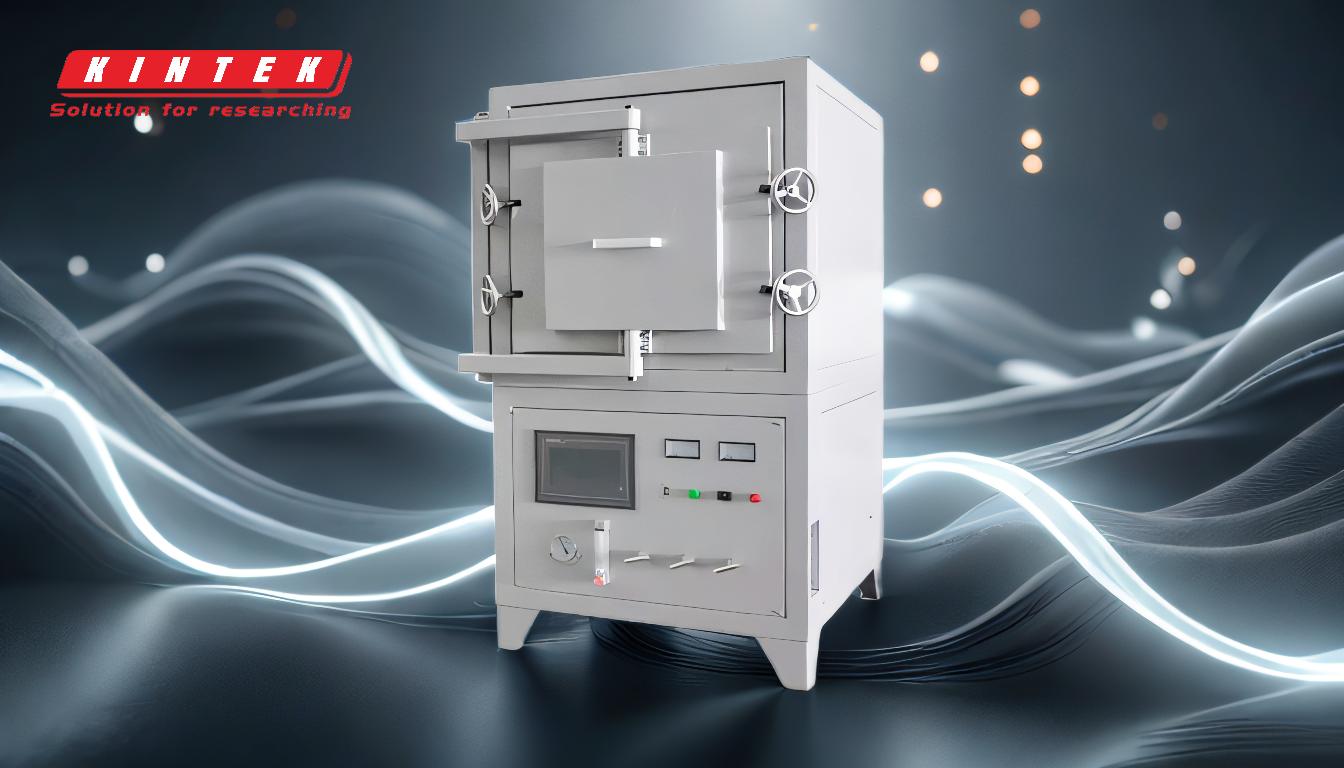
-
Zweck von Inertgasen in der Wärmebehandlung:
- Inertgase werden verwendet, um eine Schutzatmosphäre zu schaffen, die Oxidation und andere chemische Reaktionen während der Wärmebehandlung verhindert.Dies ist entscheidend, um die Integrität des Materials zu erhalten und qualitativ hochwertige Ergebnisse zu gewährleisten.
- Oxidation kann die Qualität von Teilen beeinträchtigen und zu Problemen wie Entkohlung führen, die das Material schwächt.Inertgase mindern diese Risiken.
-
Häufig verwendete Inertgase:
- Stickstoff (N2):Das am häufigsten verwendete Inertgas, da es kostengünstig ist und nicht mit Stahl reagiert.Es ist in verschiedenen Wärmebehandlungsanwendungen weit verbreitet.
- Argon (Ar):Wird häufig bei Prozessen verwendet, die eine höhere Reinheit erfordern, oder bei der Verarbeitung von Nichteisenmetallen wie Kupfer, Messing und Aluminium.Argon wird auch bei speziellen Verfahren wie dem heißisostatischen Pressen (HIP) bevorzugt, um sicherzustellen, dass keine chemischen Reaktionen auftreten.
- Helium (He):Wird manchmal in Kombination mit Argon oder Stickstoff verwendet, insbesondere bei Anwendungen, die eine schnelle Abkühlung oder besondere thermische Eigenschaften erfordern.
-
Anwendungen von Inertgasatmosphären:
- Kleben und Aushärten:Durch den Einsatz von Inertgasen wird eine kontrollierte Umgebung für Klebe- und Aushärtungsprozesse geschaffen, die gleichbleibende Ergebnisse gewährleistet.
- Wärmebehandlung:Unverzichtbar für Prozesse wie Glühen, Härten und Anlassen, bei denen die Erhaltung der Materialeigenschaften entscheidend ist.
- Spezialisierte Prozesse:Wie z. B. HIP, wo Argon verwendet wird, um chemische Reaktionen zu verhindern und die Materialintegrität zu erhalten.
-
Vorteile von Öfen mit Schutzgasatmosphäre:
- Präzisionskontrolle:Moderne Öfen mit Schutzgasatmosphäre verfügen häufig über eine präzise mikroprozessorgesteuerte Temperaturregelung, die eine genaue und gleichmäßige Wärmebehandlung ermöglicht.
- Energie-Effizienz:Diese Öfen sind mit einer energieeffizienten Isolierung ausgestattet, die die Betriebskosten bei gleichbleibend hoher Leistung senkt.
- Qualität und Leistung:Die Verwendung von Inertgasen gewährleistet, dass die Materialeigenschaften erhalten bleiben, was zu qualitativ hochwertigeren Endprodukten führt.
-
Kombination von Gasen:
- Bei einigen Anwendungen wird eine Kombination von Inertgasen verwendet, um bestimmte Ergebnisse zu erzielen.Übliche Kombinationen sind Ar/He, Ar/He/N2 und N2/He.Diese Mischungen werden auf die spezifischen Anforderungen des Werkstoffs und des Wärmebehandlungsverfahrens zugeschnitten.
-
Überlegungen zur Auswahl eines Schutzgases:
- Material Typ:Die Wahl des Inertgases kann von der Art des zu behandelnden Materials abhängen.Bei Nichteisenmetallen wird zum Beispiel häufig Argon bevorzugt.
- Anforderungen an den Prozess:Bestimmte Wärmebehandlungsverfahren können bestimmte Gase oder Gasgemische erfordern, um die gewünschten Ergebnisse zu erzielen.
- Kosten und Verfügbarkeit:Stickstoff ist im Allgemeinen kostengünstiger und weithin verfügbar, was ihn zu einer beliebten Wahl für viele Anwendungen macht.
Zusammenfassend lässt sich sagen, dass die Verwendung von Inertgasen wie Stickstoff und Argon in Wärmebehandlungsöfen für den Schutz der Materialien vor Oxidation und zur Gewährleistung hochwertiger Ergebnisse unerlässlich ist.Die Wahl des Gases hängt vom Material, den Prozessanforderungen und Kostenerwägungen ab, wobei moderne Ofenkonstruktionen eine präzise Steuerung und Energieeffizienz ermöglichen.
Zusammenfassende Tabelle:
Inertes Gas | Wesentliche Merkmale | Allgemeine Anwendungen |
---|---|---|
Stickstoff (N2) | Kostengünstig, nicht reaktiv mit Stahl | Allgemeine Wärmebehandlung, Stahlverarbeitung |
Argon (Ar) | Hohe Reinheit, ideal für Nichteisenmetalle | HIP-Verfahren, Behandlung von Nichteisenmetallen |
Helium (He) | Schnelle Abkühlung, spezifische thermische Eigenschaften | Spezialisierte Anwendungen, kombiniert mit Ar/N2 |
Benötigen Sie Hilfe bei der Auswahl des richtigen Inertgases für Ihren Wärmebehandlungsprozess? Kontaktieren Sie noch heute unsere Experten für eine persönliche Beratung!