Dünnfilmbeschichtungen sind spezielle Schichten, die auf Oberflächen aufgebracht werden, um deren Eigenschaften zu verbessern oder neue Funktionalitäten hinzuzufügen.Diese Beschichtungen sind in der Regel dünn, zwischen Nanometern und Mikrometern, und werden in verschiedenen Branchen zu Zwecken wie Schutz, Dekoration und Leistungsverbesserung eingesetzt.Sie können die Oberflächenhärte, Korrosionsbeständigkeit, elektrische Leitfähigkeit, optische Eigenschaften und vieles mehr verbessern.Dünnfilmbeschichtungen sind vielseitig und können auf spezifische Anforderungen zugeschnitten werden, was sie zu einem unverzichtbaren Bestandteil von Anwendungen macht, die von Industriewerkzeugen bis hin zu moderner Elektronik und dekorativen Oberflächen reichen.
Die wichtigsten Punkte erklärt:
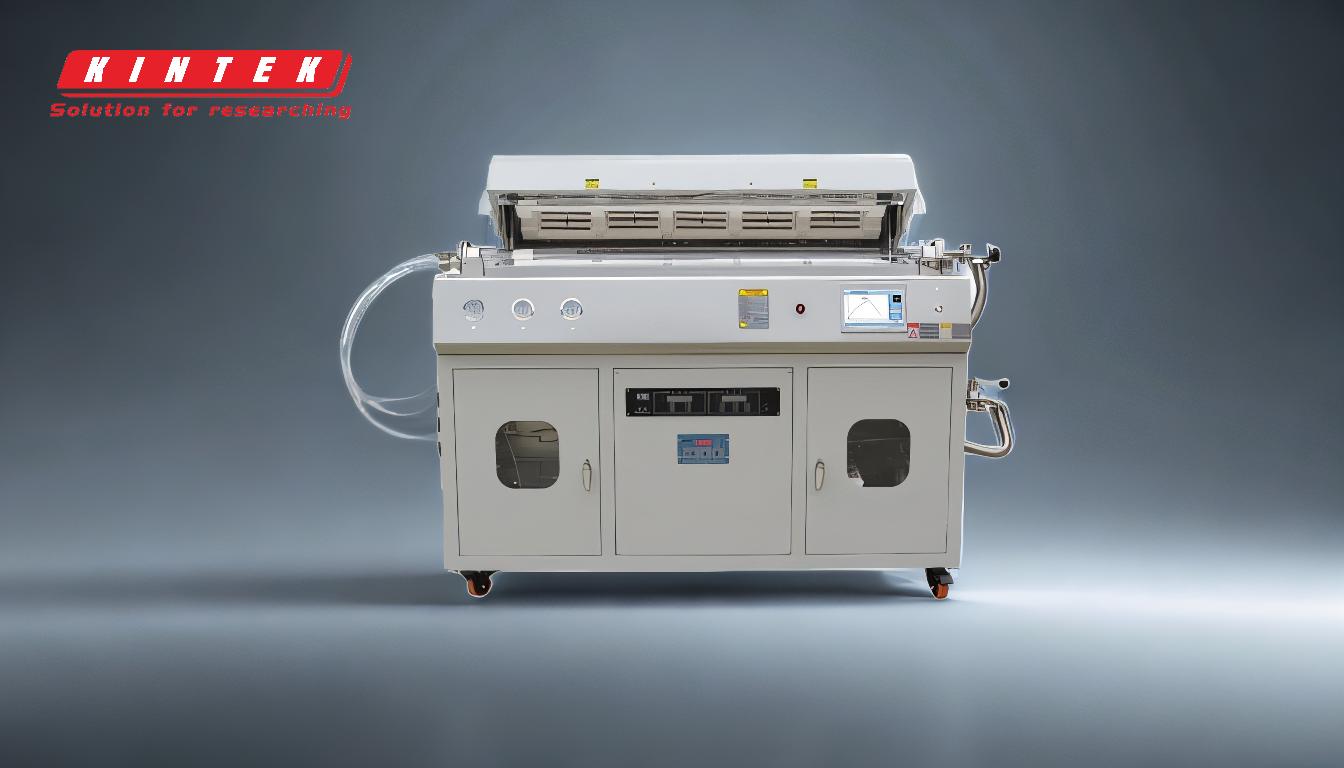
-
Definition und Zweck von Dünnfilmbeschichtungen:
- Dünnfilmbeschichtungen sind ultradünne Schichten, die auf Oberflächen aufgebracht werden, um deren Eigenschaften zu verändern oder neue Funktionalitäten hinzuzufügen.
- Sie dienen verschiedenen Zwecken, u. a. dem Schutz (z. B. vor Abnutzung, Kratzern, Korrosion), der Dekoration (z. B. Veränderung der Farbe oder des Glanzes) und der Leistungsverbesserung (z. B. Verbesserung der Leitfähigkeit oder Härte).
-
Merkmale von Dünnfilmbeschichtungen:
- Transparenz:Einige Beschichtungen sind so konzipiert, dass sie transparent sind und sich für optische Anwendungen wie Linsen oder Displays eignen.
- Dauerhaftigkeit:Beschichtungen können die Haltbarkeit von Oberflächen verbessern und sie widerstandsfähig gegen Abnutzung, Kratzer und Umwelteinflüsse machen.
- Elektrische und optische Eigenschaften:Dünne Schichten können die elektrische Leitfähigkeit erhöhen oder verringern oder die Übertragung von Signalen und Licht verändern, was sie in der Elektronik und Photonik nützlich macht.
- Korrosionsbeständigkeit:Viele Beschichtungen werden aufgebracht, um Oberflächen vor Korrosion zu schützen und die Lebensdauer von Materialien zu verlängern.
-
Arten von Dünnfilmbeschichtungen:
-
Funktionelle Beschichtungen:Sie dienen der Verbesserung bestimmter Eigenschaften wie Härte, Verschleißfestigkeit oder Wärmebeständigkeit.Beispiele hierfür sind:
- Ti-Al-N:Erhöht die Härte und verringert die Reibung, wird häufig für Schneidwerkzeuge verwendet.
- Al-Cr-N:Erhöht die Standzeit und die thermische Beständigkeit, ideal für Hochtemperaturanwendungen.
- Cr-N und Ti-C-N:Verbessert die Korrosionsbeständigkeit und die Schnittleistung.
- Dekorative Beschichtungen:Diese werden zu ästhetischen Zwecken aufgebracht, wie z. B. metallische Beschichtungen auf Kunststoffsubstraten, um ein glänzendes oder strukturiertes Aussehen zu erzeugen.
-
Funktionelle Beschichtungen:Sie dienen der Verbesserung bestimmter Eigenschaften wie Härte, Verschleißfestigkeit oder Wärmebeständigkeit.Beispiele hierfür sind:
-
Anwendungen von Dünnfilmbeschichtungen:
- Industrielle Werkzeuge:Beschichtungen wie Ti-Al-N und Al-Cr-N werden verwendet, um die Leistung und Lebensdauer von Schneidwerkzeugen und Maschinen zu verbessern.
- Elektronik:Dünne Schichten werden in Geräten zur Umwandlung von Lichtenergie in elektrische Energie (z. B. Solarzellen) und in fortschrittlichen Speichertechnologien verwendet.
- Optik:Transparente Beschichtungen werden auf Linsen, Spiegel und Displays aufgebracht, um die optische Leistung und Haltbarkeit zu verbessern.
- Dekorative Beschichtungen:Dünne Schichten werden verwendet, um reflektierende Oberflächen zu schaffen, Oberflächenstrukturen zu verändern und Produkten Farbe zu verleihen.
-
Vorteile von Dünnfilmbeschichtungen:
- Verbesserte Leistung:Beschichtungen können die Leistung von Trägermaterialien durch zusätzliche Eigenschaften wie Härte, Leitfähigkeit oder Widerstandsfähigkeit gegen Umwelteinflüsse erheblich verbessern.
- Vielseitigkeit:Dünnfilmbeschichtungen können auf spezifische Anforderungen zugeschnitten werden und eignen sich daher für eine breite Palette von Anwendungen.
- Schutz der Oberfläche:Sie schützen Oberflächen vor Abnutzung, Kratzern, Fingerabdrücken und Korrosion und verlängern so die Lebensdauer der Materialien.
- Ästhetisches Erscheinungsbild:Dekorative Beschichtungen können die visuelle Attraktivität von Produkten verbessern und sie für die Verbraucher attraktiver machen.
-
Beschichtungseigenschaften und Wechselwirkung mit dem Substrat:
- Dünnfilmbeschichtungen sind extrem haftend, d. h. sie gehen eine starke Verbindung mit dem Substrat ein und gewährleisten eine lang anhaltende Leistung.
- Die Wechselwirkung zwischen der Beschichtung und dem Substrat ist von entscheidender Bedeutung, da sie die Wirksamkeit der Beschichtung bei der Erzielung der gewünschten Eigenschaften wie Härte, Leitfähigkeit oder optische Übertragung bestimmt.
-
Beispiele für prominente Beschichtungen:
- Ti-Al-N:Es ist für seine hohe Härte und geringe Reibung bekannt und wird häufig für Schneidwerkzeuge und industrielle Anwendungen verwendet.
- Al-Cr-N:Bietet eine ausgezeichnete thermische Beständigkeit und eine lange Lebensdauer der Werkzeuge und ist daher für Hochtemperaturumgebungen geeignet.
- Cr-N und Ti-C-N:Diese Beschichtungen werden wegen ihrer Korrosionsbeständigkeit und Schneidleistung geschätzt und häufig in rauen Umgebungen eingesetzt.
Zusammenfassend lässt sich sagen, dass Dünnfilmbeschichtungen eine wichtige Technologie sind, die die Funktionalität, Haltbarkeit und das Aussehen von Materialien in verschiedenen Branchen verbessert.Ihre Fähigkeit, für spezifische Anwendungen angepasst zu werden, macht sie in der modernen Fertigung und Technologie unverzichtbar.
Zusammenfassende Tabelle:
Hauptaspekt | Einzelheiten |
---|---|
Zweck | Veränderung von Oberflächeneigenschaften, Hinzufügen von Funktionalität, Schutz, Dekoration, Verbesserung. |
Schichtdicke | Nanometer bis Mikrometer. |
Wichtigste Merkmale | Transparenz, Haltbarkeit, elektrische/optische Eigenschaften, Korrosionsbeständigkeit. |
Arten | Funktionelle (z. B. Ti-Al-N, Al-Cr-N) und dekorative Beschichtungen. |
Anwendungen | Industriewerkzeuge, Elektronik, Optik, dekorative Oberflächen. |
Vorteile | Verbesserte Leistung, Vielseitigkeit, Oberflächenschutz, ästhetische Wirkung. |
Erfahren Sie, wie Dünnfilmbeschichtungen Ihre Produkte verändern können. Kontaktieren Sie unsere Experten noch heute !