Das Sintern ist ein wichtiger Prozess in der additiven Fertigung (AM), bei dem pulverförmige Materialien durch Hitze und Druck zu festen Strukturen verdichtet und verbunden werden, ohne dass das Material vollständig schmilzt.Dieses Verfahren ist für die Herstellung komplexer, hochpräziser Bauteile mit verbesserten mechanischen Eigenschaften wie Härte, Zähigkeit und Haltbarkeit unerlässlich.Beim AM werden Sintertechniken wie das selektive Lasersintern (SLS) und das Elektronenstrahlsintern (EBS) eingesetzt, um pulverförmige Materialien auf der Grundlage digitaler Entwürfe zu schichten und zu verschmelzen, was die Herstellung komplizierter 3D-Objekte ermöglicht.Das Sintern eignet sich besonders für Materialien mit hohem Schmelzpunkt, wie Metalle und Keramiken, und ist in Branchen wie der Luft- und Raumfahrt, der Automobilindustrie und dem Gesundheitswesen weit verbreitet, um funktionale, dichte und kostengünstige Teile herzustellen.
Die wichtigsten Punkte erklärt:
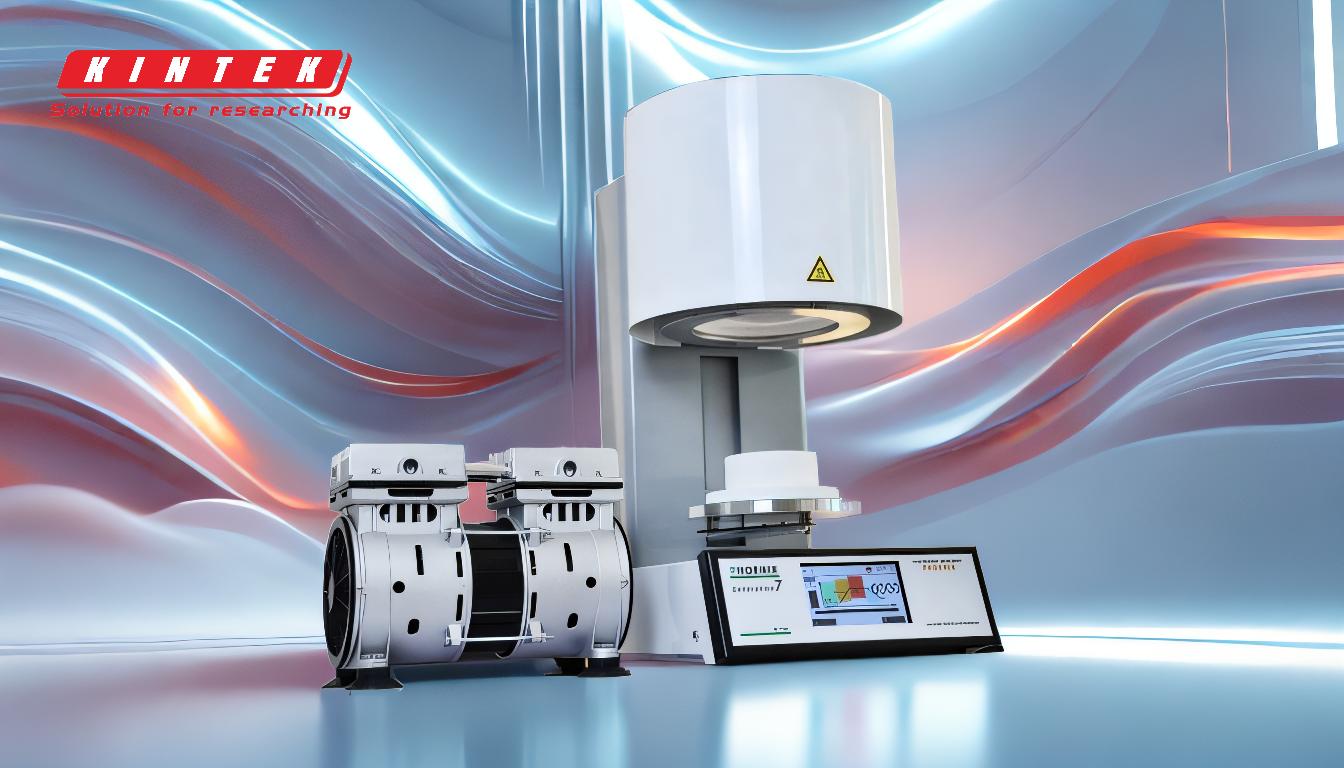
-
Definition und Zweck des Sinterns:
- Das Sintern ist ein Fertigungsverfahren, bei dem pulverförmige Werkstoffe durch Anwendung von Hitze und Druck zu festen Strukturen verdichtet und verbunden werden, ohne dass das Material vollständig geschmolzen wird.
- Es verbessert die mechanischen Eigenschaften von Werkstoffen, wie Härte, Zähigkeit und Haltbarkeit, und ist damit ideal für die Herstellung von Hochleistungskomponenten.
- Das Verfahren wird häufig in der Pulvermetallurgie, der Keramik und der additiven Fertigung eingesetzt, um komplexe Formen und Geometrien zu erzeugen, die mit herkömmlichen Methoden nur schwer zu erreichen sind.
-
Wie das Sintern funktioniert:
- Beim Sintern diffundieren die Atome des pulverförmigen Materials durch Hitze und Druck über die Partikelgrenzen und verschmelzen zu einer festen Masse.
- Die verwendete Temperatur liegt unter dem Schmelzpunkt des Materials, so dass das Material seine Form beibehält und gleichzeitig dichter und fester wird.
- Dieses Verfahren eignet sich besonders für Werkstoffe mit extrem hohen Schmelzpunkten, wie Wolfram und Molybdän, die mit herkömmlichen Methoden nur schwer zu verarbeiten sind.
-
Die Rolle des Sinterns in der additiven Fertigung:
- In der additiven Fertigung wird das Sintern bei Verfahren wie dem selektiven Lasersintern (SLS) und dem Elektronenstrahlsintern (EBS) eingesetzt, um 3D-Objekte Schicht für Schicht zu erzeugen.
- Ein digitaler Entwurf steuert das selektive Sintern von pulverförmigen Materialien und ermöglicht so die Herstellung komplizierter und präziser Komponenten.
- Das Sintern in der additiven Fertigung ermöglicht die Verfestigung von pulverförmigen Werkstoffen zu vollständig dichten und funktionalen Teilen und eignet sich daher für das Rapid Prototyping und die Massenproduktion.
-
Vorteile des Sinterns in der additiven Fertigung:
- Komplexe Geometrien:Das Sintern ermöglicht die Herstellung komplizierter Formen und innerer Strukturen, die mit herkömmlichen Fertigungsmethoden nur schwer oder gar nicht zu erreichen sind.
- Effizienz des Materials:Das Verfahren minimiert den Materialabfall, da unbenutztes Pulver oft für künftige Produktionen wiederverwendet werden kann.
- Kosteneffizienz:Das Sintern reduziert den Bedarf an teuren Werkzeugen und ist damit eine kostengünstige Lösung für die Herstellung komplexer Teile.
- Verbesserte Eigenschaften:Die entstehenden Teile weisen verbesserte mechanische Eigenschaften auf, wie Festigkeit, Verschleißfestigkeit und thermische Stabilität.
-
Anwendungen des Sinterns in der additiven Fertigung:
- Luft- und Raumfahrt:Gesinterte Bauteile werden in der Luft- und Raumfahrt verwendet, da sie ein gutes Verhältnis zwischen Festigkeit und Gewicht aufweisen und extremen Bedingungen standhalten.
- Automobilindustrie:Die Sintertechnik wird zur Herstellung leichter, haltbarer Teile für Motoren, Getriebe und andere kritische Systeme eingesetzt.
- Gesundheitswesen:Das Verfahren wird zur Herstellung von maßgeschneiderten medizinischen Implantaten und Prothesen mit präzisen Geometrien und biokompatiblen Materialien eingesetzt.
- Elektronik:Das Sintern wird zur Herstellung von Komponenten wie Kühlkörpern, Anschlüssen und Sensoren mit hoher thermischer und elektrischer Leitfähigkeit eingesetzt.
-
Herausforderungen und Beschränkungen:
- Materielle Zwänge:Nicht alle Materialien sind für das Sintern geeignet, und das Verfahren kann spezielle Pulver mit besonderen Eigenschaften erfordern.
- Oberflächengüte:Gesinterte Teile können eine raue Oberfläche haben und müssen nachbearbeitet werden, um die gewünschte Qualität zu erreichen.
- Maßgenauigkeit:Das Erreichen einer hohen Maßgenauigkeit kann eine Herausforderung sein, insbesondere bei komplexen Geometrien.
- Stromverbrauch:Das Verfahren kann aufgrund der erforderlichen hohen Temperaturen energieintensiv sein.
-
Zukünftige Trends beim Sintern für die additive Fertigung:
- Fortgeschrittene Materialien:Die Forschung wird fortgesetzt, um neue Werkstoffe und Pulver zu entwickeln, die für das Sintern optimiert sind und dessen Anwendungsmöglichkeiten erweitern.
- Hybride Verfahren:Kombination des Sinterns mit anderen Fertigungstechniken, wie z. B. Bearbeitung oder Beschichtung, zur Verbesserung der Leistung und Funktionalität von Teilen.
- Automatisierung und KI:Integration von Automatisierung und künstlicher Intelligenz, um die Prozesssteuerung zu verbessern, Abfall zu reduzieren und die Produktionseffizienz zu steigern.
- Nachhaltigkeit:Entwicklung energieeffizienterer Sinterverfahren und Verwendung recycelter Materialien zur Verringerung der Umweltauswirkungen.
Zusammenfassend lässt sich sagen, dass das Sintern ein revolutionärer Prozess in der additiven Fertigung ist, der die Herstellung komplexer, leistungsstarker Komponenten mit verbesserten mechanischen Eigenschaften ermöglicht.Seine Anwendungen erstrecken sich über verschiedene Branchen, und die laufenden Fortschritte bei Werkstoffen und Technologie versprechen eine weitere Ausweitung seiner Möglichkeiten und Effizienz.
Zusammenfassende Tabelle:
Aspekt | Einzelheiten |
---|---|
Definition | Verdichtet und verbindet pulverförmige Materialien mit Hilfe von Hitze und Druck. |
Schlüsseltechniken | Selektives Laser-Sintern (SLS), Elektronenstrahl-Sintern (EBS). |
Vorteile | Komplexe Geometrien, Materialeffizienz, Kosteneffizienz, verbesserte Eigenschaften. |
Anwendungen | Luft- und Raumfahrt, Automobilindustrie, Gesundheitswesen, Elektronik. |
Herausforderungen | Materialbeschränkungen, Oberflächengüte, Maßhaltigkeit, Energieverbrauch. |
Zukünftige Trends | Moderne Werkstoffe, Hybridverfahren, Automatisierung, Nachhaltigkeit. |
Entdecken Sie, wie das Sintern Ihren Fertigungsprozess revolutionieren kann. Kontaktieren Sie uns noch heute !