SPS (Spark Plasma Sintering) ist ein fortschrittliches Sinterverfahren in der Materialwissenschaft, das die schnelle Verfestigung von Pulvern zu dichten Hochleistungswerkstoffen ermöglicht.Es kombiniert die Anwendung von gepulstem elektrischem Strom und einachsigem Druck, was schnelle Heizraten, eine präzise Steuerung der Sinterparameter und die Möglichkeit der Verarbeitung von Materialien bei niedrigeren Temperaturen im Vergleich zu herkömmlichen Verfahren ermöglicht.SPS ist besonders vorteilhaft für die Herstellung von nanostrukturierten Keramiken, Refraktärmetallen und Verbundwerkstoffen mit verbesserten mechanischen, thermischen und elektrischen Eigenschaften.Es minimiert das Kornwachstum und die Vergröberung und ist damit ideal für die Herstellung feinkörniger Materialien mit hoher Dichte und hervorragender Leistung.
Die wichtigsten Punkte werden erklärt:
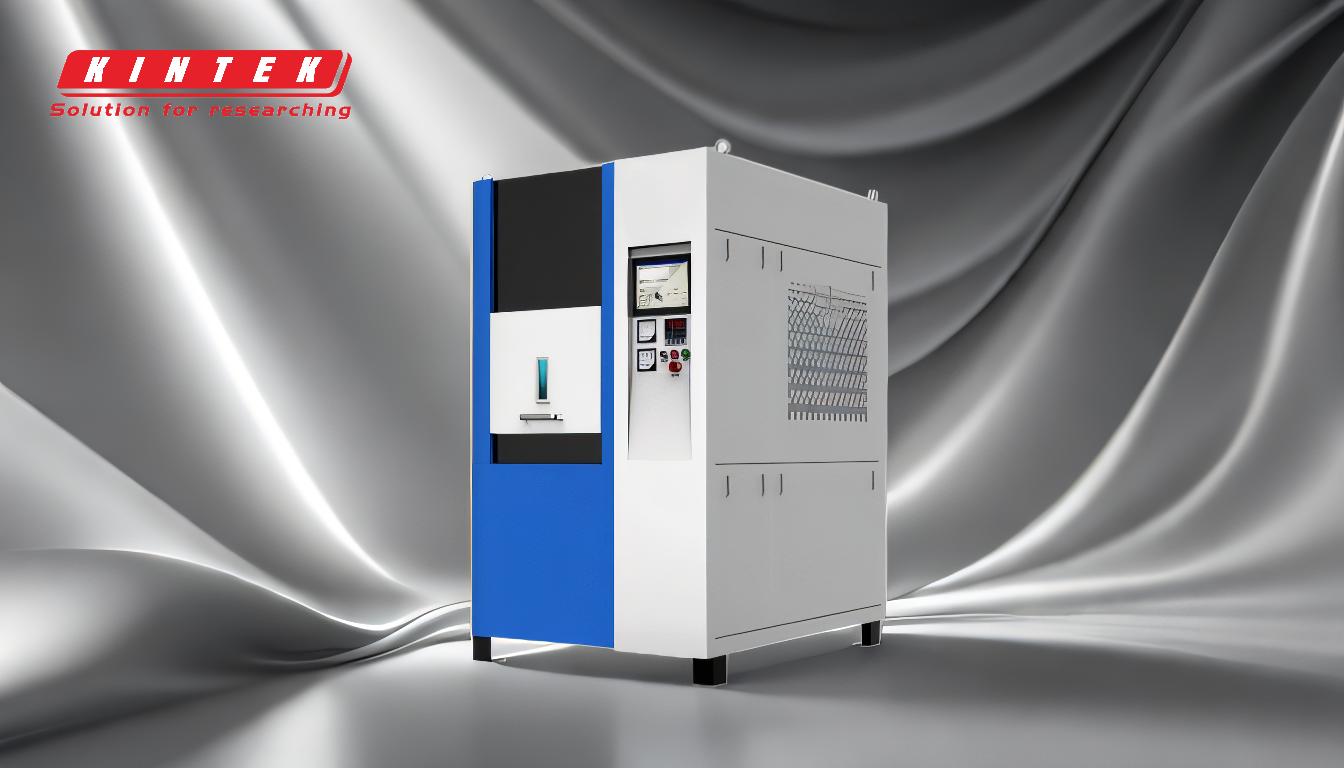
-
Definition und Mechanismus von SPS:
- SPS steht für Spark Plasma Sintering, eine Sintertechnik, bei der gepulster elektrischer Strom und mechanischer Druck eingesetzt werden, um Pulver zu dichten Materialien zu verfestigen.
- Bei diesem Verfahren wird ein elektrischer Strom mit hoher Intensität direkt auf das Pulvermaterial aufgebracht, wodurch durch Joulesche Erwärmung Wärme erzeugt und eine schnelle Verdichtung ermöglicht wird.
- Gleichzeitig wird uniaxialer Druck ausgeübt, um die Umlagerung und Bindung der Partikel zu erleichtern, was zu Materialien mit hoher Dichte und minimalem Kornwachstum führt.
-
Die wichtigsten Vorteile von SPS:
- Schnelle Aufheizraten:Mit SPS können Heizraten von bis zu 1000°C/min erreicht werden, wodurch sich die Sinterzeit im Vergleich zu herkömmlichen Verfahren erheblich verkürzt.
- Niedertemperatur-Verarbeitung:SPS kann bei niedrigeren Temperaturen (z. B. 500-1000 °C) betrieben werden und erreicht dennoch eine vollständige Verdichtung, was besonders bei temperaturempfindlichen Materialien von Vorteil ist.
- Präzise Steuerung:Das Verfahren ermöglicht eine präzise Steuerung von Temperatur, Druck und Heizrate und damit maßgeschneiderte Materialeigenschaften.
- Minimiertes Kornwachstum:Der schnelle Sinterprozess verhindert Vergröberung und Kornwachstum, wodurch Nanostrukturen erhalten bleiben und feinkörnige Materialien mit verbesserten mechanischen Eigenschaften entstehen.
-
Anwendungen von SPS:
- Nanomaterialien:SPS wird häufig zur Herstellung von nanostrukturierten Keramiken, Nanokompositen und amorphen Legierungen mit hoher Dichte und minimalen Defekten eingesetzt.
- Refraktäre Metalle:Es eignet sich besonders gut für das Sintern von hochschmelzenden Metallen wie Wolfram, Vanadium, Niob und deren Legierungen, wobei Materialien mit feineren Körnern und besseren mechanischen Eigenschaften entstehen.
- Gradient Functional Materials:SPS ermöglicht die Herstellung von Materialien mit abgestuften Zusammensetzungen und Eigenschaften, die mit herkömmlichen Methoden nur schwer zu erreichen sind.
- Keramiken und Cermets mit hoher Dichte:Das Verfahren ist ideal für die Herstellung dichter, feinkörniger Keramiken und Cermets mit hoher Festigkeit, Härte und Verschleißfestigkeit.
-
Leistungsvorteile:
- Verbesserte mechanische Eigenschaften:Die mit SPS hergestellten Werkstoffe weisen eine höhere Festigkeit, Härte und Biegefestigkeit auf als die mit herkömmlichen Verfahren gesinterten.
- Verbesserte thermische und elektrische Eigenschaften:Die feinkörnige Mikrostruktur und die hohe Dichte, die durch SPS erreicht werden, führen zu Materialien mit ausgezeichneter Wärmeleitfähigkeit und elektrischer Leistung.
- Konservierung von Nanostrukturen:SPS verhindert das Kornwachstum während des Sinterns und ermöglicht so die Beibehaltung der intrinsischen Nanostrukturen und einzigartigen chemischen Eigenschaften.
-
Vergleich mit traditionellen Sinterverfahren:
- Zeit-Effizienz:SPS verkürzt die Sinterzeit erheblich.Eine vergleichende Studie zeigte beispielsweise, dass das SPS-Sintern von WCl2-Co-Hartmetall nur 1/26 der für das Vakuumsintern benötigten Zeit in Anspruch nahm.
- Qualität der Werkstoffe:SPS erzeugt Materialien mit feineren Körnern und höherer Dichte, was zu besseren mechanischen Eigenschaften führt.In derselben Studie wiesen SPS-gesinterte Werkstoffe im Vergleich zu vakuumgesinterten Gegenstücken eine um 13 % höhere Biegefestigkeit auf.
- Vielseitigkeit:SPS kann Werkstoffe konsolidieren, die mit herkömmlichen Methoden nur schwer oder gar nicht zu bearbeiten sind, wie z. B. Ultrahochtemperaturkeramik wie ZrC.
-
Zukünftiges Potenzial und Forschungsrichtungen:
- Fortgeschrittene Materialentwicklung:SPS wird in zunehmendem Maße zur Entwicklung technischer Strukturen und einzigartiger chemischer Eigenschaften eingesetzt, die während des Sinterns erhalten bleiben, was sie zu einer Schlüsseltechnologie für die moderne Materialforschung macht.
- Synthese von neuartigen Pulvern:Die Technik wird auch für die Synthese von Pulvern erforscht, die mit herkömmlichen Methoden nur schwer zu gewinnen sind, wie z. B. Ultrahochtemperaturmaterialien.
- Nachhaltigkeit:Die Fähigkeit, Materialien bei niedrigeren Temperaturen und kürzeren Zeiten zu verarbeiten, macht SPS zu einem energieeffizienteren und umweltfreundlicheren Sinterverfahren.
Zusammenfassend lässt sich sagen, dass SPS eine transformative Technologie in der Materialwissenschaft ist, die eine beispiellose Kontrolle über Sinterprozesse bietet und die Herstellung von Hochleistungswerkstoffen mit einzigartigen Eigenschaften ermöglicht.Ihre Anwendungen umfassen ein breites Spektrum von Werkstoffen, von nanostrukturierten Keramiken bis hin zu hochschmelzenden Metallen, und ihre Vorteile gegenüber herkömmlichen Sinterverfahren machen sie zu einem entscheidenden Werkzeug für den Fortschritt in der Materialwissenschaft und -technik.
Zusammenfassende Tabelle:
Aspekt | Einzelheiten |
---|---|
Definition | SPS verwendet gepulsten elektrischen Strom und einachsigen Druck zur schnellen Sinterung. |
Die wichtigsten Vorteile | Schnelle Heizraten (bis zu 1000°C/min), Niedertemperaturverarbeitung, präzise Steuerung, minimiertes Kornwachstum. |
Anwendungen | Nanomaterialien, hochschmelzende Metalle, funktionelle Materialien mit Gradienten, Keramik mit hoher Dichte. |
Leistungsvorteile | Verbesserte mechanische, thermische und elektrische Eigenschaften; Erhaltung von Nanostrukturen. |
Vergleich | Schneller, feinere Körner, höhere Dichte und Vielseitigkeit im Vergleich zu traditionellen Methoden. |
Zukünftiges Potenzial | Fortschrittliche Materialentwicklung, neuartige Pulversynthese, Nachhaltigkeit. |
Erschließen Sie das Potenzial des Spark-Plasma-Sinterns für Ihre Werkstoffe. Kontaktieren Sie uns noch heute um mehr zu erfahren!