Das magnetisch unterstützte Sputtern, auch Magnetronsputtern genannt, ist ein hocheffizientes und vielseitiges Verfahren zur Abscheidung von Dünnschichten, das zahlreiche Vorteile gegenüber herkömmlichen Sputterverfahren bietet.Durch den Einsatz von Magnetfeldern zum Einfangen von Sekundärelektronen in der Nähe der Target-Oberfläche wird die Ionisierungseffizienz erhöht, die Abscheidungsrate gesteigert und die Schichtqualität verbessert.Diese Methode eignet sich für eine breite Palette von Materialien, einschließlich Metallen und Isolatoren, und wird in vielen Branchen eingesetzt, z. B. in der Mikroelektronik, der Optik und bei verschleißfesten Beschichtungen.Die Fähigkeit, gleichmäßige, hochreine Schichten mit präziser Dickenkontrolle zu erzeugen, macht es zu einer bevorzugten Wahl sowohl für die Forschung als auch für industrielle Anwendungen.
Die wichtigsten Punkte erklärt:
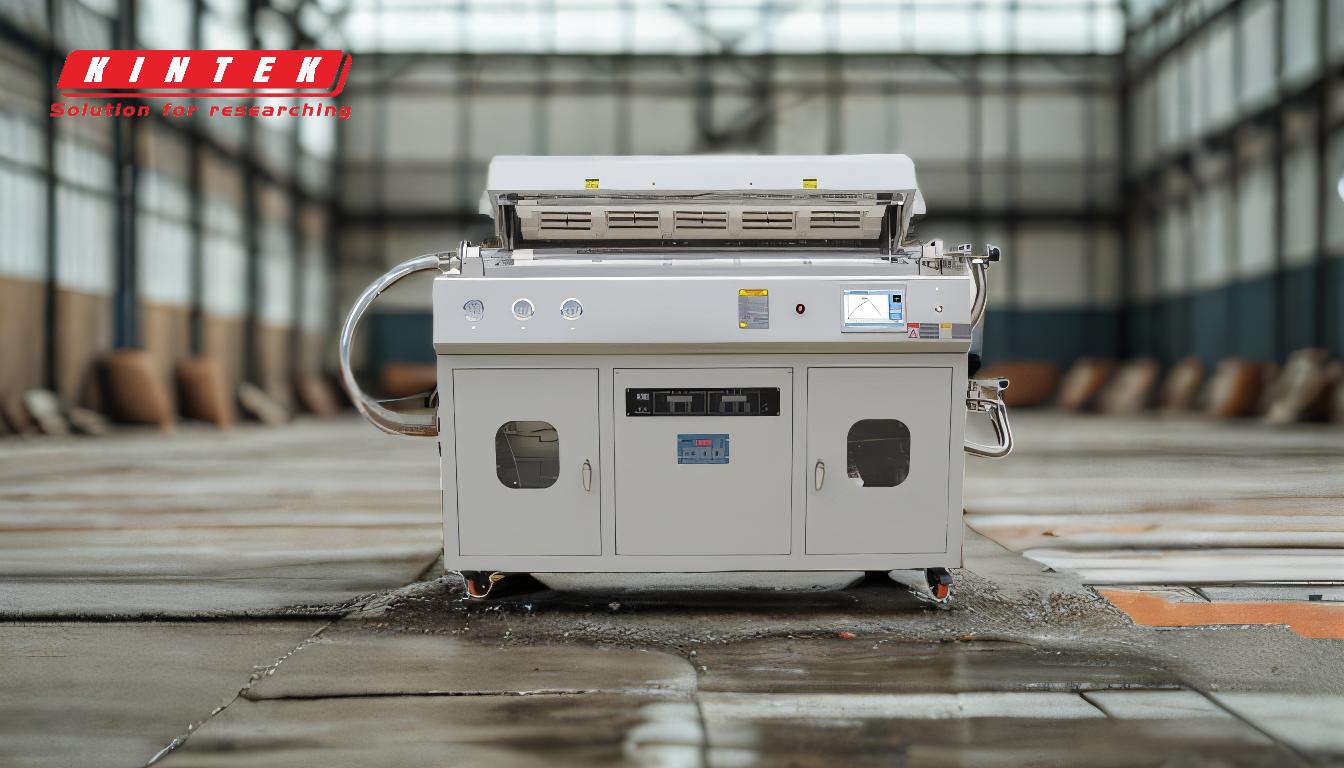
-
Erhöhte Ionisierung und Plasmadichte:
- Beim magnetisch unterstützten Sputtern werden die Sekundärelektronen mit Hilfe von Magnetfeldern in der Nähe der Targetoberfläche eingeschlossen.
- Dieser Einschluss erhöht die Ionisierung des Argongases, wodurch ein dichteres Plasma entsteht.
- Eine höhere Plasmadichte führt zu einem effizienteren Sputtern und schnelleren Abscheidungsraten.
-
Betrieb mit niedrigerem Druck:
- Dank des Magnetfelds kann das Verfahren im Vergleich zum herkömmlichen Sputtern mit niedrigerem Druck betrieben werden.
- Der niedrigere Druck verringert die Verunreinigung und verbessert die Reinheit der abgeschiedenen Schichten.
-
Hohe Abscheideraten:
- Die erhöhte Ionisierung und Plasmadichte führen zu höheren Sputterraten.
- Dadurch wird das Magnetronsputtern schneller und effizienter als herkömmliche Verfahren.
-
Präzision und Gleichmäßigkeit:
- Die Magnetronzerstäubung bietet eine hervorragende Kontrolle über die Schichtdicke mit Schwankungen von weniger als 2 % über das gesamte Substrat.
- Es gewährleistet eine gleichmäßige Abscheidung über große Flächen und ist damit ideal für industrielle Anwendungen.
-
Vielseitigkeit bei der Materialabscheidung:
- Im Gegensatz zur thermischen Verdampfung ist beim Magnetronsputtern kein Erhitzen oder Schmelzen des Zielmaterials erforderlich.
- Es kann eine breite Palette von Materialien abgeschieden werden, darunter Metalle, Isolatoren und Verbindungen, unabhängig von ihrem Schmelzpunkt.
-
Hochwertige Filme:
- Das Verfahren erzeugt dichte, hochreine Schichten mit hervorragender Haftung auf dem Substrat.
- Die durch Magnetronsputtern abgeschiedenen Schichten sind frei von Defekten und haben hervorragende mechanische, optische und elektrische Eigenschaften.
-
Niedertemperaturabscheidung:
- Das Magnetronsputtern arbeitet bei relativ niedrigen Temperaturen, so dass temperaturempfindliche Substrate nicht beschädigt werden.
- Daher eignet sich dieses Verfahren für Anwendungen in der Mikroelektronik und der Halbleiterfertigung.
-
Kosten-Nutzen-Verhältnis:
- Die hohen Abscheidungsraten und die Fähigkeit, große Mengen an Schichten zu produzieren, machen das Magnetronsputtern zu einer kostengünstigen Lösung.
- Es reduziert die Produktionszeit und den Materialabfall und senkt so die gesamten Herstellungskosten.
-
Mehrere Konfigurationen:
- Magnetron-Sputteranlagen können mit mehreren Targets konfiguriert werden, was die Abscheidung von Mehrschicht- oder Verbundschichten ermöglicht.
- Das RF-Magnetron-Sputtern erweitert die Technik auf nichtleitende Materialien, was ihre Anwendbarkeit noch weiter ausdehnt.
-
Industrielle Anwendungen:
- Das magnetisch unterstützte Sputtern wird in verschiedenen Industriezweigen für Anwendungen wie verschleißfeste Beschichtungen, Korrosionsschutz und funktionelle Beschichtungen eingesetzt.
- Besonders wertvoll ist es in der Mikroelektronik für die Abscheidung von dielektrischen und Nitridschichten.
Zusammenfassend lässt sich sagen, dass das magnetisch unterstützte Sputtern eine Kombination aus Effizienz, Präzision und Vielseitigkeit darstellt, die es zu einem überlegenen Dünnschichtverfahren sowohl für die Forschung als auch für industrielle Anwendungen macht.Die Fähigkeit, qualitativ hochwertige, gleichmäßige Schichten bei niedrigeren Kosten und Temperaturen zu erzeugen, sorgt für eine anhaltende Dominanz in diesem Bereich.
Zusammenfassende Tabelle:
Hauptmerkmal | Beschreibung |
---|---|
Verbesserte Ionisierung | Magnetfelder erhöhen die Plasmadichte und verbessern die Sputtereffizienz. |
Betrieb mit niedrigerem Druck | Verringert Verunreinigungen und gewährleistet hochreine Schichten. |
Hohe Abscheideraten | Schneller und effizienter als herkömmliche Methoden. |
Präzision und Gleichmäßigkeit | Kontrolle der Schichtdicke mit weniger als 2 % Abweichung über alle Substrate hinweg. |
Vielseitigkeit bei Materialien | Abscheidung von Metallen, Isolatoren und Verbindungen ohne Schmelzen. |
Hochwertige Filme | Erzeugt dichte, defektfreie Schichten mit hervorragenden Eigenschaften. |
Niedertemperatur-Beschichtung | Ideal für temperaturempfindliche Substrate in der Mikroelektronik. |
Kosteneffizienz | Reduziert die Produktionszeit und den Materialabfall und senkt so die Kosten. |
Mehrere Konfigurationen | Unterstützt mehrschichtige und zusammengesetzte Folien, einschließlich nicht leitender Materialien. |
Industrielle Anwendungen | Einsatz in der Mikroelektronik, Optik, bei verschleißfesten Beschichtungen und mehr. |
Erschließen Sie das Potenzial des magnetisch unterstützten Sputterns für Ihre Anwendungen. Kontaktieren Sie unsere Experten noch heute !