PVD-Beschichtungen (Physical Vapor Deposition) bestehen aus einer Vielzahl von Materialien, darunter Metalle, Legierungen, Keramiken und spezielle Verbindungen, die auf die spezifischen Leistungsanforderungen verschiedener Branchen zugeschnitten sind.Zu den gängigen Materialien gehören Titan, Zirkonium, Aluminium, Edelstahl, Kupfer und Gold, die häufig in der Luft- und Raumfahrt sowie in der Elektronik verwendet werden.Darüber hinaus werden spezielle Beschichtungen wie Karbide, Nitride, Silizide und Boride eingesetzt, um Haltbarkeit und Funktionalität zu verbessern.Diese Beschichtungen können auf verschiedene Substrate wie Metalle, Kunststoffe, Glas und Keramik aufgebracht werden, was sie vielseitig einsetzbar macht - von dekorativen Oberflächen bis hin zu hochleistungsfähigen Industriekomponenten.
Die wichtigsten Punkte erklärt:
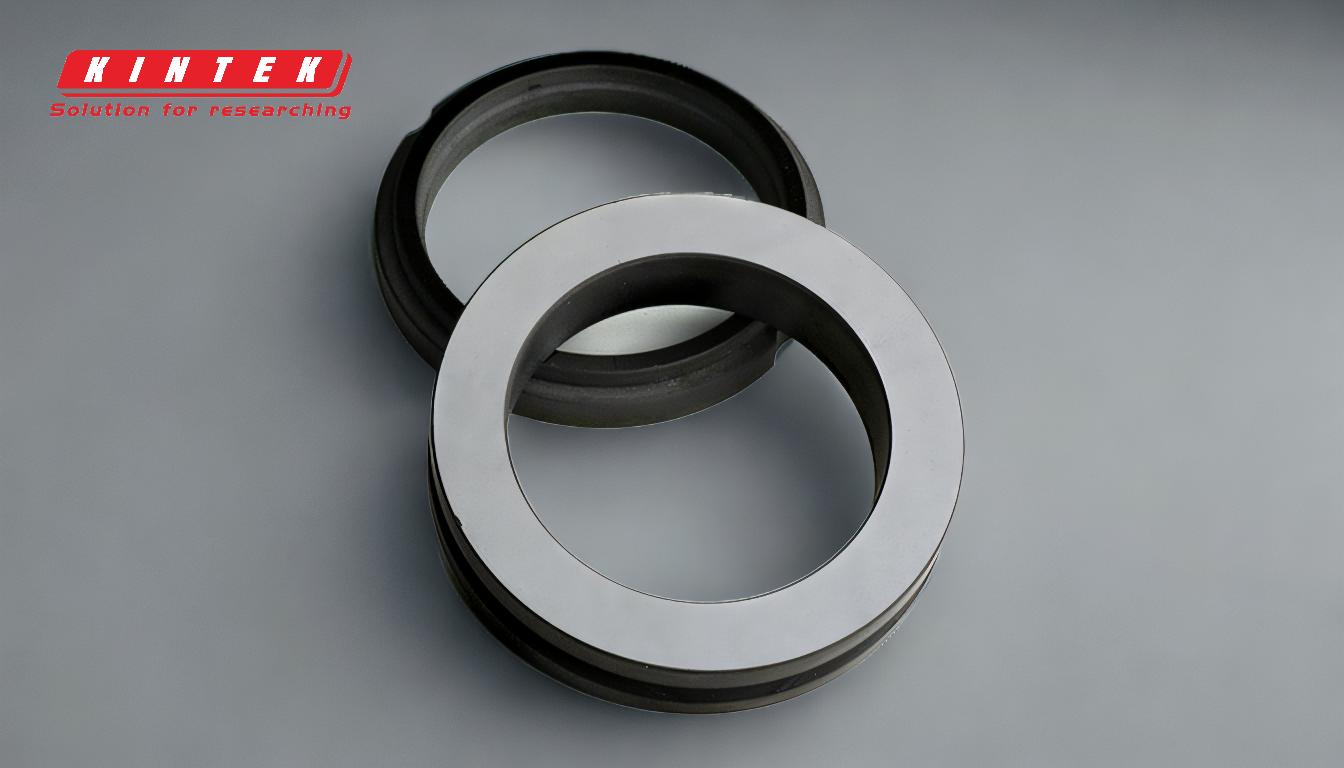
-
Primärmaterialien in PVD-Beschichtungen:
- Metalle:Titan, Zirkonium, Aluminium, rostfreier Stahl und Kupfer werden üblicherweise verwendet.Auch Gold wird häufig nachgefragt, insbesondere in der Luft- und Raumfahrtelektronik, da es eine hervorragende Leitfähigkeit und Korrosionsbeständigkeit aufweist.
- Legierungen und Keramiken:Materialien wie Cr2N, TiN, ZnSn, AlCr und ITO (Indium-Zinn-Oxid) werden häufig verwendet.Diese Verbindungen bieten spezifische Eigenschaften wie Härte, Leitfähigkeit und optische Leistung und eignen sich daher für Anwendungen in der Uhren-, Schmuck-, Elektronik- und Industrietechnik.
-
Spezialisierte Verbindungen:
- Karbide, Nitride und Silizide:Sie werden wegen ihrer hohen Härte und Verschleißfestigkeit verwendet und sind daher ideal für Schneidwerkzeuge, Maschinenteile und Automobilkomponenten.
- Diamantähnlicher Kohlenstoff (DLC):DLC ist für seine außergewöhnliche Härte und geringe Reibung bekannt und wird für Anwendungen verwendet, die eine hohe Verschleißfestigkeit und Haltbarkeit erfordern.
- Materialien auf Schwefel- und Molybdänbasis:Diese werden wegen ihrer Schmiereigenschaften verwendet, die Reibung und Verschleiß in beweglichen Teilen verringern.
-
Anwendungsspezifische Materialien:
- Dekorative Beschichtungen:TiN wird aufgrund seiner attraktiven goldenen Farbe und seiner Haltbarkeit häufig für dekorative Zwecke bei Gegenständen wie Uhren, Brillen und Hardware verwendet.
- Optische Beschichtungen:ZnSn wird in Fenstern und Gläsern mit niedrigem Emissionsgrad (Low-e) verwendet, die durch die Reflexion von Infrarotlicht für Energieeffizienz sorgen.
- Leitfähige Beschichtungen:ITO-Dünnschichten werden aufgrund ihrer hohen Leitfähigkeit und Transparenz in LCDs, Plasmabildschirmen und Touchpanels verwendet.
-
Substrate für PVD-Beschichtungen:
- Metalle:Edelstahl und Aluminium sind gängige Substrate, die häufig in der Industrie und in der Luft- und Raumfahrt eingesetzt werden.
- Nicht-Metalle:PVD-Beschichtungen können auch auf Nylon, Kunststoff, Glas und Keramik aufgebracht werden, was ihre Verwendung in der Unterhaltungselektronik, der Automobilindustrie und der dekorativen Industrie erweitert.
-
Industrie-spezifische Anforderungen:
- Luft- und Raumfahrt:Goldbeschichtungen werden wegen ihrer hervorragenden Leitfähigkeit und Korrosionsbeständigkeit verwendet, die für elektronische Bauteile in rauen Umgebungen entscheidend sind.
- Automobilindustrie:AlCr-Beschichtungen verlängern die Lebensdauer von Werkzeugen und Maschinenteilen und sorgen für bessere Haltbarkeit und Leistung.
- Elektronik:ITO-Dünnschichten sind unverzichtbar für Anwendungen mit hoher Leitfähigkeit und hoher Härte in Displays und Touchpanels.
Zusammenfassend lässt sich sagen, dass die chemische Zusammensetzung von PVD-Beschichtungen sehr vielseitig ist und eine breite Palette von Materialien und Verbindungen umfasst, die auf spezifische Leistungsanforderungen in verschiedenen Branchen zugeschnitten sind.Diese Vielseitigkeit macht PVD-Beschichtungen zu einer wichtigen Technologie in der modernen Fertigung und bei industriellen Anwendungen.
Zusammenfassende Tabelle:
Kategorie | Werkstoffe | Anwendungen |
---|---|---|
Primäre Materialien | Titan, Zirkonium, Aluminium, rostfreier Stahl, Kupfer, Gold | Luft- und Raumfahrtelektronik, Industriewerkzeuge, dekorative Oberflächen |
Legierungen und Keramiken | Cr2N, TiN, ZnSn, AlCr, ITO | Uhren, Schmuck, Elektronik, Fenster mit niedrigem Emissionsgrad, LCDs, Touchpanels |
Spezialisierte Verbindungen | Karbide, Nitride, Silizide, diamantähnlicher Kohlenstoff (DLC), Schwefel, Molybdän | Schneidwerkzeuge, Maschinenteile, Automobilteile, hohe Verschleißfestigkeit |
Substrate | Metalle (Edelstahl, Aluminium), Nicht-Metalle (Kunststoffe, Glas, Keramik) | Industrie, Luft- und Raumfahrt, Unterhaltungselektronik, dekorative Industrie |
Branchenspezifisch | Gold (Luft- und Raumfahrt), AlCr (Automobil), ITO (Elektronik) | Korrosionsbeständigkeit, Langlebigkeit, Anwendungen mit hoher Leitfähigkeit |
Erschließen Sie das Potenzial von PVD-Beschichtungen für Ihre Branche. Kontaktieren Sie unsere Experten noch heute um mehr zu erfahren!