Der Hauptunterschied zwischen AC- (RF) und DC-Sputtern liegt in der Art der verwendeten Stromquelle und den Materialien, für die sie geeignet sind.Beim DC-Sputtern wird eine Gleichstromquelle verwendet, die sich ideal für leitfähige Materialien wie reine Metalle eignet und hohe Abscheideraten und Kosteneffizienz für große Substrate bietet.Im Gegensatz dazu verwendet das HF-Sputtern eine Wechselstromquelle, in der Regel bei 13,56 MHz, und eignet sich sowohl für leitende als auch für nichtleitende Materialien, insbesondere für dielektrische Targets.Das RF-Sputtern hat eine geringere Abscheiderate, ist teurer und eignet sich besser für kleinere Substrate.Darüber hinaus umfasst das HF-Sputtern einen zweistufigen Prozess der Polarisierung und Umkehrung der Polarisierung, während beim DC-Sputtern positiv geladene Gasionen zur Abscheidung auf das Target beschleunigt werden.
Die wichtigsten Punkte werden erklärt:
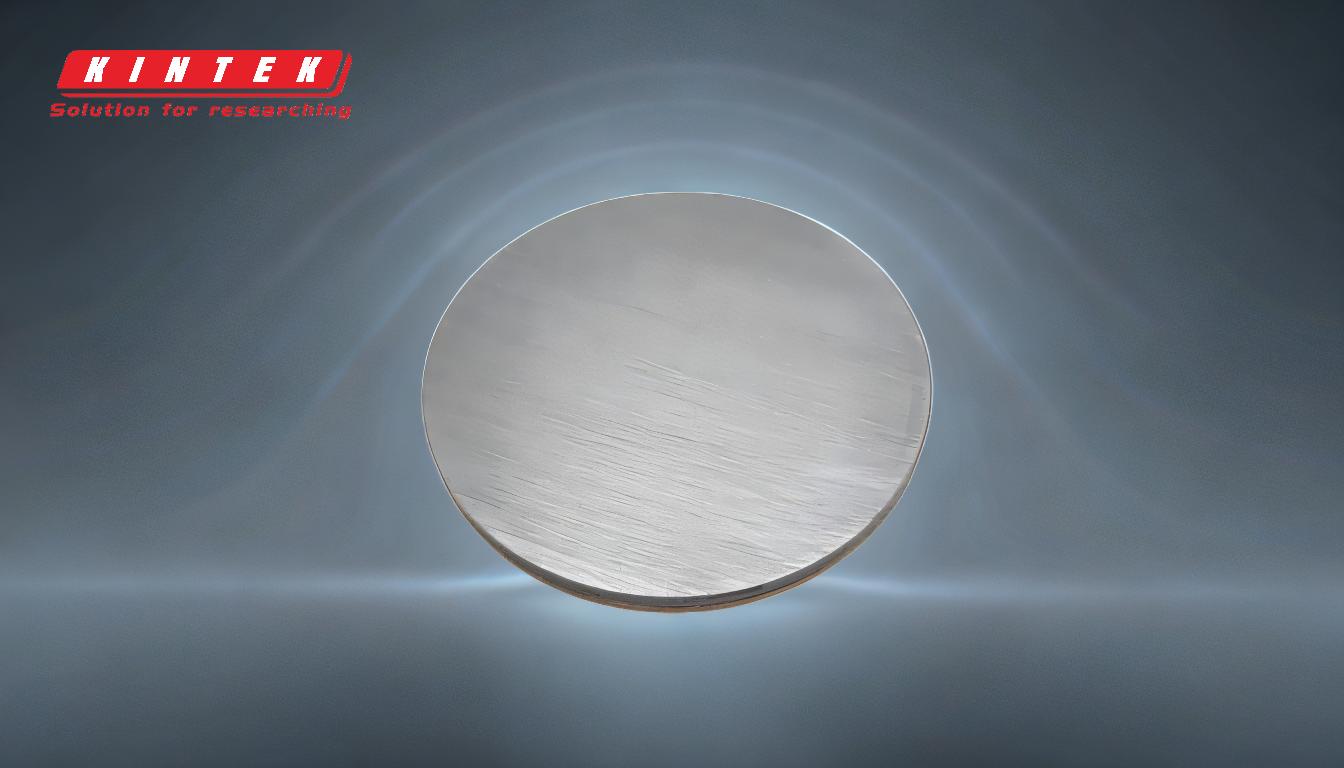
-
Stromquelle:
- DC-Sputtern:Verwendet eine Gleichstromquelle (DC).Diese Methode ist einfach und effektiv für leitfähige Materialien, da sie auf einem konstanten Stromfluss beruht.
- RF-Sputtern:Verwendet eine Wechselstromquelle (AC), typischerweise bei 13,56 MHz.Durch die wechselnde Polarität können sowohl leitende als auch nichtleitende Materialien bearbeitet werden.
-
Material-Eignung:
- DC-Sputtern:Am besten geeignet für leitende Materialien wie reine Metalle (z. B. Eisen, Kupfer, Nickel).Für nichtleitende Materialien ist es nicht geeignet, da der konstante Strom die Ladungsansammlung auf der Zieloberfläche nicht neutralisieren kann.
- RF-Sputtern:Geeignet sowohl für leitende als auch für nichtleitende Materialien, insbesondere für dielektrische Ziele.Der Wechselstrom neutralisiert die Ladungsansammlungen auf der Oberfläche des Targets, wodurch es für ein breiteres Spektrum von Materialien geeignet ist.
-
Abscheiderate:
- DC-Sputtern:Bietet eine hohe Abscheidungsrate und ist damit effizient für die Großserienproduktion und große Substrate.
- RF-Sputtern:Im Vergleich zum DC-Sputtern ist die Abscheiderate geringer, was bei großflächigen Anwendungen ein limitierender Faktor sein kann, bei kleineren Substraten jedoch akzeptabel ist.
-
Kosten und Effizienz:
- DC-Sputtern:Kosteneffizienter und wirtschaftlicher, vor allem bei der Bearbeitung großer Mengen von großen Substraten.
- RF-Sputtern:Teurer aufgrund der Komplexität der Wechselstromquelle und der geringeren Sputterausbeute, daher eher für kleinere Substratgrößen geeignet.
-
Prozess-Mechanismus:
- DC-Sputtern:Beschleunigt positiv geladene Gasionen auf das Ziel und stößt dabei Atome aus, die sich auf den Substraten ablagern.Dieses Verfahren ist einfach und effizient für leitende Materialien.
- RF-Sputtern:Es handelt sich um einen Zwei-Zyklen-Prozess mit Polarisation und umgekehrter Polarisation.Während eines Halbzyklus neutralisieren die Elektronen die positiven Ionen auf der Oberfläche des Targets, und während des anderen Halbzyklus werden die Atome des Targets zerstäubt und auf dem Substrat abgelagert.Durch diesen abwechselnden Prozess kann das RF-Sputtern nichtleitende Materialien effektiv behandeln.
-
Anwendungen:
- DC-Sputtern:Ideal für Anwendungen, die hohe Abscheideraten und große Produktionsmengen erfordern, wie z. B. bei der Herstellung von Metallbeschichtungen und leitfähigen Schichten.
- RF-Sputtern:Geeignet für Anwendungen, bei denen sowohl leitende als auch nichtleitende Materialien zum Einsatz kommen, z. B. bei der Abscheidung dielektrischer Schichten und spezieller Beschichtungen auf kleineren Substraten.
Durch die Kenntnis dieser Hauptunterschiede können Käufer von Anlagen und Verbrauchsmaterialien fundierte Entscheidungen auf der Grundlage der spezifischen Anforderungen ihrer Projekte treffen, unabhängig davon, ob sie der Kosteneffizienz, der Materialvielfalt oder der Abscheiderate Vorrang einräumen.
Zusammenfassende Tabelle:
Blickwinkel | DC-Zerstäubung | RF-Sputtern |
---|---|---|
Stromquelle | Gleichstrom (DC) | Wechselstrom (AC), typischerweise bei 13,56 MHz |
Material-Eignung | Am besten für leitende Materialien (z. B. reine Metalle) | Geeignet sowohl für leitende als auch für nicht leitende Materialien (z. B. dielektrische Schichten) |
Abscheiderate | Hohe Abscheiderate, ideal für die Großserienproduktion | Geringere Abscheidungsrate, besser für kleinere Substrate |
Kosten und Effizienz | Kostengünstig für große Substrate und Großserienproduktion | Teurer, geeignet für kleinere Substrate |
Mechanismus des Verfahrens | Beschleunigt positiv geladene Gas-Ionen auf das Ziel | Zweistufiger Prozess: Polarisation und umgekehrte Polarisation |
Anwendungen | Metallbeschichtungen, leitende Schichten, Großserienproduktion | Dielektrische Filme, spezielle Beschichtungen, kleinere Substrate |
Benötigen Sie Hilfe bei der Auswahl des richtigen Sputtering-Verfahrens für Ihr Projekt? Kontaktieren Sie noch heute unsere Experten für eine persönliche Beratung!