CVD (Chemical Vapour Deposition) und PVD (Physical Vapour Deposition) sind zwei weit verbreitete Beschichtungstechnologien mit jeweils unterschiedlichen Prozessen, Vorteilen und Anwendungen. CVD beinhaltet chemische Reaktionen zwischen gasförmigen Vorläufern und dem Substrat bei hohen Temperaturen, was zu einer multidirektionalen Abscheidung und der Möglichkeit zur Beschichtung komplexer Geometrien führt. PVD hingegen beruht auf der physikalischen Verdampfung fester Materialien, wodurch diese bei niedrigeren Temperaturen direkt sichtbar abgeschieden werden. Die Wahl zwischen CVD und PVD hängt von Faktoren wie Substratmaterial, gewünschten Beschichtungseigenschaften und Anwendungsanforderungen ab.
Wichtige Punkte erklärt:
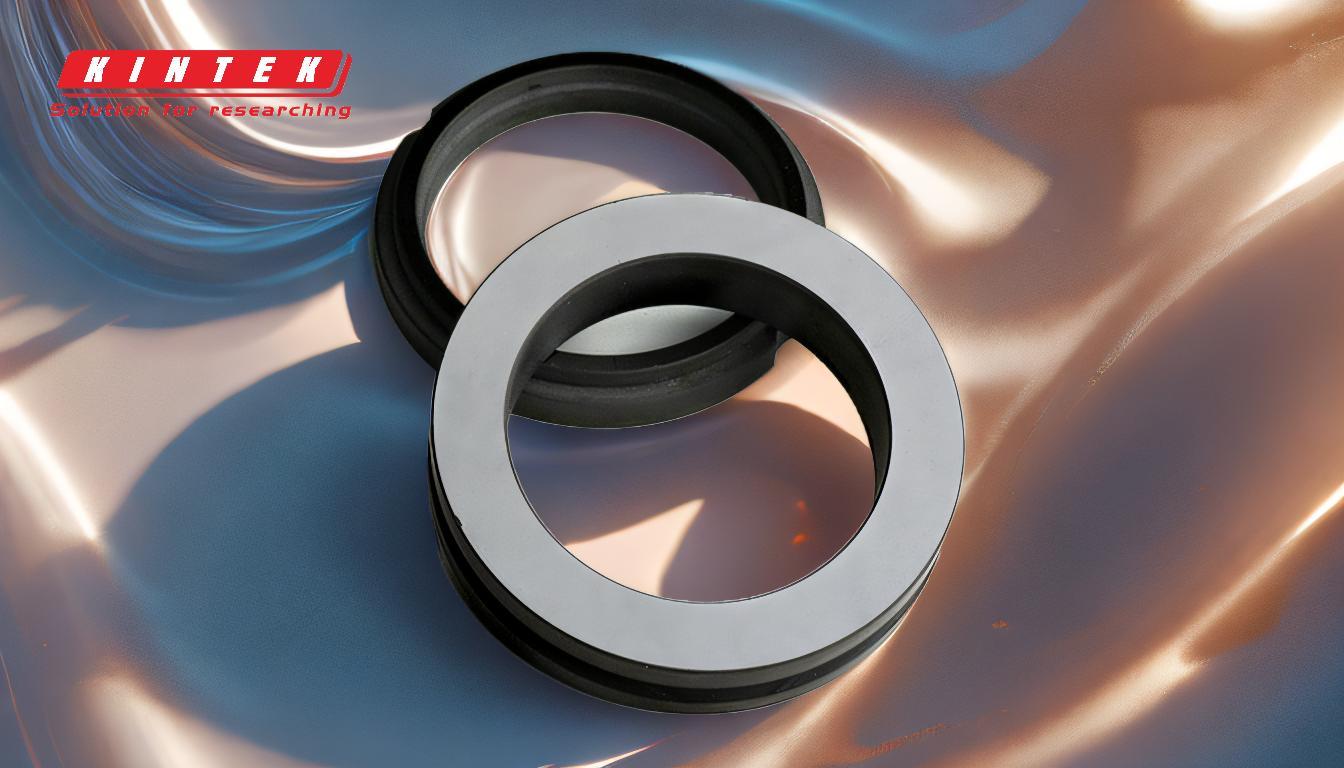
-
Ablagerungsmechanismus:
- CVD: Beinhaltet chemische Reaktionen zwischen gasförmigen Vorläufern und dem Substrat. Der Prozess ist multidirektional und ermöglicht die gleichmäßige Beschichtung komplexer Formen, Löcher und tiefer Vertiefungen.
- PVD: Beruht auf der physikalischen Verdampfung fester Materialien, die dann direkt auf dem Substrat abgeschieden werden. Dies schränkt seine Fähigkeit ein, komplexe Geometrien gleichmäßig zu beschichten.
-
Temperaturanforderungen:
- CVD: Arbeitet bei hohen Temperaturen, typischerweise zwischen 450 °C und 1050 °C. Diese Hochtemperaturumgebung begünstigt chemische Reaktionen, kann aber auch zu thermischer Spannung und feinen Rissen in der Beschichtung führen.
- PVD: Funktioniert bei niedrigeren Temperaturen, normalerweise zwischen 250 °C und 450 °C. Dadurch eignet es sich für temperaturempfindliche Untergründe und verringert das Risiko einer thermischen Schädigung.
-
Beschichtungsmaterial und -dicke:
- CVD: Verwendet gasförmige Vorläufer, die unter Bildung einer festen Beschichtung reagieren. CVD kann dickere Beschichtungen erzeugen (10–20 μm) und wird häufig für Anwendungen eingesetzt, die eine hohe Verschleißfestigkeit erfordern.
- PVD: Verwendet feste Materialien, die verdampft und auf dem Substrat abgeschieden werden. PVD-Beschichtungen sind normalerweise dünner (3–5 μm), bieten aber eine hervorragende Härte und Haftung.
-
Beschichtungseigenschaften:
- CVD: Erzeugt Beschichtungen mit hoher Streufähigkeit und eignet sich daher ideal für die Beschichtung komplexer Formen und tiefer Vertiefungen. Allerdings kann es durch die hohen Temperaturen zu Zugspannungen und feinen Rissen kommen.
- PVD: Bildet beim Abkühlen Druckspannung, was zu Beschichtungen mit hoher Härte und ausgezeichneter Haftung führt. PVD-Beschichtungen sind im Vergleich zu CVD außerdem glatter und gleichmäßiger.
-
Anwendungen:
- CVD: Wird häufig in Anwendungen verwendet, die dicke, verschleißfeste Beschichtungen erfordern, wie z. B. Schneidwerkzeuge, Halbleiterbauteile und verschleißfeste Komponenten.
- PVD: Bevorzugt für Anwendungen, die dünne, harte Beschichtungen mit hoher Präzision erfordern, wie z. B. dekorative Beschichtungen, optische Beschichtungen und Präzisionswerkzeuge.
-
Wirtschaftliche und betriebliche Überlegungen:
- CVD: Oft wirtschaftlicher aufgrund hoher Abscheidungsraten und der Möglichkeit, dicke Beschichtungen zu erzeugen. Es ist kein Ultrahochvakuum erforderlich, was die Betriebskosten senken kann.
- PVD: Während die Abscheidungsraten im Allgemeinen niedriger sind, bietet PVD eine hohe Materialausnutzungseffizienz und kann bei niedrigeren Temperaturen durchgeführt werden, was den Energieverbrauch senkt.
Zusammenfassend hängt die Wahl zwischen CVD und PVD von den spezifischen Anforderungen der Anwendung ab, einschließlich des Substratmaterials, der gewünschten Beschichtungseigenschaften und der betrieblichen Einschränkungen. CVD ist ideal für komplexe Geometrien und dicke Beschichtungen, während PVD sich durch die Herstellung dünner, harter Beschichtungen mit hervorragender Haftung und Oberflächengüte auszeichnet.
Übersichtstabelle:
Aspekt | CVD | PVD |
---|---|---|
Ablagerungsmechanismus | Chemische Reaktionen mit gasförmigen Vorläufern; multidirektionale Abscheidung | Physikalische Verdampfung fester Stoffe; Sichtlinienablagerung |
Temperatur | Hoch (450 °C–1050 °C) | Niedrig (250 °C–450 °C) |
Beschichtungsdicke | Dicker (10~20μm) | Dünner (3~5μm) |
Beschichtungseigenschaften | Hohe Streukraft, gleichmäßig bei komplexen Formen; Zugspannung | Hohe Härte, hervorragende Haftung; glatter und gleichmäßiger |
Anwendungen | Schneidwerkzeuge, Halbleiter, verschleißfeste Komponenten | Dekorative Beschichtungen, optische Beschichtungen, Präzisionswerkzeuge |
Wirtschaftliche Überlegungen | Hohe Abschmelzleistung, wirtschaftlich bei dicken Schichten | Geringere Abschmelzleistung, hohe Materialeffizienz, energieeffizient |
Benötigen Sie Hilfe bei der Auswahl der richtigen Beschichtungslösung? Kontaktieren Sie noch heute unsere Experten für individuelle Beratung!