CVD (Chemical Vapor Deposition) und Sputtern (eine Form der Physical Vapor Deposition, PVD) sind beides Techniken zur Abscheidung dünner Schichten auf Substraten, die sich jedoch in ihren Mechanismen, Verfahren und Anwendungen erheblich unterscheiden.CVD beruht auf chemischen Reaktionen zwischen gasförmigen Vorläufern, um dünne Schichten zu bilden, während Sputtern physikalische Prozesse nutzt, um Material zu verdampfen und auf einem Substrat abzuscheiden.CVD arbeitet bei höheren Temperaturen und kann komplexe Geometrien beschichten, da es keine Sichtverbindung gibt, während Sputtern ein Verfahren mit niedrigeren Temperaturen ist, das sich für temperaturempfindliche Materialien eignet.Darüber hinaus weisen CVD-Beschichtungen aufgrund der chemischen Bindung in der Regel eine bessere Haftung auf, während das Sputtern in seinen Anwendungsmöglichkeiten eingeschränkter ist, aber eine genaue Kontrolle über die Zusammensetzung und Dicke der Schicht ermöglicht.
Die wichtigsten Punkte erklärt:
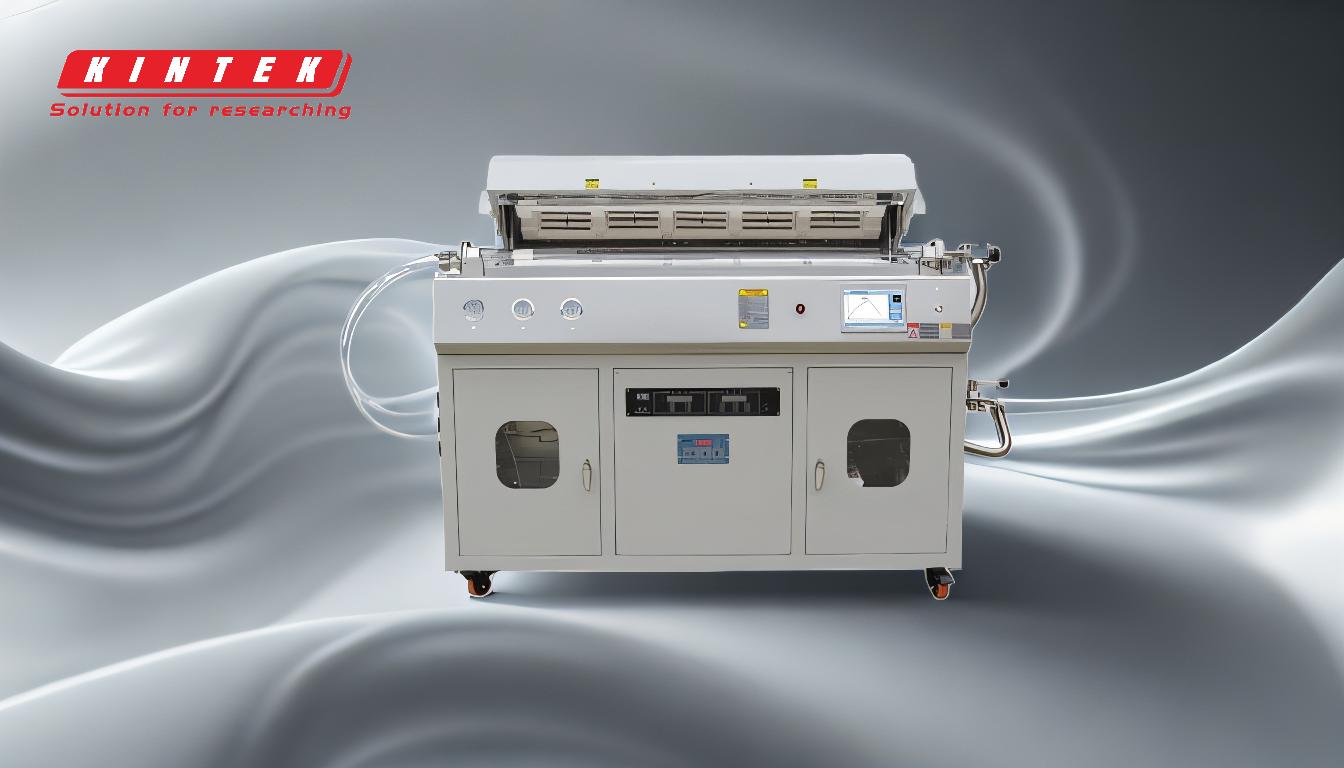
-
Mechanismus der Ablagerung:
- CVD:Chemische Reaktionen zwischen gasförmigen Vorläufersubstanzen an der Substratoberfläche zur Bildung eines dünnen festen Films.Der Prozess wird durch chemische Reaktionen angetrieben und erfordert oft hohe Temperaturen, um die Reaktionen zu aktivieren.
- Sputtern:Ein physikalisches Verfahren, bei dem Atome durch den Beschuss mit hochenergetischen Ionen aus einem festen Zielmaterial herausgeschleudert werden.Die herausgeschleuderten Atome lagern sich dann auf dem Substrat ab und bilden einen dünnen Film.Bei diesem Verfahren sind keine chemischen Reaktionen erforderlich.
-
Anforderungen an die Temperatur:
- CVD:Wird in der Regel bei höheren Temperaturen betrieben, was den Einsatz bei temperaturempfindlichen Materialien einschränken kann.Die hohen Temperaturen sind notwendig, um die chemischen Reaktionen zu aktivieren.
- Sputtern:Arbeitet bei relativ niedrigen Temperaturen und eignet sich daher für Substrate, die hohen Temperaturen nicht standhalten, wie z. B. Kunststoffe oder bestimmte Halbleiter.
-
Gleichmäßigkeit und Deckkraft der Beschichtung:
- CVD:Es handelt sich um ein Verfahren ohne Sichtverbindung, d. h. es können komplexe Geometrien beschichtet werden, darunter Gewinde, Sacklöcher und Innenflächen.Dies liegt daran, dass die gasförmigen Vorläuferstoffe jede freiliegende Oberfläche erreichen und dort reagieren können.
- Sputtern:Es handelt sich um ein Sichtlinienverfahren, das heißt, es können nur Oberflächen beschichtet werden, die dem Sputtertarget direkt ausgesetzt sind.Dies schränkt seine Fähigkeit ein, komplexe oder verborgene Geometrien gleichmäßig zu beschichten.
-
Adhäsion und Bonding:
- CVD:Die Beschichtungen werden während der Reaktion chemisch mit dem Substrat verbunden, was zu einer hervorragenden Haftung führt.Dies macht CVD-Beschichtungen äußerst haltbar und widerstandsfähig gegen Ablösung.
- Sputtern:Die Beschichtungen werden physikalisch auf das Substrat aufgebracht, was im Vergleich zur CVD zu einer schwächeren Haftung führen kann.Dennoch können durch Sputtern qualitativ hochwertige Schichten mit guter Haftung erzeugt werden, insbesondere wenn sie mit zusätzlichen Oberflächenbehandlungen kombiniert werden.
-
Anwendungen und Materialkompatibilität:
- CVD:Weit verbreitet in der Industrie für die Herstellung organischer und anorganischer Schichten auf Metallen, Halbleitern und anderen Materialien.Es ist besonders nützlich für Anwendungen, die hochreine Schichten und komplexe Geometrien erfordern.
- Sputtern:Eher begrenzte Anwendungsmöglichkeiten, aber sehr vielseitig für die Abscheidung einer breiten Palette von Materialien, einschließlich Metallen, Legierungen und Keramiken.Es wird häufig für die Herstellung von optischen Beschichtungen, Halbleiterbauelementen und dekorativen Oberflächen verwendet.
-
Prozesskomplexität und Kontrolle:
- CVD:Im Allgemeinen komplexer, da Gasfluss, Temperatur und chemische Reaktionen genau gesteuert werden müssen.Das Verfahren kann für eine großtechnische Produktion schwieriger zu handhaben sein.
- Sputtern:Bietet eine präzise Kontrolle der Filmzusammensetzung und -dicke und eignet sich daher für Anwendungen, die hohe Präzision erfordern.Das Verfahren ist relativ einfach und lässt sich für industrielle Anwendungen leichter skalieren.
-
Umwelt- und Sicherheitsaspekte:
- CVD:Häufig werden dabei gefährliche Gase und hohe Temperaturen verwendet, was strenge Sicherheitsmaßnahmen und Umweltkontrollen erfordert.
- Sputtern:In der Regel kommen weniger gefährliche Stoffe zum Einsatz und es wird mit niedrigeren Temperaturen gearbeitet, was es in vielen Fällen zu einer sichereren und umweltfreundlicheren Option macht.
Zusammenfassend lässt sich sagen, dass sowohl CVD als auch Sputtern wichtige Techniken für die Abscheidung dünner Schichten sind, die sich jedoch aufgrund ihrer einzigartigen Eigenschaften für unterschiedliche Anwendungen eignen.CVD eignet sich hervorragend für die Herstellung hochreiner, chemisch gebundener Schichten auf komplexen Geometrien, während das Sputtern eine präzise Kontrolle bietet und besser für temperaturempfindliche Materialien und einfachere Geometrien geeignet ist.
Zusammenfassende Tabelle:
Blickwinkel | CVD | Sputtern |
---|---|---|
Mechanismus | Chemische Reaktionen zwischen gasförmigen Vorläufern | Physikalischer Prozess des Ausstoßens von Atomen aus einem Ziel |
Temperatur | Hohe Temperaturen erforderlich | Niedrigere Temperaturen, geeignet für empfindliche Materialien |
Gleichmäßigkeit der Beschichtung | Nicht-Sichtlinie, beschichtet komplexe Geometrien | Sichtverbindung, beschränkt auf exponierte Oberflächen |
Haftung | Hervorragend durch chemische Bindung | Physikalisch abgelagert, kann zusätzliche Behandlungen erfordern |
Anwendungen | Hochreine Schichten, komplexe Geometrien | Optische Beschichtungen, Halbleiter, dekorative Veredelungen |
Komplexität des Prozesses | Komplex, erfordert präzise Kontrolle | Einfacher, leichter zu skalieren |
Sicherheit | Mit gefährlichen Gasen und hohen Temperaturen verbunden | Weniger Gefahren, umweltfreundlicher |
Benötigen Sie Hilfe bei der Auswahl des richtigen Verfahrens zur Dünnschichtabscheidung? Kontaktieren Sie noch heute unsere Experten !