Verdampfen und Sputtern sind beides physikalische Gasphasenabscheidungsverfahren (PVD), die zur Herstellung dünner Schichten auf Substraten verwendet werden, aber sie unterscheiden sich grundlegend in ihren Mechanismen, Betriebsbedingungen und Anwendungen.Bei der Verdampfung wird ein Material erhitzt, bis es verdampft, während beim Sputtern energiereiche Ionen verwendet werden, um Atome aus einem Zielmaterial herauszuschlagen.Diese Unterschiede führen zu Variationen bei den Abscheideraten, der Schichtqualität, der Skalierbarkeit und der Eignung für bestimmte Anwendungen.Im Folgenden werden diese Unterschiede im Detail erläutert.
Die wichtigsten Punkte werden erklärt:
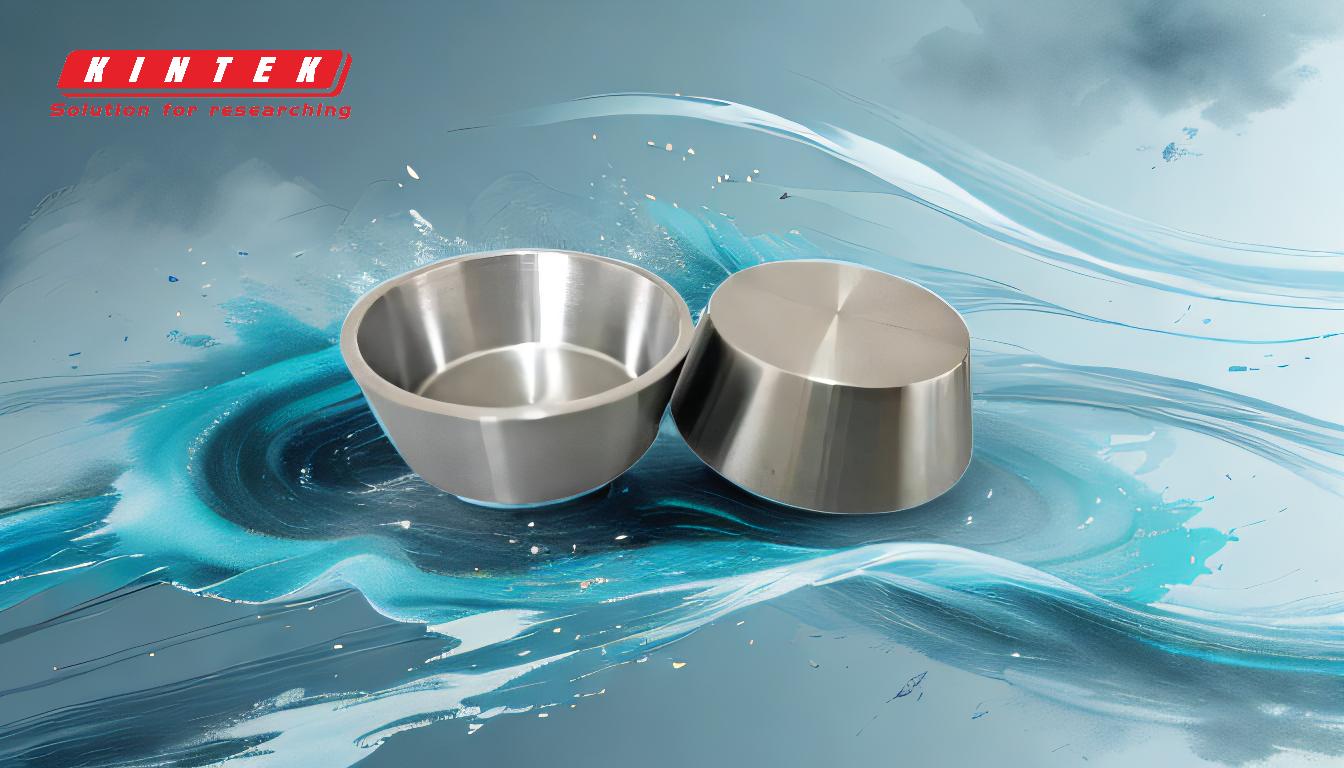
-
Mechanismus der Materialverdampfung:
-
Verdampfung:
- Nutzt thermische Energie (z. B. Widerstandsheizung oder Elektronenstrahl), um das Ausgangsmaterial zu erhitzen, bis es seine Verdampfungstemperatur erreicht.
- Erzeugt einen robusten Dampfstrom, der höhere Abscheideraten ermöglicht.
- Arbeitet in einer Hochvakuumumgebung zur Minimierung von Gasphasenkollisionen.
-
Sputtern:
- Beschuss eines Zielmaterials mit energiereichen Ionen (in der Regel Argon) in einer Plasmaumgebung.
- Dabei werden einzelne Atome oder kleine Cluster aus dem Zielmaterial herausgeschleudert.
- Arbeitet bei höheren Gasdrücken (5-15 mTorr), bei denen die gesputterten Partikel Gasphasenkollisionen ausgesetzt sind, bevor sie das Substrat erreichen.
-
Verdampfung:
-
Abscheiderate und Wirkungsgrad:
-
Verdampfung:
- Hat in der Regel eine höhere Abscheiderate im Vergleich zum Sputtern, insbesondere bei Hochtemperaturmaterialien.
- Kürzere Laufzeiten aufgrund des robusten Dampfstroms.
-
Sputtern:
- Hat im Allgemeinen eine geringere Abscheidungsrate, außer bei reinen Metallen.
- Langsameres Verfahren, bietet aber bessere Skalierbarkeit und Automatisierungsmöglichkeiten.
-
Verdampfung:
-
Filmqualität und Eigenschaften:
-
Verdampfung:
- Erzeugt Schichten mit größerer Korngröße und geringerer Homogenität.
- Geringere Haftung auf dem Substrat aufgrund der geringeren Energie der abgeschiedenen Stoffe.
- Weniger Gasabsorption in der Schicht, da im Hochvakuum gearbeitet wird.
-
Sputtern:
- Erzeugt Schichten mit kleineren Korngrößen und höherer Homogenität.
- Höhere Adhäsion aufgrund der höheren Energie der gesputterten Partikel.
- Mehr absorbiertes Gas in der Schicht, da sie mit höheren Gasdrücken arbeitet.
-
Verdampfung:
-
Betriebsbedingungen:
-
Verdampfung:
- Erfordert eine Hochvakuumumgebung, um minimale Gasphasenkollisionen zu gewährleisten.
- Line-of-sight-Abscheidung, d. h. das Substrat muss dem Dampfstrom direkt ausgesetzt sein.
-
Sputtern:
- Wird bei niedrigerem Vakuum (höherem Gasdruck) betrieben.
- Die Abscheidung ist aufgrund von Gasphasenkollisionen weniger gerichtet und ermöglicht eine bessere Abdeckung komplexer Geometrien.
-
Verdampfung:
-
Vielseitigkeit der Materialien:
-
Verdunstung:
- Geeignet für Materialien, die hohen Temperaturen standhalten können, ohne sich zu zersetzen.
- Es können Legierungen durch gemeinsames Verdampfen mehrerer Materialien hergestellt werden.
-
Sputtern:
- Es kann ein breiteres Spektrum von Materialien abgeschieden werden, einschließlich solcher mit hohem Schmelzpunkt oder solcher, die sich bei Erhitzung zersetzen.
- Je nach Konfiguration der Beschichtungsanlage können sequenzielle Beschichtungen durchgeführt werden.
-
Verdunstung:
-
Anwendungen:
-
Aufdampfen:
- Ideal für Anwendungen, die hohe Abscheideraten und einfache Geometrien erfordern, wie z. B. optische Beschichtungen und einige Halbleiteranwendungen.
-
Sputtern:
- Besser geeignet für Anwendungen, die eine hohe Schichtqualität, Haftung und Abdeckung komplexer Formen erfordern, wie z. B. Mikroelektronik, dekorative Beschichtungen und verschleißfeste Beschichtungen.
-
Aufdampfen:
-
Skalierbarkeit und Automatisierung:
-
Verdampfung:
- Weniger skalierbar, da Hochvakuumbedingungen und Sichtverbindung erforderlich sind.
-
Sputtern:
- Hochgradig skalierbar und automatisierbar für die Produktion in großem Maßstab, was es für industrielle Anwendungen geeignet macht.
-
Verdampfung:
Zusammenfassend lässt sich sagen, dass sowohl das Verdampfen als auch das Sputtern wirksame PVD-Verfahren sind, die sich jedoch aufgrund ihrer Mechanismen, Betriebsbedingungen und resultierenden Schichteigenschaften für unterschiedliche Anwendungen eignen.Die Verdampfung zeichnet sich durch hohe Abscheideraten und Einfachheit aus, während das Sputtern eine bessere Schichtqualität, Haftung und Skalierbarkeit bietet.Das Verständnis dieser Unterschiede ist entscheidend für die Auswahl der geeigneten Technik für bestimmte Anforderungen bei der Abscheidung von Dünnschichten.
Zusammenfassende Tabelle:
Blickwinkel | Verdampfung | Sputtern |
---|---|---|
Mechanismus | Thermische Energie erhitzt Material zum Verdampfen. | Energetische Ionen schlagen Atome aus einem Zielmaterial heraus. |
Abscheiderate | Höher, insbesondere bei Hochtemperaturwerkstoffen. | Niedriger, außer bei reinen Metallen. |
Filmqualität | Größere Korngrößen, weniger Homogenität, geringere Haftung. | Kleinere Korngrößen, höhere Homogenität, bessere Haftung. |
Betriebliche Bedingungen | Hochvakuum, gerichtete Abscheidung. | Niedrigeres Vakuum, weniger gerichtete Abscheidung. |
Vielseitigkeit der Materialien | Begrenzt auf hochtemperaturbeständige Materialien. | Breiteres Spektrum, einschließlich hochschmelzender Materialien. |
Anwendungen | Optische Beschichtungen, einfache Geometrien. | Mikroelektronik, komplexe Formen, verschleißfeste Beschichtungen. |
Skalierbarkeit | Weniger skalierbar aufgrund des hohen Vakuums und der Anforderungen an die Sichtverbindung. | Hochgradig skalierbar und automatisierbar für den industriellen Einsatz. |
Benötigen Sie Hilfe bei der Auswahl des richtigen PVD-Verfahrens für Ihre Anwendung? Kontaktieren Sie noch heute unsere Experten !