Physical Vapour Deposition (PVD) und Chemical Vapour Deposition (CVD) sind zwei weit verbreitete Techniken zum Aufbringen dünner Filme und Beschichtungen auf Substrate. Obwohl beide Methoden darauf abzielen, qualitativ hochwertige Beschichtungen zu erzeugen, unterscheiden sie sich erheblich in ihren Mechanismen, Materialien und Anwendungen. PVD beruht auf physikalischen Prozessen wie Verdampfen oder Sputtern, um feste Materialien auf einem Substrat abzuscheiden, während CVD chemische Reaktionen zwischen gasförmigen Vorläufern und dem Substrat beinhaltet, um eine feste Beschichtung zu bilden. Die Wahl zwischen PVD und CVD hängt von Faktoren wie den gewünschten Beschichtungseigenschaften, der Substratkompatibilität und den Verarbeitungsbedingungen ab.
Wichtige Punkte erklärt:
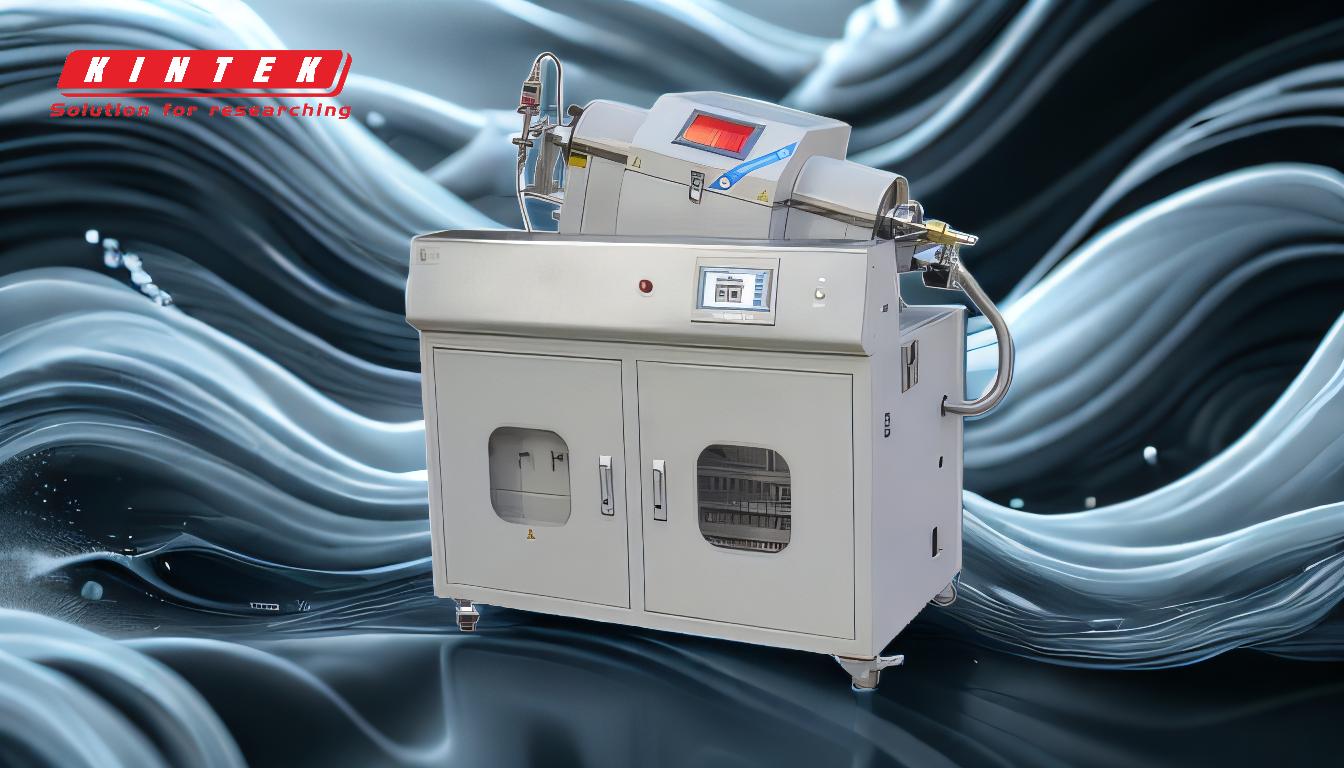
-
Mechanismus der Ablagerung:
- PVD: PVD ist ein physikalischer Prozess, bei dem feste Materialien verdampft werden (durch Verdampfen, Sputtern oder Sublimation) und dann auf einem Substrat abgeschieden werden. Der Prozess ist ein Sichtlinienprozess, d. h. das Material gelangt direkt von der Quelle zum Substrat.
- CVD: CVD ist ein chemischer Prozess, bei dem gasförmige Vorläufer auf einem erhitzten Substrat reagieren oder sich zersetzen, um eine feste Beschichtung zu bilden. Der Prozess ist multidirektional und ermöglicht eine gleichmäßige Abdeckung auch komplexer Geometrien.
-
Materialquellen:
- PVD: Verwendet feste Materialien (Targets), die verdampft werden, um die Beschichtung zu erzeugen. Zu den gängigen Techniken gehören Sputtern und Verdampfen.
- CVD: Verwendet gasförmige Vorläufer, die auf der Substratoberfläche chemisch reagieren, um die Beschichtung zu bilden. Bei den gasförmigen Vorläufern handelt es sich häufig um flüchtige Verbindungen, die das gewünschte Beschichtungsmaterial enthalten.
-
Temperaturanforderungen:
- PVD: Wird im Vergleich zu CVD typischerweise bei niedrigeren Temperaturen betrieben. Dadurch eignet sich PVD für temperaturempfindliche Substrate.
- CVD: Erfordert hohe Temperaturen (500 °C–1100 °C), um die für die Abscheidung erforderlichen chemischen Reaktionen zu ermöglichen. Dies schränkt den Einsatz auf Untergründen ein, die hohen Temperaturen nicht standhalten.
-
Ablagerungsraten:
- PVD: Im Allgemeinen sind die Ablagerungsraten geringer als bei CVD. Allerdings können Techniken wie Elektronenstrahl-PVD (EBPVD) hohe Abscheidungsraten (0,1 bis 100 μm/min) bei relativ niedrigen Substrattemperaturen erreichen.
- CVD: Bietet aufgrund der beteiligten chemischen Reaktionen höhere Abscheidungsraten, diese können jedoch je nach spezifischem CVD-Verfahren und verwendeten Materialien variieren.
-
Beschichtungseigenschaften:
- PVD: Erzeugt dichte, hochreine Beschichtungen mit hervorragender Haftung. Die Sichtlinienbeschaffenheit von PVD kann bei komplexen Formen zu einer ungleichmäßigen Abdeckung führen.
- CVD: Bietet gleichmäßige Beschichtungen mit ausgezeichneter Konformität und eignet sich daher ideal für die Beschichtung komplexer Geometrien. Allerdings können CVD-Beschichtungen aufgrund der beteiligten chemischen Reaktionen Verunreinigungen enthalten.
-
Anwendungen:
- PVD: Wird häufig für dekorative Beschichtungen, verschleißfeste Beschichtungen und optische Filme verwendet. Es wird auch in der Halbleiterfertigung zur Abscheidung dünner Schichten verwendet.
- CVD: Wird in der Halbleiterindustrie häufig zur Abscheidung dielektrischer Schichten, leitender Schichten und Schutzbeschichtungen verwendet. Es wird auch zur Herstellung harter Beschichtungen wie diamantähnlicher Kohlenstofffilme (DLC) verwendet.
-
Umwelt- und Sicherheitsaspekte:
- PVD: Gilt allgemein als sicherer und umweltfreundlicher, da keine gefährlichen chemischen Reaktionen oder korrosiven Nebenprodukte auftreten.
- CVD: Kann ätzende oder giftige Nebenprodukte erzeugen, die eine sorgfältige Handhabung und Entsorgung erfordern. Die hohen Temperaturen bergen auch Sicherheitsrisiken.
-
Effizienz der Materialnutzung:
- PVD: Aufgrund der Sichtlinienbeschaffenheit des Prozesses ist die Materialausnutzungseffizienz normalerweise geringer. Techniken wie EBPVD bieten jedoch eine hohe Materialausnutzung.
- CVD: Bietet eine hohe Materialausnutzungseffizienz, da die gasförmigen Vorläufer vollständig reagieren und sich auf dem Substrat ablagern können.
Zusammenfassend lässt sich sagen, dass sich PVD und CVD in ihren Mechanismen, Materialien und Anwendungen unterscheiden. PVD ist ideal für temperaturempfindliche Substrate und Anwendungen, die hochreine Beschichtungen erfordern, während CVD sich bei der Beschichtung komplexer Geometrien und der Erzielung hoher Abscheidungsraten auszeichnet. Die Wahl zwischen beiden hängt von den spezifischen Anforderungen der Anwendung ab, einschließlich der Substratkompatibilität, den gewünschten Beschichtungseigenschaften und den Verarbeitungsbedingungen.
Übersichtstabelle:
Aspekt | PVD | CVD |
---|---|---|
Mechanismus | Physikalischer Prozess (Verdampfung, Sputtern) | Chemischer Prozess (Gasreaktionen) |
Materialquellen | Feste Materialien (Ziele) | Gasförmige Vorläufer |
Temperatur | Niedrigere Temperaturen (geeignet für empfindliche Untergründe) | Hohe Temperaturen (500°C–1100°C) |
Ablagerungsrate | Im Allgemeinen niedriger (außer EBPVD) | Höhere Ablagerungsraten |
Beschichtungseigenschaften | Dicht, hochrein, hervorragende Haftung | Gleichmäßig, ausgezeichnete Konformität, kann Verunreinigungen enthalten |
Anwendungen | Dekorative, verschleißfeste, optische Folien, Halbleiter | Halbleiter, dielektrische Schichten, Hartbeschichtungen (z. B. DLC) |
Umweltauswirkungen | Sicherer, weniger gefährliche Nebenprodukte | Kann giftige/ätzende Nebenprodukte erzeugen |
Materialeffizienz | Niedriger (Sichtlinie), außer EBPVD | Hoch (gasförmige Vorläufer reagieren vollständig) |
Benötigen Sie Hilfe bei der Auswahl der richtigen Abscheidungstechnik? Kontaktieren Sie noch heute unsere Experten für individuelle Beratung!