Physical Vapour Deposition (PVD) und Chemical Vapour Deposition (CVD) sind zwei unterschiedliche Dünnschichtabscheidungstechniken, die in verschiedenen Branchen eingesetzt werden. Obwohl beide Methoden darauf abzielen, dünne Filme auf Substraten abzuscheiden, unterscheiden sie sich erheblich in ihren Mechanismen, Prozessen und Ergebnissen. PVD beruht auf physikalischen Prozessen wie Verdampfen oder Sputtern, um Materialien zu verdampfen und abzuscheiden, typischerweise bei niedrigeren Temperaturen und ohne chemische Reaktionen. Im Gegensatz dazu beinhaltet CVD chemische Reaktionen zwischen gasförmigen Vorläufern und dem Substrat, die häufig höhere Temperaturen erfordern und komplexere Filme erzeugen. Die Wahl zwischen PVD und CVD hängt von Faktoren wie Abscheidungsrate, Substrattemperatur, Filmqualität und Anwendungsanforderungen ab.
Wichtige Punkte erklärt:
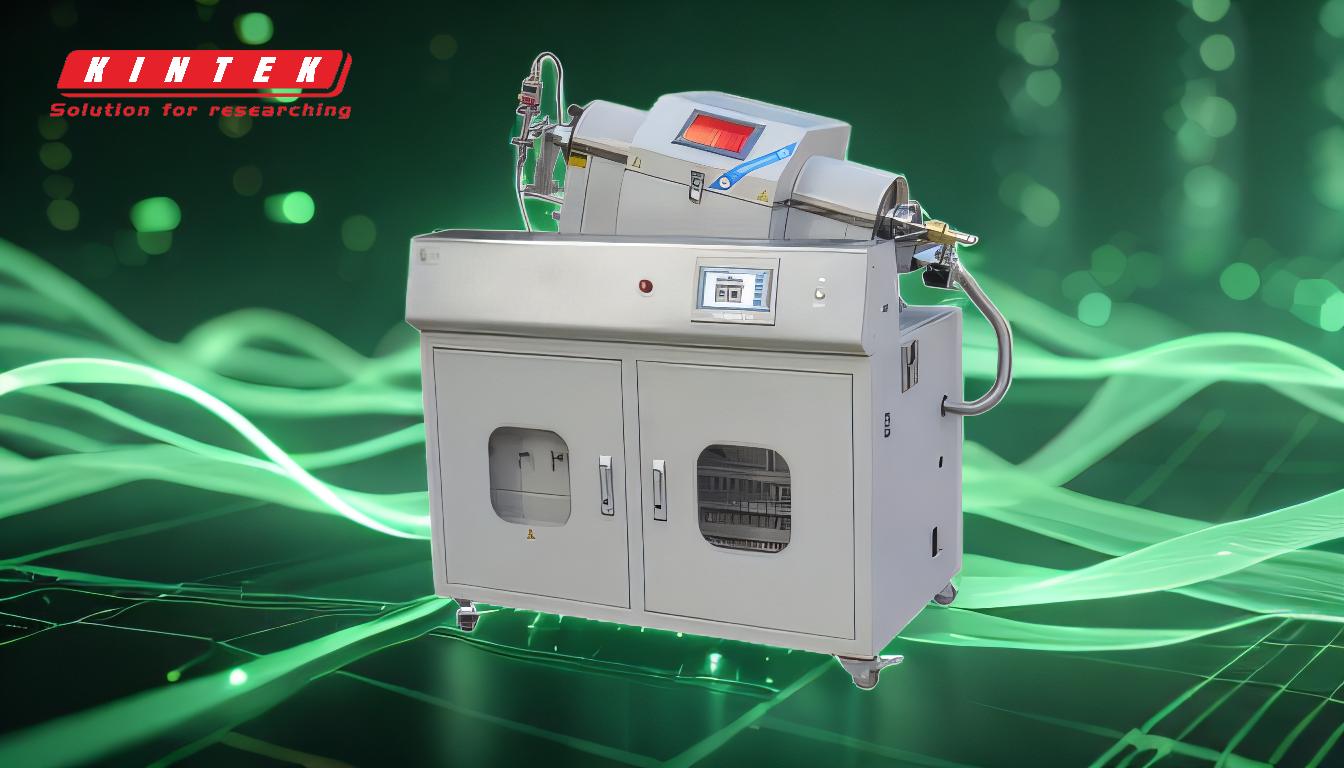
-
Ablagerungsmechanismus:
- PVD: Beim PVD wird das abzuscheidende Material durch Prozesse wie Verdampfen oder Sputtern physikalisch verdampft. Die verdampften Atome oder Moleküle kondensieren dann auf dem Substrat und bilden einen dünnen Film. Dieser Prozess beinhaltet keine chemischen Reaktionen.
- CVD: CVD beruht auf chemischen Reaktionen zwischen gasförmigen Vorläufern und dem Substrat. Die gasförmigen Moleküle reagieren auf der Substratoberfläche und bilden einen festen Film. Diese Methode erfordert oft höhere Temperaturen, um die chemischen Reaktionen zu erleichtern.
-
Temperaturanforderungen:
- PVD: PVD-Prozesse finden typischerweise bei niedrigeren Temperaturen statt, normalerweise zwischen 250 °C und 450 °C. Dadurch eignet sich PVD für Substrate, die hohen Temperaturen nicht standhalten.
- CVD: CVD-Prozesse erfordern im Allgemeinen höhere Temperaturen im Bereich von 450 °C bis 1050 °C. Diese erhöhten Temperaturen sind notwendig, um die bei der Filmbildung beteiligten chemischen Reaktionen zu aktivieren.
-
Ablagerungsrate:
- PVD: PVD weist im Vergleich zu CVD im Allgemeinen geringere Abscheidungsraten auf. Mit speziellen PVD-Techniken wie der Elektronenstrahl-Physikalischen Gasphasenabscheidung (EBPVD) können jedoch hohe Abscheidungsraten im Bereich von 0,1 bis 100 μm/min erzielt werden.
- CVD: CVD bietet typischerweise höhere Abscheidungsraten, was es für bestimmte Anwendungen effizienter macht, insbesondere wenn dicke Schichten erforderlich sind.
-
Filmqualität und Eigenschaften:
- PVD: PVD-Folien weisen häufig eine bessere Oberflächenglätte und Haftung auf. Das Fehlen chemischer Reaktionen bei PVD kann zu reineren Filmen mit weniger Verunreinigungen führen.
- CVD: CVD-Filme weisen tendenziell eine bessere Dichte und Abdeckung auf, insbesondere bei komplexen Geometrien. Durch die chemischen Reaktionen beim CVD können Filme mit ausgezeichneter Konformität und Gleichmäßigkeit erzeugt werden.
-
Effizienz der Materialnutzung:
- PVD: PVD-Verfahren, insbesondere EBPVD, sind für ihre hohe Materialausnutzungseffizienz bekannt. Dies bedeutet, dass ein erheblicher Teil des verdampften Materials auf dem Substrat abgelagert wird, wodurch der Abfall reduziert wird.
- CVD: CVD-Prozesse können aufgrund der Beteiligung gasförmiger Vorläufer und chemischer Reaktionen, die zur Bildung von Nebenprodukten und Verunreinigungen führen können, eine geringere Materialausnutzungseffizienz aufweisen.
-
Anwendungen:
- PVD: PVD wird häufig in Anwendungen eingesetzt, die hochreine Filme erfordern, wie etwa optische Beschichtungen, dekorative Beschichtungen und bestimmte elektronische Anwendungen. Aufgrund seiner Fähigkeit, Filme effizient auf große Substratflächen aufzutragen, wird es auch für die Massenproduktion bevorzugt.
- CVD: CVD wird in der Halbleiterindustrie häufig zur Herstellung organischer und anorganischer Filme auf Metallen, Halbleitern und anderen Materialien eingesetzt. Es wird auch bei der Herstellung von Beschichtungen für Verschleißfestigkeit, Korrosionsschutz und Wärmedämmung eingesetzt.
-
Umwelt- und Sicherheitsaspekte:
- PVD: PVD-Verfahren erzeugen im Allgemeinen weniger korrosive Nebenprodukte und gelten im Vergleich zu CVD als sicherer und umweltfreundlicher.
- CVD: CVD-Prozesse können korrosive gasförmige Nebenprodukte erzeugen und erfordern möglicherweise strengere Sicherheitsmaßnahmen und Abfallbewirtschaftungspraktiken.
Zusammenfassend lässt sich sagen, dass sowohl PVD als auch CVD zwar wertvolle Techniken zur Dünnschichtabscheidung sind, sie sich jedoch in ihren Mechanismen, Temperaturanforderungen, Abscheidungsraten, Filmeigenschaften und Anwendungen unterscheiden. Die Wahl zwischen PVD und CVD hängt von den spezifischen Anforderungen der Anwendung ab, einschließlich der gewünschten Filmeigenschaften, Substratkompatibilität und Produktionseffizienz.
Übersichtstabelle:
Aspekt | PVD | CVD |
---|---|---|
Ablagerungsmechanismus | Physikalische Prozesse (Verdampfen/Sputtern) ohne chemische Reaktionen. | Chemische Reaktionen zwischen gasförmigen Vorläufern und dem Substrat. |
Temperatur | Niedriger (250 °C bis 450 °C). | Höher (450°C bis 1050°C). |
Ablagerungsrate | Niedriger, aber EBPVD kann 0,1 bis 100 μm/min erreichen. | Höher, ideal für dicke Filme. |
Filmqualität | Bessere Oberflächenglätte und Haftung; weniger Verunreinigungen. | Bessere Dichte, Abdeckung und Konformität bei komplexen Geometrien. |
Materialeffizienz | Hohe Materialausnutzungseffizienz. | Niedriger aufgrund von Nebenprodukten und Verunreinigungen. |
Anwendungen | Optische Beschichtungen, dekorative Beschichtungen, Großserienfertigung. | Halbleiterfolien, Verschleißfestigkeit, Korrosionsschutzbeschichtungen. |
Umweltauswirkungen | Weniger korrosive Nebenprodukte; sicherer und umweltfreundlicher. | Erzeugt ätzende Nebenprodukte; erfordert strenge Sicherheitsmaßnahmen. |
Benötigen Sie Hilfe bei der Auswahl der richtigen Dünnschicht-Abscheidungstechnik? Kontaktieren Sie noch heute unsere Experten !