Sputtern und Aufdampfen sind zwei unterschiedliche Verfahren der physikalischen Gasphasenabscheidung (PVD), mit denen dünne Schichten auf Substraten erzeugt werden.Beide Verfahren zielen darauf ab, Materialien auf einer Oberfläche abzuscheiden, unterscheiden sich aber grundlegend in ihren Mechanismen, Betriebsbedingungen und Ergebnissen.Beim Sputtern stoßen energiereiche Ionen mit einem Zielmaterial zusammen und stoßen Atome aus, die sich dann auf einem Substrat ablagern.Im Gegensatz dazu wird bei der Verdampfung ein Material erhitzt, bis es verdampft und einen Dampfstrom bildet, der auf dem Substrat kondensiert.Diese Unterschiede führen zu Variationen bei den Abscheideraten, der Schichtqualität, der Skalierbarkeit und der Anwendungseignung.Das Verständnis dieser Unterschiede ist entscheidend für die Auswahl der geeigneten Technik für bestimmte Anwendungen.
Die wichtigsten Punkte werden erklärt:
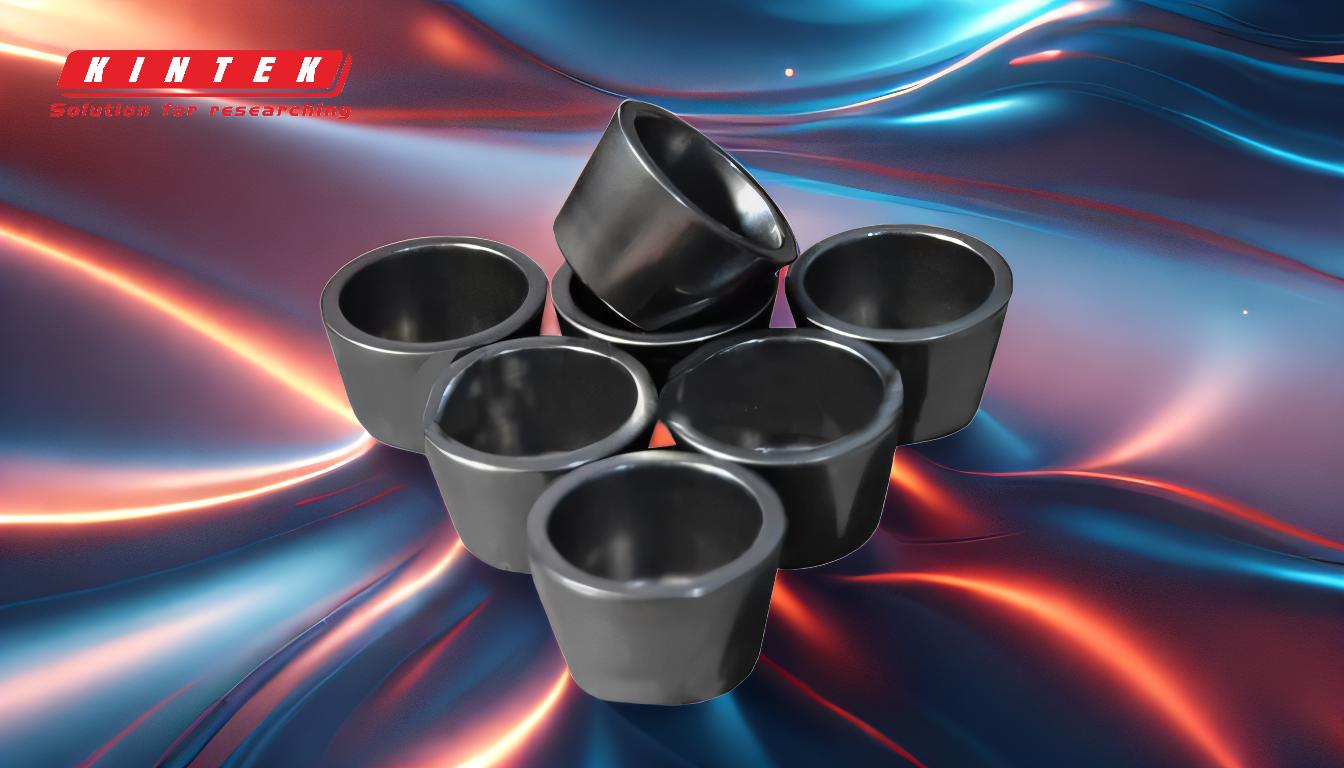
1. Mechanismus der Abscheidung
-
Sputtern:
- Beschuss eines Zielmaterials mit hochenergetischen Ionen (in der Regel Argon-Ionen) in einer Vakuumumgebung.
- Durch die Kollision werden Atome oder Cluster aus dem Target herausgeschleudert, die sich dann auf dem Substrat ablagern.
- Dieser Prozess ist nicht thermisch und beruht eher auf Impulsübertragung als auf Erhitzung.
-
Verdampfung:
- Nutzt thermische Energie, um das Ausgangsmaterial zu erhitzen, bis es seine Verdampfungstemperatur erreicht.
- Das verdampfte Material bildet einen Dampfstrom, der sich in einer Sichtlinie zum Substrat bewegt, wo er kondensiert.
- Zu den gängigen Verfahren gehört die Elektronenstrahlverdampfung, bei der ein Elektronenstrahl das Material erhitzt.
2. Betriebsbedingungen
-
Vakuumniveaus:
- Das Sputtern erfolgt bei relativ niedrigem Vakuum (5-15 mTorr), was Gasphasenkollisionen ermöglicht, die die gesputterten Partikel thermisch aufladen.
- Die Verdampfung erfordert eine Hochvakuumumgebung, um Gasphasenkollisionen zu minimieren und einen direkten Dampfstrom zu gewährleisten.
-
Abscheidungsrate:
- Die Verdampfung hat im Allgemeinen eine höhere Abscheidungsrate und eignet sich daher für Anwendungen, die dicke Schichten in kurzer Zeit erfordern.
- Das Sputtern hat eine geringere Abscheidungsrate, außer bei reinen Metallen, bietet aber eine bessere Kontrolle über die Schichtdicke und Gleichmäßigkeit.
3. Eigenschaften des Films
-
Haftvermögen:
- Sputtern bietet eine bessere Haftung aufgrund der höheren Energie der abgeschiedenen Partikel, was die Verbindung mit dem Substrat verbessert.
- Verdampfungsschichten können eine geringere Haftung aufweisen, insbesondere bei Materialien mit hohem Schmelzpunkt.
-
Filmhomogenität und Korngröße:
- Durch Sputtern werden Schichten mit kleineren Korngrößen und besserer Homogenität erzeugt, was sie ideal für Anwendungen macht, die eine genaue Kontrolle der Schichteigenschaften erfordern.
- Das Aufdampfen führt tendenziell zu größeren Korngrößen und weniger Homogenität, was für weniger anspruchsvolle Anwendungen akzeptabel sein kann.
4. Skalierbarkeit und Automatisierung
-
Sputtern:
- Hochgradig skalierbar und automatisierbar für die Produktion in großem Maßstab, daher geeignet für industrielle Anwendungen wie die Halbleiterherstellung.
- Die Möglichkeit, Materialien von oben (von oben nach unten) abzuscheiden, sorgt für mehr Flexibilität bei der Platzierung und Handhabung der Substrate.
-
Verdampfung:
- Weniger skalierbar, da ein Hochvakuum und eine präzise thermische Kontrolle erforderlich sind.
- In der Regel auf die Abscheidung von unten nach oben beschränkt, was die Ausrichtung und Handhabung des Substrats einschränken kann.
5. Energie der abgeschiedenen Spezies
-
Sputtern:
- Die abgeschiedenen Partikel haben eine höhere Energie, was die Filmdichte und Haftung verbessert.
- Diese hohe Energie verringert auch die Wahrscheinlichkeit von Defekten und verbessert die Filmqualität.
-
Verdampfung:
- Die abgeschiedenen Partikel haben eine geringere Energie, was zu weniger dichten Schichten und geringerer Haftung führen kann.
- Dies kann jedoch bei der Abscheidung empfindlicher oder hitzeempfindlicher Materialien von Vorteil sein.
6. Anwendungen
-
Sputtern:
- Wird häufig bei Anwendungen eingesetzt, die hochwertige, gleichmäßige Schichten erfordern, z. B. bei optischen Beschichtungen, Halbleitergeräten und magnetischen Speichermedien.
- Geeignet für die Abscheidung einer breiten Palette von Materialien, einschließlich Metallen, Legierungen und Keramiken.
-
Verdampfung:
- Ideal für Anwendungen, die hohe Abscheideraten und dicke Schichten erfordern, wie z. B. dekorative Beschichtungen, Solarpaneele und bestimmte elektronische Komponenten.
- Am besten geeignet für Materialien mit niedrigerem Schmelzpunkt und weniger strengen Anforderungen an die Folienqualität.
7. Absorbiertes Gas und Verunreinigung
-
Sputtern:
- Höhere Wahrscheinlichkeit der Gasabsorption aufgrund des Vorhandenseins von Sputtergas (z. B. Argon) in der Kammer.
- Dies kann die Reinheit des Films beeinträchtigen und zusätzliche Schritte zur Minimierung der Kontamination erfordern.
-
Verdampfung:
- Geringere Gasabsorption aufgrund der Hochvakuumumgebung, was zu reineren Filmen führt.
- Dennoch kann es zu Verunreinigungen kommen, wenn das Ausgangsmaterial unrein ist oder das Vakuum beeinträchtigt ist.
8. Direktionalität der Abscheidung
-
Sputtern:
- Die Partikel sind dispergierter und gerichteter, was eine bessere Abdeckung komplexer Geometrien und unebener Oberflächen ermöglicht.
- Dadurch eignet sich das Sputtern für die Beschichtung von Substraten mit komplizierten Formen oder hohen Aspektverhältnissen.
-
Verdampfung:
- Die Partikel folgen einer Sichtlinie, was die Erfassung komplexer oder vertiefter Oberflächen einschränken kann.
- Diese Methode ist besser für flache oder einfache Geometrien geeignet.
9. Kosten und Komplexität
-
Sputtern:
- Im Allgemeinen teurer, da spezielle Geräte wie Ionenquellen und Magnetfelder benötigt werden.
- Das Verfahren ist komplexer und erfordert eine genaue Kontrolle der Ionenenergie und der Eigenschaften des Zielmaterials.
-
Verdampfung:
- In der Regel preiswerter und einfacher einzurichten, insbesondere für Anwendungen im kleinen Maßstab oder in der Forschung.
- Allerdings können die Kosten für Systeme mit hoher Reinheit oder hohem Durchsatz steigen.
Zusammenfassend lässt sich sagen, dass die Wahl zwischen Sputtern und Verdampfen von den spezifischen Anforderungen der Anwendung abhängt, einschließlich Schichtqualität, Abscheiderate, Substratgeometrie und Budget.Das Sputtern bietet eine hervorragende Schichtqualität und Skalierbarkeit und ist daher ideal für Hochleistungsanwendungen, während das Aufdampfen schnellere Abscheidungsraten und Einfachheit bietet und sich für weniger anspruchsvolle oder durchsatzstarke Aufgaben eignet.
Zusammenfassende Tabelle:
Blickwinkel | Sputtern | Verdampfung |
---|---|---|
Mechanismus | Beschießt das Ziel mit Ionen und stößt Atome für die Abscheidung aus | Erhitzt Material zum Verdampfen und bildet einen Dampfstrom für die Abscheidung |
Vakuumniveaus | Niedriges Vakuum (5-15 mTorr) | Hochvakuum |
Abscheiderate | Geringer (außer bei reinen Metallen) | Höher |
Adhäsion | Bessere Haftung durch Partikel mit höherer Energie | Geringere Adhäsion, insbesondere bei hochschmelzenden Materialien |
Homogenität des Films | Kleinere Korngrößen, bessere Homogenität | Größere Korngrößen, weniger Homogenität |
Skalierbarkeit | Hochgradig skalierbar, geeignet für industrielle Anwendungen | Weniger skalierbar, begrenzt durch Vakuum und thermische Kontrolle |
Energie der Partikel | Höhere Energie, dichtere Filme, weniger Defekte | Niedrigere Energie, weniger dichte Filme |
Anwendungen | Optische Beschichtungen, Halbleiter, Magnetspeicher | Dekorative Beschichtungen, Sonnenkollektoren, bestimmte Elektronik |
Kosten | Teurer, komplexer Aufbau | Weniger teuer, einfachere Einrichtung |
Benötigen Sie Hilfe bei der Auswahl des richtigen PVD-Verfahrens für Ihre Anwendung? Kontaktieren Sie noch heute unsere Experten für eine persönliche Beratung!