Die Auswirkung der Frequenz auf das Induktionshärten ist erheblich und beeinflusst direkt die Tiefe und Effizienz des Härteprozesses.Höhere Frequenzen führen zu einem größeren Stromdichteunterschied zwischen der Oberfläche und dem Inneren des Werkstücks, was zu einer dünneren Heizschicht führt.Dies ermöglicht eine präzise Steuerung der Härtetiefe und ist daher ideal für Anwendungen, die eine geringe Härtetiefe erfordern.Wenn die Oberflächentemperatur den kritischen Punkt des Stahls überschreitet, kann eine schnelle Abkühlung erfolgen, um die gewünschte Oberflächenhärte zu erreichen.Diese Beziehung zwischen Frequenz und Härtetiefe ist entscheidend für die Auswahl der geeigneten Induktionserwärmungsparameter für bestimmte Anwendungen.
Die wichtigsten Punkte werden erklärt:
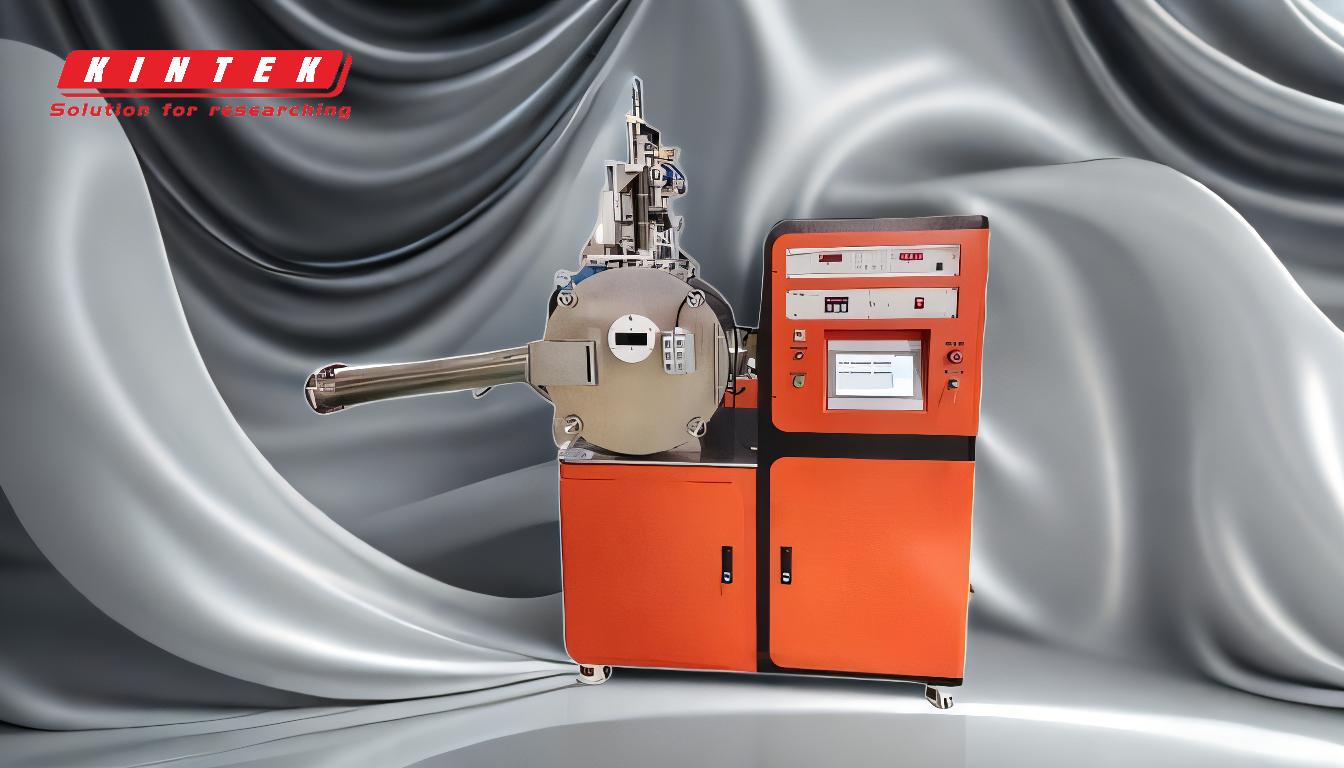
-
Beziehung zwischen Frequenz und Stromdichte:
- Höhere Frequenzen bewirken eine größere Stromkonzentration in der Nähe der Oberfläche des Werkstücks, ein Phänomen, das als Skin-Effekt bekannt ist.
- Dies führt zu einer höheren Stromdichte an der Oberfläche im Vergleich zum Inneren, was sich direkt auf die Tiefe der Erwärmung auswirkt.
-
Auswirkung auf die Heizschichtdicke:
- Mit steigender Frequenz wird die Heizschicht dünner, da der Strom näher an der Oberfläche konzentriert wird.
- Dies ermöglicht eine präzise Steuerung der Härtetiefe, was besonders bei Anwendungen nützlich ist, die eine geringe Härtetiefe erfordern, z. B. bei Zahnrädern oder Lagern.
-
Kritische Temperatur und schnelle Abkühlung:
- Die Heizschicht muss eine Temperatur oberhalb des kritischen Punkts des Stahls erreichen, um eine Phasenumwandlung (z. B. Austenitisierung) zu ermöglichen.
- Sobald diese Temperatur erreicht ist, erfolgt eine rasche Abkühlung (Abschrecken), um das gehärtete Gefüge zu fixieren, was zu einer harten Oberflächenschicht führt.
-
Anwendungen und praktische Erwägungen:
- Das Hochfrequenz-Induktionshärten ist ideal für kleine oder dünne Bauteile, bei denen eine flache Härtung erforderlich ist.
- Niedrigere Frequenzen werden für größere Bauteile verwendet oder wenn eine tiefere Härtung erforderlich ist, da der Strom weiter in das Material eindringt.
-
Vorteile des Induktionshärtens mit höheren Frequenzen:
- Präzision:Ermöglicht die gezielte Härtung bestimmter Bereiche.
- Wirkungsgrad:Verringert die Energieverschwendung durch Konzentration der Wärme auf die Oberfläche.
- Schnelligkeit:Schnellere Heizzyklen durch konzentrierte Energie.
-
Beschränkungen und Kompromisse:
- Höhere Frequenzen sind möglicherweise nicht für Bauteile geeignet, die tief gehärtet werden müssen.
- Anlagen, die hohe Frequenzen erzeugen können, sind unter Umständen teurer und komplexer.
Wenn die Hersteller die Beziehung zwischen Frequenz und Induktionshärtung verstehen, können sie den Prozess optimieren, um die gewünschten Oberflächeneigenschaften für ihre spezifischen Anwendungen zu erzielen.Dieses Wissen ist wichtig für die Auswahl der richtigen Ausrüstung und Parameter, um gleichbleibende und hochwertige Ergebnisse zu gewährleisten.
Zusammenfassende Tabelle:
Aspekt | Einzelheiten |
---|---|
Frequenz und Stromdichte | Höhere Frequenzen erhöhen die Oberflächenstromdichte (Skin-Effekt). |
Dicke der Heizschicht | Höhere Frequenzen führen zu dünneren Heizschichten. |
Kritische Temperatur | Die Oberfläche muss den kritischen Punkt des Stahls für die Phasenumwandlung überschreiten. |
Anwendungen | Hochfrequenz: flaches Härten (Zahnräder, Lager).Niederfrequenz: Tiefhärten. |
Vorteile | Präzision, Effizienz und schnellere Heizzyklen. |
Beschränkungen | Nicht für das Tiefhärten geeignet; höhere Anlagenkosten. |
Optimieren Sie Ihren Induktionshärteprozess mit der richtigen Frequenz - Kontaktieren Sie unsere Experten noch heute !