Die Kalzinierungstemperatur spielt eine entscheidende Rolle bei der Bestimmung der strukturellen, chemischen und physikalischen Eigenschaften von Materialien.Sie beeinflusst die Phasenumwandlung, die Kristallinität, die Partikelgröße, die Porosität und die Oberfläche, was sich wiederum auf die Leistung des Materials in verschiedenen Anwendungen auswirkt.Durch eine sorgfältige Steuerung der Kalzinierungstemperatur lassen sich die Materialeigenschaften für bestimmte Anwendungen optimieren, z. B. für die Katalyse, die Energiespeicherung oder für Keramiken.Zu hohe Temperaturen können jedoch zu unerwünschten Effekten wie Versinterung, Agglomeration oder Phasenzerfall führen.Die Kenntnis des Einflusses der Kalzinierungstemperatur ist von entscheidender Bedeutung für die Anpassung von Werkstoffen an spezifische funktionale Anforderungen.
Die wichtigsten Punkte werden erklärt:
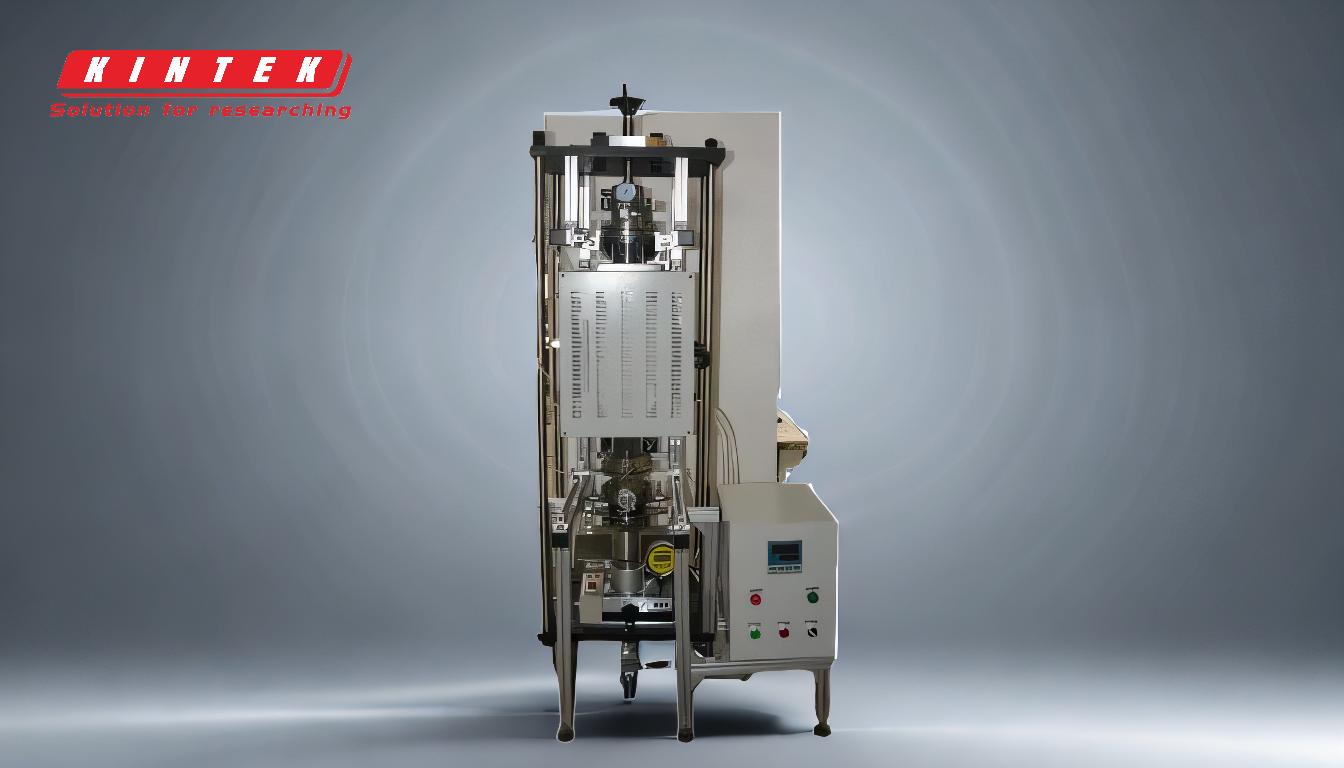
-
Phasenumwandlung und Kristallinität:
- Erläuterung: Die Kalzinierungstemperatur wirkt sich direkt auf die Phasenzusammensetzung und Kristallinität der Materialien aus.Bei niedrigeren Temperaturen können die Materialien amorph oder teilkristallin bleiben.Mit steigender Temperatur kommt es zu Phasenübergängen, die zur Bildung stabilerer kristalliner Phasen führen.Bei der Herstellung von Keramik beispielsweise kann das Kalzinieren bei höheren Temperaturen die Bildung der gewünschten kristallinen Phasen wie Aluminiumoxid oder Zirkoniumdioxid fördern.
- Auswirkungen: Die korrekte Steuerung der Kalzinierungstemperatur gewährleistet die Bildung der gewünschten Phase, die für die Erzielung optimaler mechanischer, thermischer und chemischer Eigenschaften entscheidend ist.
-
Partikelgröße und Morphologie:
- Erläuterung: Die Kalzinierungstemperatur beeinflusst das Wachstum der Partikel.Bei mäßigen Temperaturen können die Partikel leicht wachsen, wodurch sich die Kristallinität ohne nennenswerte Agglomeration verbessert.Bei zu hohen Temperaturen können die Partikel jedoch versintern oder miteinander verschmelzen, was zu größeren Partikeln und einer geringeren Oberfläche führt.
- Auswirkungen: Kleinere Partikelgrößen und eine kontrollierte Morphologie sind häufig für Anwendungen wie die Katalyse wünschenswert, wo eine große Oberfläche die Reaktivität verbessert.Übermäßiges Partikelwachstum kann die Leistung verringern.
-
Porosität und Oberfläche:
- Erläuterung: Die Kalzinierungstemperatur beeinflusst die Porosität und die Oberfläche von Materialien.Bei niedrigeren Temperaturen können eine größere Oberfläche und Porosität erhalten bleiben, was für Anwendungen wie Adsorption oder Katalyse von Vorteil ist.Höhere Temperaturen können zum Zusammenbruch oder zur Verdichtung der Poren führen, wodurch sich die Oberfläche verkleinert.
- Auswirkungen: Die Anpassung der Kalzinierungstemperatur ermöglicht die Optimierung von Porosität und Oberfläche, die für Anwendungen, die eine hohe Reaktivität oder Adsorptionskapazität erfordern, entscheidend sind.
-
Chemische Stabilität und Zersetzung:
- Erläuterung: Einige Materialien werden bei bestimmten Temperaturen chemisch zersetzt oder verändern ihre Phase.So zerfallen beispielsweise Metallhydroxide oder Karbonate beim Kalzinieren in Oxide.Die Temperatur muss sorgfältig kontrolliert werden, um eine vollständige Zersetzung zu gewährleisten, ohne das Material zu zersetzen.
- Auswirkungen: Eine ordnungsgemäße Kalzinierung gewährleistet die Bildung stabiler, hochreiner Phasen, die für Anwendungen in der Elektronik, Energiespeicherung oder Katalyse unerlässlich sind.
-
Sinterung und Agglomeration:
- Erläuterung: Bei sehr hohen Temperaturen kann es zu einer Sinterung kommen, bei der die Partikel miteinander verschmelzen, wodurch sich die Oberfläche und die Porosität verringern.Die Agglomeration kann auch zu einer ungleichmäßigen Partikelgrößenverteilung führen.
- Auswirkungen: Sinterung und Agglomeration können sich negativ auf die Materialleistung auswirken, insbesondere bei Anwendungen, die eine große Oberfläche oder eine einheitliche Partikelgröße erfordern.
-
Thermische und mechanische Eigenschaften:
- Erläuterung: Die Kalzinierungstemperatur beeinflusst die thermischen und mechanischen Eigenschaften von Materialien.Höhere Temperaturen verbessern im Allgemeinen die mechanische Festigkeit und die thermische Stabilität, können aber auch zu Sprödigkeit führen.
- Auswirkungen: Das Verständnis des Gleichgewichts zwischen Temperatur und Materialeigenschaften ist für Anwendungen wie feuerfeste Materialien oder Strukturkeramiken von entscheidender Bedeutung.
-
Anwendungsspezifische Optimierung:
- Erläuterung: Verschiedene Anwendungen erfordern unterschiedliche Materialeigenschaften.So benötigen Katalysatoren beispielsweise eine große Oberfläche und Porosität, während Strukturkeramiken eine hohe Dichte und mechanische Festigkeit erfordern.
- Auswirkungen: Durch die Anpassung der Kalzinierungstemperatur können die Materialien für bestimmte Anwendungen optimiert werden, um maximale Leistung und Effizienz zu gewährleisten.
-
Energieeffizienz und Kostenüberlegungen:
- Erläuterung: Höhere Kalzinierungstemperaturen erfordern mehr Energie und erhöhen die Produktionskosten.Für eine kosteneffiziente Herstellung ist es wichtig, die Temperatur mit den gewünschten Materialeigenschaften in Einklang zu bringen.
- Auswirkungen: Die Optimierung der Kalzinierungstemperatur kann den Energieverbrauch und die Produktionskosten senken und gleichzeitig die gewünschten Materialeigenschaften erzielen.
Durch das Verständnis und die Kontrolle des Einflusses der Kalzinierungstemperatur können Hersteller und Forscher Werkstoffe auf spezifische funktionale Anforderungen zuschneiden und so eine optimale Leistung in einem breiten Spektrum von Anwendungen sicherstellen.
Zusammenfassende Tabelle:
Aspekt | Auswirkung |
---|---|
Phasenumwandlung | Bestimmt die Kristallinität und Phasenstabilität für die gewünschten Materialeigenschaften. |
Partikelgröße und Morphologie | Steuert das Partikelwachstum und die Oberfläche für verbesserte Reaktivität oder Festigkeit. |
Porosität und Oberfläche | Optimiert die Porosität für hohe Reaktivität oder Adsorptionskapazität. |
Chemische Stabilität | Gewährleistet eine vollständige Zersetzung ohne Beeinträchtigung der Materialqualität. |
Sinterung und Agglomeration | Verhindert das Verschmelzen der Partikel und sorgt für eine einheitliche Größe und Oberfläche. |
Thermische und mechanische Eigenschaften | Ausgewogene Festigkeit, Stabilität und Sprödigkeit für spezifische Anwendungen. |
Anwendungsspezifische Optimierung | Maßgeschneiderte Materialien für Katalyse, Keramik oder Energiespeicherung. |
Energie-Effizienz | Reduziert den Energieverbrauch und die Produktionskosten und erzielt gleichzeitig die gewünschten Eigenschaften. |
Benötigen Sie Hilfe bei der Optimierung der Kalzinierungstemperatur für Ihre Materialien? Kontaktieren Sie noch heute unsere Experten !