Das PVD-Beschichtungsverfahren (Physical Vapor Deposition) ist eine hochentwickelte Methode zur Herstellung dünner, haltbarer und funktioneller Beschichtungen auf verschiedenen Substraten.Dabei wird ein festes Material in einer Vakuumumgebung verdampft, die verdampften Atome werden zum Substrat transportiert und dort zu einem dünnen Film abgeschieden.Dieses Verfahren verbessert die Eigenschaften des Substrats, wie z. B. Härte, Verschleißfestigkeit und Korrosionsbeständigkeit, und verbessert gleichzeitig sein ästhetisches Erscheinungsbild.Der Mechanismus der PVD-Beschichtung kann in mehrere wichtige Schritte unterteilt werden, darunter Reinigung, Verdampfung, Transport, Reaktion und Abscheidung.Jeder Schritt ist entscheidend für die Qualität und Leistung der endgültigen Beschichtung.
Die wichtigsten Punkte werden erklärt:
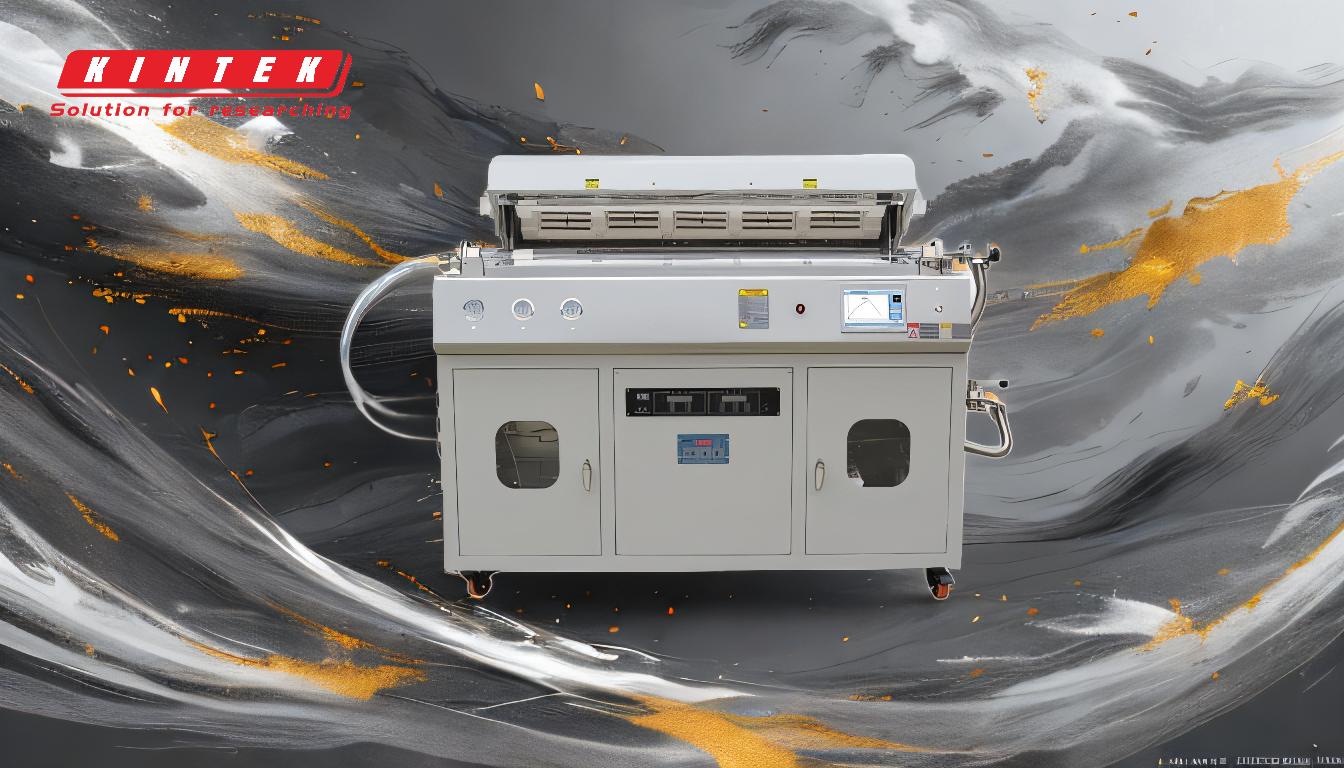
-
Reinigung und Vorbehandlung des Substrats:
- Bevor der PVD-Beschichtungsprozess beginnt, muss das Substrat gründlich gereinigt werden, um alle Verunreinigungen wie Öle, Staub oder Oxide zu entfernen.Dies ist von entscheidender Bedeutung, da Verunreinigungen auf der Oberfläche die Haftung und Qualität der Beschichtung negativ beeinflussen können.
- Vorbehandlungsverfahren wie Plasmareinigung oder Ätzen können ebenfalls eingesetzt werden, um die Oberflächenenergie und die Haftung der Beschichtung zu verbessern.Dieser Schritt stellt sicher, dass die Beschichtung effektiv auf dem Substrat haftet.
-
Schaffung einer Hochvakuum-Umgebung:
- Das PVD-Beschichtungsverfahren findet in einer Vakuumkammer statt, die auf einen extrem niedrigen Druck evakuiert ist, der üblicherweise im Bereich von 10^-3 bis 10^-9 Torr liegt.Diese Hochvakuumumgebung ist unerlässlich, um eine Verunreinigung durch atmosphärische Gase zu verhindern und um zu gewährleisten, dass das verdampfte Material ungehindert zum Substrat gelangen kann.
- Das Vakuum sorgt auch dafür, dass das verdampfte Material sauber und rein bleibt, was für die Erzielung hochwertiger Beschichtungen entscheidend ist.
-
Verdampfung des Zielmaterials:
- Das Targetmaterial, die Quelle der Beschichtung, wird mit einer von mehreren Techniken verdampft, z. B. durch Sputtern, Bogenverdampfung oder Elektronenstrahlverdampfung.Beim Sputtern wird das Target mit hochenergetischen Ionen beschossen, wodurch Atome von der Oberfläche abgelöst werden.Bei der Lichtbogenverdampfung verdampft ein elektrischer Lichtbogen das Targetmaterial, während bei der Elektronenstrahlverdampfung ein fokussierter Elektronenstrahl das Target erhitzt und verdampft.
- Die Wahl der Verdampfungstechnik hängt von dem zu beschichtenden Material und den gewünschten Eigenschaften der Beschichtung ab.
-
Transport der verdampften Atome:
- Sobald das Zielmaterial verdampft ist, werden die Atome oder Moleküle durch die Vakuumkammer zum Substrat transportiert.Dieser Transport erfolgt in einer geraden Linie, da in der Vakuumumgebung keine Luftmoleküle vorhanden sind.
- Der Abstand zwischen dem Target und dem Substrat sowie die Energie der verdampften Atome beeinflussen die Gleichmäßigkeit und Dicke der Beschichtung.
-
Reaktion mit reaktiven Gasen (optional):
- Während der Transportphase können reaktive Gase wie Stickstoff, Sauerstoff oder Acetylen in die Vakuumkammer eingeleitet werden.Diese Gase reagieren mit den verdampften Metallatomen und bilden Verbindungen wie Metallnitride, -oxide oder -carbide.
- Dieser Reaktionsschritt ist entscheidend für die Veränderung der Eigenschaften der Beschichtung.So kann die Zugabe von Stickstoff beispielsweise zur Bildung einer harten, verschleißfesten Metallnitridschicht führen.
-
Abscheidung und Kondensation auf dem Substrat:
- Die verdampften Atome oder Moleküle erreichen schließlich das Substrat, wo sie kondensieren und einen dünnen, gleichmäßigen Film bilden.Diese Abscheidung erfolgt Atom für Atom, was zu einer sehr kontrollierten und präzisen Beschichtung führt.
- Der Abscheidungsprozess wird durch Faktoren wie die Substrattemperatur, die Energie der verdampften Atome und den Einfallswinkel der Atome auf das Substrat beeinflusst.
-
Qualitätskontrolle und Endbearbeitung:
- Nach dem Auftragen der Beschichtung wird durch Qualitätskontrollen sichergestellt, dass die Beschichtung den erforderlichen Spezifikationen entspricht.Dazu können Prüfungen der Schichtdicke, der Haftung, der Härte und anderer Eigenschaften gehören.
- Zur Verbesserung des Aussehens oder der Leistung der Beschichtung können auch Veredelungsverfahren wie Polieren oder zusätzliche Oberflächenbehandlungen angewandt werden.
-
Ökologische und betriebliche Vorteile:
- Die PVD-Beschichtung gilt als umweltfreundliches Verfahren, da keine schädlichen Chemikalien eingesetzt werden und kein nennenswerter Abfall anfällt.Außerdem ist das Verfahren hocheffizient, mit minimalem Materialverlust.
- Die resultierenden Beschichtungen sind langlebig, verschleiß- und korrosionsbeständig und können auf spezifische funktionale oder ästhetische Anforderungen zugeschnitten werden.
Zusammenfassend lässt sich sagen, dass der Mechanismus der PVD-Beschichtung eine Reihe sorgfältig kontrollierter Schritte umfasst, die ein festes Zielmaterial in eine dünne Hochleistungsschicht auf einem Substrat verwandeln.Jeder Schritt, von der Reinigung und Verdampfung bis zur Abscheidung und Endbearbeitung, spielt eine entscheidende Rolle bei der Gewährleistung der Qualität und Funktionalität des Endprodukts.Das Verfahren ist äußerst vielseitig und ermöglicht die Herstellung von Beschichtungen mit einer breiten Palette von Eigenschaften, was es zu einer wertvollen Technik in Branchen wie der Automobilindustrie, der Luft- und Raumfahrt, der Medizintechnik und der Unterhaltungselektronik macht.
Zusammenfassende Tabelle:
Schritt | Beschreibung |
---|---|
Reinigung und Vorbehandlung | Entfernen Sie Verunreinigungen und verbessern Sie die Haftfähigkeit durch Reinigung und Oberflächenbehandlung. |
Hoch-Vakuum-Umgebung | Erzeugen Sie ein Vakuum, um Verunreinigungen zu vermeiden und sauberes, verdampftes Material zu gewährleisten. |
Verdampfung des Targets | Verdampfen des Targetmaterials durch Sputtern, Bogenverdampfung oder Elektronenstrahl. |
Transport von Atomen | Transportieren Sie verdampfte Atome in einer geraden Linie zum Substrat. |
Reaktion mit Gasen (optional) | Einführung reaktiver Gase zur Veränderung der Beschichtungseigenschaften (z. B. Härte). |
Abscheidung und Kondensation | Abscheidung von Atomen auf dem Substrat zur Bildung eines dünnen, gleichmäßigen Films. |
Qualitätskontrolle und Endbearbeitung | Testen und verbessern Sie die Beschichtungseigenschaften hinsichtlich Leistung und Aussehen. |
Vorteile für die Umwelt | Umweltfreundlich, effizient und erzeugt dauerhafte, maßgeschneiderte Beschichtungen. |
Erschließen Sie das Potenzial von PVD-Beschichtungen für Ihre Anwendungen. Kontaktieren Sie unsere Experten noch heute !