Die optimale Sintertemperatur hängt von dem zu verarbeitenden Material, den gewünschten Eigenschaften des Endprodukts und dem verwendeten Sinterverfahren ab.Im Allgemeinen liegen die Sintertemperaturen zwischen 70 % und 90 % des Schmelzpunkts des Materials.Für viele Materialien bedeutet dies Temperaturen zwischen 900°C und 1400°C.Zu den Schlüsselfaktoren, die die optimale Temperatur beeinflussen, gehören die Zusammensetzung des Materials, die Partikelgröße sowie die gewünschte Dichte und die mechanischen Eigenschaften des Endprodukts.Darüber hinaus spielen die Aufheiz- und Abkühlgeschwindigkeit sowie die atmosphärischen Bedingungen (z. B. Luft, Vakuum oder Inertgas) eine entscheidende Rolle für das Erreichen der besten Ergebnisse.Im Folgenden gehen wir auf diese Faktoren im Detail ein, um die optimale Sintertemperatur für verschiedene Anwendungen zu ermitteln.
Die wichtigsten Punkte erklärt:
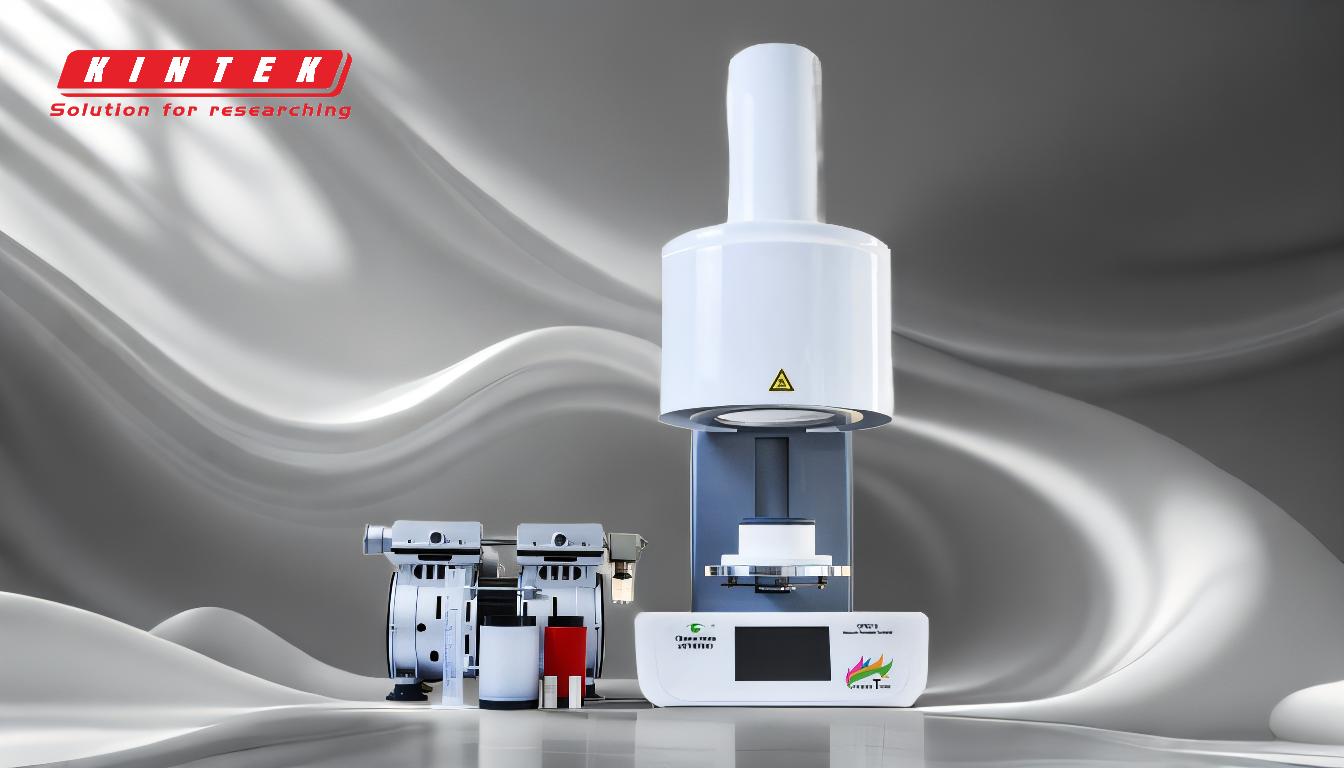
-
Werkstoffspezifische Sintertemperaturen:
-
Die optimale Sintertemperatur hängt stark von dem zu verarbeitenden Material ab.Zum Beispiel:
- Keramiken:Normalerweise bei 1200°C bis 1400°C gesintert.
- Metalle:Sie werden häufig bei 70 bis 90 % ihres Schmelzpunkts gesintert, der zwischen 900 und 1300 °C liegen kann.
- Polymere:Erfordern niedrigere Temperaturen, in der Regel unter 300°C.
- Die Wahl der Temperatur gewährleistet eine ordnungsgemäße Verdichtung, ohne dass es zu übermäßigem Kornwachstum oder Materialverschlechterung kommt.
-
Die optimale Sintertemperatur hängt stark von dem zu verarbeitenden Material ab.Zum Beispiel:
-
Einfluss der Partikelgröße:
- Feinere Pulver erfordern aufgrund ihrer höheren Oberflächenenergie im Allgemeinen niedrigere Sintertemperaturen, was eine schnellere Verdichtung fördert.
- Größere Partikel benötigen unter Umständen höhere Temperaturen, um den gleichen Verdichtungsgrad zu erreichen.
-
Aufheiz- und Abkühlraten:
- Heizrate:Eine kontrollierte Anstiegsgeschwindigkeit von 900°C bis zur Höchsttemperatur ist entscheidend, um einen Temperaturschock zu vermeiden und eine gleichmäßige Verdichtung zu gewährleisten.
- Abkühlungsrate:Eine schnelle Abkühlung kann zu Eigenspannungen führen, während eine langsame Abkühlung ein gleichmäßiges Mikrogefüge fördert.Die Abkühlungsgeschwindigkeit bis auf 900°C ist besonders wichtig, um die gewünschten mechanischen Eigenschaften zu erreichen.
-
Atmosphärische Bedingungen:
-
Die Sinteratmosphäre (z. B. Luft, Vakuum oder Inertgase wie Argon oder Stickstoff) beeinflusst die optimale Temperatur:
- Vakuum oder Inertgas:Verhindert Oxidation und ermöglicht höhere Temperaturen für eine bessere Verdichtung.
- Luft:Die Höchsttemperatur kann begrenzt werden, um eine Oxidation oder Zersetzung des Materials zu vermeiden.
-
Die Sinteratmosphäre (z. B. Luft, Vakuum oder Inertgase wie Argon oder Stickstoff) beeinflusst die optimale Temperatur:
-
Gewünschte Produkteigenschaften:
- Höhere Sintertemperaturen verbessern im Allgemeinen die Zugfestigkeit, die Biegewechselfestigkeit und die Kerbschlagarbeit.
- Überhöhte Temperaturen können jedoch zu Kornwachstum, verminderter Festigkeit und Instabilität der Abmessungen führen.
-
Prozess-Parameter:
- Schichtdicke:Bei dickeren Schichten (250-500 mm) können höhere Temperaturen erforderlich sein, um eine gleichmäßige Sinterung zu gewährleisten.
- Maschinengeschwindigkeit:Gesteuert mit 1,5-4m/min, um sicherzustellen, dass der Sintervorschub am geplanten Endpunkt verbrannt wird.
- Luftmenge und Vakuum:Ein angemessener Luftstrom (z.B. 3200m³ pro Tonne Sintererz) und ein angemessenes Vakuum sind für gleichbleibende Ergebnisse unerlässlich.
-
Praktische Überlegungen:
- Der Typ des Sinterofens (Förderband-, Stoß- oder Chargenofen) und seine Möglichkeiten beeinflussen den erreichbaren Temperaturbereich.
- Die Wahl des Verfahrens hängt von der Abwägung zwischen den gewünschten Produkteigenschaften und begrenzenden Parametern wie Anlagenbeschränkungen und Materialverhalten ab.
Zusammenfassend lässt sich sagen, dass die optimale Sintertemperatur kein fester Wert ist, sondern ein sorgfältig gewählter Parameter, der die Materialeigenschaften, die Prozessbedingungen und die gewünschten Ergebnisse in Einklang bringt.Durch die Berücksichtigung von Faktoren wie Materialzusammensetzung, Partikelgröße, Heiz- und Kühlraten, atmosphärische Bedingungen und Prozessparameter können Hersteller die beste Temperatur für ihre spezifische Anwendung bestimmen.
Zusammenfassende Tabelle:
Faktor | Einfluss auf die Sintertemperatur |
---|---|
Werkstoff | Keramiken: 1200°C-1400°C; Metalle:70%-90% des Schmelzpunkts (900°C-1300°C); Polymere:<300°C. |
Partikelgröße | Feinere Pulver:Niedrigere Temperaturen; Größere Partikel:Höhere Temperaturen. |
Aufheiz-/Abkühlraten | Kontrolliertes Erhitzen vermeidet thermische Schocks; langsames Abkühlen fördert das Gleichgewicht der Mikrostrukturen. |
Atmosphäre | Vakuum/Inertgas:Höhere Temperaturen; Luft:Begrenzt, um Oxidation zu vermeiden. |
Gewünschte Eigenschaften | Höhere Temperaturen verbessern die Festigkeit, bergen aber die Gefahr des Kornwachstums; das Gleichgewicht ist entscheidend. |
Prozessparameter | Schichtdicke, Maschinengeschwindigkeit, Luftstrom und Vakuumniveau beeinflussen die Sinterkonsistenz. |
Benötigen Sie Hilfe bei der Bestimmung der optimalen Sintertemperatur für Ihre Materialien? Kontaktieren Sie noch heute unsere Experten !