Das Verfahren der Plasmaschichtabscheidung, oft auch als Physical Vapor Deposition (PVD) bezeichnet, ist eine Technik zur Abscheidung dünner Schichten auf Substraten.Bei diesem Verfahren wird ein festes Material in eine Dampfphase umgewandelt, die dann auf einem Substrat kondensiert und eine dünne Schicht bildet.Der Prozess umfasst in der Regel Schritte wie die Verdampfung des Beschichtungsmaterials, die Wanderung von Atomen oder Ionen und die Abscheidung auf dem Substrat.Das Plasma spielt bei diesem Prozess eine entscheidende Rolle, da es das Gas ionisiert und die für die Verdampfungs- und Abscheidungsschritte erforderliche Energie liefert.Im Folgenden werden wir die wichtigsten Aspekte dieses Prozesses im Detail untersuchen.
Die wichtigsten Punkte werden erklärt:
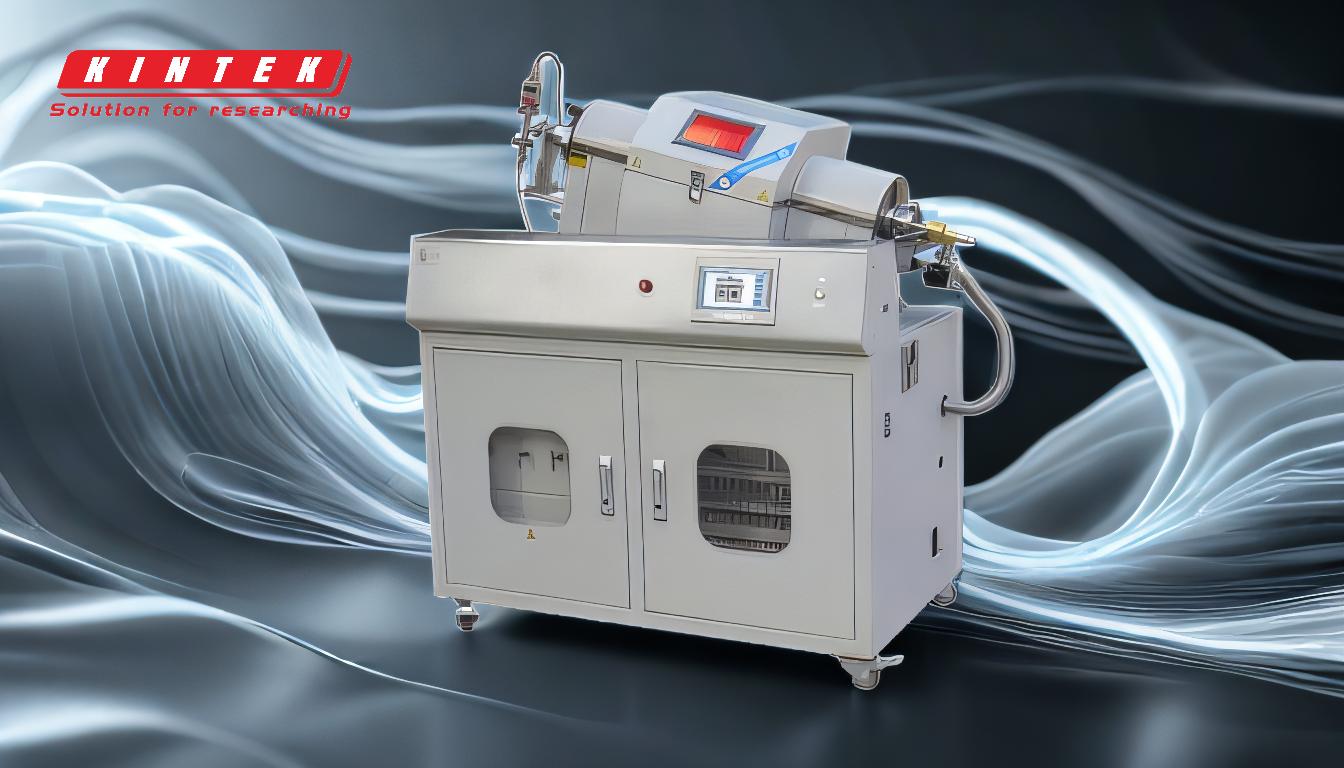
-
Verdampfung von Beschichtungsmaterialien:
- Der erste Schritt im PVD-Verfahren ist die Verdampfung des Beschichtungsmaterials.Dies kann durch verschiedene Methoden wie Verdampfung, Sputtern oder Abscheidung erfolgen.
- Beim Verdampfen wird das Material erhitzt, bis es sich in einen Dampf verwandelt.Beim Sputtern wird das Zielmaterial mit hochenergetischen Teilchen beschossen, wodurch Atome aus der Oberfläche herausgeschleudert werden.
- Die Wahl der Verdampfungsmethode hängt von den Materialeigenschaften und den gewünschten Merkmalen der fertigen Schicht ab.
-
Die Rolle des Plasmas bei der Ionisierung:
- Ein Plasma wird durch Ionisierung eines Gases erzeugt, in der Regel mit einer induktiv gekoppelten Plasmaquelle (ICP).Das Gas wird durch Anlegen eines hochfrequenten elektromagnetischen Feldes ionisiert, das Elektronen aus den Gasatomen herauslöst und ein Plasma erzeugt.
- Das Plasma enthält hochenergetische Elektronen, die mit den Gasmolekülen kollidieren, wodurch diese in Atome oder Ionen dissoziieren.Diese Ionen sind für die nachfolgenden Schritte des Abscheidungsprozesses entscheidend.
-
Migration und Reaktion von Partikeln:
- Sobald sich das Beschichtungsmaterial in der Dampfphase befindet, wandern die Atome, Moleküle oder Ionen durch das Plasma.Während dieser Wanderung können die Teilchen zusammenstoßen und miteinander oder mit einem in das System eingeführten reaktiven Gas reagieren.
- Bei diesen Reaktionen können neue Verbindungen entstehen, die dann auf dem Substrat abgeschieden werden.Das reaktive Gas kann so gewählt werden, dass die chemische Zusammensetzung des abgeschiedenen Films maßgeschneidert ist.
-
Abscheidung auf dem Substrat:
- Der letzte Schritt ist die Abscheidung des verdampften Materials auf dem Substrat.Das Substrat wird in der Regel bei einer niedrigeren Temperatur gehalten, um die Kondensation des Dampfes zu fördern.
- Die abgeschiedenen Atome oder Moleküle bilden einen dünnen Film auf dem Substrat.Die Eigenschaften dieses Films, wie Dicke, Gleichmäßigkeit und Haftung, werden durch die Abscheidungsbedingungen beeinflusst, darunter die Plasmadichte, die Substrattemperatur und das Vorhandensein von reaktiven Gasen.
-
Vorteile der Plasmaschichtabscheidung:
- Hohe Reinheit:Das PVD-Verfahren ermöglicht die Abscheidung hochreiner Schichten, da es in einer Vakuumumgebung durchgeführt wird, die die Verunreinigung minimiert.
- Vielseitigkeit:Mit PVD kann eine Vielzahl von Materialien abgeschieden werden, darunter Metalle, Keramiken und Verbundwerkstoffe.
- Kontrolle über Filmeigenschaften:Die Prozessparameter können fein abgestimmt werden, um die Dicke, die Zusammensetzung und die Mikrostruktur der abgeschiedenen Schicht zu steuern.
- Vorteile für die Umwelt:PVD ist ein trockenes Verfahren, bei dem keine Lösungsmittel oder Chemikalien verwendet werden, was es im Vergleich zu einigen anderen Beschichtungsverfahren umweltfreundlicher macht.
-
Anwendungen der Plasmaschichtabscheidung:
- Elektronik:PVD wird in der Elektronikindustrie häufig für die Abscheidung dünner Schichten auf Halbleitern, Solarzellen und Displays eingesetzt.
- Optik:Das Verfahren wird zur Herstellung von reflektierenden und antireflektierenden Beschichtungen auf optischen Komponenten verwendet.
- Dekorative Beschichtungen:PVD wird eingesetzt, um haltbare und ästhetisch ansprechende Beschichtungen auf Konsumgüter wie Uhren und Schmuck aufzubringen.
- Medizinische Geräte:Das Verfahren wird zur Abscheidung biokompatibler Beschichtungen auf medizinischen Implantaten und Instrumenten eingesetzt.
Zusammenfassend lässt sich sagen, dass das Verfahren der Plasmaschichtabscheidung eine hochentwickelte Technik ist, die Plasma zur Abscheidung dünner Schichten mit hoher Präzision und Kontrolle einsetzt.Der Prozess umfasst mehrere wichtige Schritte, darunter Verdampfung, Ionisierung, Migration und Abscheidung, die jeweils optimiert werden können, um die gewünschten Schichteigenschaften zu erzielen.Die Vielseitigkeit und die Umweltvorteile von PVD machen es zu einem wertvollen Werkzeug in verschiedenen Branchen, von der Elektronik bis zu medizinischen Geräten.
Zusammenfassende Tabelle:
Hauptaspekt | Beschreibung |
---|---|
Verdampfungsmethoden | Verdampfung, Sputtern oder Trennung zur Umwandlung von festem Material in Dampf. |
Die Rolle des Plasmas | Ionisiert Gas und liefert Energie für Verdampfung und Ablagerung. |
Migration und Reaktion | Partikel wandern und reagieren und bilden Verbindungen für die Ablagerung. |
Abscheidung | Dampf kondensiert auf einem Substrat und bildet einen dünnen Film. |
Vorteile | Hohe Reinheit, Vielseitigkeit, präzise Kontrolle und Vorteile für die Umwelt. |
Anwendungen | Elektronik, Optik, dekorative Beschichtungen und medizinische Geräte. |
Entdecken Sie, wie die Plasmaschichtabscheidung Ihre Projekte verbessern kann. Kontaktieren Sie unsere Experten noch heute !