Die Aufdampfung ist eine Schlüsseltechnik bei der Herstellung von Dünnschichten, bei der ein Material verdampft und dann auf ein Substrat aufgebracht wird, um eine dünne, gleichmäßige Schicht zu bilden.Bei diesem Verfahren wird das Zielmaterial erhitzt, bis es in einen gasförmigen Zustand übergeht. Anschließend werden die verdampften Atome oder Moleküle auf das Substrat transportiert, wo sie kondensieren und eine feste Schicht bilden.Diese Methode ist in Branchen wie der Halbleiterherstellung, der Produktion von Solarzellen und der Displaytechnik weit verbreitet.Das Verfahren kann mit verschiedenen Methoden durchgeführt werden, darunter die thermische Verdampfung, die Elektronenstrahlverdampfung und das Sputtern, die jeweils ihre eigenen Vorteile und Anwendungen haben.
Die wichtigsten Punkte werden erklärt:
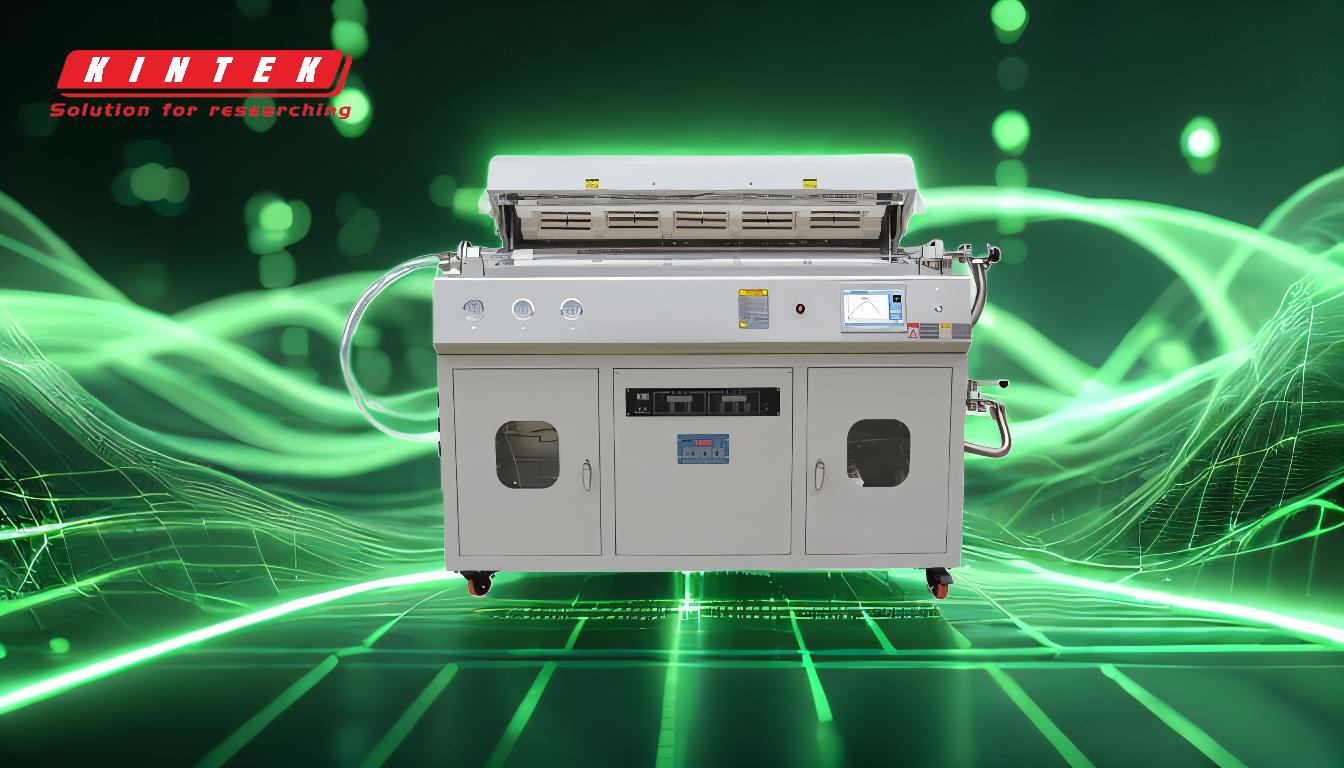
-
Verdampfungsprozess:
- Das aufzubringende Material wird erhitzt, bis es seinen Verdampfungspunkt erreicht.Dies kann mit thermischer Energie aus einem Wolframheizelement oder einem Elektronenstrahl geschehen.Die Atome oder Moleküle gewinnen genügend Energie, um die Bindungskräfte in der festen oder flüssigen Phase zu überwinden und in die Gasphase überzugehen.
- Das verdampfte Material wird dann durch eine Vakuumumgebung zum Substrat transportiert.
-
Transport:
- Die verdampften Atome oder Moleküle wandern durch ein Hochdruckvakuum zum Substrat.Diese Vakuumumgebung ist von entscheidender Bedeutung, da sie eine Verunreinigung verhindert und gewährleistet, dass das verdampfte Material das Substrat erreicht, ohne mit anderen Gasen zu reagieren.
-
Abscheidung:
- Wenn das verdampfte Material das Substrat erreicht, kondensiert es und bildet einen dünnen, gleichmäßigen Film.Die Qualität der Schicht hängt von Faktoren wie der Substrattemperatur, der Abscheidungsrate und den Vakuumbedingungen ab.
-
Methoden der Verdampfungsabscheidung:
- Thermische Verdampfung:Verwendet ein Wolfram-Heizelement, um das Zielmaterial zu verdampfen.Dieses Verfahren eignet sich für die Abscheidung von reinen Metallen, Nichtmetallen, Oxiden und Nitriden.
- Elektronenstrahlverdampfung (E-Beam):Ein hochenergetischer Elektronenstrahl wird eingesetzt, um das Material zu verdampfen.Dieses Verfahren eignet sich besonders für Materialien mit hohem Schmelzpunkt und wird häufig bei der Herstellung von Solarzellen und Glas verwendet.
- Sputtering-Beschichtung:Bei diesem Verfahren wird das Zielmaterial mit hochenergetischen Argonionen beschossen, um Atome zu lösen, die sich dann auf dem Substrat ablagern.Mit dieser Methode lassen sich hochwertige, gleichmäßige Schichten erzeugen.
-
Anwendungen:
- Sonnenkollektoren:Zur Abscheidung leitfähiger Metallschichten, die den Wirkungsgrad von Solarzellen erhöhen.
- OLED-Anzeigen:Unverzichtbar für die Herstellung der für die OLED-Technologie erforderlichen dünnen, leitfähigen Schichten.
- Dünnschicht-Transistoren:Wird für die Herstellung von Transistoren in elektronischen Geräten verwendet.
-
Vorteile:
- Hohe Reinheit:Die Vakuumumgebung gewährleistet, dass die abgeschiedene Schicht frei von Verunreinigungen ist.
- Gleichmäßigkeit:Das Verfahren ermöglicht die Abscheidung sehr dünner, gleichmäßiger Schichten, was für viele Anwendungen entscheidend ist.
- Vielseitigkeit:Kann für eine breite Palette von Materialien verwendet werden, darunter Metalle, Oxide und Nitride.
-
Herausforderungen:
- Hochvakuum-Anforderungen:Die Aufrechterhaltung eines hohen Vakuums kann technisch anspruchsvoll und kostspielig sein.
- Grenzen des Materials:Einige Materialien eignen sich aufgrund ihres hohen Schmelzpunkts oder anderer Eigenschaften nicht für die Aufdampfung.
- Komplexität:Das Verfahren erfordert eine präzise Steuerung von Parametern wie Temperatur, Druck und Abscheidungsrate.
Zusammenfassend lässt sich sagen, dass die Aufdampfung eine vielseitige und weit verbreitete Technik zur Herstellung dünner Schichten für verschiedene industrielle Anwendungen ist.Wenn man die wichtigsten Schritte und Methoden versteht, kann man die Komplexität und Präzision einschätzen, die erforderlich sind, um hochwertige Ergebnisse zu erzielen.
Zusammenfassende Tabelle:
Aspekt | Einzelheiten |
---|---|
Verfahren | Das Material wird verdampft und auf ein Substrat aufgebracht, um einen dünnen Film zu bilden. |
Wichtigste Schritte | 1.Verdampfung 2.Transport 3.Ablagerung |
Methoden | Thermisches Verdampfen, Elektronenstrahlverdampfung, Sputtern |
Anwendungen | Solarzellen, OLED-Displays, Dünnschichttransistoren |
Vorteile | Hohe Reinheit, Gleichmäßigkeit, Vielseitigkeit |
Herausforderungen | Hohe Vakuumanforderungen, Materialbeschränkungen, Prozesskomplexität |
Entdecken Sie, wie die Aufdampfung Ihren Fertigungsprozess verbessern kann. Kontaktieren Sie unsere Experten noch heute !