Beim Rotationskalzinierverfahren werden die Materialien in einem Drehrohrofen auf hohe Temperaturen erhitzt, wodurch chemische Dissoziationen oder physikalische Veränderungen wie z. B. Feuchtigkeitsentzug bewirkt werden.Das Verfahren beruht auf einer rotierenden Trommel, die leicht geneigt ist, um den Materialfluss zu ermöglichen, und die entweder von innen oder von außen beheizt wird.Das Material wird in der Trommel umgewälzt, so dass es gleichmäßig der Hitze ausgesetzt ist, während die kontrollierte Temperatur und Verweilzeit die gewünschte Reaktion gewährleisten.Rotationskalzinatoren werden in der Regel für anorganische Materialien wie Kalkstein, Dolomit und Magnesit eingesetzt und erzeugen effizient gleichmäßige Produkte.
Die wichtigsten Punkte erklärt:
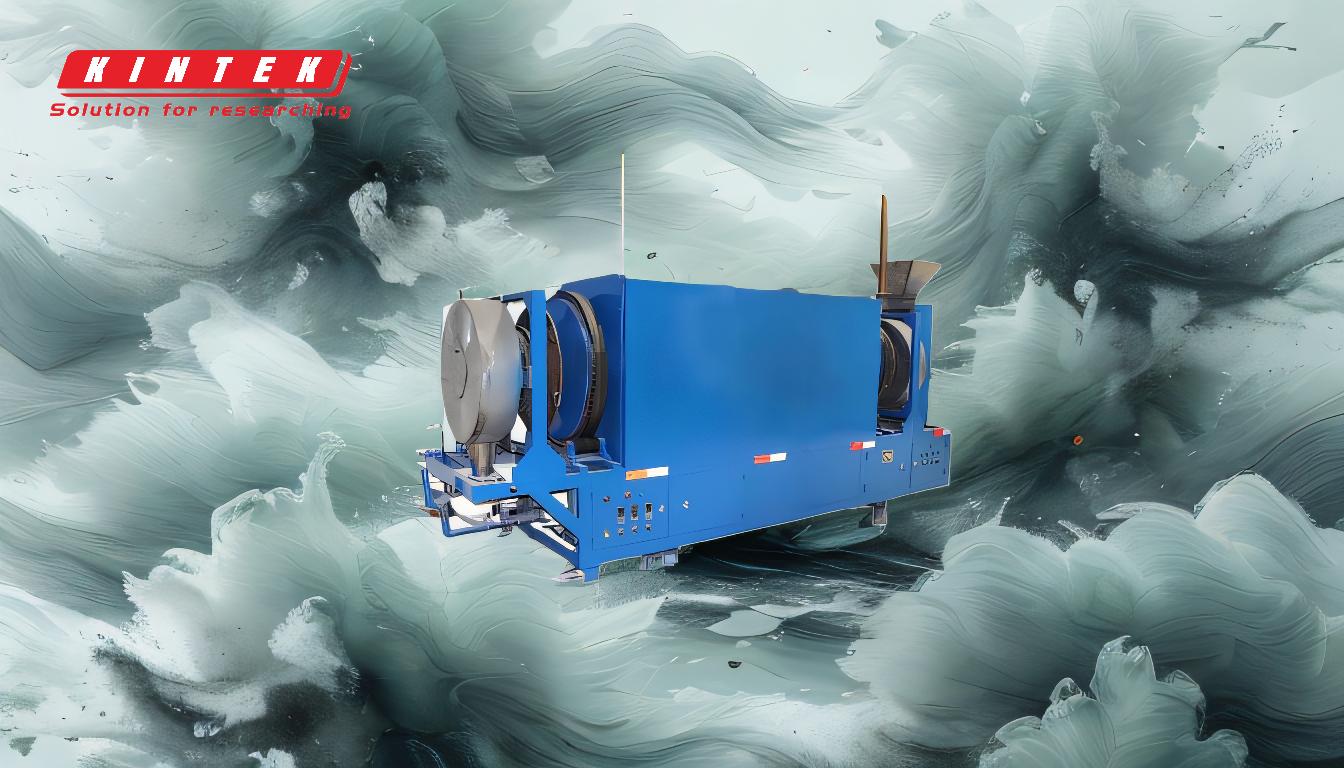
-
Kernfunktion von Rotationskalzinatoren:
- Rotationskalzinatoren sind so konzipiert, dass sie Materialien auf hohe Temperaturen erhitzen und so chemische Dissoziationen oder physikalische Veränderungen wie den Entzug von Feuchtigkeit ermöglichen.
- Dieses Verfahren ist besonders nützlich für anorganische Materialien wie Kalziumkarbonat, das in Kalziumoxid und Kohlendioxid zerfällt.
-
Aufbau und Funktionsweise von Drehrohröfen:
- Der Drehrohrofen ist eine große, hohle, zylindrische Trommel, die sich langsam um ihre Längsachse dreht.
- Sie ist leicht geneigt, damit das Material durch die Schwerkraft vom oberen Ende (Eingang des Einsatzmaterials) zum unteren Ende (Ausgang) befördert werden kann.
- Die Rotation sorgt für eine Verwirbelung und Durchmischung des Materials und fördert eine gleichmäßige Wärmeeinwirkung.
-
Heizmechanismen:
-
Die Beheizung kann durch direkte oder indirekte Methoden erfolgen:
- Direkte Erwärmung:Heiße Gase werden im Inneren des Ofens erzeugt oder von einem externen Ofen eingeleitet.
- Indirekte Beheizung:Die Wärme wird von außen auf die Trommel aufgebracht, wodurch ein direkter Kontakt zwischen dem Material und der Wärmequelle vermieden wird.
- Die Richtung der heißen Gase kann im Gleichstrom (gleiche Richtung wie der Materialfluss) oder im Gegenstrom (entgegengesetzte Richtung) erfolgen, je nach gewünschter thermischer Effizienz und Reaktionssteuerung.
-
Die Beheizung kann durch direkte oder indirekte Methoden erfolgen:
-
Temperatur und Verweilzeit:
- Die Temperatur und die Verweilzeit werden auf der Grundlage chemischer und thermischer Analysen des Materials festgelegt.
- Diese Parameter stellen sicher, dass das Material den gewünschten Zustand erreicht, sei es für die chemische Dissoziation oder den Feuchtigkeitsentzug.
- Die geschlossene Bauweise des Ofens trägt zur Aufrechterhaltung einer kontrollierten Atmosphäre bei, wodurch die Reaktionsbedingungen optimiert werden.
-
Anwendungen des Drehrohrofens:
-
Rotationskalzinatoren werden häufig in Industrien eingesetzt, die eine Hochtemperaturverarbeitung erfordern, wie z. B.:
- Zementherstellung:Kalzinierung von Kalkstein zur Herstellung von Kalk.
- Mineralische Verarbeitung:Verarbeitung von Dolomit, Magnesit und anderen Mineralien.
- Chemische Produktion:Herstellung von anorganischen Verbindungen und Entfernung von gebundener Feuchtigkeit aus Materialien wie Borax.
-
Rotationskalzinatoren werden häufig in Industrien eingesetzt, die eine Hochtemperaturverarbeitung erfordern, wie z. B.:
-
Vorteile von Rotationskalzinatoren:
- Einheitliche Produktqualität:Die Taumelbewegung sorgt für eine gleichmäßige Wärmeverteilung und damit für ein einheitliches Produkt.
- Hohe Verarbeitungsgeschwindigkeit:Rotationskalzinatoren können große Mengen an Material effizient verarbeiten und eignen sich daher für den Einsatz im industriellen Maßstab.
- Vielseitigkeit:Sie können ein breites Spektrum an Materialien und Partikelgrößen verarbeiten, typischerweise bis zu 60 mm.
-
Betriebliche Erwägungen:
- Material-Vorschubgeschwindigkeit:Die Geschwindigkeit, mit der das Material dem Ofen zugeführt wird, muss so gesteuert werden, dass sie den Anforderungen an Verweilzeit und Temperatur entspricht.
- Rotationsgeschwindigkeit des Ofens:Die Rotationsgeschwindigkeit wirkt sich auf die Taumelwirkung und den Materialfluss aus und beeinflusst die Wärmeeinwirkung und die Reaktionseffizienz.
- Management der Wärmequelle:Die Wahl der Wärmequelle (direkt oder indirekt) und der Gasströmungsrichtung (Gleichstrom oder Gegenstrom) hat Auswirkungen auf die Energieeffizienz und die Prozesssteuerung.
Wenn ein Käufer diese Schlüsselpunkte kennt, kann er die Eignung von Rotationskalzinatoren für seine spezifischen Anforderungen beurteilen und dabei Faktoren wie Materialart, gewünschte Leistung und Betriebseffizienz berücksichtigen.
Zusammenfassende Tabelle:
Aspekt | Einzelheiten |
---|---|
Kernfunktion | Erhitzt Materialien zur chemischen Dissoziation oder zu physikalischen Veränderungen wie Feuchtigkeitsentzug. |
Aufbau | Rotierende Trommel, leicht geneigt für Materialfluss und gleichmäßige Wärmeeinwirkung. |
Heizmechanismen | Direkte (interne) oder indirekte (externe) Heizmethoden. |
Anwendungen | Zementherstellung, Mineralienverarbeitung und chemische Produktion. |
Vorteile | Gleichmäßige Produktqualität, hohe Verarbeitungsgeschwindigkeit und Vielseitigkeit. |
Betriebliche Faktoren | Materialzufuhr, Drehgeschwindigkeit des Ofens und Wärmequellenmanagement. |
Sind Sie bereit, Ihre Materialverarbeitung zu optimieren? Kontaktieren Sie uns noch heute um mehr über Rotationskalzinatoren zu erfahren!