Das Sintern ist ein wichtiger Prozess in der Fertigung, insbesondere in der Pulvermetallurgie und der Keramik, bei dem pulverförmige Materialien in dichte, feste Strukturen umgewandelt werden. Der Prozess umfasst mehrere Stufen, darunter die Vorbereitung des Pulvers, die Verdichtung und die kontrollierte Erhitzung in einem Sinterofen. Beim Erhitzen verbinden sich die Partikel durch Diffusion und bilden eine kohäsive Struktur, ohne dass das Material vollständig schmilzt. Eine zentrale Rolle spielt der Sinterofen, dessen Atmosphäre und Temperaturprofil sorgfältig reguliert werden, um bestimmte Ergebnisse zu erzielen, wie z. B. die Entfernung von Schmiermitteln, die Reduzierung von Oxiden und die Bindung von Partikeln. Das Endprodukt ist ein haltbares, hochfestes Material mit geringer Porosität. Nachstehend finden Sie eine detaillierte Aufschlüsselung des Sinterprozesses und seiner wichtigsten Phasen.
Die wichtigsten Punkte werden erklärt:
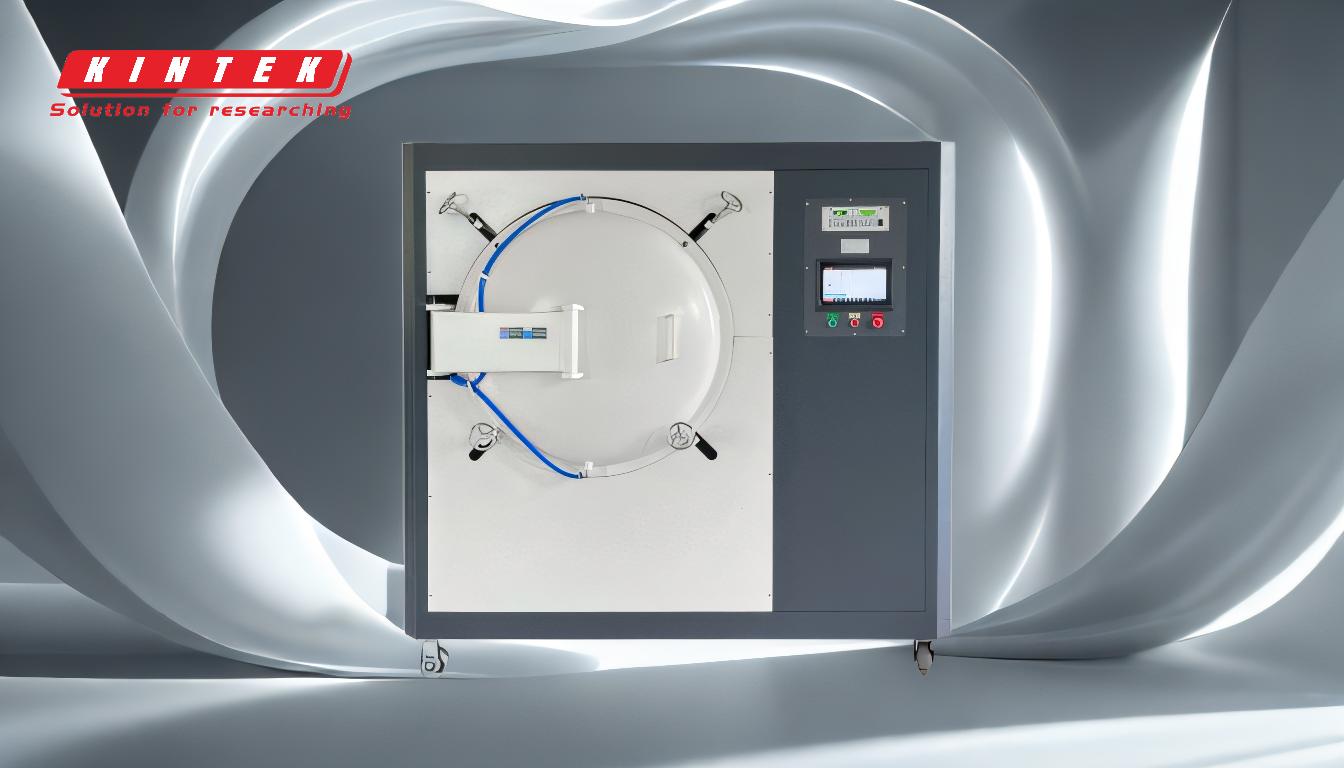
-
Stadien des Sinterprozesses:
- Vorbereitung des Pulvers: Das Rohmaterial, oft in Pulverform, wird mit Zusatzstoffen wie Bindemitteln, Entflockungsmitteln und Wasser zu einem Brei vermischt. Diese Mischung wird sprühgetrocknet, um ein gleichmäßiges Pulver zu erhalten, das verdichtet werden kann.
- Verdichtung: Das Pulver wird durch mechanische Verfahren wie Kalt- oder Heißpressen in eine bestimmte Form gepresst. In dieser Phase werden Hohlräume beseitigt und die Gleichmäßigkeit sichergestellt, so dass ein "grünes Teil" entsteht, das zwar seine Form behält, aber keine Festigkeit aufweist.
- Sintern (Brennen): Das Rohteil wird unter kontrollierten Bedingungen in einem Sinterofen erhitzt. Die Temperatur wird unter dem Schmelzpunkt des Materials gehalten, um die Partikelbindung durch Diffusion zu erleichtern, so dass sich zwischen den Partikeln Nasen bilden und die Struktur verdichtet wird.
- Kühlung: Nach dem Sintern wird das Material allmählich abgekühlt und verfestigt sich zu einer starren, zusammenhängenden Struktur.
-
Die Rolle des Sinterofens:
-
Der Ofen ist mit mehreren Zonen ausgestattet, die jeweils einem bestimmten Zweck dienen:
- Schmierstoff-Entnahmezone: Entfernt die bei der Verdichtung verwendeten Schmiermittel.
- Oxidreduktionszone: Reduziert Oberflächenoxide zur Verbesserung der Partikelbindung.
- Sinterzone: Erleichtert die Diffusion und Bindung von Partikeln bei hohen Temperaturen.
- Kühlung Zone: Senkt allmählich die Temperatur, um das Material zu verfestigen.
- Die Ofenatmosphäre (z. B. Wasserstoff, Stickstoff oder Vakuum) wird sorgfältig kontrolliert, um Oxidation zu verhindern und optimale Sinterbedingungen zu gewährleisten.
-
Der Ofen ist mit mehreren Zonen ausgestattet, die jeweils einem bestimmten Zweck dienen:
-
Mechanismen der Sinterung:
- Diffusion: Die Atome bewegen sich über die Partikelgrenzen hinweg und bilden dabei Einschnürungen und verringern die Porosität.
- Bildung des Halses: Durch die anfängliche Bindung zwischen den Teilchen entsteht ein Netz von miteinander verbundenen Strukturen.
- Verdichtung: Mit der Zeit wird das Material dichter, da die Poren schrumpfen und die Partikel zusammenwachsen.
-
Arten des Sinterns:
- Festkörpersintern: Findet ohne flüssige Phasen statt und beruht ausschließlich auf Diffusion.
- Flüssigphasensintern: Enthält eine flüssige Phase, die die Partikelbindung unterstützt; wird häufig für Materialien mit hohem Schmelzpunkt verwendet.
- Transiente Flüssigphasensinterung: Beim Erhitzen bildet sich eine vorübergehende flüssige Phase, die beim Abkühlen wieder erstarrt.
-
Anwendungen des Sinterns:
- Pulvermetallurgie: Zur Herstellung von Metallteilen mit hoher Festigkeit und Haltbarkeit, z. B. Zahnräder, Lager und Automobilteile.
- Keramik: Zur Herstellung von keramischen Produkten wie Fliesen, Isolatoren und modernen Materialien für die Elektronik.
- Hochschmelzende Materialien: Ideal für Materialien wie Wolfram und Molybdän, die mit herkömmlichen Schmelzverfahren nur schwer zu verarbeiten sind.
-
Vorteile des Sinterns:
- Kostengünstig: Verringert den Materialabfall und den Energieverbrauch im Vergleich zu Schmelzverfahren.
- Hohe Präzision: Ermöglicht die Herstellung von komplexen Formen mit engen Toleranzen.
- Materialeigenschaften: Verbessert die Festigkeit, Haltbarkeit und Verschleißfestigkeit des Endprodukts.
-
Herausforderungen und Überlegungen:
- Temperaturkontrolle: Eine genaue Regelung ist unerlässlich, um ein Schmelzen oder eine unvollständige Verklebung zu vermeiden.
- Atmosphärenmanagement: Die Ofenatmosphäre muss sorgfältig kontrolliert werden, um Verunreinigungen oder Oxidation zu vermeiden.
- Auswahl des Materials: Nicht alle Materialien eignen sich zum Sintern, insbesondere solche mit niedrigem Schmelzpunkt oder schlechten Diffusionseigenschaften.
Wenn die Käufer von Anlagen und Verbrauchsmaterialien diese Schlüsselpunkte kennen, können sie fundierte Entscheidungen über Sinteröfen und die entsprechenden Materialien treffen und so optimale Ergebnisse für ihre spezifischen Anwendungen erzielen.
Zusammenfassende Tabelle:
Hauptaspekt | Einzelheiten |
---|---|
Stadien der Sinterung | Pulveraufbereitung, Verdichtung, Sintern (Brennen), Kühlung |
Die Rolle des Sinterofens | Schmiermittelentfernung, Oxidreduktion, Sinterzone, Kühlzone |
Mechanismen | Diffusion, Halsbildung, Verdichtung |
Arten des Sinterns | Festkörper, Flüssigphase, transiente Flüssigphase |
Anwendungen | Pulvermetallurgie, Keramik, Werkstoffe mit hohem Schmelzpunkt |
Vorteile | Kosteneffektiv, hochpräzise, verbesserte Materialeigenschaften |
Herausforderungen | Temperaturkontrolle, Atmosphärenmanagement, Materialauswahl |
Sind Sie bereit, Ihren Herstellungsprozess mit dem richtigen Sinterofen zu optimieren? Kontaktieren Sie uns heute für fachkundige Beratung!