Die thermische Verdampfung ist eine weit verbreitete Technik zur Abscheidung von Dünnschichten, bei der ein Material in einer Hochvakuumumgebung bis zu seinem Verdampfungspunkt erhitzt wird. Das verdampfte Material wandert dann durch das Vakuum und kondensiert auf einem Substrat, wobei eine dünne, gleichmäßige Schicht entsteht. Dieses Verfahren beruht auf thermischer Energie, um das Zielmaterial zu verdampfen, wobei in der Regel Widerstandsheizelemente wie Wolframschiffchen oder Spulen verwendet werden. Die Vakuumumgebung gewährleistet eine minimale Verunreinigung und ermöglicht es den verdampften Partikeln, ungehindert auf das Substrat zu gelangen. Diese Methode wird besonders wegen ihrer Einfachheit, Kosteneffizienz und der Fähigkeit zur Herstellung hochreiner Schichten geschätzt.
Die wichtigsten Punkte werden erklärt:
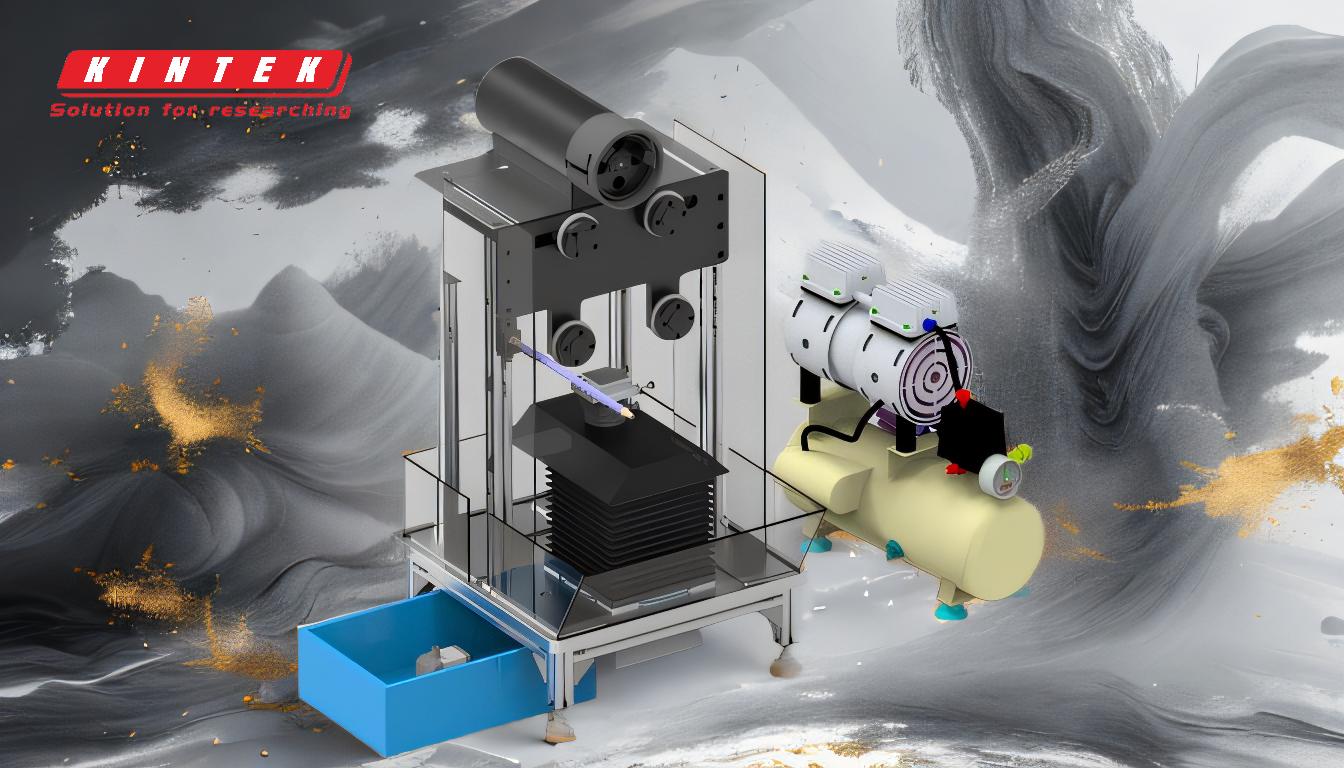
-
Überblick über die thermische Verdampfungsabscheidung:
- Die thermische Verdampfung ist ein Verfahren zur physikalischen Abscheidung aus der Gasphase (PVD), mit dem dünne Schichten auf Substraten erzeugt werden.
- Bei diesem Verfahren wird ein Zielmaterial erhitzt, bis es verdampft, und der entstehende Dampf kondensiert auf einem Substrat und bildet einen Film.
- Aufgrund ihrer Einfachheit und Effektivität wird sie häufig in Branchen wie Elektronik, Optik und Beschichtungen eingesetzt.
-
Schlüsselkomponenten des Prozesses:
- Vakuumkammer: Das Verfahren findet in einer Hochvakuumumgebung statt, um die Kontamination zu minimieren und den freien Weg für verdampfte Partikel zu gewährleisten.
- Verdampfung Quelle: Das Zielmaterial wird in ein Widerstandsheizelement, z. B. ein Wolframschiffchen, eine Spule oder einen Korb, gelegt.
- Mechanismus der Heizung: Elektrischer Strom wird durch das Heizelement geleitet, wodurch Wärmeenergie erzeugt wird, die das Material bis zu seinem Verdampfungspunkt erhitzt.
- Substrat: Die Oberfläche, auf der das verdampfte Material kondensiert und einen dünnen Film bildet.
-
Schritt-für-Schritt-Verfahren:
-
Schritt 1: Vorbereitung:
- Das Zielmaterial wird in die Verdampfungsquelle (z. B. ein Wolframschiffchen oder eine Wolframspule) geladen.
- Das Substrat wird gereinigt und über der Verdampfungsquelle in der Vakuumkammer positioniert.
-
Schritt 2: Evakuierung:
- Die Vakuumpumpe saugt Luft und andere Gase aus der Kammer ab, so dass eine Hochvakuumumgebung entsteht.
-
Schritt 3: Heizung:
- Das Heizelement wird mit elektrischem Strom beaufschlagt, wodurch es sich erhitzt und Wärmeenergie auf das Zielmaterial überträgt.
- Das Material wird bis zu seinem Schmelzpunkt und dann bis zu seinem Verdampfungspunkt erhitzt, wo es von einem festen in einen dampfförmigen Zustand übergeht.
-
Schritt 4: Verdampfung und Ablagerung:
- Das verdampfte Material bildet eine Dampfwolke im Inneren der Kammer.
- Die Dampfpartikel wandern durch das Vakuum, kondensieren auf dem Substrat und bilden einen dünnen Film.
-
Schritt 5: Abkühlung und Entnahme:
- Nach der Beschichtung wird das Substrat abgekühlt, und die Vakuumkammer wird belüftet, um das beschichtete Substrat zu entfernen.
-
Schritt 1: Vorbereitung:
-
Vorteile der thermischen Verdampfungsabscheidung:
- Hohe Reinheit: Die Vakuumumgebung minimiert die Verunreinigung, was zu hochreinen Filmen führt.
- Vereinfachung: Das Verfahren ist einfach und erfordert keine komplexe Ausrüstung.
- Kosten-Wirksamkeit: Sie ist im Vergleich zu anderen Dünnschichttechniken relativ kostengünstig.
- Vielseitigkeit: Es kann für eine Vielzahl von Materialien verwendet werden, darunter Metalle, Legierungen und einige Verbindungen.
-
Grenzen der thermischen Verdampfungsabscheidung:
- Materielle Beschränkungen: Einige Materialien, wie hochschmelzende Metalle und Keramiken, lassen sich aufgrund ihres hohen Schmelzpunkts nur schwer verdampfen.
- Einheitlichkeit: Eine gleichmäßige Schichtdicke zu erreichen, kann eine Herausforderung sein, insbesondere bei großen oder komplexen Substraten.
- Haftung: Die Haftung der abgeschiedenen Schicht auf dem Substrat kann im Vergleich zu anderen Abscheidungsmethoden schwächer sein.
-
Anwendungen der thermischen Verdampfungsabscheidung:
- Elektronik: Zur Abscheidung von leitenden Schichten, wie Aluminium oder Gold, in Halbleiterbauelementen.
- Optik: Wird bei der Herstellung von Reflexionsschichten, Antireflexionsschichten und optischen Filtern verwendet.
- Beschichtungen: Wird für dekorative und schützende Beschichtungen auf verschiedenen Materialien, einschließlich Kunststoffen und Metallen, verwendet.
-
Vergleich mit anderen Abscheidungstechniken:
- Thermisches Verdampfen vs. Sputtern: Die thermische Verdampfung ist einfacher und kostengünstiger, hat aber mit hochschmelzenden Materialien zu kämpfen, während das Sputtern ein breiteres Spektrum von Materialien verarbeiten kann, aber komplexer und teurer ist.
- Thermische Verdampfung vs. Chemische Gasphasenabscheidung (CVD): Die thermische Verdampfung ist ein physikalischer Prozess, während bei der CVD chemische Reaktionen ablaufen. Mit CVD können komplexere Schichten hergestellt werden, doch sind höhere Temperaturen und komplexere Anlagen erforderlich.
Wenn man den Prozess, die Komponenten, die Vorteile und die Grenzen der thermischen Aufdampfung versteht, können Käufer von Geräten und Verbrauchsmaterialien fundierte Entscheidungen über die Eignung für ihre spezifischen Anwendungen treffen.
Zusammenfassende Tabelle:
Aspekt | Einzelheiten |
---|---|
Prozess-Übersicht | Erhitzt Material im Vakuum bis zum Verdampfungspunkt und bildet dünne Schichten. |
Wichtige Komponenten | Vakuumkammer, Verdampfungsquelle (z. B. Wolframschiffchen), Heizmechanismus. |
Vorteile | Hohe Reinheit, Einfachheit, Kosteneffizienz und Vielseitigkeit. |
Beschränkungen | Materialbeschränkungen, Probleme mit der Gleichmäßigkeit, schwächere Haftung. |
Anwendungen | Elektronik (leitende Schichten), Optik (Beschichtungen), dekorative/schützende Folien. |
Vergleich | Einfacher und billiger als Sputtern und CVD, aber begrenzt für hochschmelzende Materialien. |
Entdecken Sie, wie die thermische Aufdampfung Ihre Projekte verbessern kann kontaktieren Sie unsere Experten noch heute !