Das Sintern in der Pulvermetallurgie ist ein kritischer Wärmebehandlungsprozess, der verdichtete Metallpulver in dichte, feste und funktionale Komponenten verwandelt.Durch Erhitzen der verdichteten Teile auf Temperaturen unterhalb des Schmelzpunkts des Primärmetalls verbindet das Sintern die Partikel miteinander, verringert die Porosität und verbessert die mechanischen Eigenschaften.Dieses Verfahren gewährleistet, dass das Endprodukt die gewünschte Festigkeit, Maßgenauigkeit und strukturelle Integrität aufweist.Das Sintern ist in der Industrie zur Herstellung von Komponenten wie Zahnrädern, Lagern und elektrischen Kontakten weit verbreitet und bietet eine kostengünstige und effiziente Herstellungsmethode für komplexe Teile.
Die wichtigsten Punkte werden erklärt:
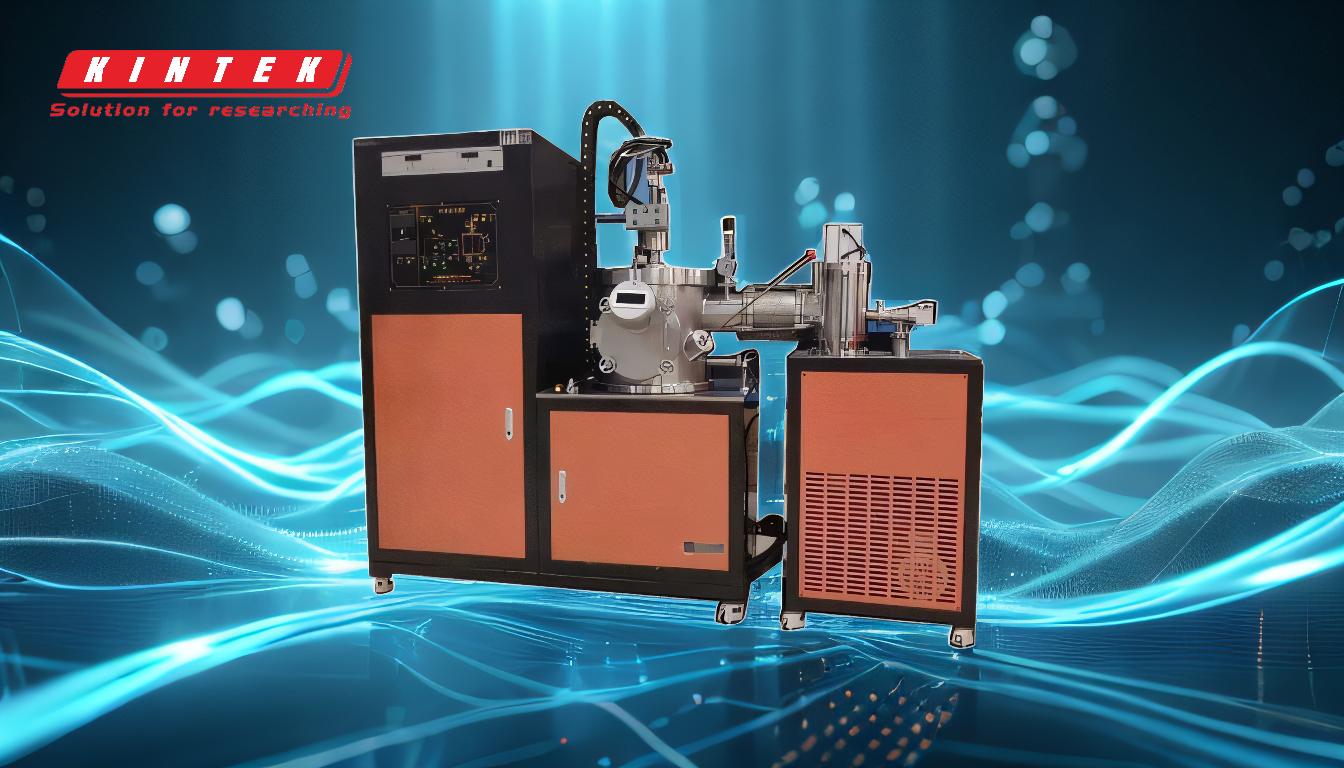
-
Definition und Zweck des Sinterns
- Sintern ist ein Wärmebehandlungsverfahren in der Pulvermetallurgie, bei dem Metallpulverpartikel zu einer zusammenhängenden, dichten Struktur verbunden werden, ohne das Material zu schmelzen.
- Der Hauptzweck besteht darin, die mechanischen Eigenschaften wie Festigkeit und Haltbarkeit zu verbessern und gleichzeitig die Porosität zu verringern und die endgültigen Abmessungen zu erreichen.
- Es verwandelt den "grünen" Pressling (eine lose gebundene Pulverstruktur) in ein festes, funktionelles Teil, das für die Endanwendung geeignet ist.
-
Wie das Sintern funktioniert
- Bei diesem Verfahren wird der Grünling in einem Ofen mit kontrollierter Atmosphäre bei Temperaturen knapp unter dem Schmelzpunkt des Primärmetalls erhitzt.
- Während des Sinterns verbinden sich die Partikel durch Diffusion, wodurch Poren eliminiert und die Dichte erhöht wird.
- Die kontrollierte Abkühlungsgeschwindigkeit nach dem Sintern ermöglicht eine weitere Feinabstimmung der Materialeigenschaften, wie z. B. der Härte und Zähigkeit.
-
Die wichtigsten Vorteile des Sinterns
- Verbesserte mechanische Eigenschaften:Durch das Sintern werden die Festigkeit, die Verschleißfestigkeit und die strukturelle Integrität des Materials erheblich verbessert.
- Maßgenauigkeit:Das Verfahren berücksichtigt geringfügige Schrumpfungen und stellt sicher, dass das endgültige Teil die genauen Maßanforderungen erfüllt.
- Kosteneffizienz:Das Sintern ist ein vielseitiges und effizientes Verfahren zur Herstellung komplexer Formen und Bauteile, das den Materialabfall und die Bearbeitungskosten reduziert.
- Vielseitigkeit:Es ist für eine breite Palette von Werkstoffen, einschließlich Metallen, Keramik und Verbundwerkstoffen, geeignet, so dass es in verschiedenen Branchen eingesetzt werden kann.
-
Anwendungen von gesinterten Teilen
- Das Sintern wird zur Herstellung von Komponenten wie Zahnrädern, Lagern, Riemenscheiben, Rotoren, Kettenrädern und elektrischen Kontakten verwendet.
- Es ist besonders wertvoll in Branchen, die Hochleistungsteile benötigen, wie z. B. die Automobil-, Luft- und Raumfahrt- sowie die Elektronikindustrie.
- Durch die Möglichkeit, endkonturnahe Bauteile herzustellen, wird der Bedarf an zusätzlicher Bearbeitung reduziert, was Zeit und Ressourcen spart.
-
Prozessparameter und Steuerung
- Temperatur:Die Sintertemperaturen werden sorgfältig kontrolliert, um unter dem Schmelzpunkt des Primärmetalls zu bleiben und eine Verbindung ohne Verflüssigung zu gewährleisten.
- Atmosphäre:Die Ofenatmosphäre (z. B. Wasserstoff, Stickstoff oder Vakuum) wird kontrolliert, um Oxidation zu verhindern und eine gute Partikelbindung zu gewährleisten.
- Abkühlungsrate:Durch die Anpassung der Abkühlgeschwindigkeit können die Hersteller die Mikrostruktur und die mechanischen Eigenschaften des Materials individuell anpassen.
-
Vergleich mit anderen Herstellungsverfahren
- Im Gegensatz zum Gießen oder Schmieden wird beim Sintern das Metall nicht geschmolzen, was den Energieverbrauch senkt und den Materialabfall minimiert.
- Es ermöglicht die Herstellung komplexer Geometrien, die mit herkömmlichen Verfahren nur schwer zu erreichen sind.
- Das Sintern ist besonders vorteilhaft für Werkstoffe mit hohen Schmelzpunkten, da es die mit dem Schmelzen und Erstarren verbundenen Probleme vermeidet.
-
Rolle in der Pulvermetallurgie
- Das Sintern ist der letzte und kritischste Schritt in der Pulvermetallurgie, bei dem das verdichtete Pulver in ein funktionsfähiges Teil verwandelt wird.
- Es stellt sicher, dass das Teil die erforderlichen physikalischen und mechanischen Eigenschaften wie Dichte, Härte und Festigkeit erreicht.
- Ohne die Sinterung würde der Grünling nicht die erforderliche strukturelle Integrität und die Leistungsmerkmale für reale Anwendungen aufweisen.
Zusammenfassend lässt sich sagen, dass das Sintern ein grundlegender Prozess in der Pulvermetallurgie ist, der die Herstellung von hochwertigen, langlebigen und präzisen Komponenten ermöglicht.Durch das Verbinden von Metallpartikeln bei hohen Temperaturen werden die Materialeigenschaften verbessert, die Porosität verringert und die Maßgenauigkeit gewährleistet, was es in der modernen Fertigung unverzichtbar macht.
Zusammenfassende Tabelle:
Aspekt | Einzelheiten |
---|---|
Zweck | Bindet Metallpartikel, reduziert die Porosität, verbessert die mechanischen Eigenschaften. |
Verfahren | Erhitzen unter den Schmelzpunkt, kontrollierte Atmosphäre, Diffusionsverklebung. |
Vorteile | Verbesserte Festigkeit, Verschleißfestigkeit, Kosteneffizienz, Vielseitigkeit. |
Anwendungen | Zahnräder, Lager, elektrische Kontakte, Automobil, Luft- und Raumfahrt, Elektronik. |
Wichtige Parameter | Temperatur, Atmosphäre, Abkühlgeschwindigkeit. |
Rolle bei der Herstellung | Letzter Schritt in der Pulvermetallurgie, gewährleistet strukturelle Integrität und Präzision. |
Entdecken Sie, wie das Sintern Ihren Fertigungsprozess optimieren kann. Kontaktieren Sie unsere Experten noch heute !