Bei der Vakuumwärmebehandlung handelt es sich um ein spezielles Verfahren zur Verbesserung der mechanischen und chemischen Eigenschaften von Metallen durch Erhitzen im Vakuum.Diese Methode verhindert die Oxidation, minimiert den Verzug und gewährleistet eine präzise Steuerung der Heiz- und Kühlparameter.Sie ist besonders effektiv für Materialien wie Superlegierungen, reaktive Metalle und Edelstahl und verbessert deren Härte, Festigkeit und Verschleißfestigkeit.Außerdem ist die Wärmebehandlung im Vakuum sicherer und umweltfreundlicher, da keine brennbaren Gase und schädlichen Verunreinigungen verwendet werden.Dies macht sie ideal für Industrien, die Hochleistungswerkstoffe mit hervorragender Haltbarkeit und Maßhaltigkeit benötigen.
Die wichtigsten Punkte erklärt:
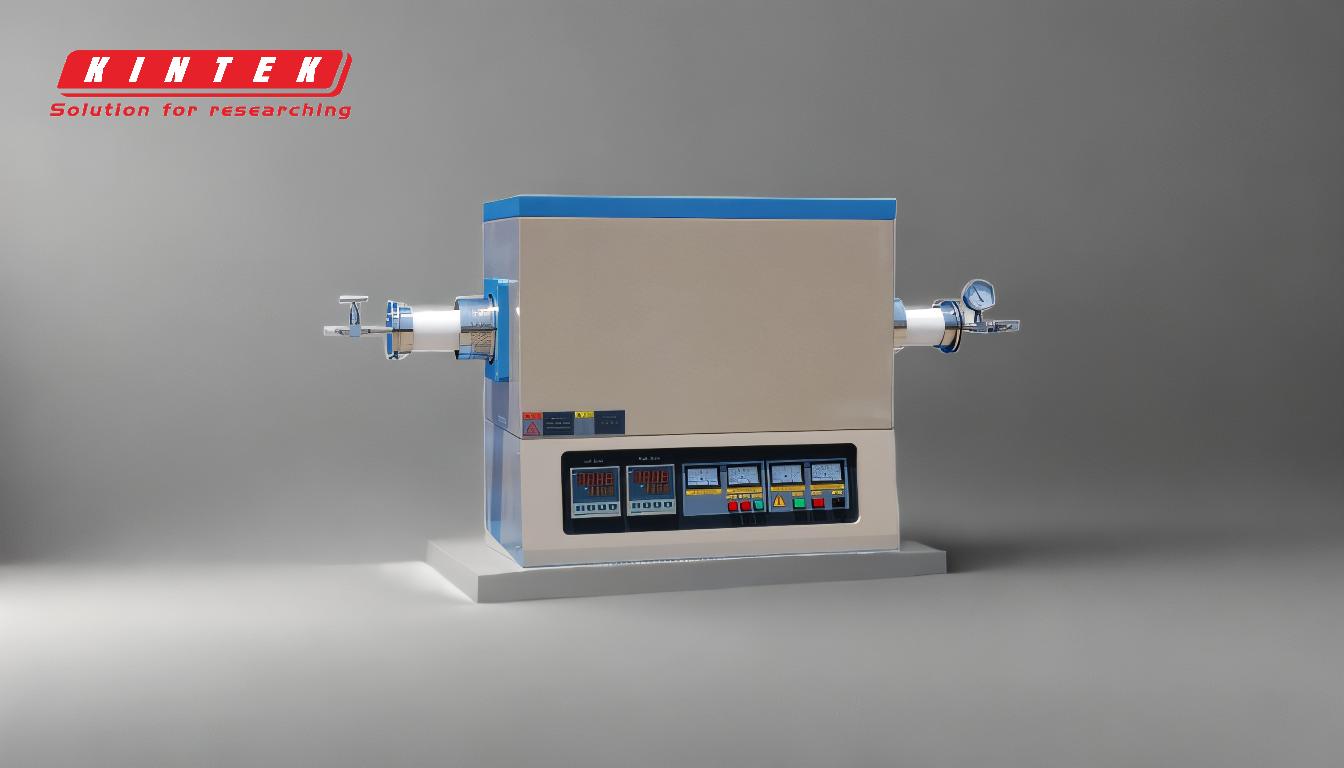
-
Verhinderung von Oxidation und Kontamination:
- Die Vakuumwärmebehandlung erfolgt in einer abgedichteten Kammer, in der die Luft mit Hilfe einer Vakuumpumpe .Dadurch wird der Sauerstoff eliminiert und die Oxidation und Verunreinigung der Metalloberflächen verhindert.
- Die Abwesenheit von Sauerstoff sorgt dafür, dass die behandelten Werkstoffe ihre ursprünglichen Eigenschaften, wie Oberflächenbeschaffenheit und chemische Zusammensetzung, behalten, was zu einer längeren Lebensdauer führt.
-
Verbesserte mechanische Eigenschaften:
-
Indem man Metalle kontrollierten Heiz- und Kühlzyklen im Vakuum aussetzt, wird die kristalline Struktur des Materials optimiert.Dies führt zu:
- Erhöhte Härte und Festigkeit.
- Verbesserte Verschleißfestigkeit, wodurch sich die Komponenten für anspruchsvolle Anwendungen eignen.
- Verbesserte Elastizität und Scherfestigkeit, die für Hochleistungsanwendungen entscheidend sind.
-
Indem man Metalle kontrollierten Heiz- und Kühlzyklen im Vakuum aussetzt, wird die kristalline Struktur des Materials optimiert.Dies führt zu:
-
Minimierte Verformung und Dimensionsstabilität:
- Der gleichmäßige Erwärmungs- und Abkühlungsprozess in einer Vakuumumgebung reduziert die thermische Belastung und minimiert das Risiko von Verformungen.
- Dadurch wird sichergestellt, dass die behandelten Teile ihre Maßgenauigkeit beibehalten, was für Präzisionskomponenten in Branchen wie der Luft- und Raumfahrt und der Automobilindustrie von entscheidender Bedeutung ist.
-
Eignung für spezialisierte Materialien:
-
Die Vakuumwärmebehandlung eignet sich besonders gut für Materialien, die oxidationsempfindlich sind oder deren Eigenschaften genau kontrolliert werden müssen.Dazu gehören:
- Superlegierungen (z. B. Nickel-, Eisen-Nickel- und Kobalt-Nickel-Basiswerkstoffe).
- Reaktive und hochschmelzende Metalle (z. B. Titan und Haynes-Legierungen).
- Rostfreier Stahl und bestimmte Messing- und Bronzesorten, die in Musikinstrumenten verwendet werden.
-
Die Vakuumwärmebehandlung eignet sich besonders gut für Materialien, die oxidationsempfindlich sind oder deren Eigenschaften genau kontrolliert werden müssen.Dazu gehören:
-
Vorteile für Umwelt und Sicherheit:
- Im Gegensatz zu herkömmlichen Wärmebehandlungsverfahren werden bei der Vakuumwärmebehandlung keine brennbaren Gase verwendet und keine schädlichen Nebenprodukte erzeugt.
- Das Verfahren ist frei von Umweltverschmutzung und entspricht den OSHA-Sicherheitsstandards, was eine sicherere Arbeitsumgebung für die Mitarbeiter gewährleistet.
-
Präzision und Kontrolle:
- Die Vakuumumgebung ermöglicht eine genaue Kontrolle der Erwärmungs- und Abkühlungsraten, so dass die Hersteller den Prozess an die spezifischen Materialanforderungen anpassen können.
- Diese Präzision gewährleistet gleichbleibende Ergebnisse und macht die Vakuum-Wärmebehandlung ideal für Hochleistungsanwendungen, bei denen Zuverlässigkeit entscheidend ist.
-
Erweiterte Anwendungen:
- Die Verbesserung der chemischen und mechanischen Eigenschaften, wie Korrosionsbeständigkeit und Härte, erweitert die Einsatzmöglichkeiten behandelter Metalle.
- Mit Vakuum-Wärmebehandlung behandelte Komponenten eignen sich für Branchen wie Luft- und Raumfahrt, Medizintechnik, Werkzeugbau und Energie, in denen Haltbarkeit und Leistung von größter Bedeutung sind.
Zusammenfassend lässt sich sagen, dass die Vakuumwärmebehandlung ein vielseitiges und fortschrittliches Verfahren ist, das die Leistung und Langlebigkeit von Metallen verbessert.Die Fähigkeit, Oxidation zu verhindern, die mechanischen Eigenschaften zu verbessern und die Dimensionsstabilität zu gewährleisten, macht es unverzichtbar für Industrien, die hochwertige, langlebige Materialien benötigen.
Zusammenfassende Tabelle:
Wichtigste Vorteile | Einzelheiten |
---|---|
Verhindert Oxidation | Eliminiert Sauerstoff und bewahrt die Oberflächenbeschaffenheit und die chemische Zusammensetzung. |
Verbessert die mechanischen Eigenschaften | Erhöht die Härte, Festigkeit, Verschleißfestigkeit und Elastizität. |
Minimiert Verformung | Verringert die thermische Belastung und gewährleistet die Maßhaltigkeit. |
Geeignet für Spezialmetalle | Ideal für Superlegierungen, reaktive Metalle und rostfreien Stahl. |
Vorteile für Umwelt und Sicherheit | Schadstofffrei, keine brennbaren Gase und OSHA-konform. |
Präzision und Kontrolle | Maßgeschneiderte Heiz- und Kühlraten für konsistente, hochwertige Ergebnisse. |
Erweiterte Anwendungen | Luft- und Raumfahrt, Medizintechnik, Werkzeugbau und Energiewirtschaft profitieren in hohem Maße davon. |
Erfahren Sie, wie die Vakuum-Wärmebehandlung die Leistung Ihrer Werkstoffe steigern kann. Kontaktieren Sie unsere Experten noch heute !