Sintern und Schmelzen sind zwei unterschiedliche Prozesse, bei denen Materialien erhitzt werden. Sie unterscheiden sich jedoch grundlegend in Bezug auf Temperatur, Energiebedarf und Ergebnisse. Das Sintern erfolgt bei Temperaturen unterhalb des Schmelzpunkts des Materials und beinhaltet die Verschmelzung von Partikeln durch Hitze und Druck ohne Verflüssigung. Im Gegensatz dazu erfordert das Schmelzen das Erreichen des Schmelzpunkts des Materials, wodurch es von einem festen in einen flüssigen Zustand überführt wird. Die Beziehung zwischen Sintertemperatur und Schmelzpunkt ist entscheidend, da das Sintern bei Temperaturen erfolgen muss, die hoch genug sind, um eine Partikelbindung zu ermöglichen, aber niedrig genug, um eine Verflüssigung zu vermeiden. Dieses Gleichgewicht gewährleistet die Materialintegrität, die Kontrolle über den Prozess und die gewünschten physikalischen Eigenschaften des Endprodukts.
Wichtige Punkte erklärt:
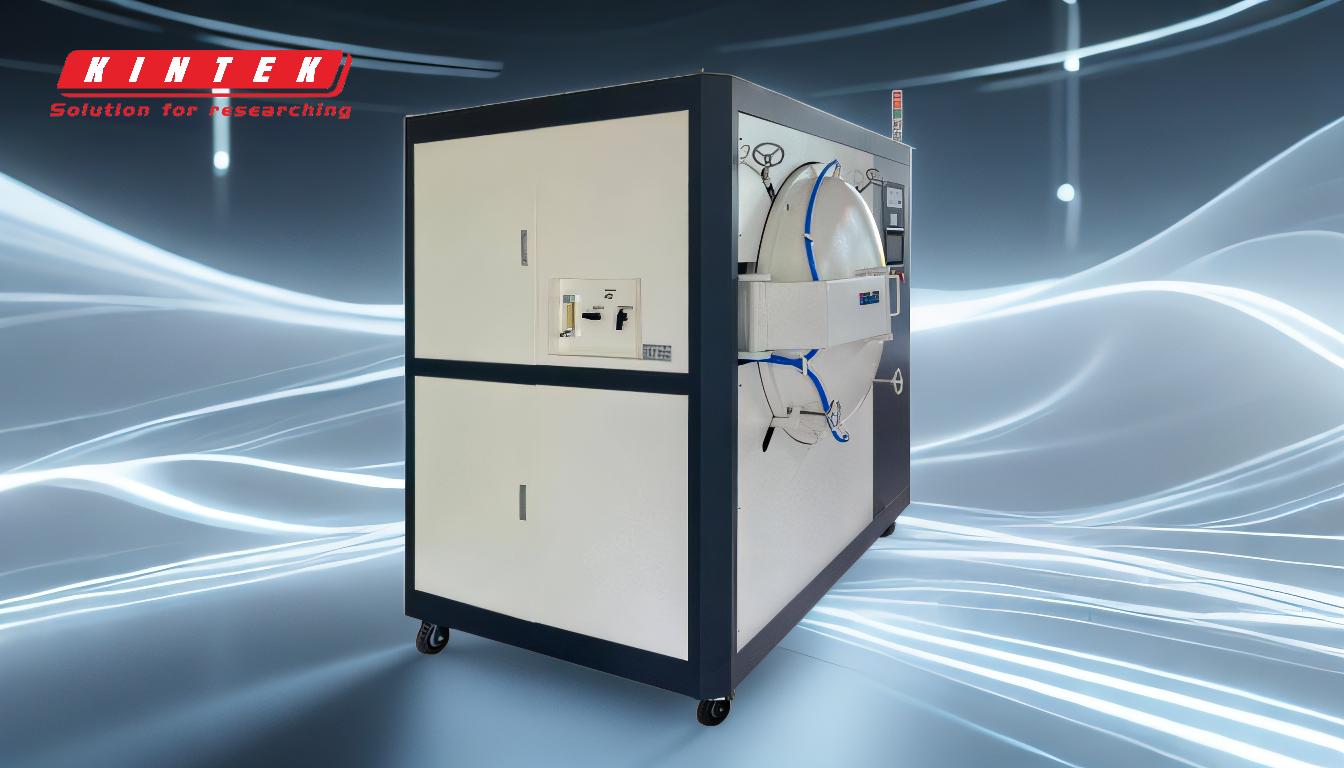
-
Definition von Sintern und Schmelzen:
- Sintern: Ein Prozess, bei dem Partikel eines Materials durch Hitze und Druck miteinander verschmolzen werden, ohne jedoch den Schmelzpunkt des Materials zu erreichen. Dadurch behält das Material seinen festen Zustand bei und erreicht gleichzeitig eine Bindung auf Partikelebene.
- Schmelzen: Ein Prozess, bei dem ein Material bis zu seinem Schmelzpunkt erhitzt wird, wodurch es von einem festen in einen flüssigen Zustand übergeht. Dies erfordert ausreichend Wärmeenergie, um die inneren Bindungen des Materials zu überwinden.
-
Temperaturbeziehung:
- Die Sintertemperaturen liegen immer unter dem Schmelzpunkt des Materials. Dies liegt daran, dass das Sintern auf einer teilweisen Diffusion und Bindung von Partikeln ohne vollständige Verflüssigung beruht.
- Der Schmelzpunkt ist die Grenztemperatur, bei der ein Material vom festen in den flüssigen Zustand übergeht. Beim Sintern wird dieser Schwellenwert umgangen, um die strukturelle Integrität des Materials aufrechtzuerhalten.
-
Energiebedarf:
- Beim Sintern ist im Vergleich zum Schmelzen weniger Wärmeenergie erforderlich, da die innere Struktur des Materials nicht vollständig zerstört wird.
- Das Schmelzen erfordert deutlich mehr Energie, um die Kohäsionskräfte zu überwinden, die die Atome oder Moleküle des Materials in einem festen Zustand zusammenhalten.
-
Prozessmechanismen:
- Sintern: Kombiniert Hitze und Druck, um Partikel zu verdichten und zu verbinden. Der Prozess kann fein abgestimmt werden, um bestimmte Materialeigenschaften wie Porosität, Dichte und Festigkeit zu erreichen.
- Schmelzen: Hauptsächlich temperaturbedingt, was zu einem vollständigen Phasenwechsel führt. Das Material wird vollständig flüssig und ermöglicht das Gießen oder Formen in neue Formen.
-
Materielle Ergebnisse:
- Durch Sintern entstehen Materialien mit kontrollierter Porosität und Mikrostruktur. Es wird häufig in der Pulvermetallurgie, Keramik und additiven Fertigung eingesetzt, um komplexe Formen mit präzisen Eigenschaften zu erzeugen.
- Beim Schmelzen entstehen Materialien mit einer homogenen flüssigen Phase, die gegossen oder geformt werden können, beim Erstarren jedoch möglicherweise einige der strukturellen Eigenschaften des ursprünglichen Materials verlieren.
-
Vorteile des Sinterns gegenüber dem Schmelzen:
- Größere Kontrolle über Materialeigenschaften wie Porosität und Korngröße.
- Geringerer Energieverbrauch aufgrund der fehlenden Verflüssigung.
- Fähigkeit, Materialien zu verarbeiten, die schwer zu schmelzen sind oder einen hohen Schmelzpunkt haben.
-
Anwendungen:
- Sintern wird häufig in Branchen wie der Automobilindustrie (für Motorkomponenten), der Luft- und Raumfahrtindustrie (für Leichtbauteile) und der Elektronikbranche (für leitfähige Pasten) eingesetzt.
- Schmelzen ist in Prozessen wie Metallguss, Glasherstellung und Kunststoffformen unerlässlich.
-
Mikrostrukturelle Unterschiede:
- Gesinterte Materialien können mikroskopisch kleine Lücken oder Poren aufweisen, was für Anwendungen, die eine kontrollierte Porosität erfordern, wie Filter oder Katalysatoren, von Vorteil sein kann.
- Geschmolzene Materialien weisen typischerweise eine dichtere, gleichmäßigere Struktur auf, da die Partikelgrenzen während der Verflüssigung vollständig aufgelöst werden.
Zusammenfassend wird die Beziehung zwischen Sintertemperatur und Schmelzpunkt durch die Notwendigkeit definiert, die Sintertemperaturen unter dem Schmelzpunkt zu halten, um eine Verflüssigung zu vermeiden und gleichzeitig eine Partikelbindung zu erreichen. Diese Unterscheidung ermöglicht eine präzise Kontrolle der Materialeigenschaften und macht das Sintern zu einem vielseitigen und energieeffizienten Prozess für eine Vielzahl industrieller Anwendungen.
Übersichtstabelle:
Aspekt | Sintern | Schmelzen |
---|---|---|
Temperatur | Unterhalb des Schmelzpunkts des Materials | Am oder über dem Schmelzpunkt des Materials |
Energiebedarf | Weniger Energie, keine Verflüssigung | Höhere Energie, vollständiger Phasenwechsel |
Prozessmechanismus | Hitze und Druck verbinden Partikel; behält seinen festen Zustand | Temperaturgesteuert; verwandelt sich fest in flüssig |
Materielle Ergebnisse | Kontrollierte Porosität, Mikrostruktur und präzise Eigenschaften | Homogene flüssige Phase; kann beim Abkühlen seine strukturellen Eigenschaften verlieren |
Anwendungen | Automobil, Luft- und Raumfahrt, Elektronik, Pulvermetallurgie, Keramik | Metallguss, Glasherstellung, Kunststoffformen |
Vorteile | Energieeffizient, bessere Kontrolle über die Eigenschaften, verarbeitet hochschmelzende Materialien | Geeignet zum Gießen und Formen |
Benötigen Sie Hilfe bei der Optimierung Ihrer Materialverarbeitung? Kontaktieren Sie noch heute unsere Experten für maßgeschneiderte Lösungen!