Der Sinterzyklus ist ein wichtiger Prozess in der Materialwissenschaft und der Fertigung, bei dem pulverförmige Materialien durch Anwendung von Hitze und Druck in dichte, feste Körper umgewandelt werden, ohne dass der Schmelzpunkt des Materials erreicht wird.Dieses Verfahren wird in der Pulvermetallurgie, der Keramik- und der Kunststoffindustrie häufig eingesetzt, um haltbare und kohäsive Produkte herzustellen.Der Sinterzyklus umfasst in der Regel mehrere Phasen, darunter die Aufbereitung des Pulvers, die Verdichtung und die kontrollierte Erhitzung, gefolgt von der Abkühlung.Jede Stufe spielt eine wichtige Rolle, um die strukturelle Integrität und die gewünschten Eigenschaften des Endprodukts zu gewährleisten.
Die wichtigsten Punkte erklärt:
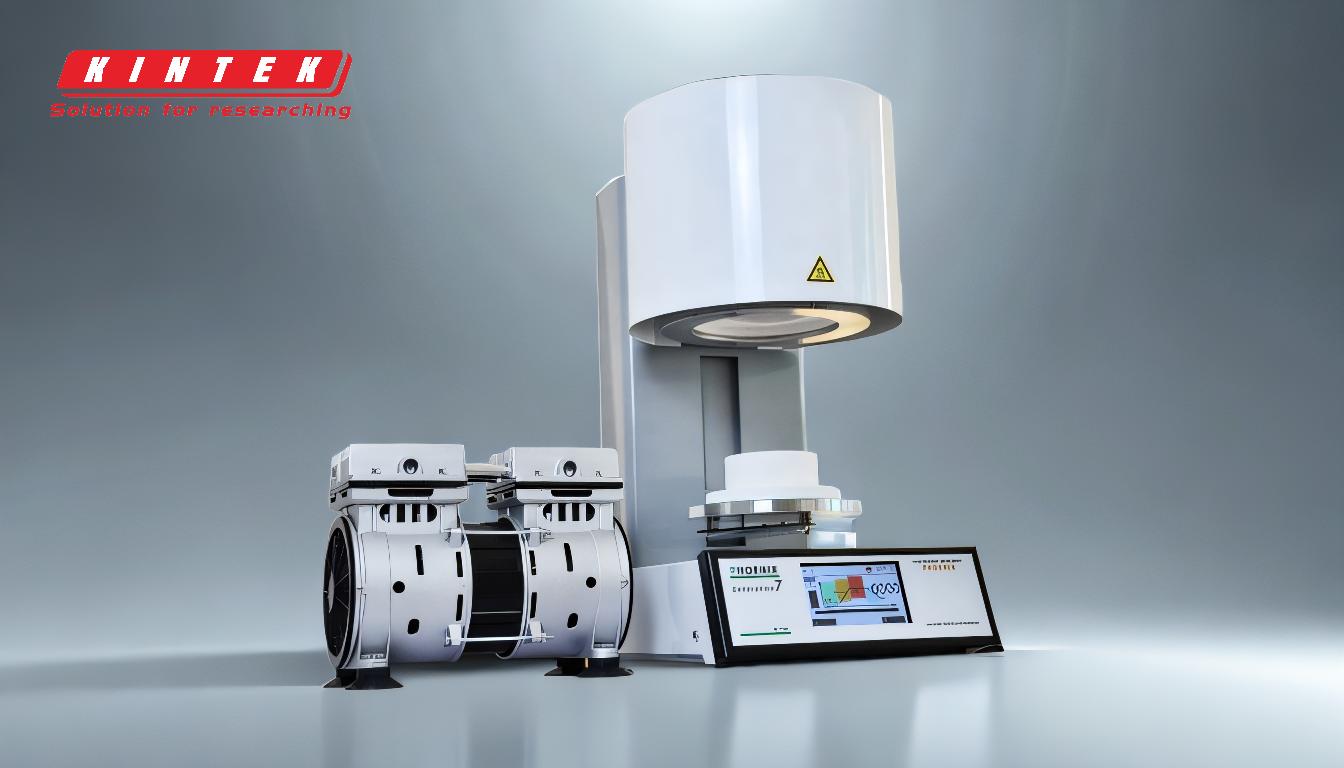
-
Definition und Zweck des Sinterns:
- Das Sintern ist ein Verfahren, bei dem kleine Partikel zu einer festen Masse verschmelzen, ohne dass das Material schmilzt.Es wird verwendet, um aus pulverförmigen Materialien wie Metallen, Keramik und Kunststoffen dichte, haltbare Produkte herzustellen.
- Der Hauptzweck des Sinterns besteht darin, benachbarte Pulverpartikel zu verbinden, wodurch eine zusammenhängende Struktur mit verbesserten mechanischen Eigenschaften wie Festigkeit, Härte und Haltbarkeit entsteht.
-
Stadien des Sinterzyklus:
-
Puderzubereitung:
- Das Verfahren beginnt mit der Aufbereitung von Rohstoffen in Pulverform.Dabei können Pulver mit Zusatzstoffen wie Bindemitteln, Entflockungsmitteln und Wasser gemischt werden, um eine Aufschlämmung zu erzeugen, die dann sprühgetrocknet wird, um ein Granulat zu bilden.
-
Verdichtung:
- Das vorbereitete Pulver wird mit mechanischem Druck verdichtet, entweder durch Kalt- oder Warmpressen, um ein "grünes" Teil zu formen.Dieser Schritt gewährleistet die Gleichmäßigkeit und eliminiert Hohlräume im Material.
-
Sintern (Brennen):
- Das Rohteil wird in einer kontrollierten Umgebung erhitzt, in der Regel in einem Sinterofen oder Brennofen.Die Temperatur wird sorgfältig reguliert, um die Partikelbindung durch Diffusion zu erleichtern, was zu einer Halsbildung und Verdichtung führt.Das Material schmilzt nicht, sondern unterliegt einer atomaren Diffusion, durch die die Partikel miteinander verschmelzen.
-
Abkühlung:
- Nach dem Sintern wird das Material allmählich abgekühlt, damit es sich zu einer festen und kohäsiven Struktur verfestigen kann.Diese Phase ist entscheidend für das Erreichen der gewünschten mechanischen Eigenschaften und die Vermeidung von Fehlern.
-
Puderzubereitung:
-
Schlüsselfaktoren, die den Sinterprozess beeinflussen:
-
Temperatur:
- Die Sintertemperatur muss hoch genug sein, um die Partikelbindung zu fördern, aber unter dem Schmelzpunkt des Materials liegen, um eine Verflüssigung zu vermeiden.
-
Druck:
- Der während der Verdichtung ausgeübte Druck gewährleistet eine gleichmäßige Dichte und reduziert die Porosität im Grünling.
-
Zeit:
- Die Dauer des Sinterns beeinflusst den Grad der Partikelbindung und der Verdichtung.Längere Sinterzeiten führen im Allgemeinen zu stärkeren Bindungen, müssen aber gegen den Energieverbrauch und die Produktionseffizienz abgewogen werden.
-
Atmosphäre:
- Die Sinterumgebung (z. B. Inertgas, Vakuum oder Luft) kann die endgültigen Eigenschaften des Materials beeinflussen, indem sie die Oxidation verhindert oder bestimmte chemische Reaktionen begünstigt.
-
Temperatur:
-
Anwendungen des Sinterns:
-
Pulvermetallurgie:
- Das Sintern wird häufig zur Herstellung von Metallteilen wie Zahnrädern, Lagern und Automobilteilen verwendet.Es ermöglicht die Herstellung komplexer Formen mit hoher Präzision und minimalem Abfall.
-
Keramiken:
- In der Keramikindustrie wird das Sintern zur Herstellung von Fliesen, Isolatoren und anderen Produkten mit hoher thermischer und mechanischer Stabilität verwendet.
-
Kunststoffe und Verbundwerkstoffe:
- Mit Hilfe des Sinterns lassen sich haltbare Kunststoffteile und Verbundwerkstoffe mit maßgeschneiderten Eigenschaften herstellen.
-
Pulvermetallurgie:
-
Vorteile des Sinterns:
-
Kosten-Wirksamkeit:
- Das Sintern reduziert den Materialabfall und ermöglicht die Herstellung von endkonturnahen Bauteilen, wodurch der Bedarf an zusätzlicher Bearbeitung minimiert wird.
-
Material Vielseitigkeit:
- Das Verfahren kann auf eine Vielzahl von Materialien angewendet werden, darunter Metalle, Keramiken und Polymere.
-
Verbesserte Eigenschaften:
- Gesinterte Produkte weisen aufgrund der Verdichtung und Bindung der Partikel eine höhere mechanische Festigkeit, Härte und Verschleißfestigkeit auf.
-
Kosten-Wirksamkeit:
-
Herausforderungen und Überlegungen:
-
Kontrolle der Prozessparameter:
- Um gleichbleibende Ergebnisse zu erzielen, ist eine präzise Steuerung von Temperatur, Druck und Zeit erforderlich, was bei der Produktion in großem Maßstab eine Herausforderung darstellen kann.
-
Grenzen des Materials:
- Nicht alle Materialien sind für das Sintern geeignet, insbesondere solche mit niedrigem Schmelzpunkt oder schlechter thermischer Stabilität.
-
Kosten der Ausrüstung:
- Sinteröfen und -pressen können teuer sein, insbesondere bei Anwendungen mit hohen Temperaturen oder hohem Druck.
-
Kontrolle der Prozessparameter:
Zusammenfassend lässt sich sagen, dass der Sinterzyklus ein vielseitiger und wesentlicher Prozess in der modernen Fertigung ist, der die Herstellung von Hochleistungswerkstoffen und -komponenten ermöglicht.Wenn die Hersteller die Phasen, Einflussfaktoren und Anwendungen des Sinterns verstehen, können sie den Prozess optimieren, um spezifische Produktanforderungen zu erfüllen und hervorragende Ergebnisse zu erzielen.
Zusammenfassende Tabelle:
Aspekt | Einzelheiten |
---|---|
Definition | Verschmelzen von Pulverpartikeln zu einer festen Masse, ohne das Material zu schmelzen. |
Etappen | Pulveraufbereitung, Verdichtung, Sintern (Brennen), Kühlung. |
Wichtige Faktoren | Temperatur, Druck, Zeit, Atmosphäre. |
Anwendungen | Pulvermetallurgie, Keramiken, Kunststoffe und Verbundwerkstoffe. |
Vorteile | Kostengünstig, Vielseitigkeit des Materials, Verbesserte mechanische Eigenschaften. |
Herausforderungen | Präzise Parametersteuerung, Materialbeschränkungen, hohe Anlagenkosten. |
Optimieren Sie Ihren Sinterprozess mit fachkundiger Beratung - Kontaktieren Sie uns noch heute !