Sputtern ist ein vielseitiges Verfahren zur Abscheidung von Dünnschichten, das in Branchen wie der Halbleiter-, Optik- und Datenspeicherindustrie weit verbreitet ist.Dabei wird ein Zielmaterial in einer Vakuumkammer mit hochenergetischen Ionen beschossen, wodurch Atome herausgeschleudert werden und sich auf einem Substrat ablagern.Diese Methode ist sehr gut steuerbar und ermöglicht die Herstellung gleichmäßiger, hochwertiger Schichten mit einer Dicke von Nanometern bis Mikrometern.Sputtern wird für Anwendungen wie Antireflexbeschichtungen, Halbleitermetallisierung und verschleißfeste Werkzeugbeschichtungen eingesetzt.Das Verfahren ist präzise, wiederholbar und in der Lage, eine breite Palette von Materialien abzuscheiden, darunter Metalle, Legierungen und Verbindungen, was es zu einem Eckpfeiler der modernen Fertigung und Technologie macht.
Die wichtigsten Punkte erklärt:
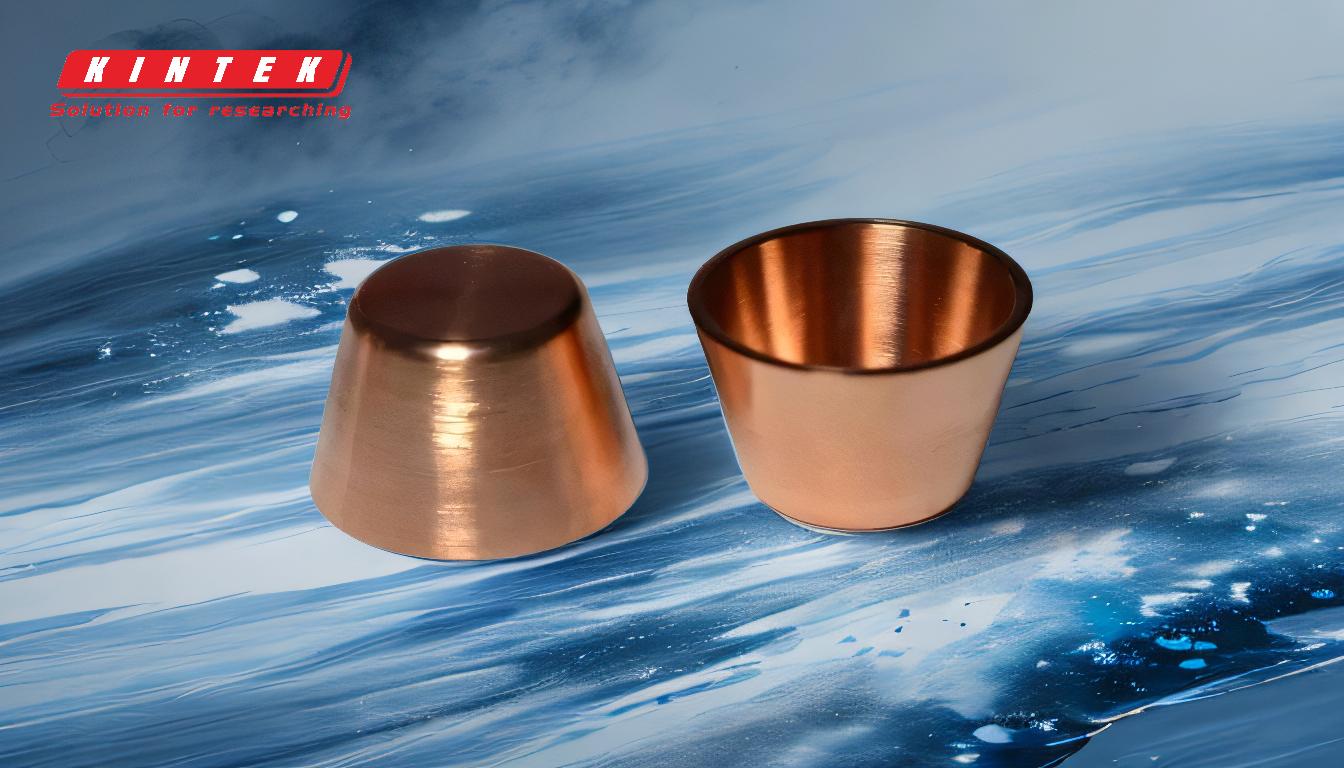
-
Definition des Sputterns
- Sputtern ist eine Technik der physikalischen Gasphasenabscheidung (PVD), bei der Atome durch den Beschuss mit hochenergetischen Ionen in einer Vakuumumgebung aus einem festen Zielmaterial herausgeschleudert werden.
- Die ausgestoßenen Atome bilden einen Dampfstrom, der sich auf einem Substrat ablagert und einen dünnen Film erzeugt.
- Dieses Verfahren ist sehr gut steuerbar und ermöglicht die Herstellung von Schichten mit präziser Dicke und Zusammensetzung.
-
Mechanismus des Sputterns
- Ein kontrolliertes Gas, in der Regel Argon, wird in eine Vakuumkammer eingeleitet.
- Eine Kathode wird elektrisch erregt, um ein Plasma zu erzeugen, das die Gasatome ionisiert.
- Die positiv geladenen Ionen werden in Richtung des Zielmaterials beschleunigt und lösen beim Aufprall Atome oder Moleküle aus dem Material.
- Diese herausgelösten Atome bilden einen Dampfstrom, der sich auf dem Substrat ablagert und eine dünne Schicht bildet.
-
Anwendungen der Sputtering-Beschichtung
- Halbleiterindustrie:Für die Abscheidung dünner Schichten in integrierten Schaltkreisen, z. B. Metallisierungsschichten und Kontaktmetalle in Dünnschichttransistoren.
- Optik und Glas:Angewandt für Antireflexionsbeschichtungen, Beschichtungen mit niedrigem Emissionsgrad und Filme mit hohem Emissionsgrad auf Glas.
- Speicherung von Daten:Wird bei der Herstellung von Computerfestplatten, CDs und DVDs verwendet.
- Werkzeug-Beschichtungen:Ablagerung von verschleißfesten Schichten wie Titannitrid auf Schneidwerkzeugen.
- Solarzellen:Wird bei der Herstellung von photovoltaischen Solarzellen verwendet.
- Dekorative und funktionelle Beschichtungen:Angewandt für reflektierende Beschichtungen auf Polymeren, Trockenfilm-Schmierstoffen und dekorativen Oberflächen.
-
Vorteile des Sputterns
- Gleichmäßigkeit:Erzeugt sehr gleichmäßige und dichte Filme.
- Vielseitigkeit:Kann eine Vielzahl von Materialien abscheiden, darunter Metalle, Legierungen und Verbindungen.
- Präzision:Ermöglicht eine präzise Kontrolle der Filmdicke und -zusammensetzung.
- Haftung:Gewährleistet eine starke Haftung der Folie auf dem Substrat.
- Skalierbarkeit:Geeignet für die industrielle Großserienproduktion.
-
Arten von Sputtering-Techniken
- DC-Sputtern:Verwendet Gleichstrom zur Erzeugung eines Plasmas, geeignet für leitende Materialien.
- RF-Sputtern:Das Gas wird mit Hilfe von Radiofrequenzen ionisiert, was die Abscheidung von nichtleitenden Materialien ermöglicht.
- Magnetron-Sputtering:Durch den Einsatz von Magnetfeldern wird die Plasmadichte erhöht, wodurch sich die Abscheideraten und die Schichtqualität verbessern.
- Reaktives Sputtern:Einleiten reaktiver Gase (z. B. Stickstoff oder Sauerstoff) zur Bildung von Verbundschichten wie Oxiden oder Nitriden.
-
Hauptbestandteile eines Sputtering-Systems
- Vakuumkammer:Sorgt für eine kontrollierte Umgebung für den Prozess.
- Ziel Material:Die Quelle der zu deponierenden Atome.
- Substrat:Die Oberfläche, auf die die dünne Schicht aufgebracht wird.
- Energieversorgung:Liefert Energie zur Erzeugung von Plasma.
- Gaszufuhrsystem:Leitet den Strom des Sputtergases ein und kontrolliert ihn.
-
Herausforderungen und Überlegungen
- Kosten:Hohe Anfangsinvestitionen für Ausrüstung und Wartung.
- Komplexität:Erfordert eine präzise Steuerung von Parametern wie Druck, Leistung und Gasfluss.
- Grenzen des Materials:Einige Materialien können aufgrund geringer Sputterausbeute oder hoher Schmelzpunkte schwer zu sputtern sein.
- Verunreinigung:Erfordert eine sorgfältige Handhabung, um Verunreinigungen in der abgeschiedenen Schicht zu vermeiden.
-
Zukünftige Trends in der Sputtering-Technologie
- Fortgeschrittene Materialien:Entwicklung neuer Zielmaterialien für spezielle Anwendungen.
- Nachhaltigkeit:Schwerpunkt auf der Reduzierung des Energieverbrauchs und der Umweltauswirkungen.
- Automatisierung:Integration von KI und maschinellem Lernen zur Prozessoptimierung.
- Miniaturisierung:Anpassung für Nanotechnologie und Mikroelektronik.
Zusammenfassend lässt sich sagen, dass das Sputtern eine entscheidende Technik in der modernen Fertigung ist, die die Abscheidung hochwertiger dünner Schichten für eine Vielzahl von Anwendungen ermöglicht.Seine Präzision, Vielseitigkeit und Skalierbarkeit machen es in Branchen wie Halbleiter, Optik und Energie unverzichtbar.
Zusammenfassende Tabelle:
Aspekt | Einzelheiten |
---|---|
Definition | Physikalische Abscheidung aus der Gasphase (PVD) unter Verwendung hochenergetischer Ionen. |
Mechanismus | Beschuss des Zielmaterials in einer Vakuumkammer zur Abscheidung dünner Schichten. |
Anwendungen | Halbleiter, Optik, Datenspeicherung, Werkzeugbeschichtungen, Solarzellen und mehr. |
Vorteile | Gleichmäßigkeit, Vielseitigkeit, Präzision, starke Adhäsion und Skalierbarkeit. |
Techniken | DC-, RF-, Magnetron- und reaktives Sputtern. |
Bestandteile | Vakuumkammer, Targetmaterial, Substrat, Stromversorgung, Gaszufuhr. |
Herausforderungen | Hohe Kosten, Komplexität, Materialbeschränkungen und Kontaminationsrisiken. |
Zukünftige Trends | Moderne Materialien, Nachhaltigkeit, Automatisierung und Miniaturisierung. |
Entdecken Sie, wie Sputtern Ihren Fertigungsprozess verbessern kann. Kontaktieren Sie unsere Experten noch heute !